BIOREACTOR MANUFACTURER IN KARNATAKA
UPM Is Enguage In Designing and BIOREACTOR MANUFACTURING Company In Karnataka. We are Pioneer as a Bioreactor Manufacturer in Karnataka India. UPM Make Following Types Of Fermenter and Bioreactor For Biotech Lab and Industries In India.
- industrial fermenter
- fermentation plant
- api plant
- fed batch bioreactor
- stirred tank fermenter
- pilot scale fermenter
- fermentation tank
Top Manufacturers of Fermenter in Karnataka-India
all right so I’ve got my P 1000 I need to put one milliliter of liquid in it this is the solution that we’re going add to it it’s the dissolved oxygen sensor electrolyte adding that to the cap. then you’ll put that back very carefully and see there’s an O-ring in there as well. it’s okay if some of it spills over don’t know if you can see that or not but a little bit of it spilt over just wipe it with the kids. it’s potassium chloride as well okay now that we’ve added the electrolyte to the do probe we’re going to put it in its proper port it does not go next to the condenser it goes one over so it goes right here put that in and screw it into place.
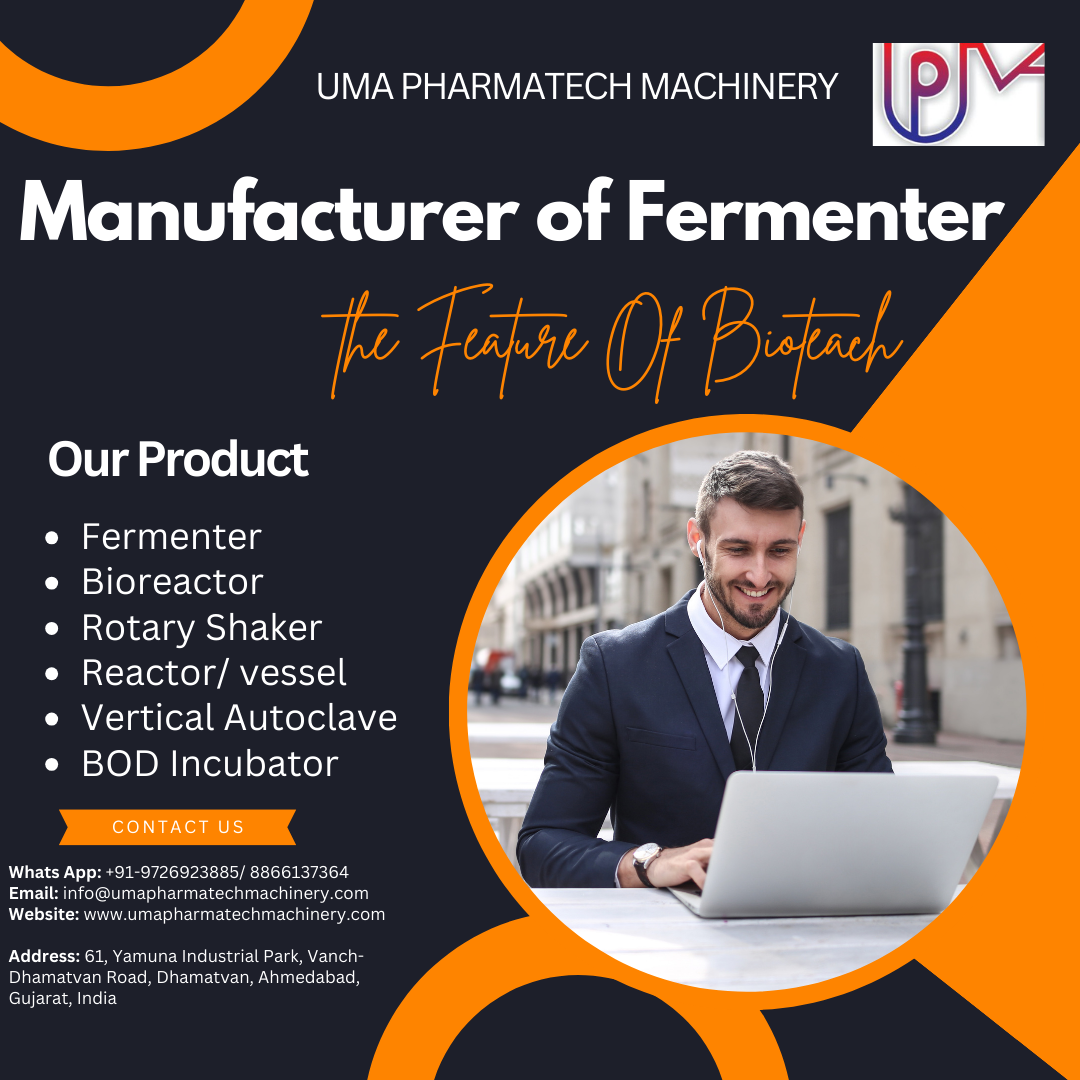
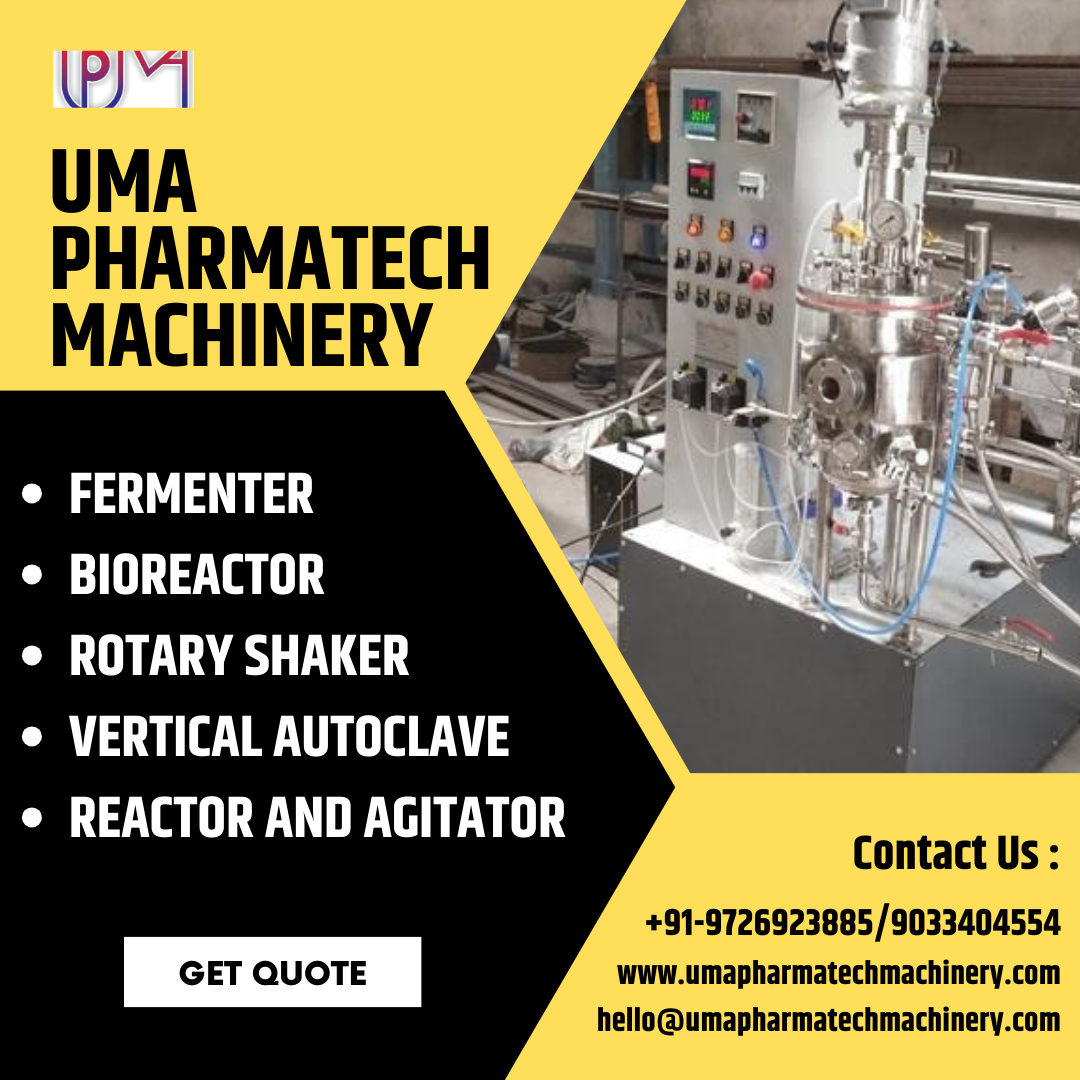
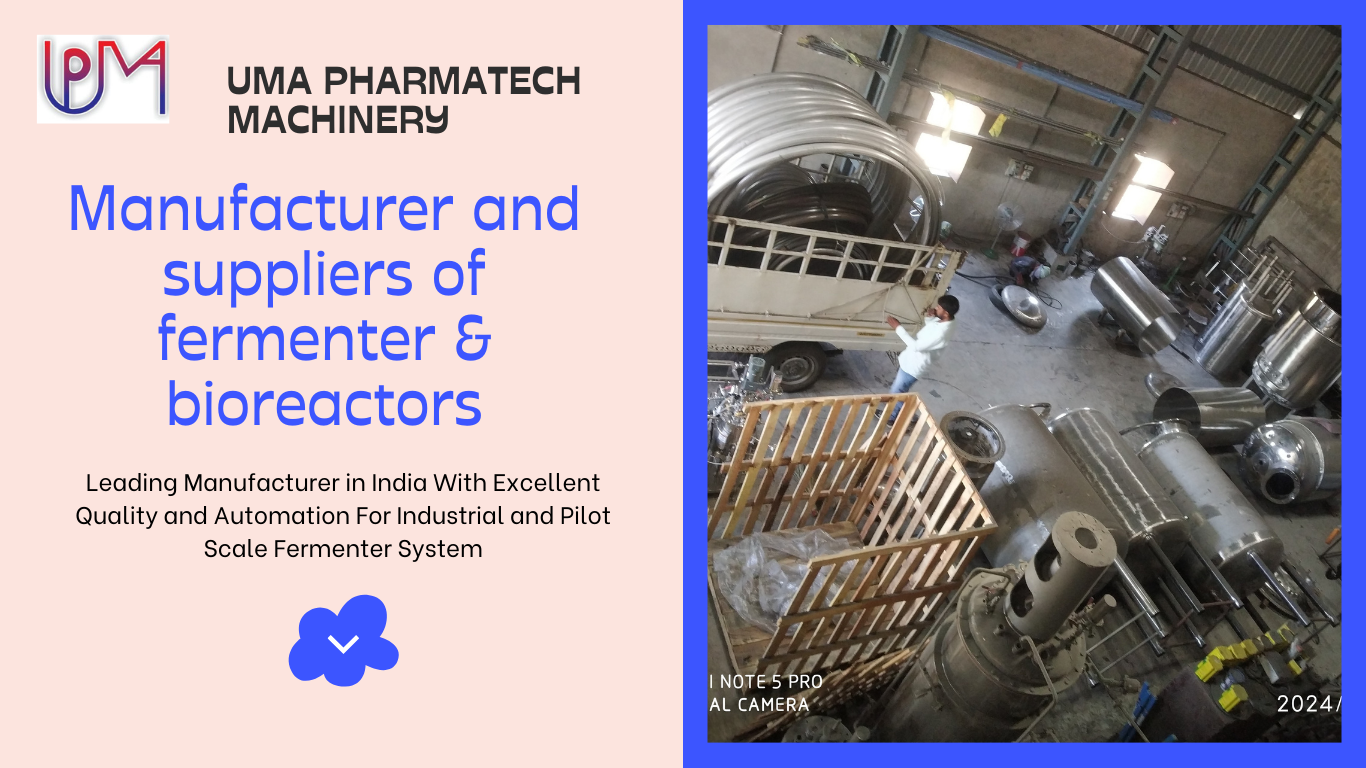
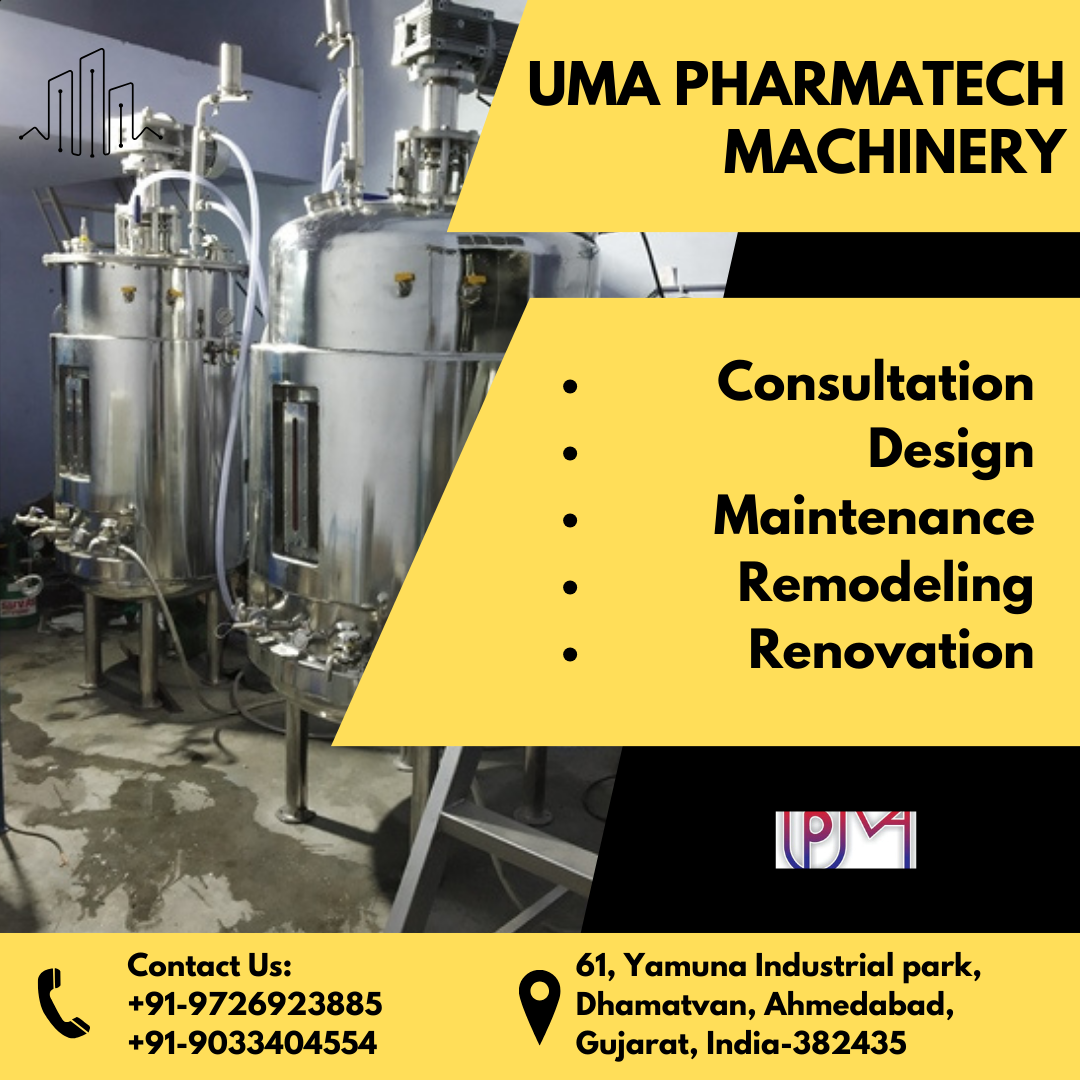
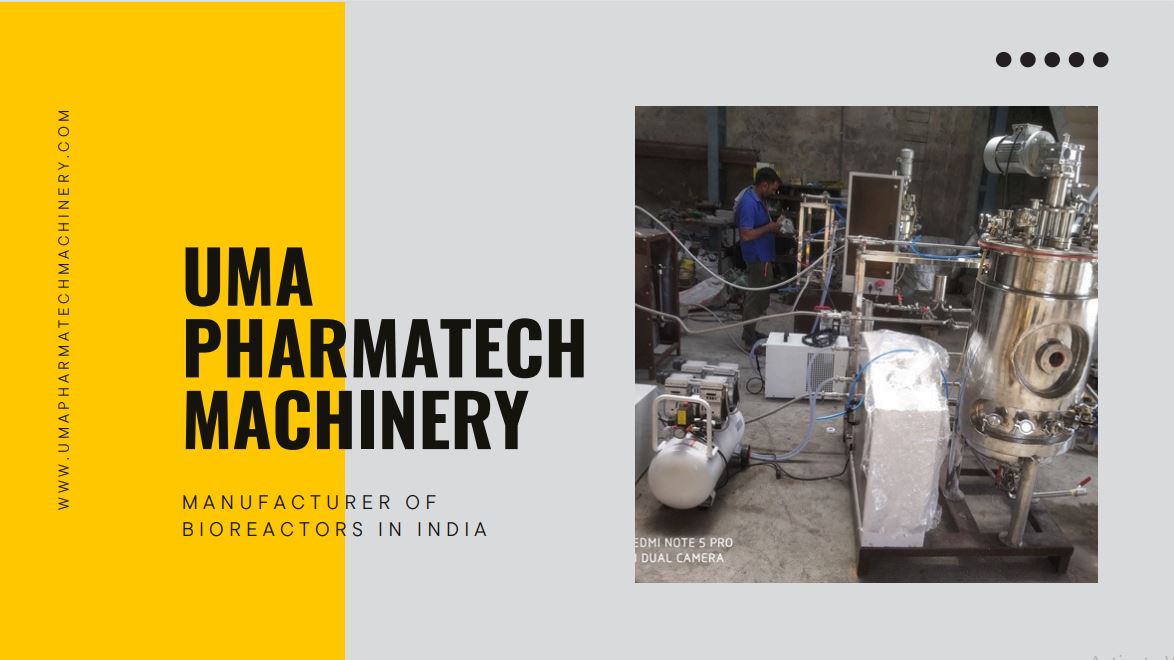
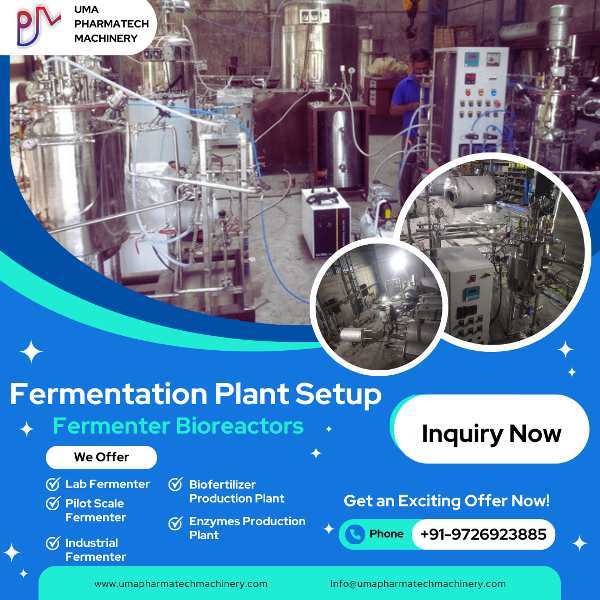
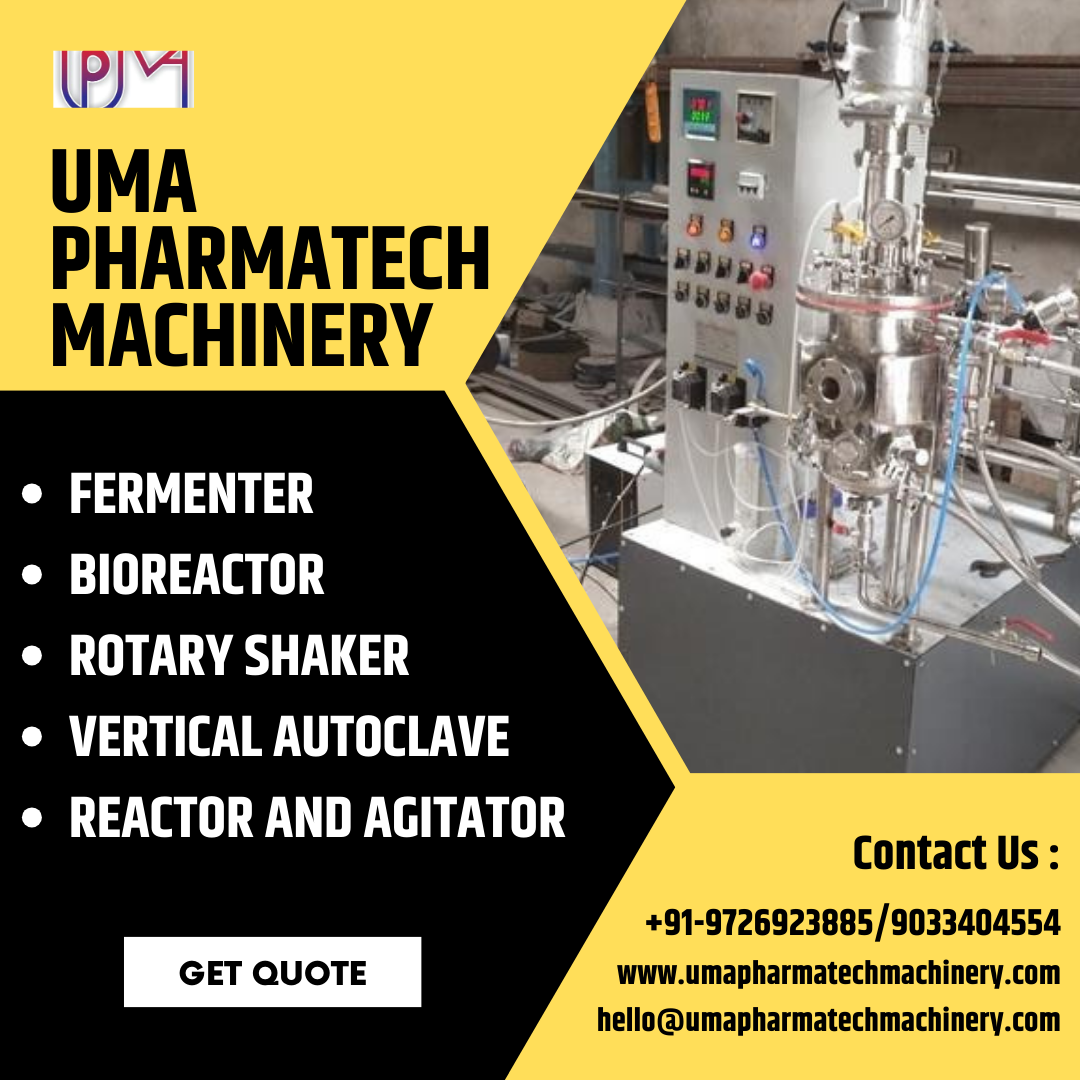
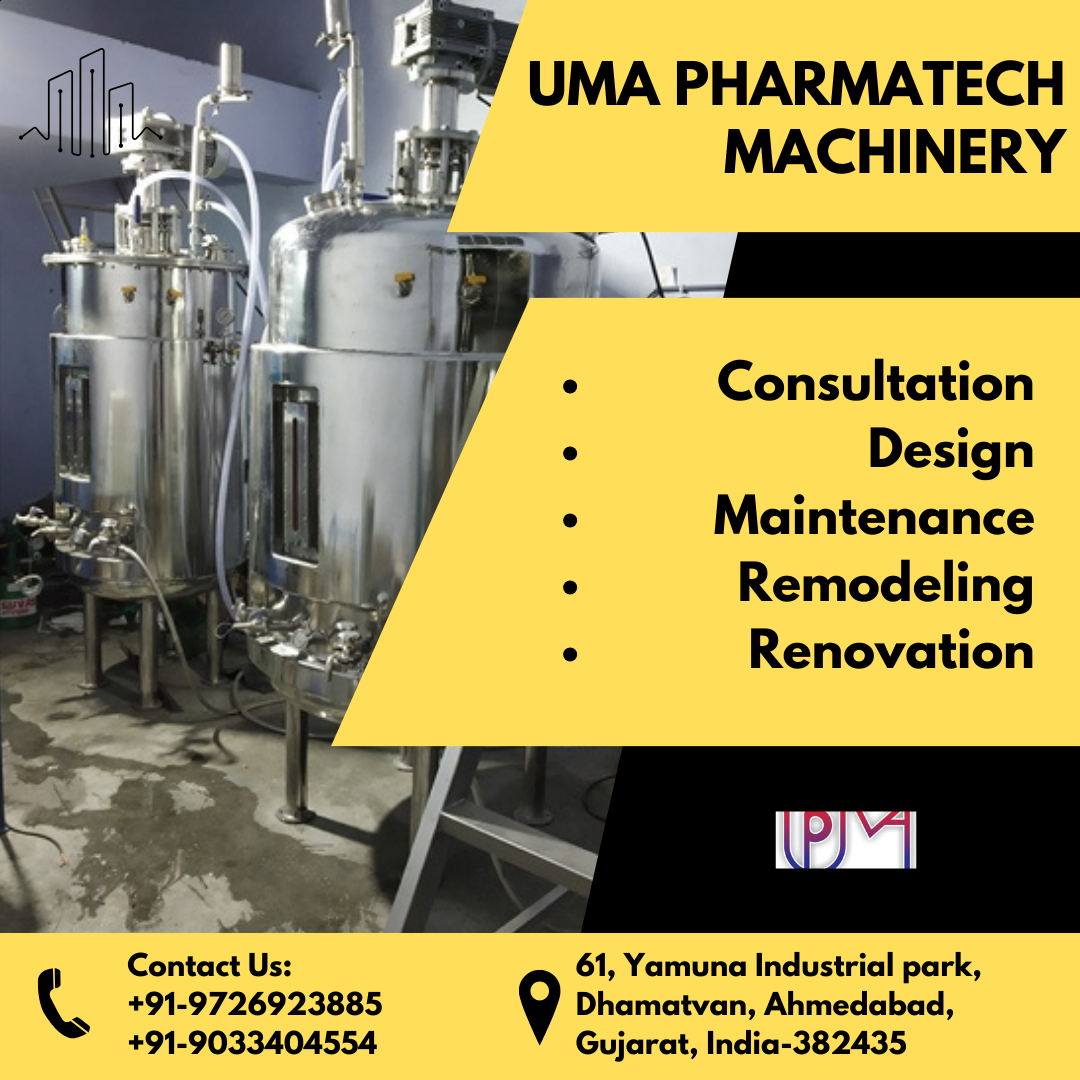
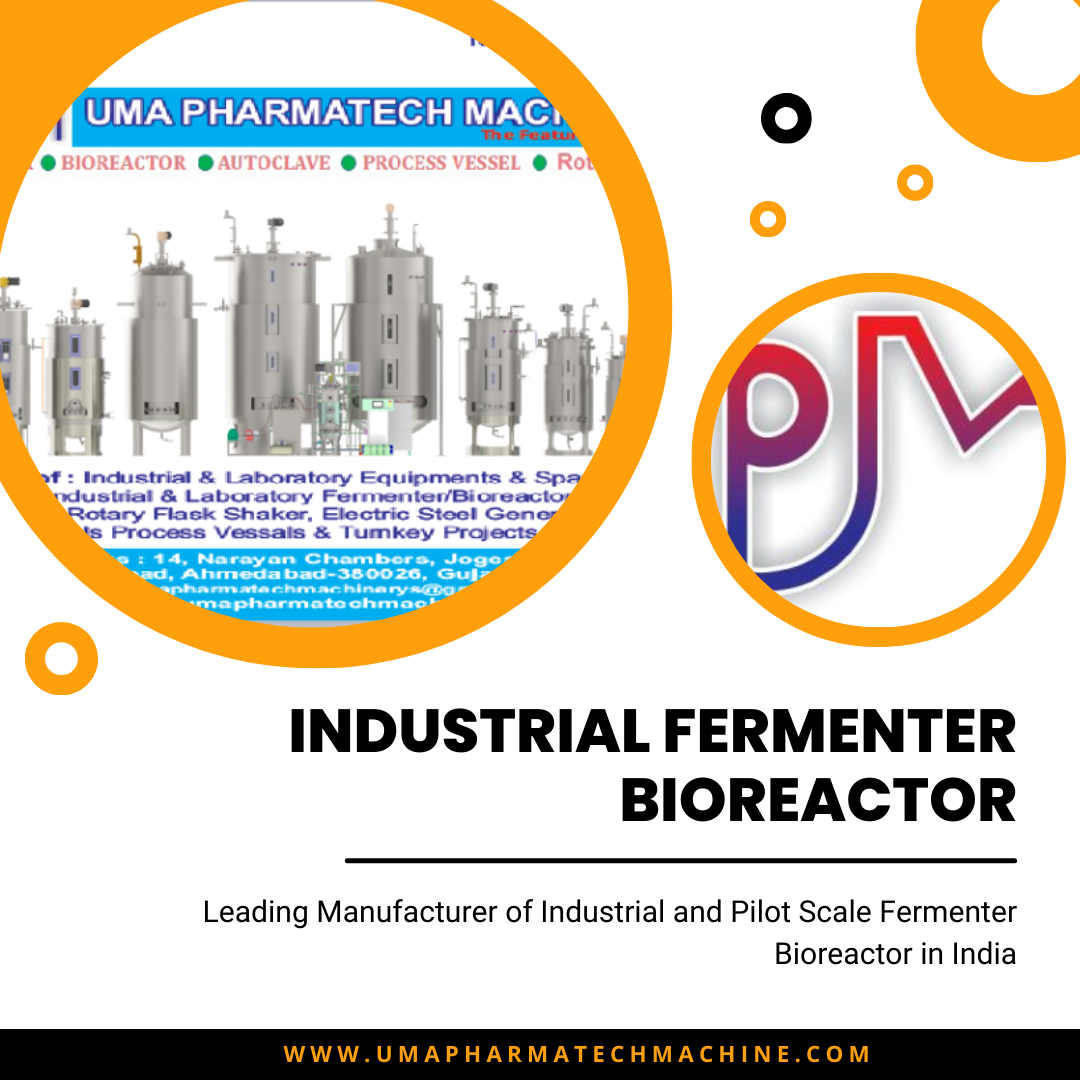
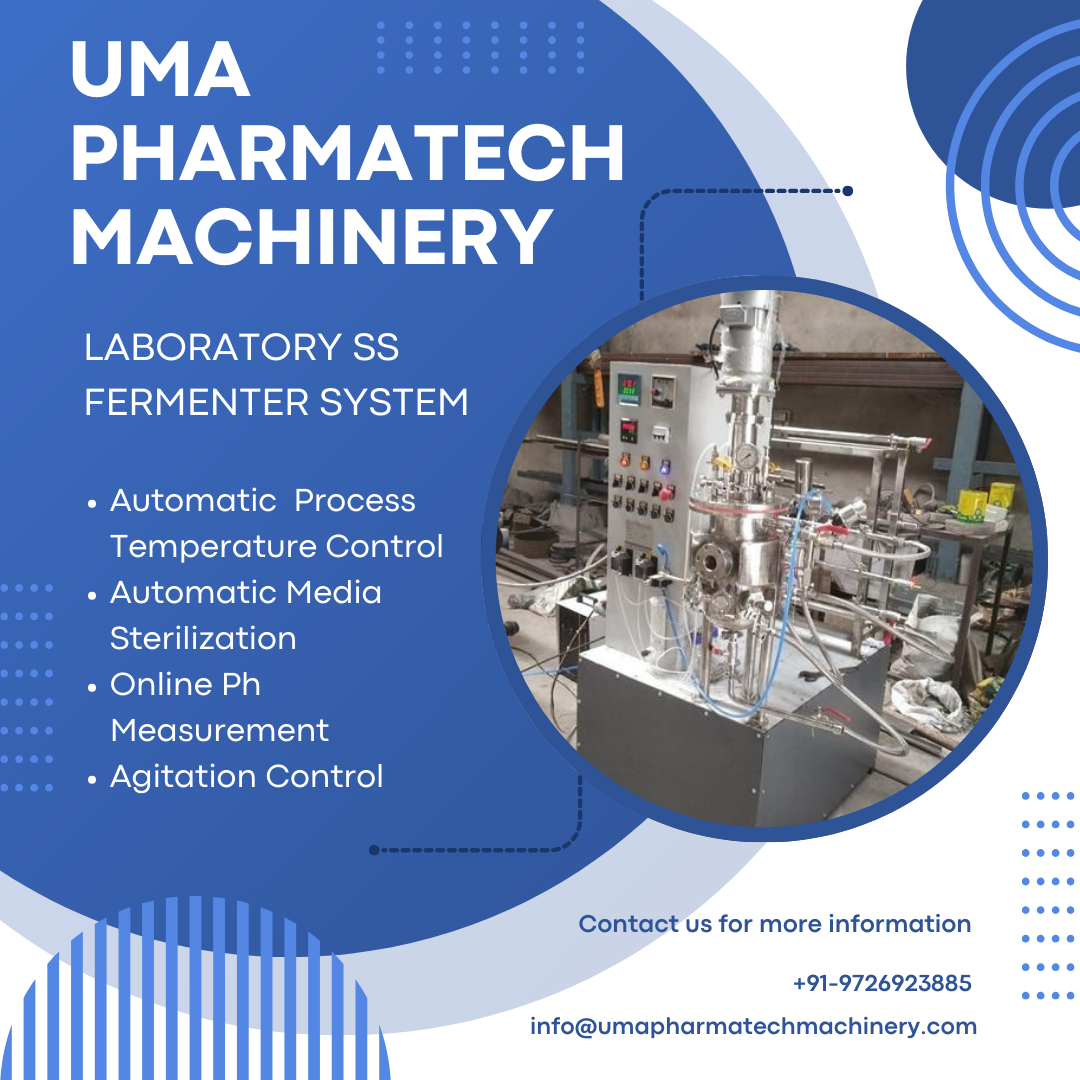
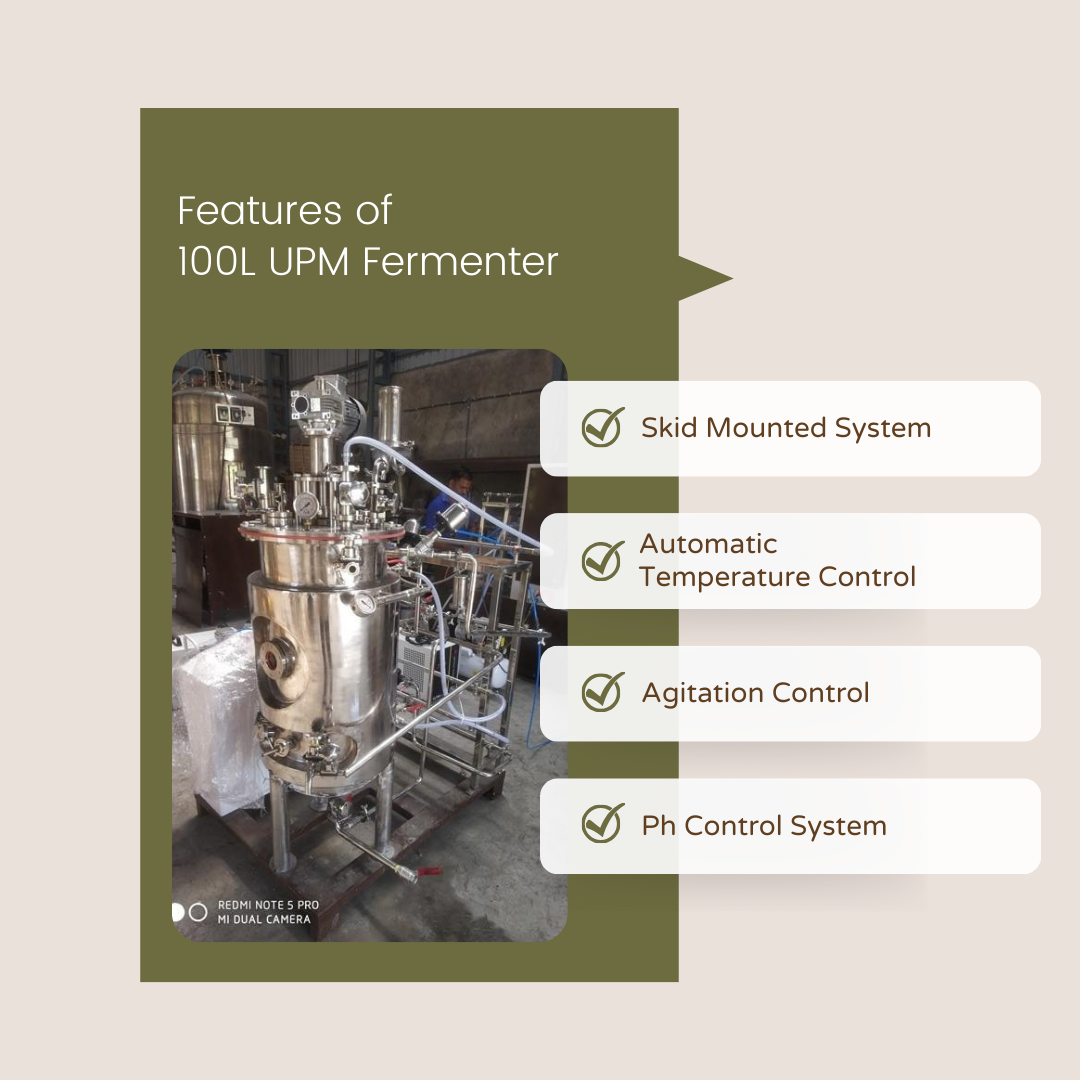
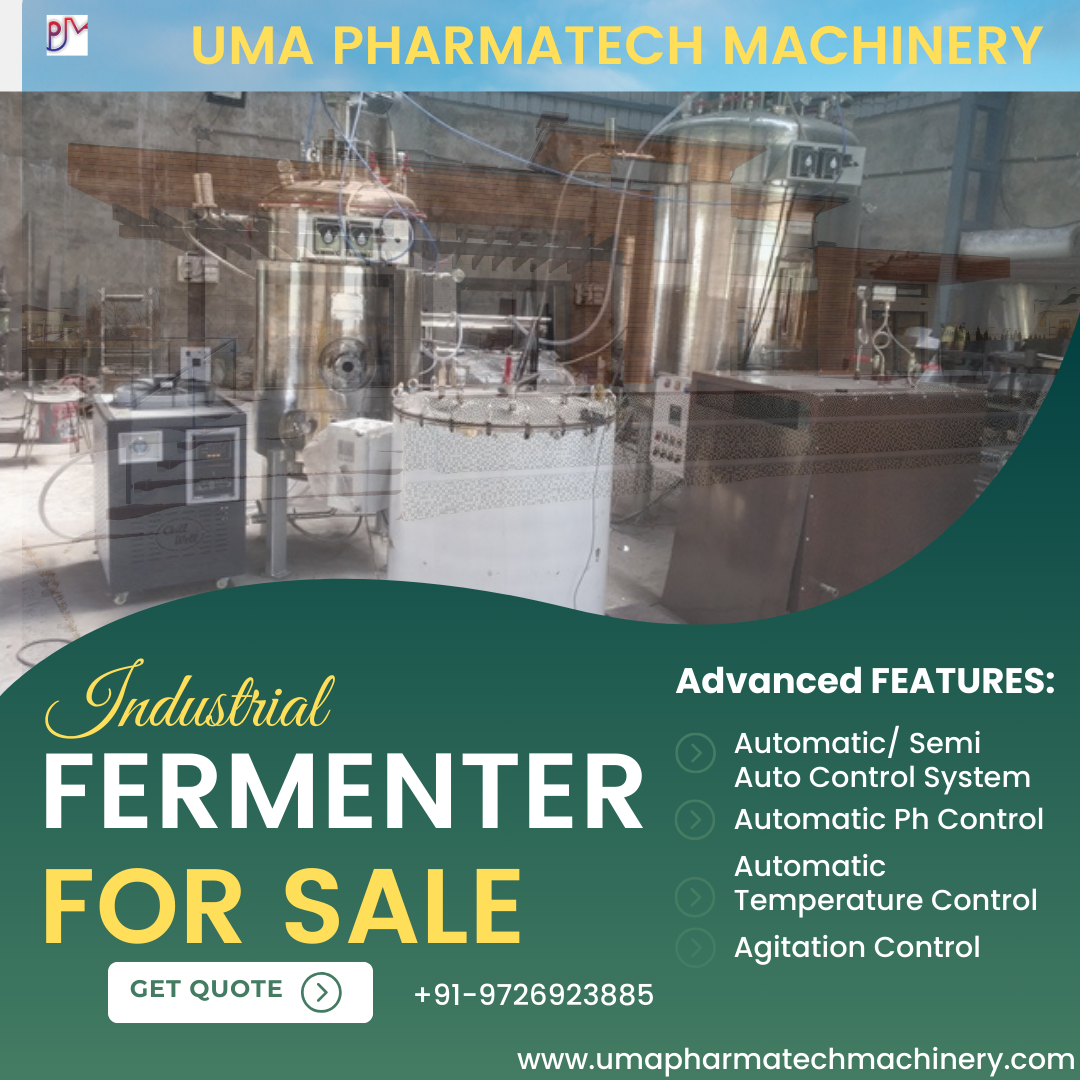
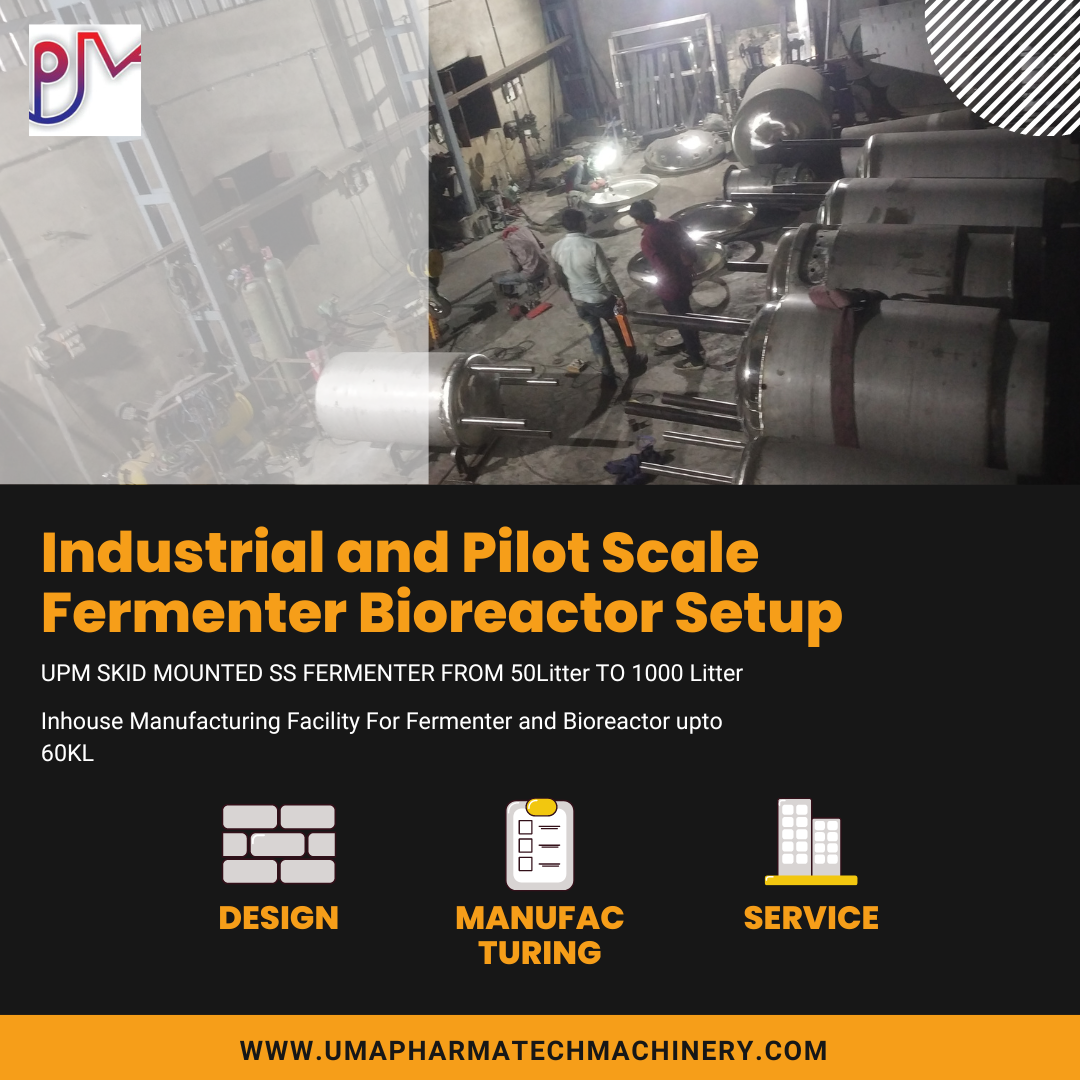
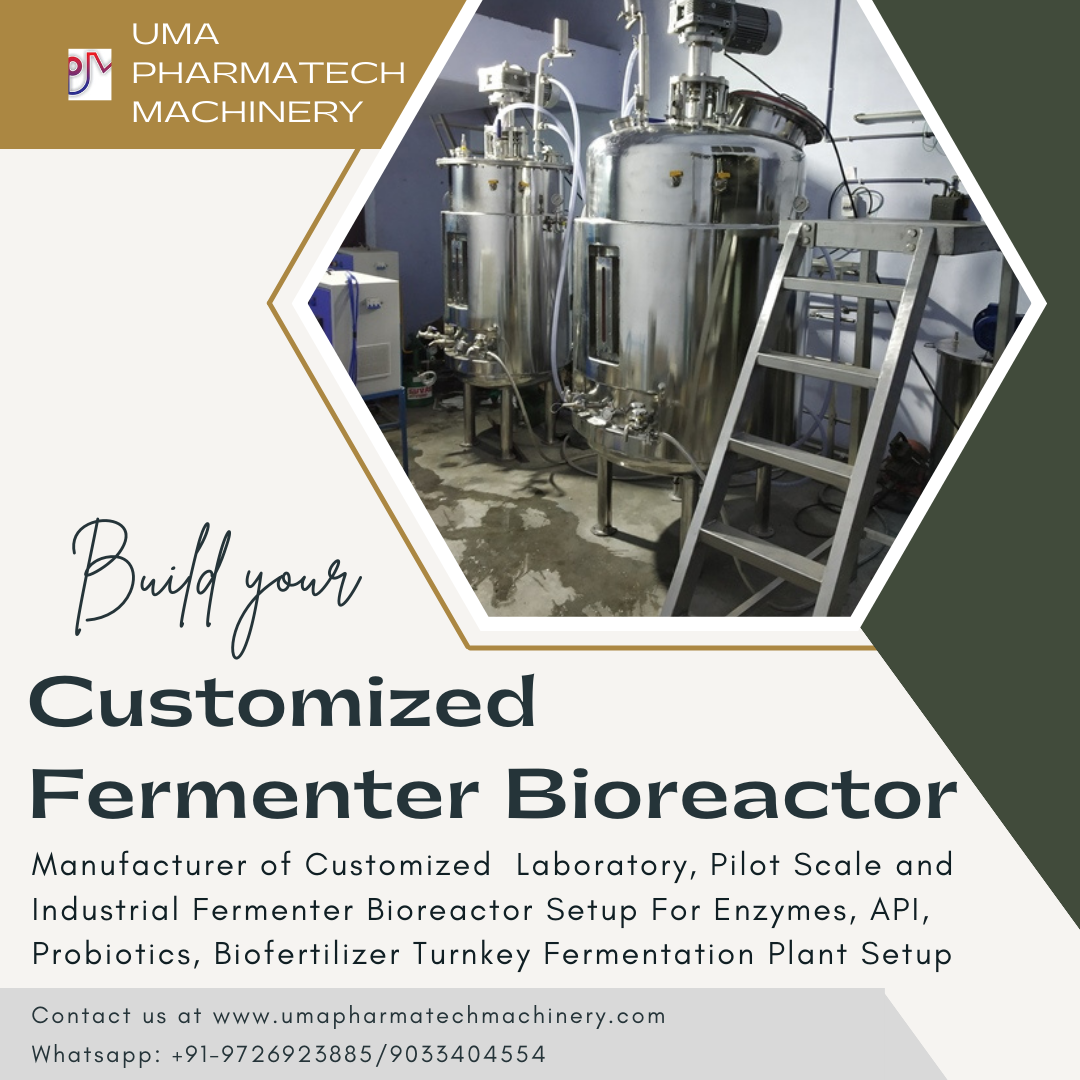
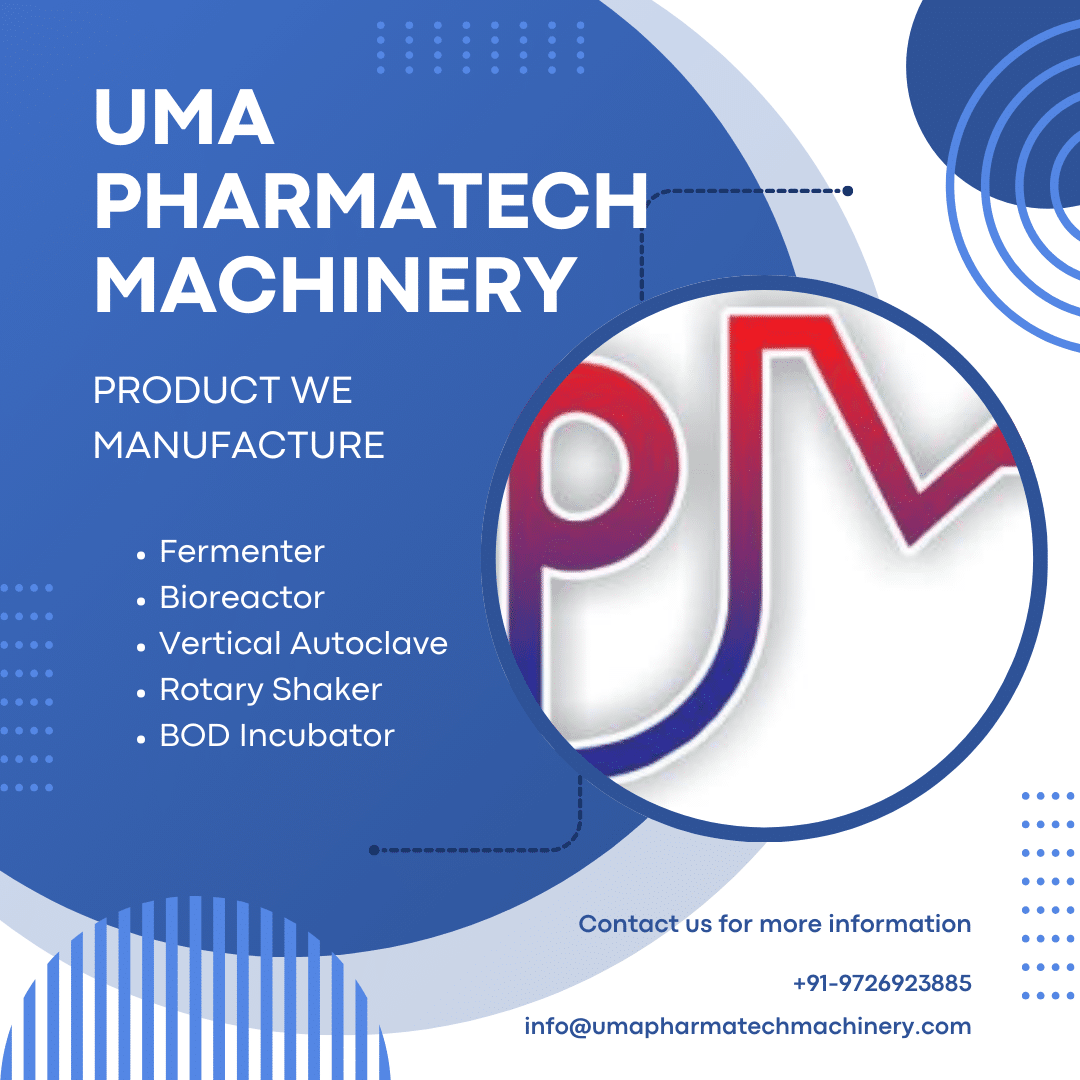
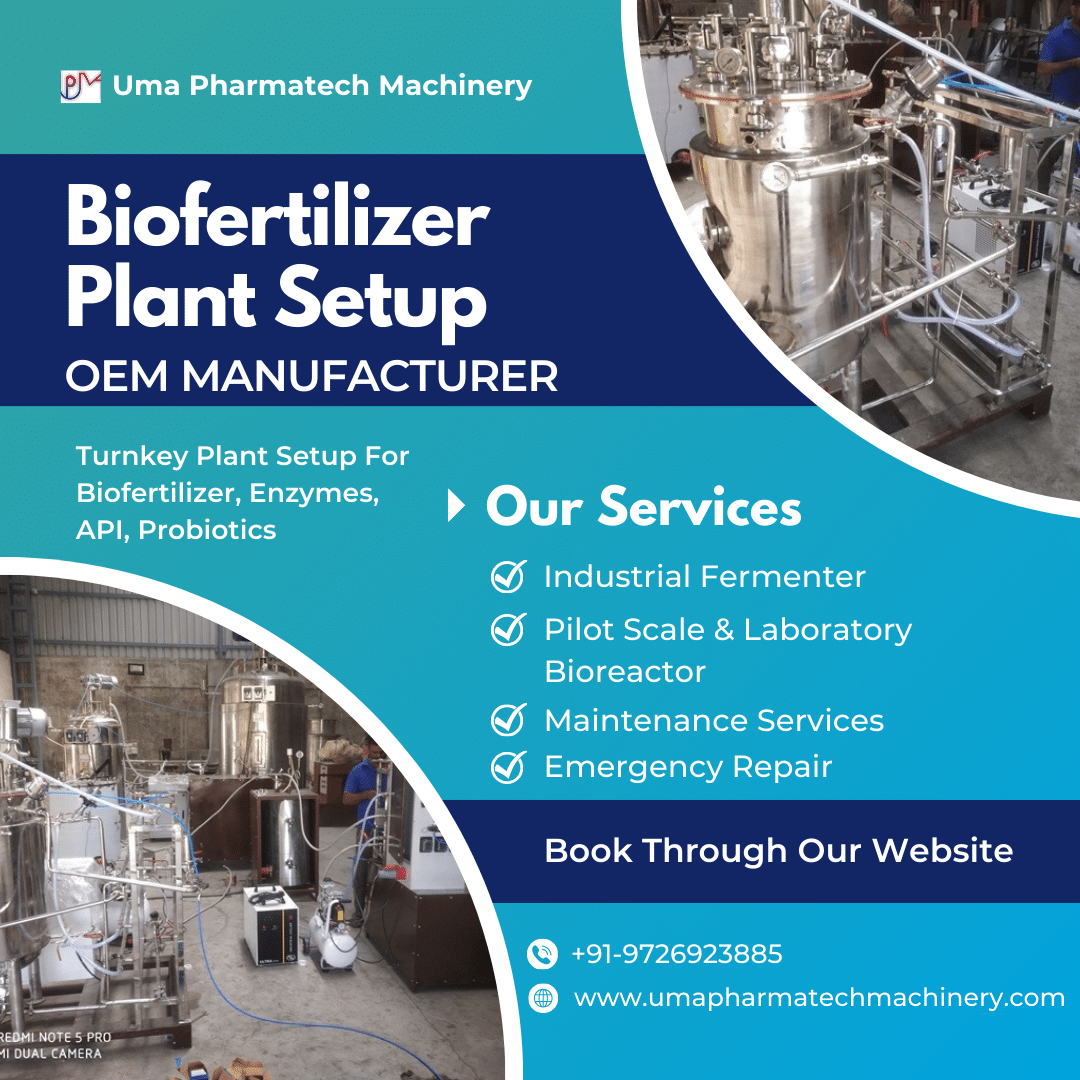
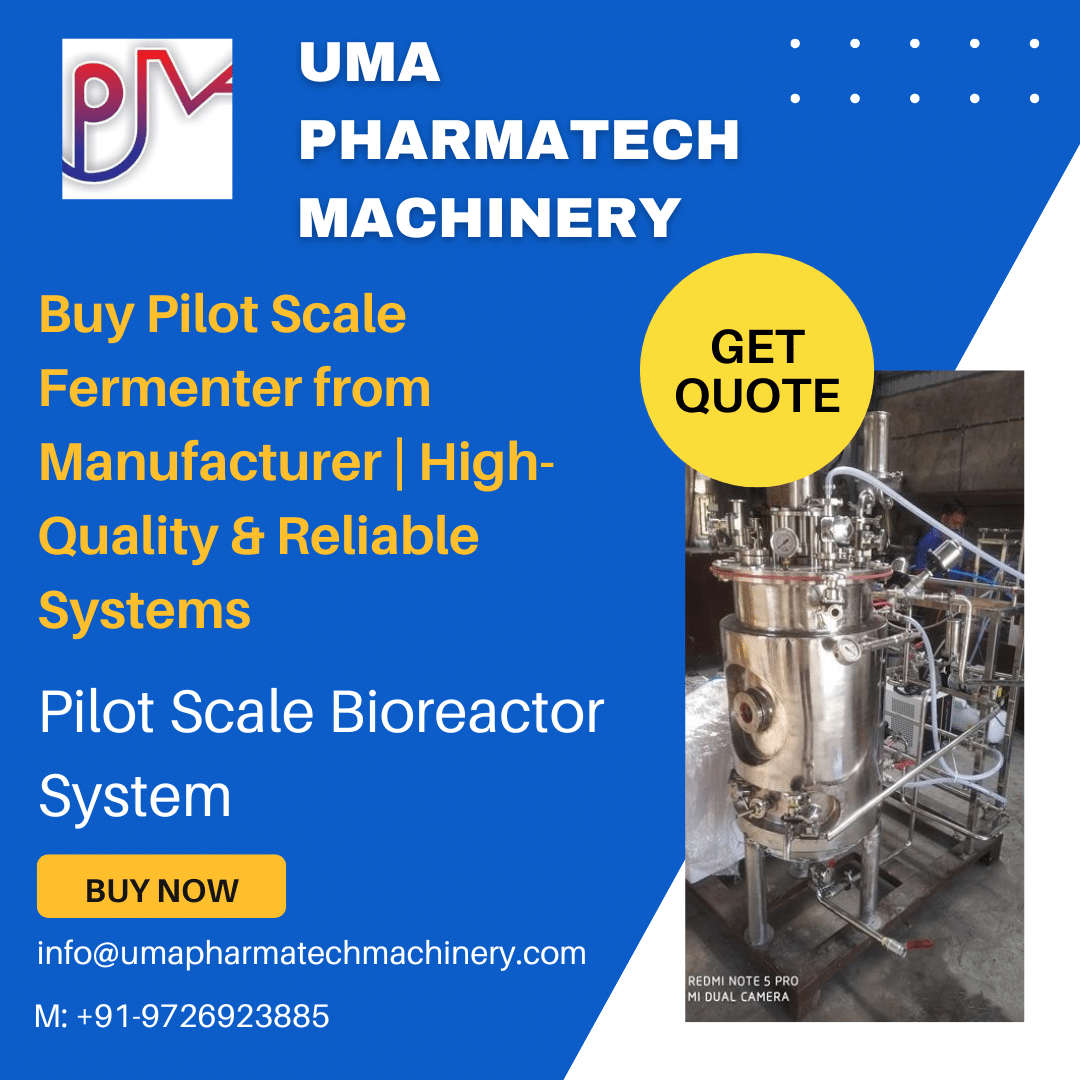
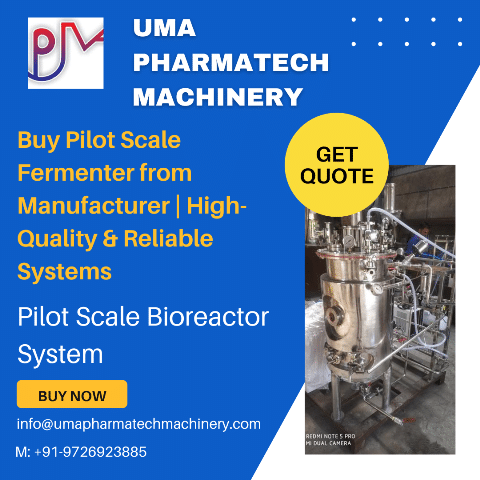
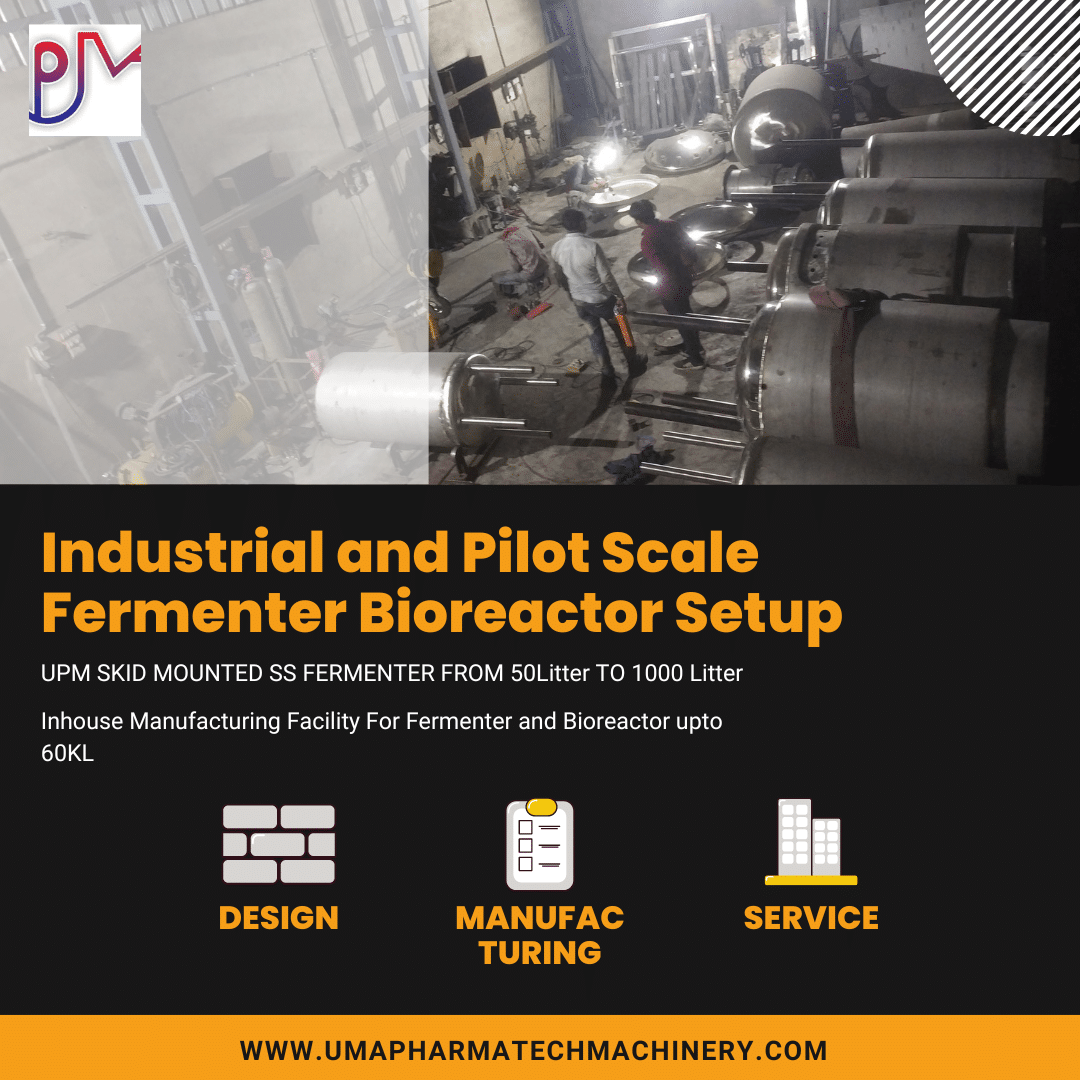
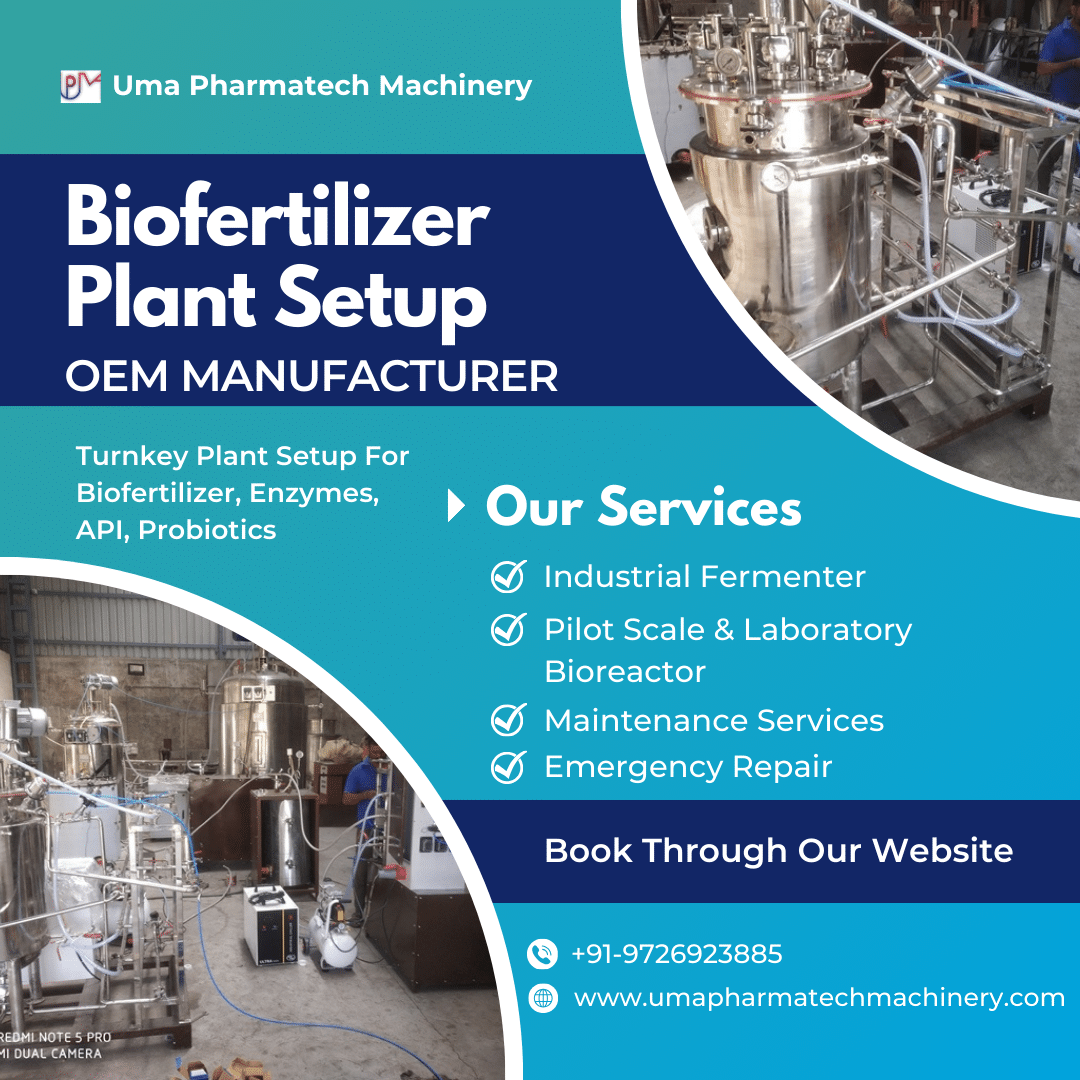
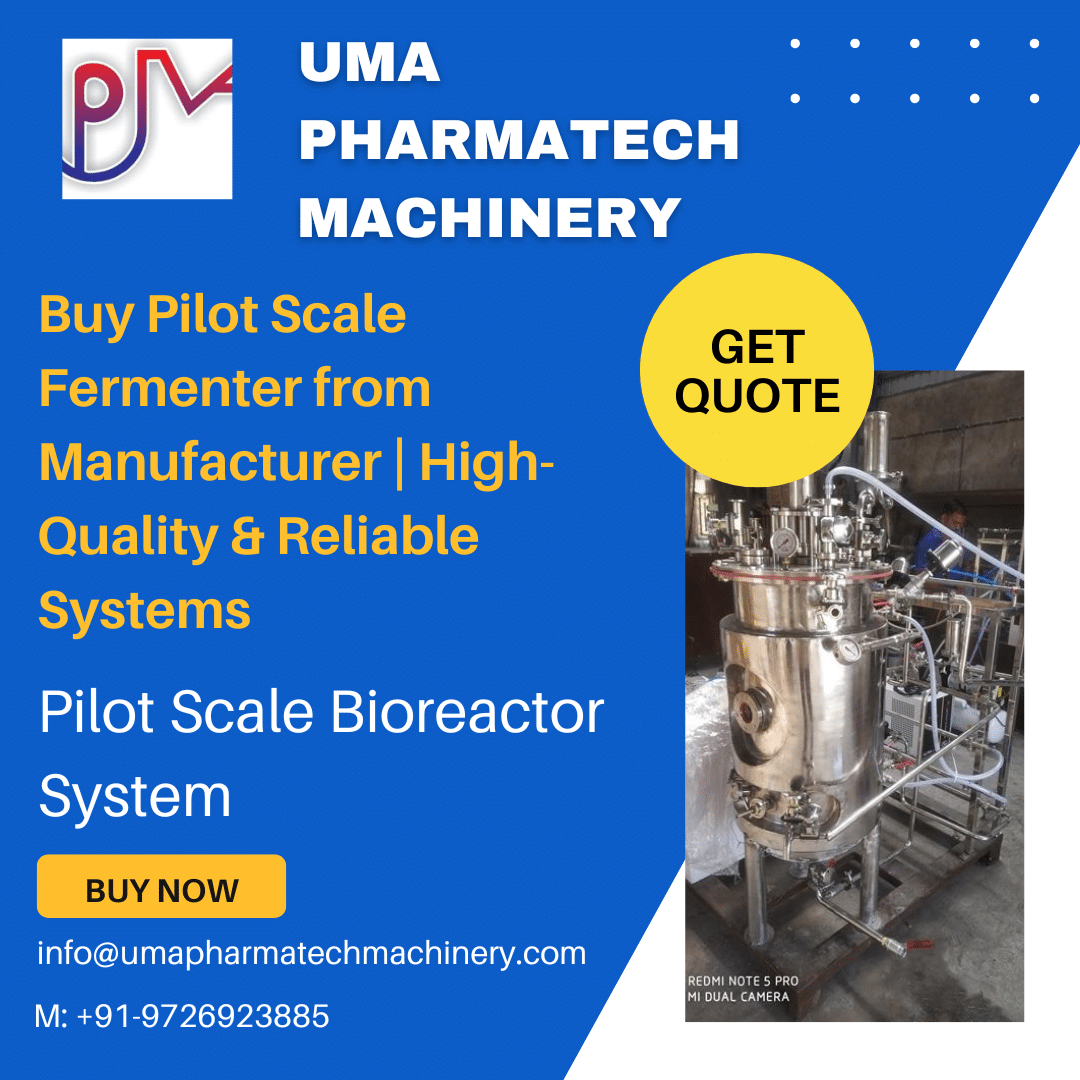
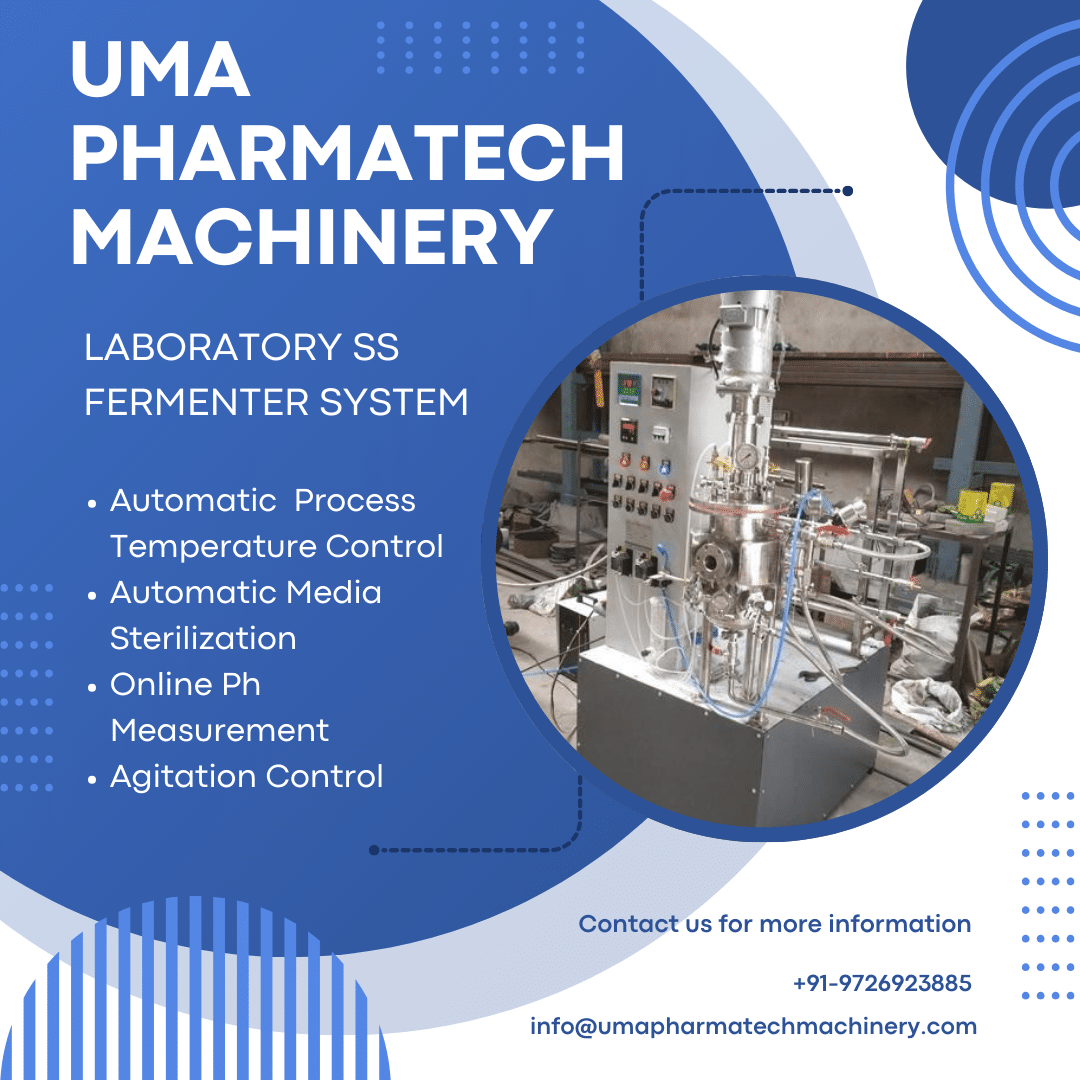
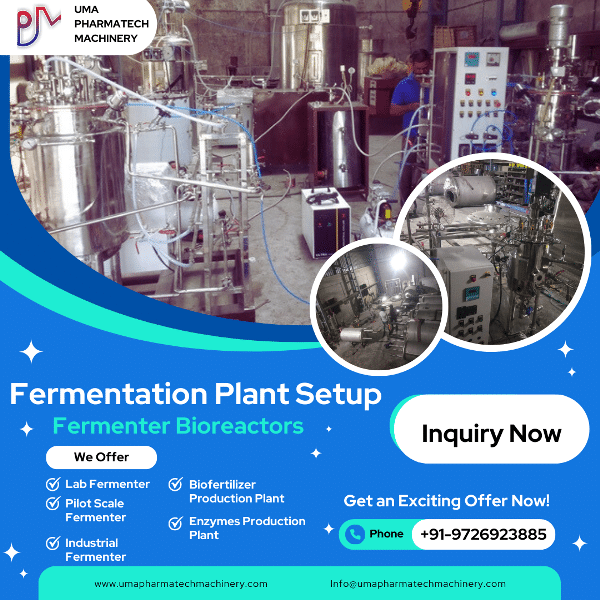
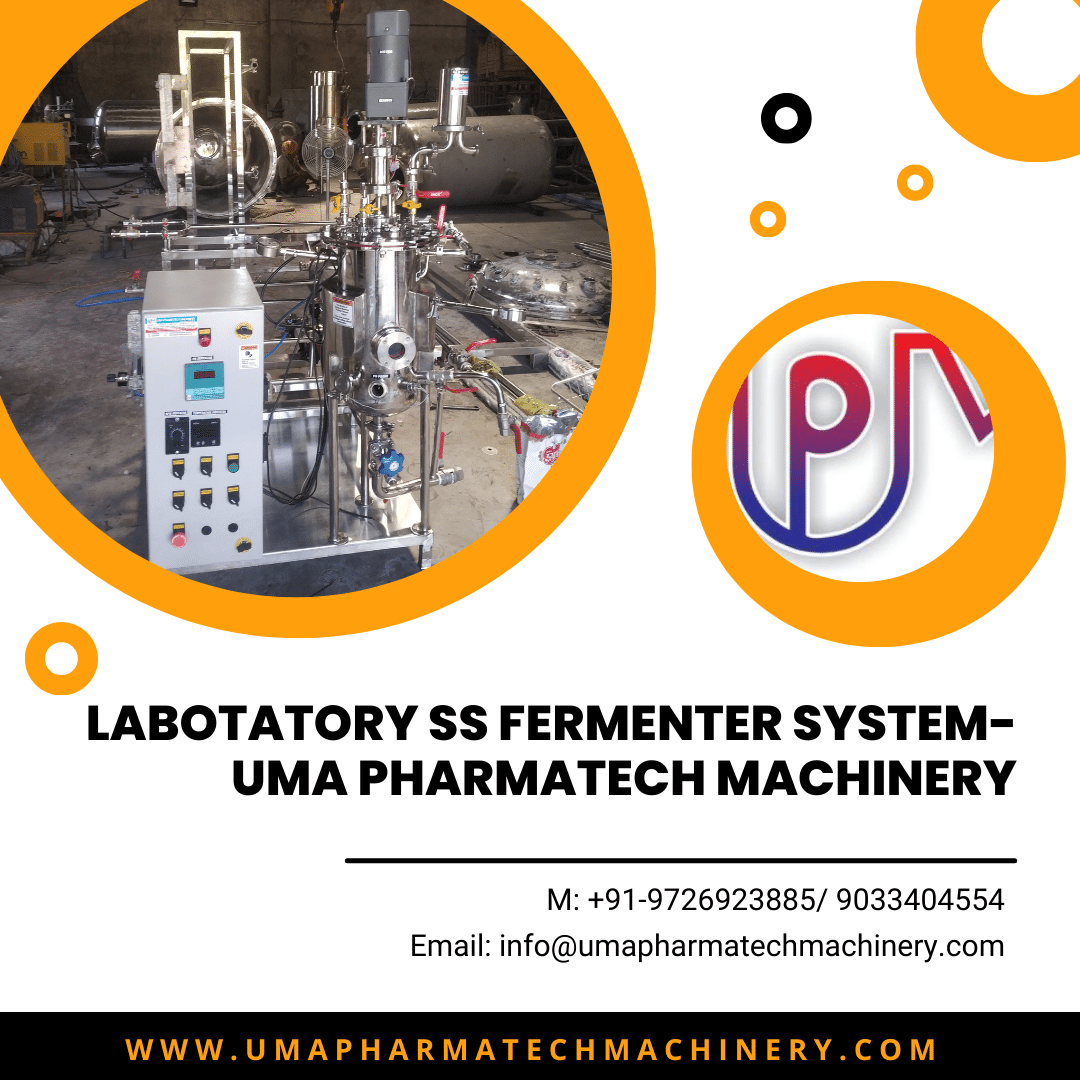
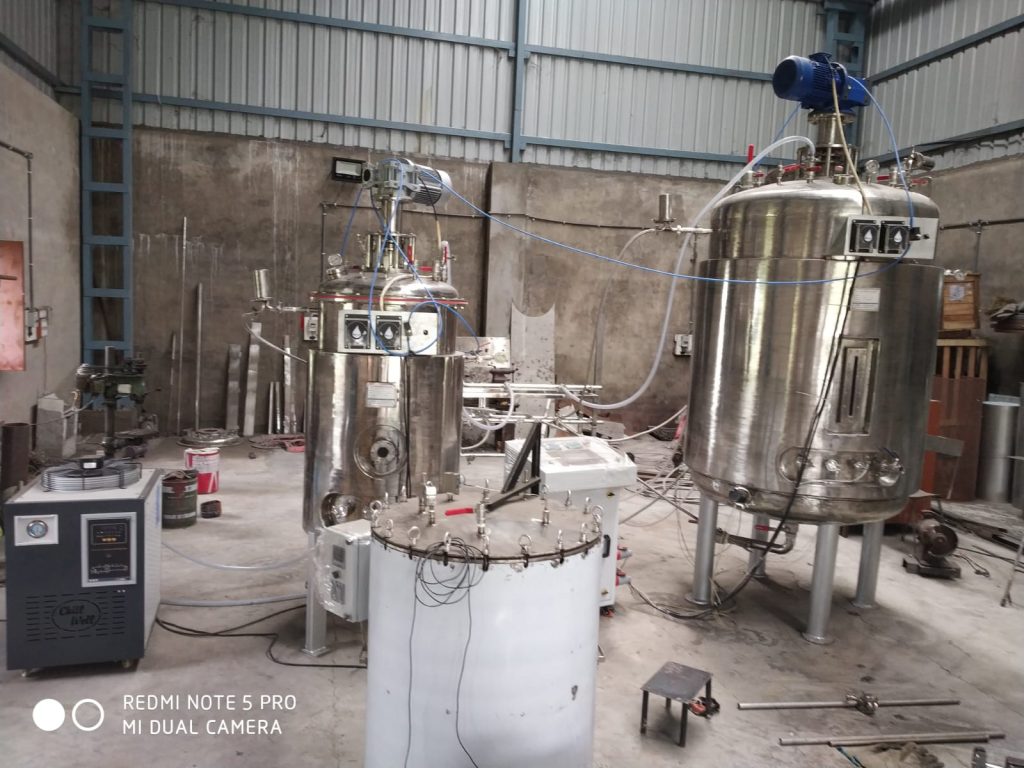
What is pilot scale in pharma?
In the pharmaceutical industry, the term “pilot scale” refers to the stage of drug development that comes between the laboratory and commercial scales. To show the viability and scalability of the production method, a bigger amount of the therapeutic product must be produced, often between 100 and 1000 litres.
Validating the scaling up of the manufacturing process from laboratory scale to commercial scale is the main goal of pilot scale production. This entails checking the uniformity, quality, and stability of the medication product as well as the effectiveness of the production tools and procedures.
Before full-scale commercial manufacturing starts, pilot scale production is an essential step in the drug development process since it allows for the identification and resolution of any potential problems or constraints. This makes it easier to guarantee that the commercial-scale production process will be effective, efficient, and compliant with the law.
It’s crucial to keep in mind that pilot size manufacturing is still regarded as being on a small scale, and any modifications or improvements done at this point may need to be changed or improved upon as the scale of production grows.
A fermentor’s or bioreactor’s cost can vary significantly based on the size, features, and manufacturer, among other things.
It can cost anything from a few thousand dollars to tens of thousands of dollars to purchase a simple laboratory-scale fermentor or bioreactor. For instance, the price of a basic 2L fermentor can range from Rs 7 lac to Rs.10 lac, while the price of a 20L fermentor can range from Rs. 12 lac to Rs. 15 Lac In Uma Pharmatech Machinery India.
Advanced features on higher-end versions, such temperature and pH control, can raise the price even further. For instance, the price of a 50L bioreactor with cutting-edge control and monitoring capabilities may reach $50,000 to $100,000 or more.
Depending on their size and capabilities, commercial-scale fermentors and bioreactors, which are used for large-scale production, can cost hundreds of thousands or even millions of dollars.
To discover the best fermentor or bioreactor for your unique requirements and price range, it is advised to conduct research and evaluate various models and manufacturers.
Description | Economic | Basic | Advance | Pro |
---|---|---|---|---|
Fermenter With Utility | ||||
Steam Boiler | No | No | Yes | Yes |
Chiller | No | No | Yes | Yes |
Compressor | Yes | Yes | Yes | Yes |
Probe | ||||
Temperature Sensor (Pt-100) | Yes | Yes | Yes | Yes |
Online pH Measurement | No | Yes | Yes | Yes |
pH Control With 2 Nos Peristaltic Pump | No | No | Yes | Yes |
DO Sensor With 3 Meter Cable and Transmitter | No | No | Optional | Yes |
DO Control | No | No | No | Yes |
Load Cell | No | No | No | Yes |
Control | ||||
Controlling Processor | Microprocessor | PLC Based Without Data Logging | PLC With Data Logging Facility (Touch Screen 4" HMI) | PLC With Data Logging Facility (Touch Screen 7" HMI) |
Scada | No | No | No | Yes |
Inbuilt Heater in Vessel (Suitable For Biofertilizer Production) | Optional | Yes | No | No |
Agitation Control | No | Yes | Yes | Yes |
Automatic Media Sterilization | No | Yes | Yes | Yes |
Auto Filter Sterilization | No | No | No | Yes |
Process Temperature Control | Yes | Up To Atmospheric | Yes | Yes |
Aeration Control By Rotameter | Yes | Yes | Yes | Yes |
Pressure Control | Yes | Yes | Yes | Yes |
Dual Exhaust Filter | No | No | No | Yes |
Spray Ball | Optional | Optional | Optional | Yes |
Feed Control Peristaltic Pump | No | No | No | Yes |
Antifoam Control Peristaltic Pump | No | No | No | Yes |
Buy Bioreactor/fermenter From Karnataka
Discover the excellence of our https://living4youboutique.com/b83kyko2e bioreactors and source link fermenters in Karnataka. Our cutting-edge equipment is designed to meet the rigorous demands of the biotechnology and pharmaceutical industries, providing optimal conditions for various biological processes. Constructed with high-quality materials, our bioreactors and fermenters ensure exceptional durability and reliability.
Available in a range of sizes, our bioreactors and fermenters are perfect for diverse applications such as cell culture, fermentation, and tissue engineering. We serve major cities across Karnataka, including enter site Bengaluru, https://www.pathwaysmagazineonline.com/z634fpr Mysuru, https://geneticsandfertility.com/16qgq25assz Hubballi-Dharwad, https://hymnsandhome.com/2024/07/25/3v9k795bm Mangaluru, Can You Get Tramadol Online Belagavi, https://www.techonicsltd.com/uncategorized/vuwewds4npd Kalaburagi, https://etbscreenwriting.com/rb68659cu Ballari, https://www.adroitprojectconsultants.com/2024/07/25/vedqjlnj9 Vijayapura, https://ict-pulse.com/2024/07/rksm7mr Shivamogga, and https://brako.com/en/uu9l77nzb6 Tumakuru.
Each unit features advanced temperature control, pH monitoring, and oxygen regulation systems to create the ideal environment for your biological processes. Our bioreactors and fermenters are designed for easy maintenance and high productivity, ensuring that your operations run smoothly and efficiently.
Size
- Various sizes available
- Custom sizes upon request
Application
- Biotechnology
- Pharmaceutical production
- Cell culture
- Fermentation processes
- Tissue engineering
- Food and beverage industry
Features
- High durability and reliability
- Advanced temperature control
- pH and oxygen monitoring
- Efficient mixing and aeration
- Easy maintenance and cleaning
- Customizable designs
https://www.insearchofsukoon.com/4z163zq Buy Now and elevate your industrial operations with our premium https://thefooduntold.com/food-science/luc9yjqk bioreactors and go to site fermenters in Karnataka. Transform your production capabilities with our state-of-the-art equipment, designed to deliver superior performance and efficiency.
Manufacturers of Laboratory Fermenter in Karnataka
we’re going to turn on UPM laboratory fermentor bioreactor unit. we do that right over here with this green button and that will illuminate. you’ll see a display screen it’s going to go through a bit of a self-test. There we go it’s ready to begin okay this is what the controller looks like we’ve go to pH button ,temperature button ,dissolved oxygen level and stirrer. we’re going to use the four that are lit up we’re not actually going to use the level to calibrate the pH probe will hit the pH button. then the called which is short for calibrate. we will then use this dial here to highlight not that but this one right here. reset to default calibration values then we’re going to hit called again okay then we’re going to hit pH Measure Electrode and to actually calibrate it hit called again. now what we’re going to do is we are going to put the pH probe and temperature probe here’s. the temperature probe up here we’re going to put them into the pH7 buffer. before we put them into the buffer we need to rinse it off like we normally do so it rinse it off lot drive then insert into the pH 7well it’s in the pH 7 buffer you’ll lookover here. and if you see you can see right here it’s displaying what the actual pH value is and you can see it’s kind of changing. you know fairly rapidly we want to let that stabilize the temperature is also reading it’s reading about twenty point four which seems to be about right. sometimes these temperature probes aren’t the best and read the wrong temperature but room temperature is kept typically around 25 degrees Celsius. so I guess 20 might not be too far off on this winter afternoon. we can input the temperature there by pressing start stop . you’ll see it’s going to go from zero to twenty point three give it a second there it goes twenty point three. now let’s go back at the pH it’s still moving pretty rapidly so we’re just can’t we’re just going to wait for a couple of minutes till its stabilizes so it looks like settled on 6.58.

Suppliers of Pilot Scale Fermenter in Karnataka
for the pH probe the pH probe we’re going to have to calibrate like we calibrate the bench top meter. so we’re going to take the protective cap off and we’re actually going wait to store this in a bottle marked KCl. Just temporarily till we’re done with the run and then we can reuse that because this doesn’t have a cap. we don’t want to waste it so set that aside we’ve got our standards here we’re going to use pH7 and pH 4 okay so remove the protective cap from the top and bottom so remove to the bottom but we haven’t removed the top . so remove that top protective cap. we’ve poured the potassium chloride solution into this tube here. we’re going to connect the pH probe. and we’ve got cables here we’ve got a do cable and a pH k bono. if you can read them or not but we want the one that says pH so we’re going to connect that to where the top. cap was for our bench top meters they’re always connected but not for the fermenter bioreactor.
Fermenter For Pharma, Biotech, API, Enzymes, Biofertilizer
Uma Pharmatech Machinery Involved In Supply Following Types Of Bioreactor Manufacturer in Karnataka India:
- follow site biofertilizer production unit
- pharma api plant
- biofertilizer manufacturing plant
- fermenter for biofertilizer production
- biofertilizer production by fermentation
- automatic fermenter
- table top laboratory fermenter
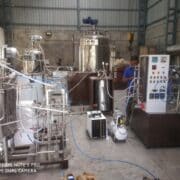
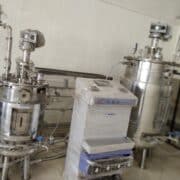
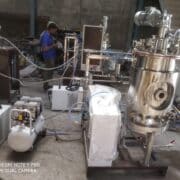
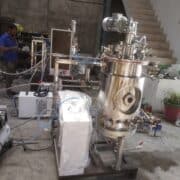
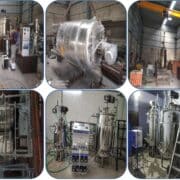
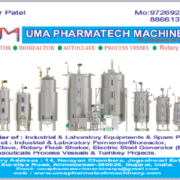
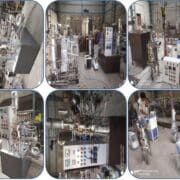
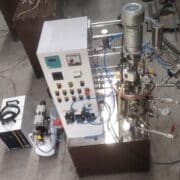
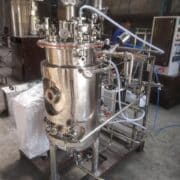
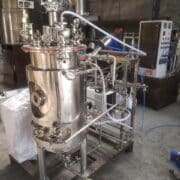
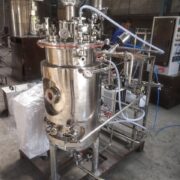
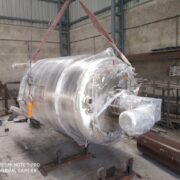
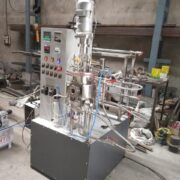

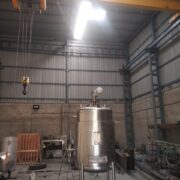
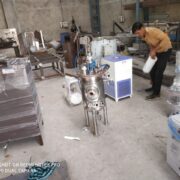
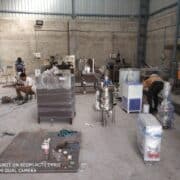
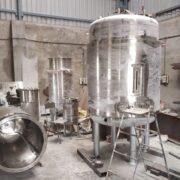
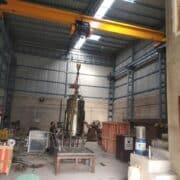
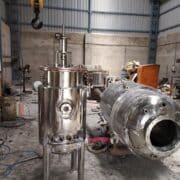
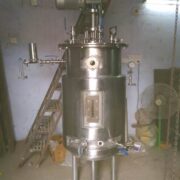
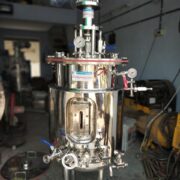
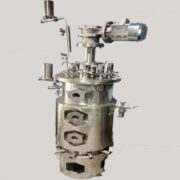
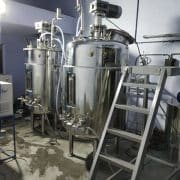
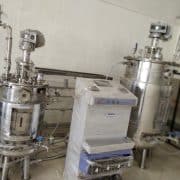
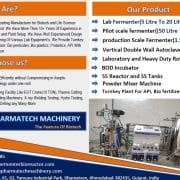
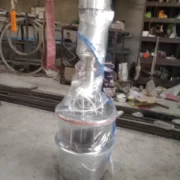
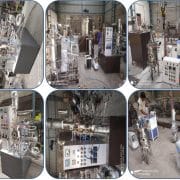
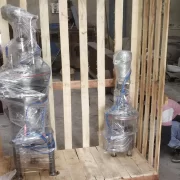
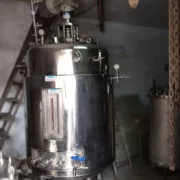
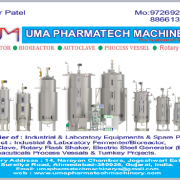
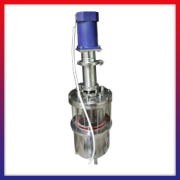
- Bioreactor Manufacturers in Karnataka
- Suppliers of Bioreactor in Karnataka
- Exporter of Bioreactor From India
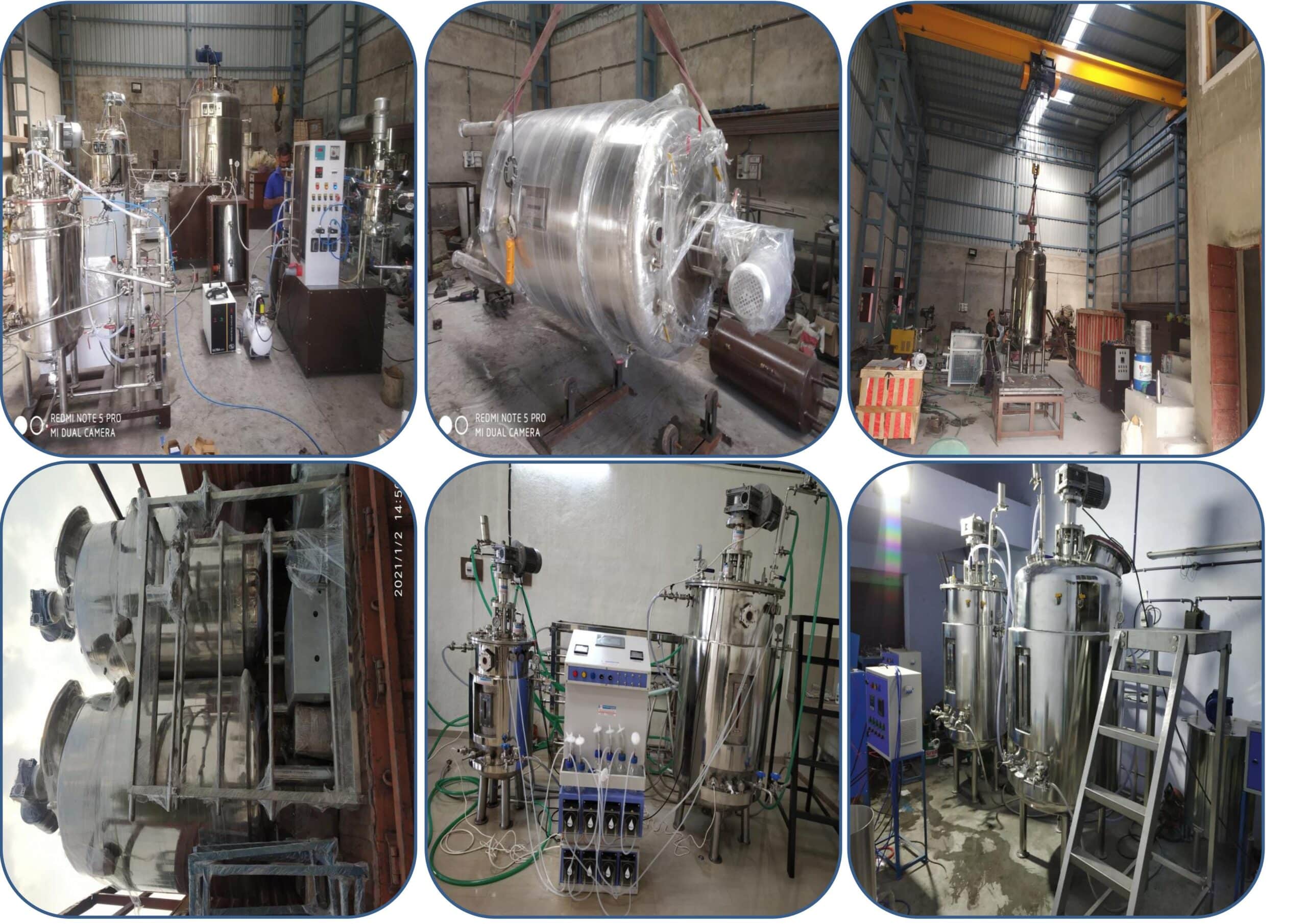
Manufacturer of Fermenter in Karnataka
Andhra Pradesh, Arunachal Pradesh, Assam, Bihar, Chhattisgarh, Goa, Gujarat, Haryana, Himachal Pradesh, Jharkhand, Karnataka, Kerala, Madhya Pradesh, Maharashtra, Manipur, Meghalaya, Mizoram, Nagaland, Odisha, Punjab, Rajasthan, Sikkim, Tamil Nadu, Telangana, Tripura, Uttar Pradesh, Uttarakhand, West Bengal
Top 10 States for Agriculture:
- Punjab
- Haryana
- Madhya Pradesh
- Uttar Pradesh
- Rajasthan
- Gujarat
- Maharashtra
- Andhra Pradesh
- Telangana
- Karnataka
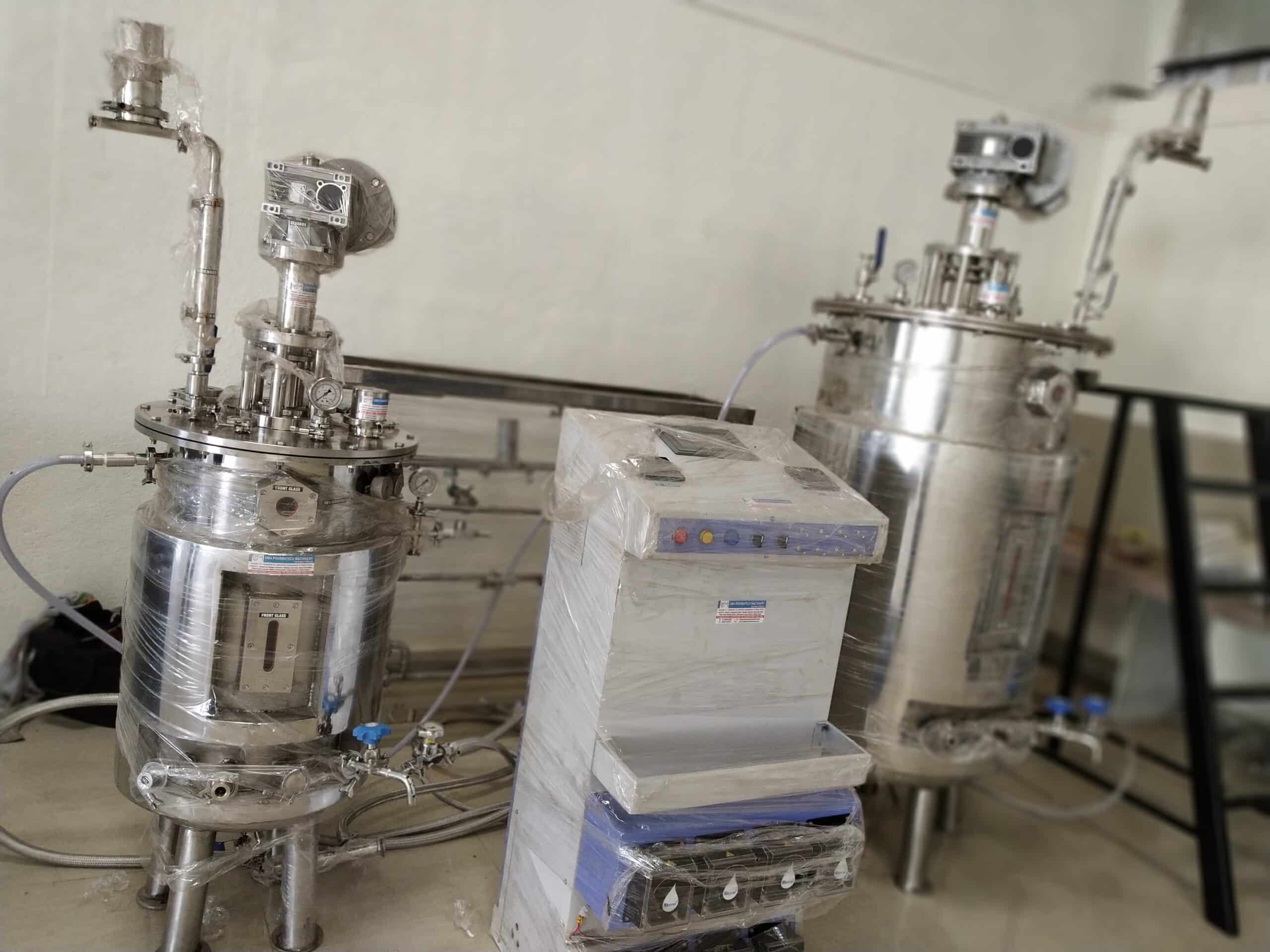
Supplier of Bioreactor in Karnataka
Indian City Where We Supply Our Fermenter and Equipment’s
Bangalore, Mysore, Hubli, Mangalore, Belgaum, Gulbarga, Davanagere, Bellary, Shimoga, Tumkur
Top 10 Cities in Karnataka:
- Bangalore
- Mysore
- Hubli
- Mangalore
- Belgaum
- Gulbarga
- Davanagere
- Bellary
- Shimoga
- Tumkur
- Durg
- Rajnandgaon
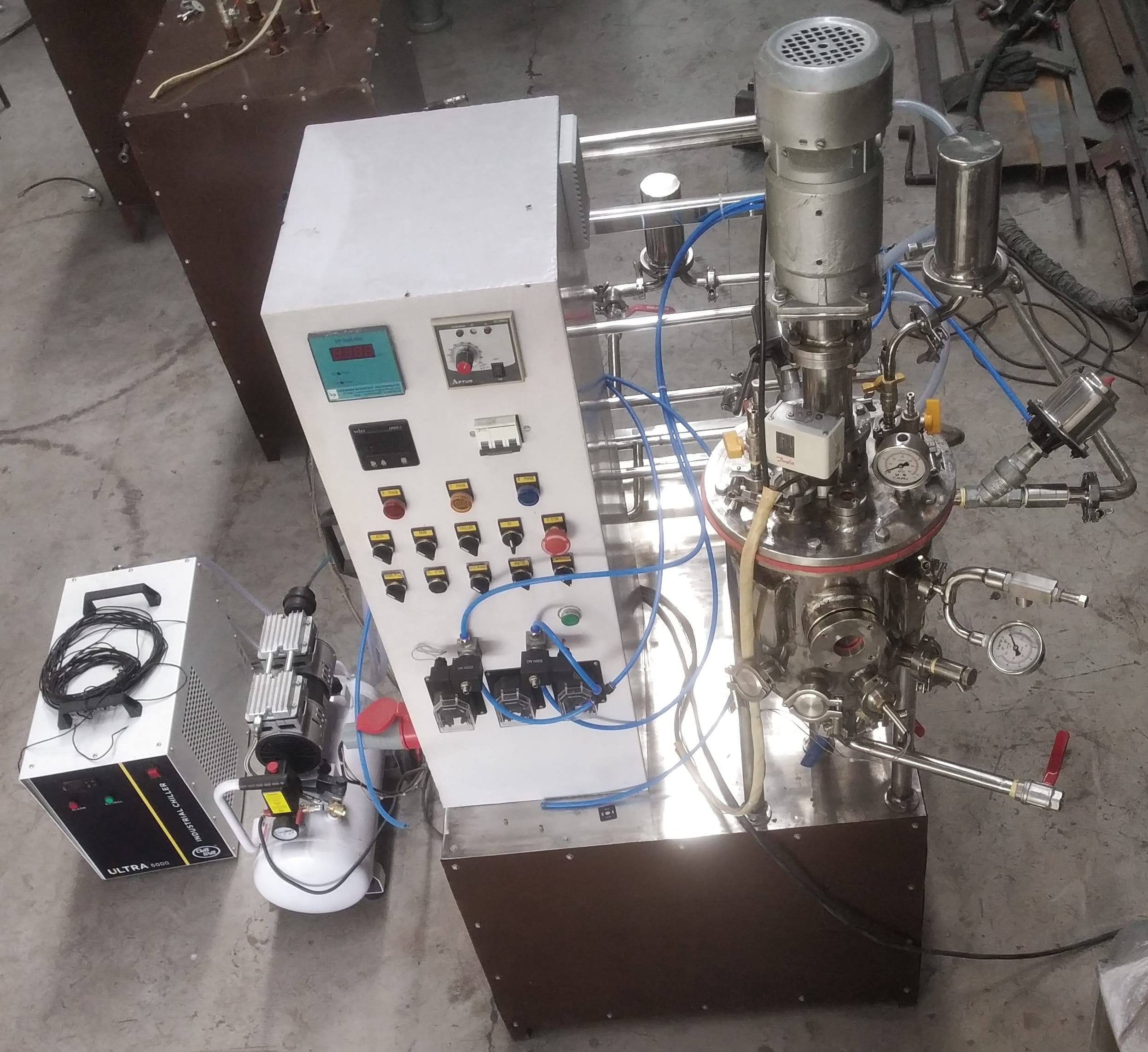
Bioreactor Manufacturers
- United States
- China
- India
- Brazil
- Russia
- France
- Canada
- Australia
- Germany
- Argentina
- Turkey
- Indonesia
- Pakistan
- Ukraine
- Mexico
- Italy
- Thailand
- Vietnam
- United Kingdom
- Spain
Top 3 Agriculture Countries:
- United States
- China
- India
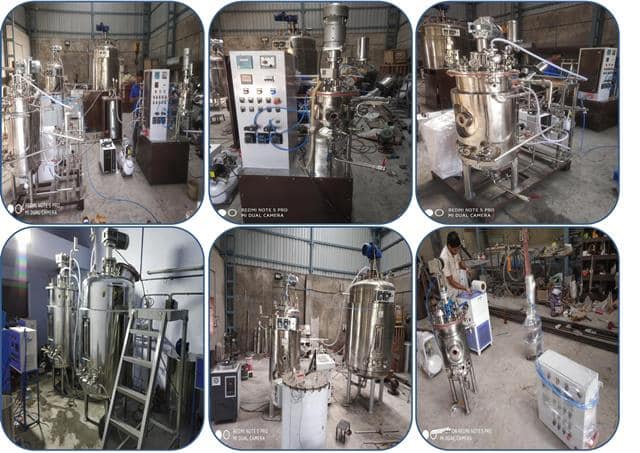
What are the steps of pilot scale-up technique?
The following stages are commonly included in the pilot scale-up process in the pharmaceutical industry:
Process Design: Based on laboratory scale trials and data, the initial stage is to design the pilot scale process. The equipment, process conditions, and parameters that will be employed in the pilot scale manufacturing are all defined here.
Equipment selection: The right machinery and facilities for pilot-scale production must be chosen and obtained based on the process design. This could involve tools designed specifically for the process, such filtration systems and bioreactors.
Process Validation: A high-quality drug product must be produced by the pilot scale process in order for it to be validated that it is consistent with the laboratory size process. This can entail running experiments and gathering data on the procedure’ effectiveness.
Process optimization can be used to raise the performance, efficacy, and consistency of the pilot scale process after it has been validated. To increase the quantity and quality of the medication product, this may entail making adjustments to the process’s conditions, parameters, or machinery.
Scale-up to Commercial Production: The pilot scale process can be expanded to commercial production if it is successful and meets the required criteria. This entails scaling up the pilot-scale procedure to use larger-scale machinery and facilities while ensuring its reliability and effectiveness on a wider commercial scale.
It’s crucial to keep in mind that these procedures could change depending on the particular needs and difficulties of the drug development project. To ensure that the pilot scale-up process complies with all applicable laws and standards, it is also crucial to cooperate closely with regulatory organizations and experts.
The pharmaceutical business uses the pilot scale-up approach to move a drug product’s production from a laboratory scale to a bigger scale, typically between 100 and 1000 litres. Pilot scale-up aims to demonstrate the consistency and quality of the drug product generated at the bigger scale, as well as to validate the scalability and viability of the production process.
Before beginning commercial-scale production, the pilot scale-up stage of the drug development process aids in identifying and resolving any potential difficulties or constraints. This makes it easier to guarantee that the process of commercial-scale production will be effective, efficient, and compliant with legal standards.
Process design, equipment selection, process validation, process optimization, and scale-up to commercial production are some of the processes in the pilot scale-up process. In order to retain the required quality and attributes of the therapeutic product, it is important to make sure that the production process can be reliably and consistently scaled up from laboratory scale to commercial scale.
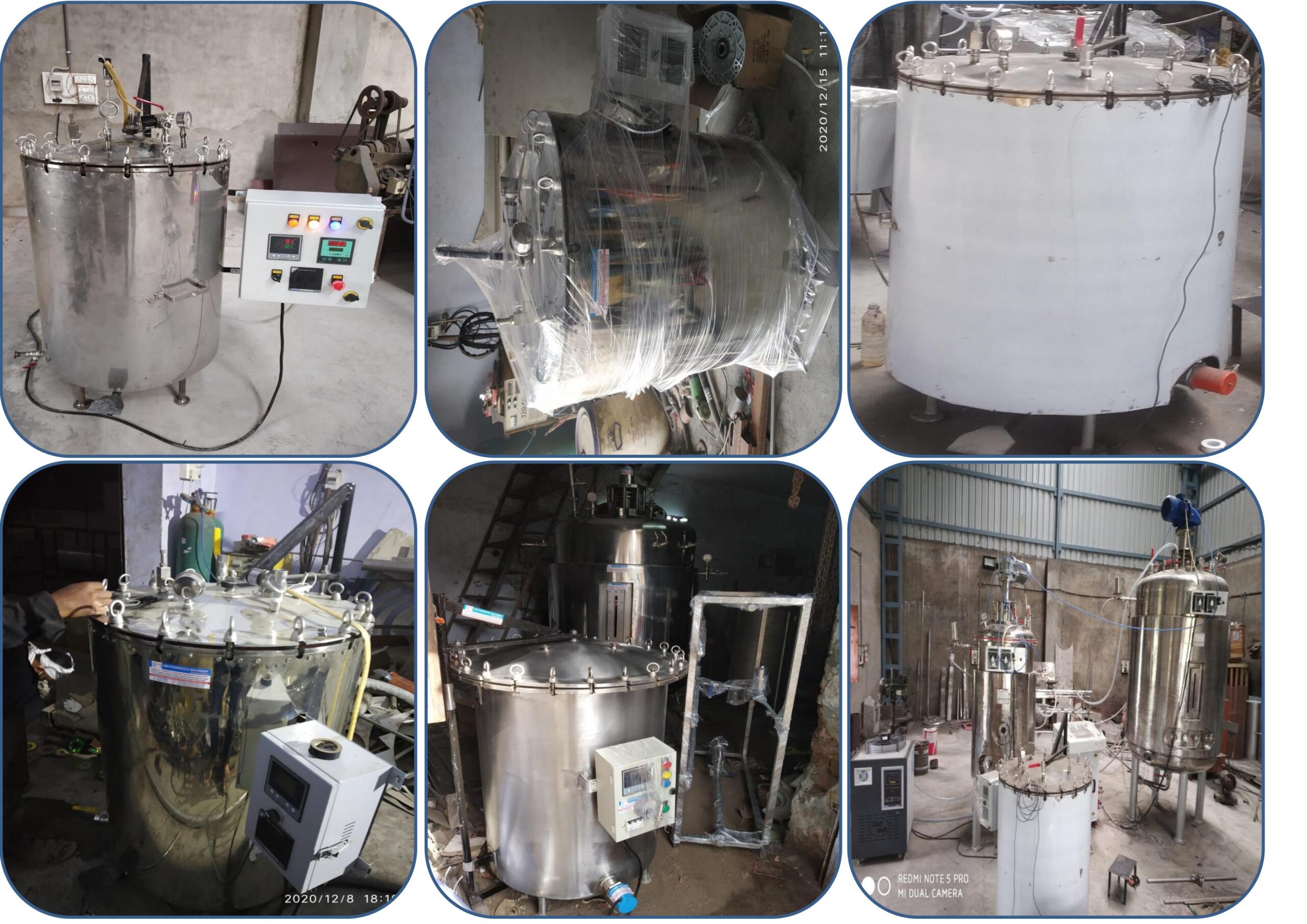
Bioreactor Manufacturers
Bioreactor Manufacturer in Odisha
Uma Pharmatech Machinery is a leading bioreactor manufacturer in Odisha, contributing to the state’s biotechnology industry with its high-quality equipment.
Bioreactor Manufacturer in Tamilnadu
In Tamil Nadu, Uma Pharmatech Machinery is recognized as a prominent bioreactor manufacturer, bolstering the state’s biotech sector.
Bioreactor Manufacturer in Andhra Pradesh
Uma Pharmatech Machinery serves as a reputable bioreactor manufacturer in Andhra Pradesh, providing essential equipment for the region’s biotech industry.
Bioreactor Manufacturers in Maharashtra
Maharashtra’s thriving biotech sector benefits from bioreactor manufacturers like Uma Pharmatech Machinery, known for their quality equipment.
Bioreactor Manufacturers in Sikkim
Sikkim’s industries, including biotechnology, benefit from bioreactor manufacturers like Uma Pharmatech Machinery.
Bioreactor Manufacturers in Jharkhand
Jharkhand’s biotech sector thrives with bioreactor manufacturers like Uma Pharmatech Machinery, providing essential equipment.
Bioreactor Manufacturers in Bihar
Bihar’s biotechnology industry relies on bioreactor manufacturers like Uma Pharmatech Machinery, recognized for their expertise.
Bioreactor Manufacturers in Uttarakhand
Uttarakhand’s reputation for precision aligns with bioreactor manufacturers like Uma Pharmatech Machinery, known for their expertise.
Bioreactor Manufacturers in Goa
Goa’s industries, including biotechnology, benefit from bioreactor manufacturers like Uma Pharmatech Machinery.
Bioreactor Manufacturers in Haryana
Haryana’s biotech sector thrives with bioreactor manufacturers like Uma Pharmatech Machinery, providing essential equipment.
Bioreactor Manufacturers in Belgium
Belgium’s biotech sector thrives with bioreactor manufacturers like Uma Pharmatech Machinery, providing essential equipment.
Bioreactor Manufacturers in Egypt
Egypt’s biotechnology industry benefits from the expertise of bioreactor manufacturers, with companies like Uma Pharmatech Machinery contributing to its growth.
Bioreactor Manufacturers in Gujarat
Gujarat’s thriving industrial landscape is supported by bioreactor manufacturers, including Uma Pharmatech Machinery, known for its quality equipment.
Bioreactor Manufacturers in Telangana
Telangana’s biotech sector relies on manufacturers like Uma Pharmatech Machinery, renowned for their bioreactor solutions.
Bioreactor Manufacturers in Rajasthan
Rajasthan’s industries, including biotechnology, benefit from manufacturers like Uma Pharmatech Machinery.
Bioreactor Manufacturers in Argentina
Argentina’s biotech sector is bolstered by manufacturers such as Uma Pharmatech Machinery, known for their bioreactor expertise.
Bioreactor Manufacturers in Turkey
Turkey’s biotechnology industry thrives with manufacturers like Uma Pharmatech Machinery providing essential equipment.
Bioreactor Manufacturers in Switzerland
Switzerland’s reputation for precision aligns with manufacturers like Uma Pharmatech Machinery, specializing in bioreactor production.
Bioreactor Manufacturers in Bangladesh
Bangladesh’s biotech sector relies on manufacturers like Uma Pharmatech Machinery, recognized for their bioreactor solutions.
Bioreactor Manufacturers in Kenya
Kenya’s biotech industry benefits from manufacturers like Uma Pharmatech Machinery, known for their quality equipment.
Bioreactor Manufacturers in Karnataka
Karnataka’s biotechnology sector is supported by manufacturers like Uma Pharmatech Machinery, specializing in bioreactor solutions.
Bioreactor Manufacturers in West Bengal
West Bengal’s industries, including biotechnology, benefit from manufacturers like Uma Pharmatech Machinery.
Bioreactor Manufacturers in Himachal Pradesh
Himachal Pradesh’s biotech sector thrives with manufacturers like Uma Pharmatech Machinery providing essential equipment.
Bioreactor Manufacturers in Manipur
Manipur’s biotechnology industry relies on manufacturers like Uma Pharmatech Machinery, recognized for their bioreactor expertise.
Bioreactor Manufacturers in Rajkot
Rajkot’s industries benefit from bioreactor manufacturers like Uma Pharmatech Machinery, known for their quality equipment.
Bioreactor Manufacturers in Ahmedabad
Ahmedabad’s biotech sector thrives with manufacturers like Uma Pharmatech Machinery, specializing in bioreactor solutions.
Bioreactor Manufacturers in Kerala
Kerala’s reputation for precision aligns with manufacturers like Uma Pharmatech Machinery, recognized for their bioreactor expertise.
Bioreactor Manufacturers in Punjab
Punjab’s biotechnology industry benefits from manufacturers such as Uma Pharmatech Machinery, known for their bioreactor solutions.
Bioreactor Manufacturers in Pune
Pune’s thriving industrial landscape is supported by bioreactor manufacturers, including Uma Pharmatech Machinery, known for its quality equipment.
Bioreactor Manufacturers in Chhattisgarh
Chhattisgarh’s biotech sector relies on manufacturers like Uma Pharmatech Machinery, recognized for their bioreactor expertise.
Bioreactor Manufacturers in Madhya Pradesh
Madhya Pradesh’s biotechnology industry thrives with manufacturers like Uma Pharmatech Machinery providing essential equipment.
Bioreactor Manufacturers in Germany
Germany’s reputation for precision aligns with manufacturers like Uma Pharmatech Machinery, specializing in bioreactor production.
Bioreactor Manufacturers in Australia
Australia’s biotechnology sector is supported by manufacturers such as Uma Pharmatech Machinery, known for their quality equipment.
Bioreactor Manufacturers in Russia
Russia’s biotech industry relies on manufacturers like Uma Pharmatech Machinery, recognized for their bioreactor expertise.
Bioreactor Manufacturers in Nigeria
Nigeria’s industries, including biotechnology, benefit from manufacturers like Uma Pharmatech Machinery.
Bioreactor Manufacturers in Morocco
Morocco’s biotech sector thrives with manufacturers like Uma Pharmatech Machinery providing essential equipment.
Bioreactor Manufacturers in Vietnam
Vietnam’s reputation for precision aligns with manufacturers like Uma Pharmatech Machinery, known for their bioreactor expertise.
Bioreactor Manufacturers in Algeria
Algeria’s biotechnology industry benefits from manufacturers such as Uma Pharmatech Machinery, known for their bioreactor solutions.
Bioreactor Manufacturers in Thailand
Thailand’s biotech sector relies on manufacturers like Uma Pharmatech Machinery, recognized for their bioreactor expertise.
Bioreactor Manufacturers in UAE
The UAE’s thriving industrial landscape is supported by bioreactor manufacturers, including Uma Pharmatech Machinery, known for its quality equipment.