What is a Bioreactor?
Bio fermenters-Fundamental Idea
In the biotechnology and pharmaceutical sectors, bio fermenter System are frequently employed for the mass manufacture of numerous bioproducts, including enzymes, antibiotics, and vaccines. We shall go into great detail about biofermentors in this thorough manual, including their definition, kinds, elements, processes, and applications.
FERMENTER MANUFACTURER IN HARYANA
Uma Pharmatech Machinery Designers aware of your request and are prepared to provide you an article that has been optimized for SEO in order to help you outrank your competitor’s website for the same set of keywords. For the purpose of educating and informing your target audience, our post will be thorough and present in-depth information about bio fermenters.
Fermenter and Bioreactor Manufactureres in Haryana
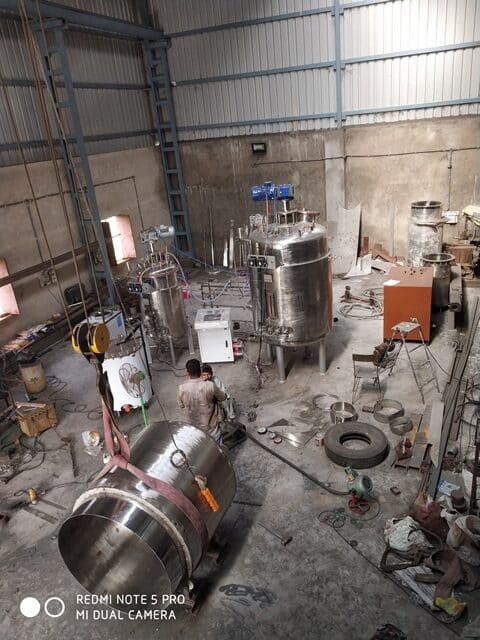
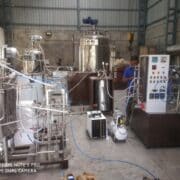
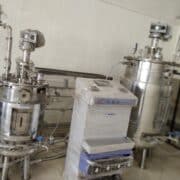
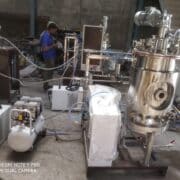
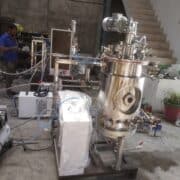
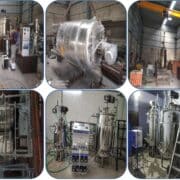
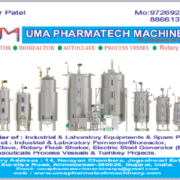
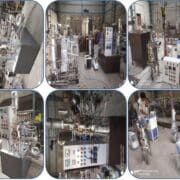
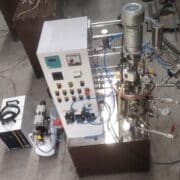
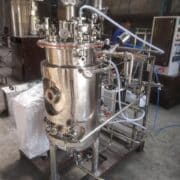
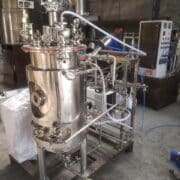
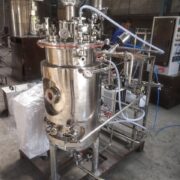
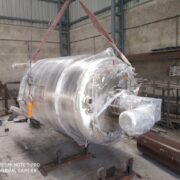
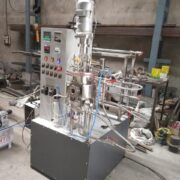

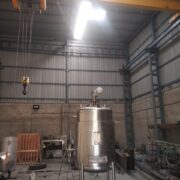
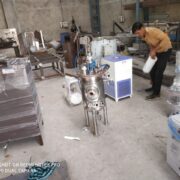
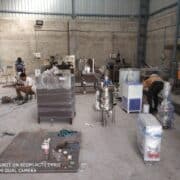
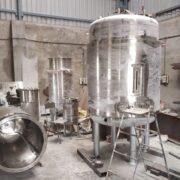
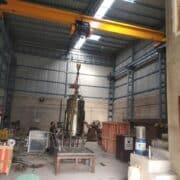
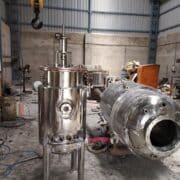
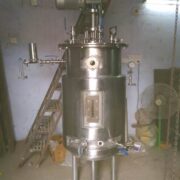
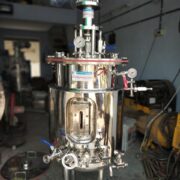
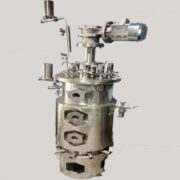
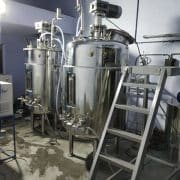
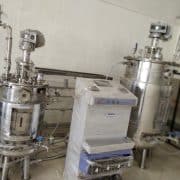
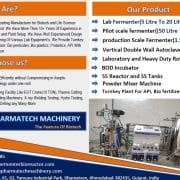
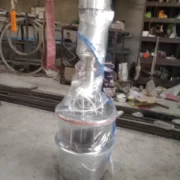
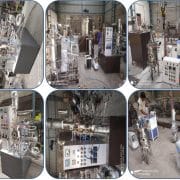
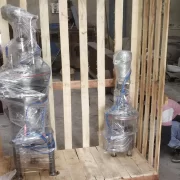
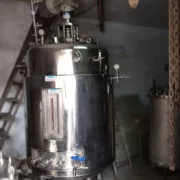
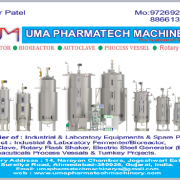
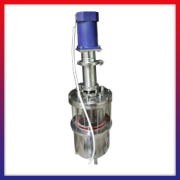
Description | Economic | Basic | Advance | Pro |
---|---|---|---|---|
Fermenter With Utility | ||||
Steam Boiler | No | No | Yes | Yes |
Chiller | No | No | Yes | Yes |
Compressor | Yes | Yes | Yes | Yes |
Probe | ||||
Temperature Sensor (Pt-100) | Yes | Yes | Yes | Yes |
Online pH Measurement | No | Yes | Yes | Yes |
pH Control With 2 Nos Peristaltic Pump | No | No | Yes | Yes |
DO Sensor With 3 Meter Cable and Transmitter | No | No | Optional | Yes |
DO Control | No | No | No | Yes |
Load Cell | No | No | No | Yes |
Control | ||||
Controlling Processor | Microprocessor | PLC Based Without Data Logging | PLC With Data Logging Facility (Touch Screen 4" HMI) | PLC With Data Logging Facility (Touch Screen 7" HMI) |
Scada | No | No | No | Yes |
Inbuilt Heater in Vessel (Suitable For Biofertilizer Production) | Optional | Yes | No | No |
Agitation Control | No | Yes | Yes | Yes |
Automatic Media Sterilization | No | Yes | Yes | Yes |
Auto Filter Sterilization | No | No | No | Yes |
Process Temperature Control | Yes | Up To Atmospheric | Yes | Yes |
Aeration Control By Rotameter | Yes | Yes | Yes | Yes |
Pressure Control | Yes | Yes | Yes | Yes |
Dual Exhaust Filter | No | No | No | Yes |
Spray Ball | Optional | Optional | Optional | Yes |
Feed Control Peristaltic Pump | No | No | No | Yes |
Antifoam Control Peristaltic Pump | No | No | No | Yes |
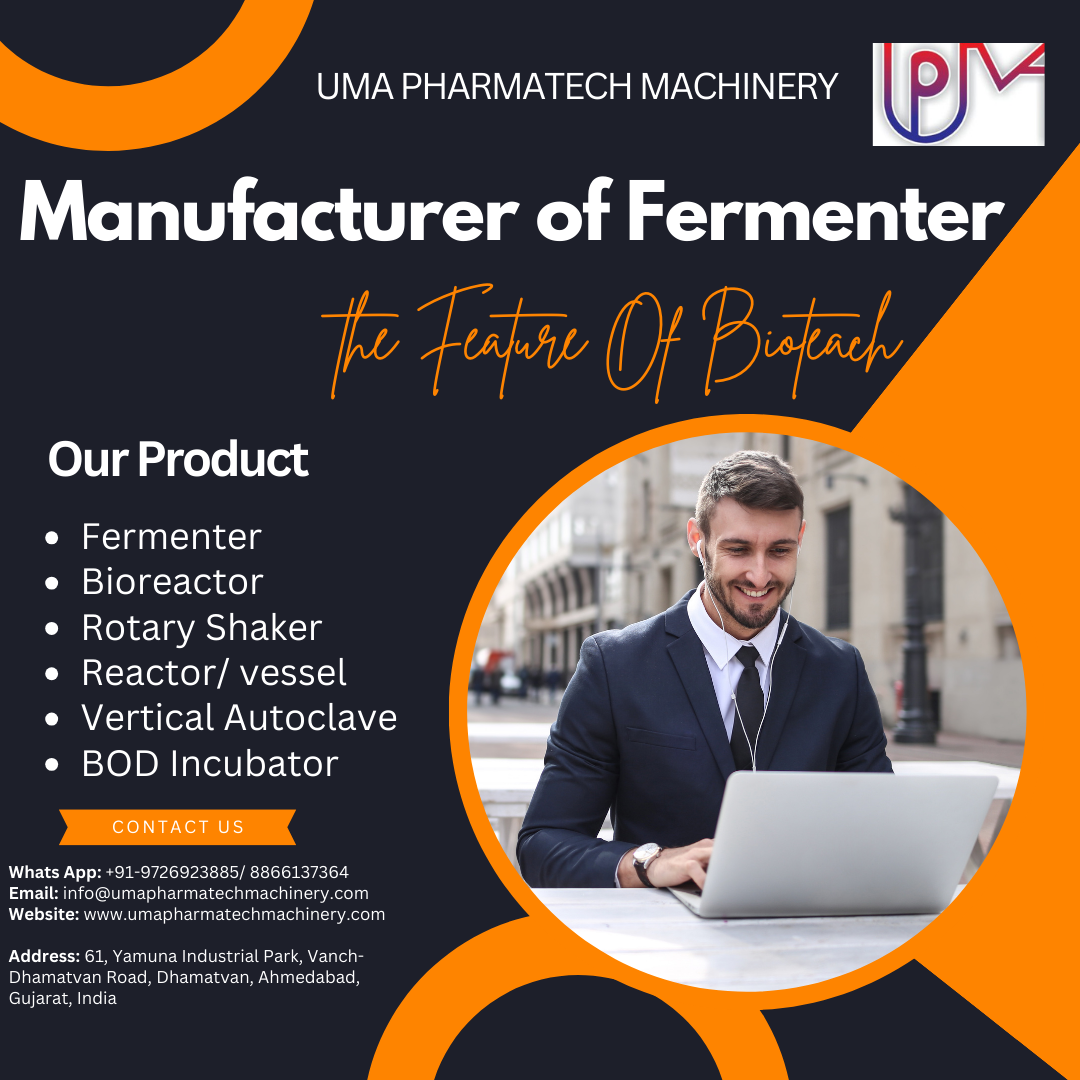
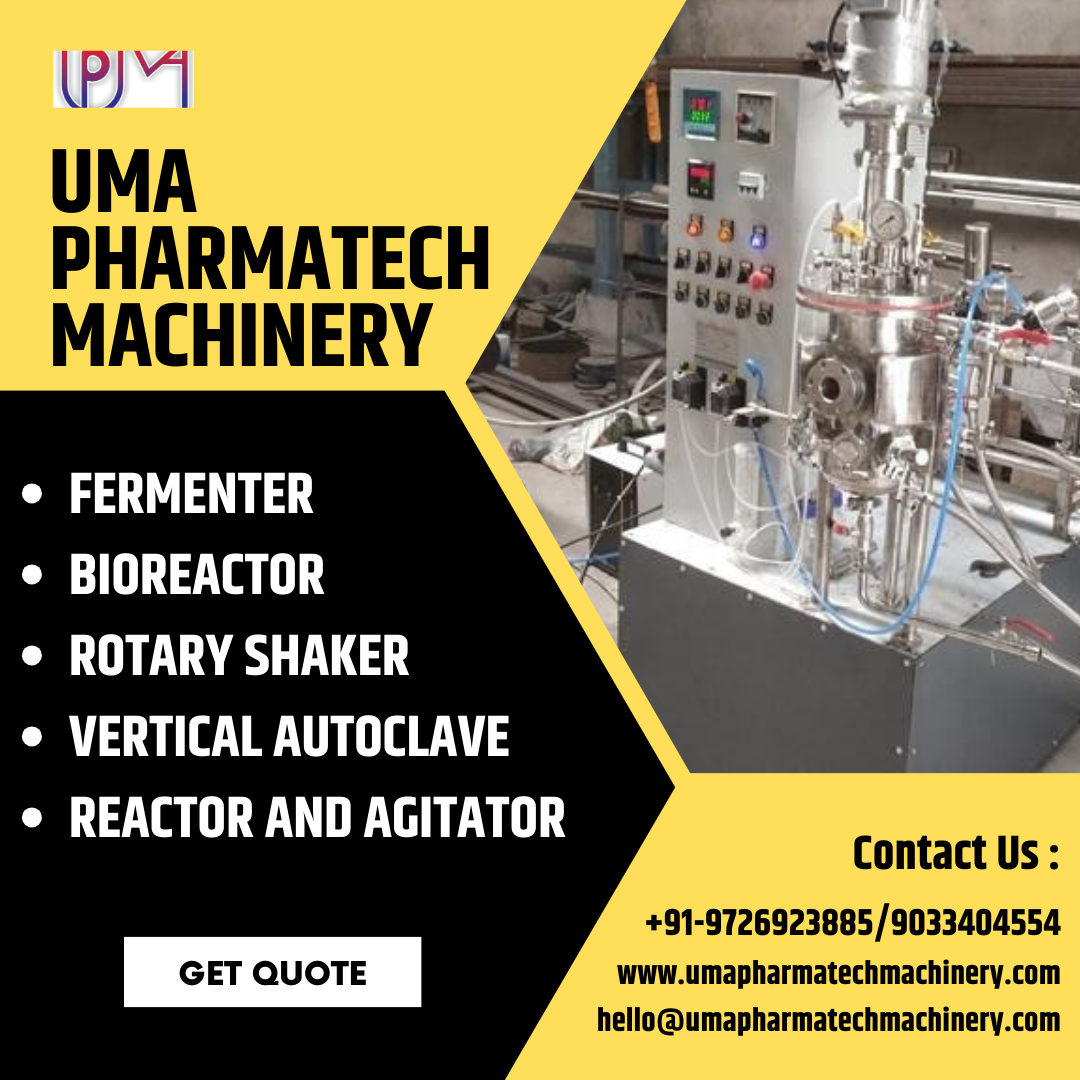
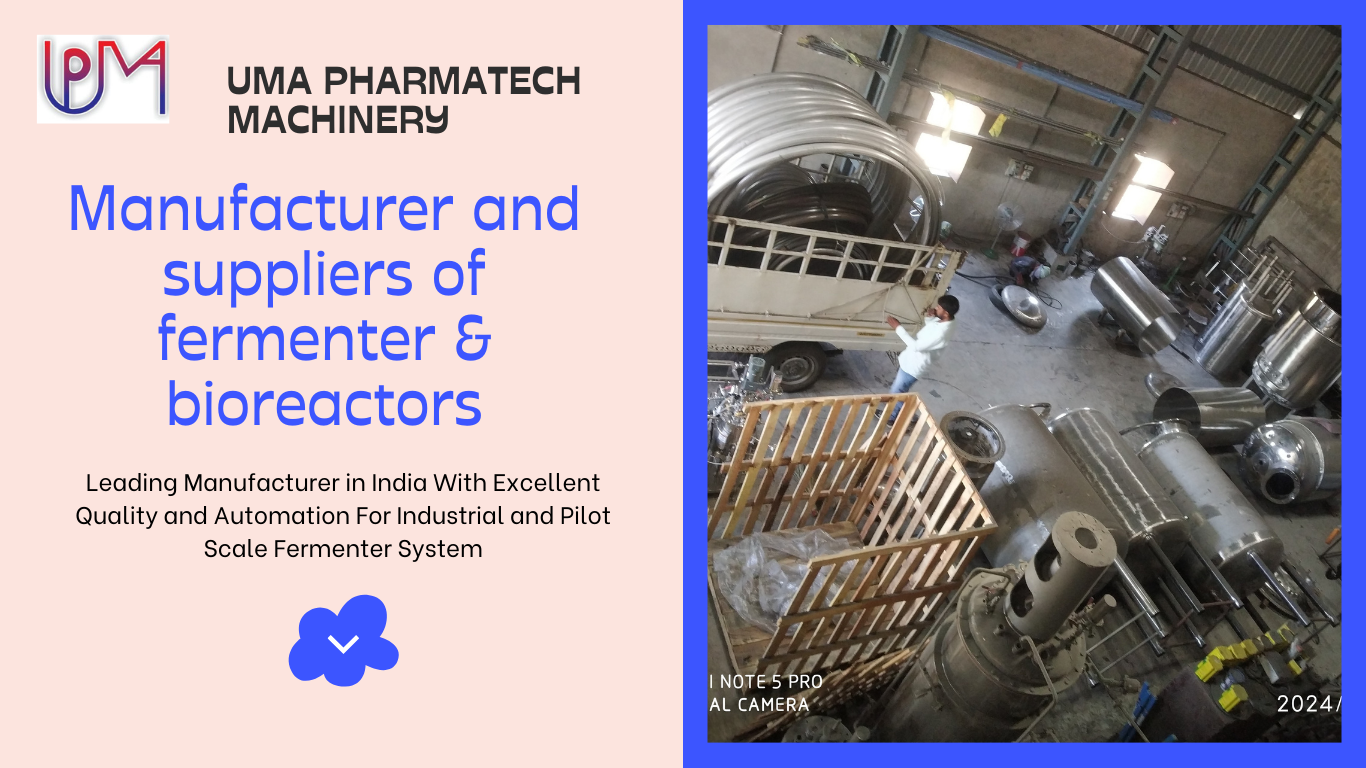
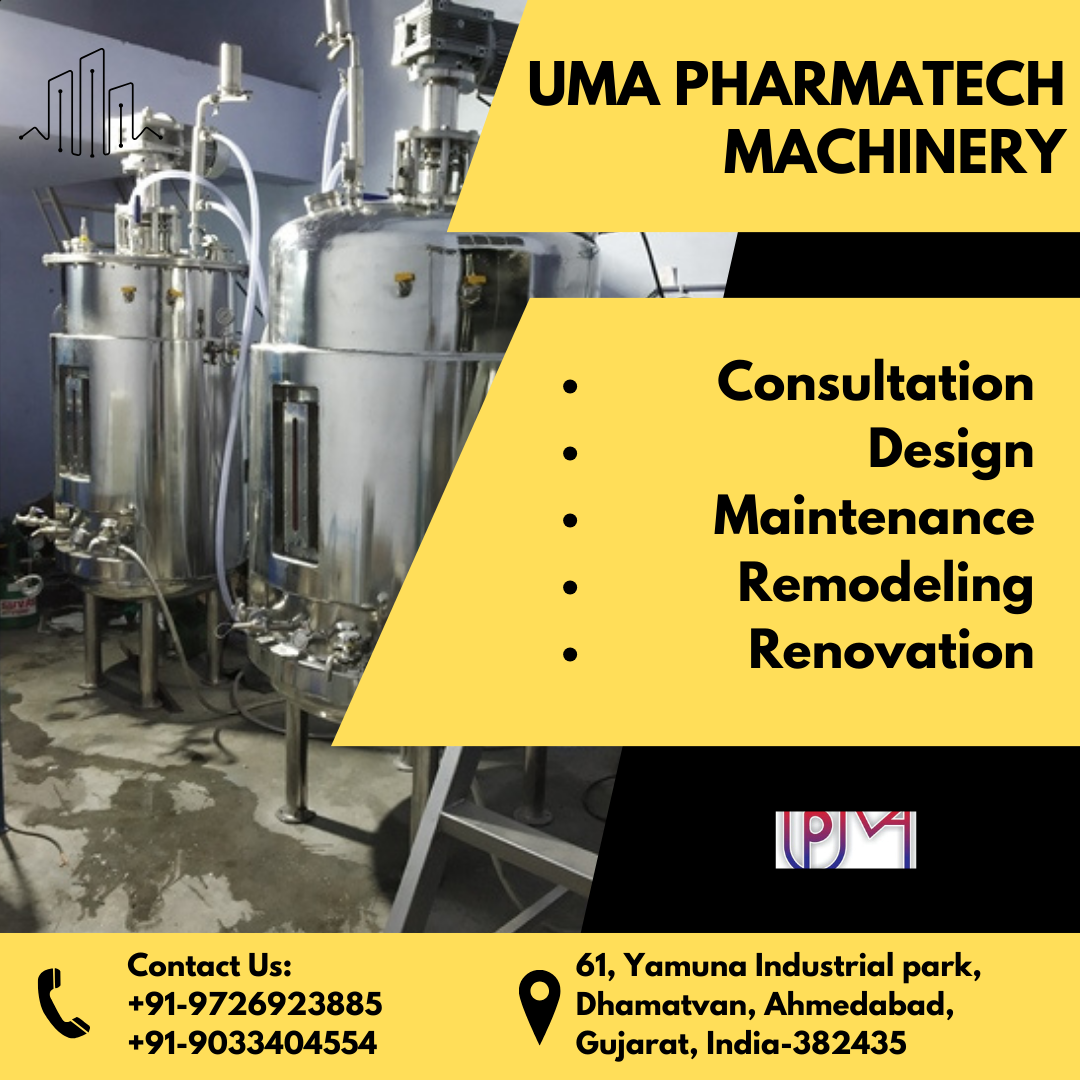
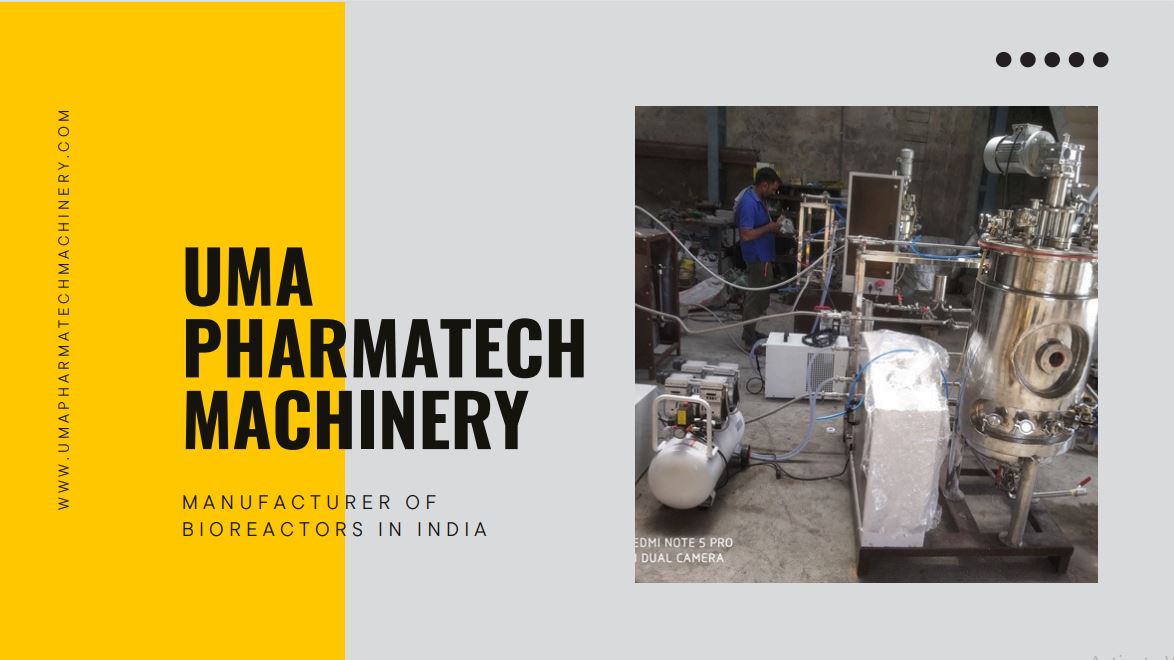
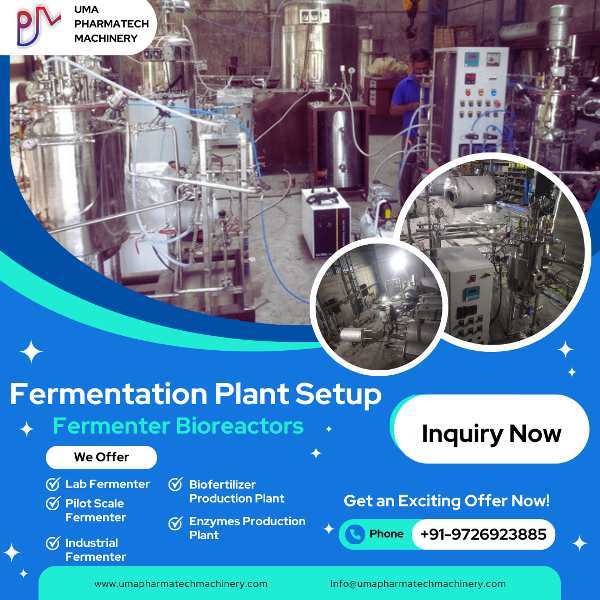
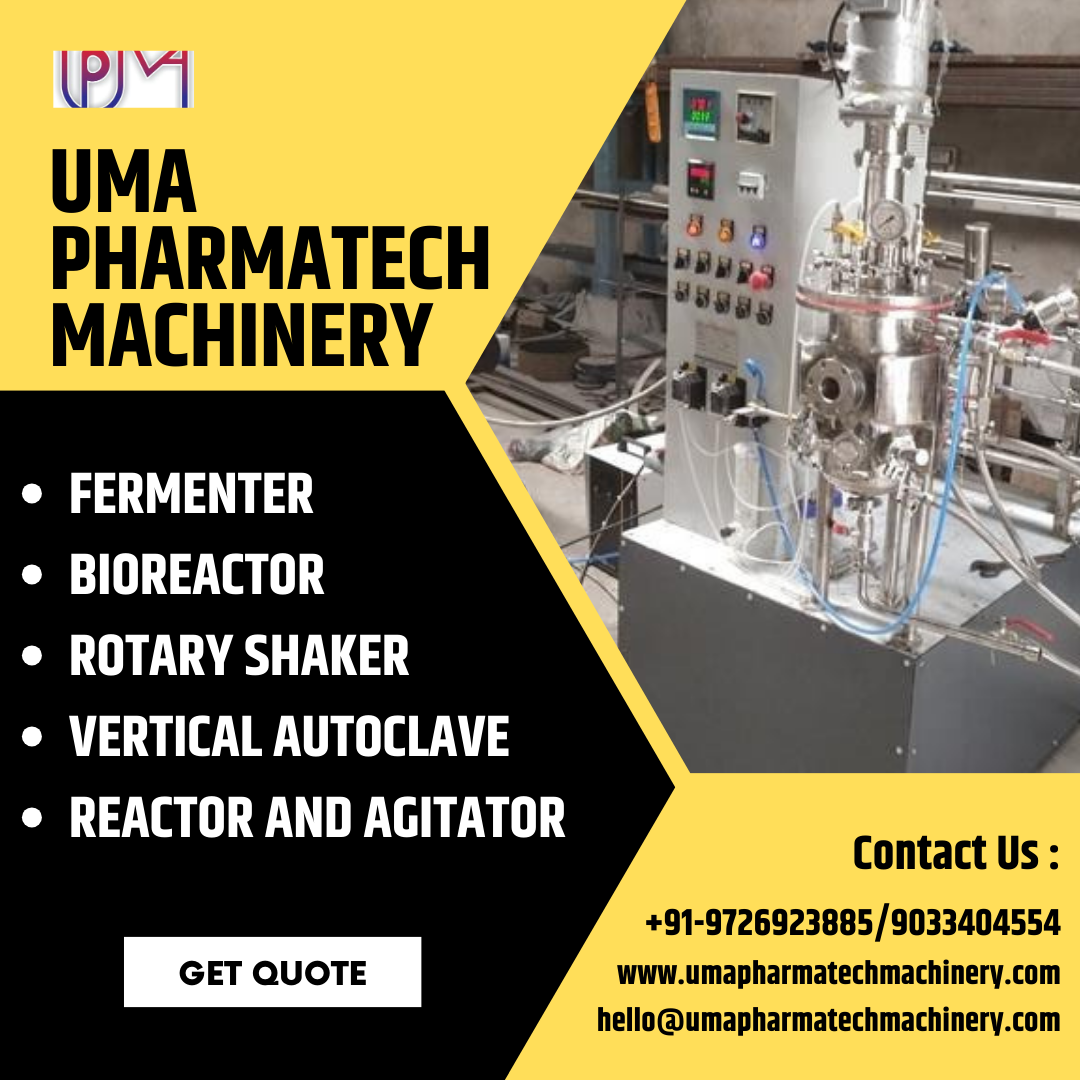
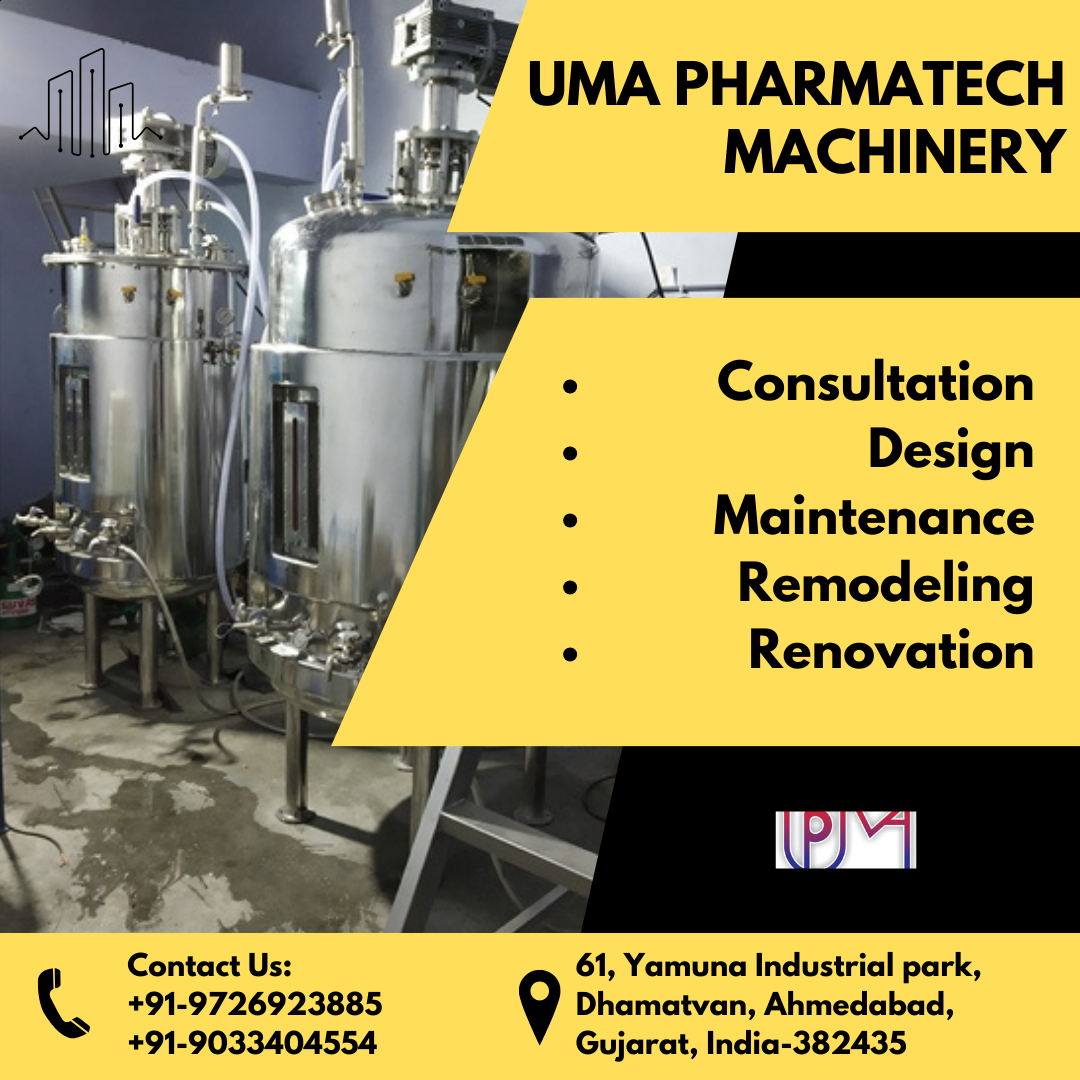
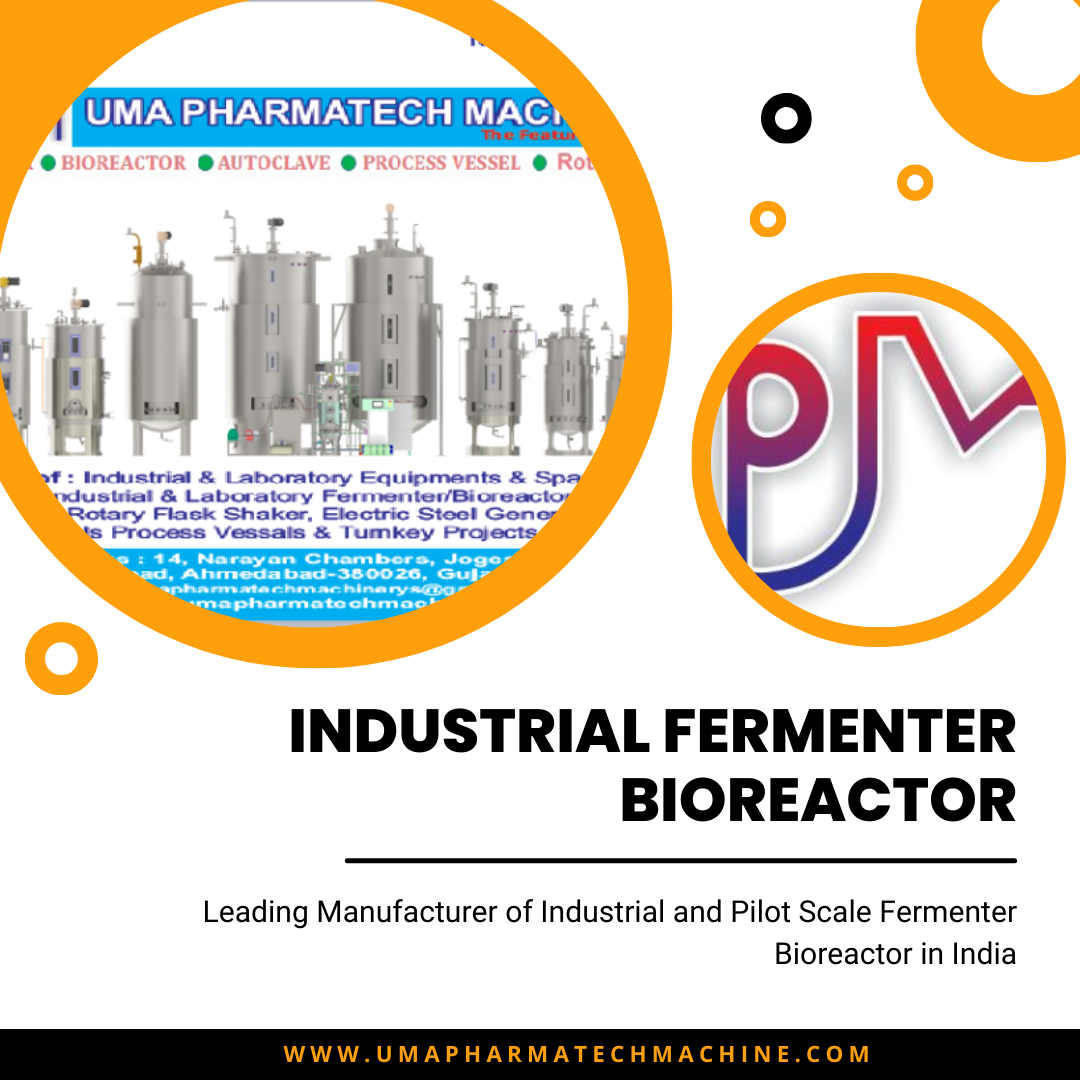
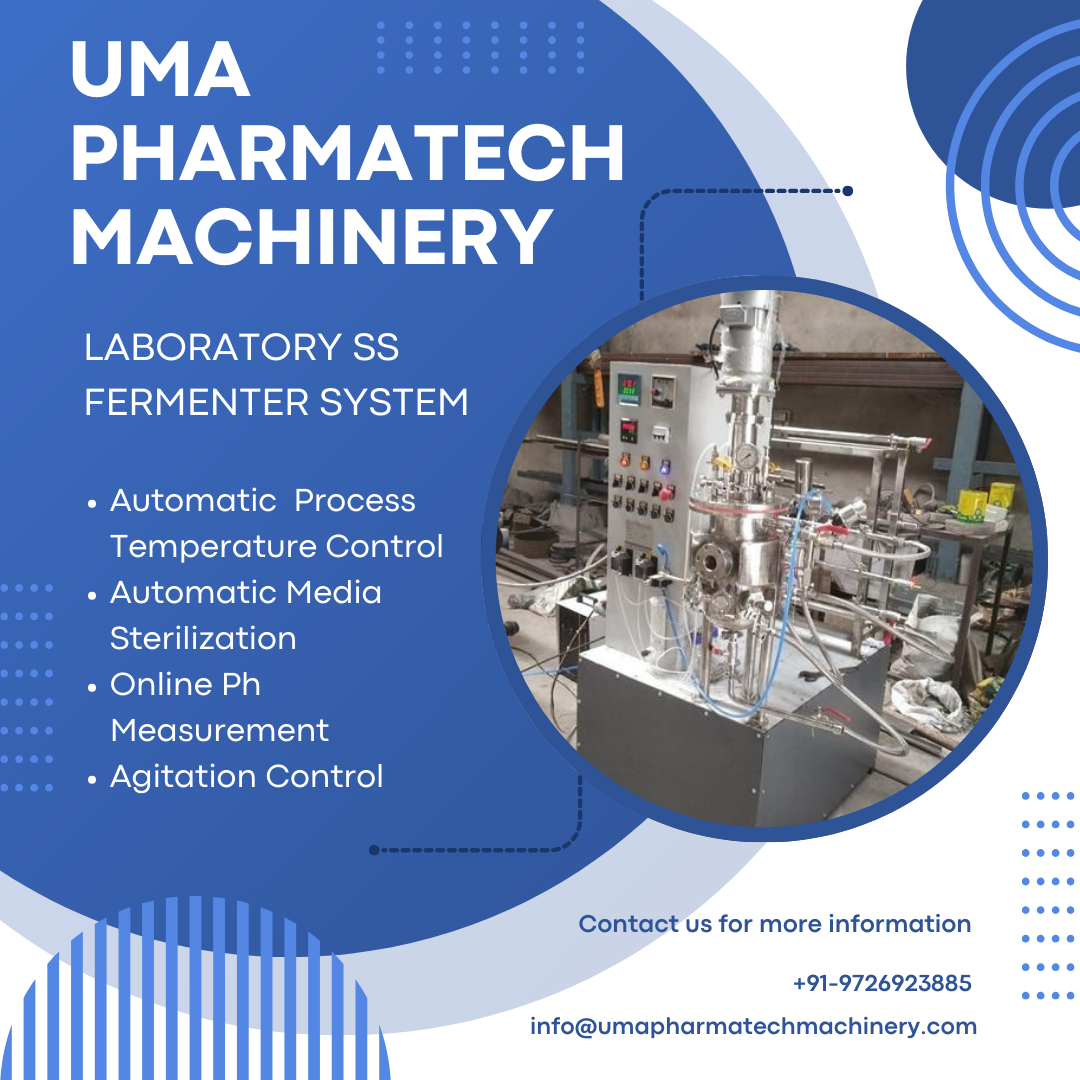
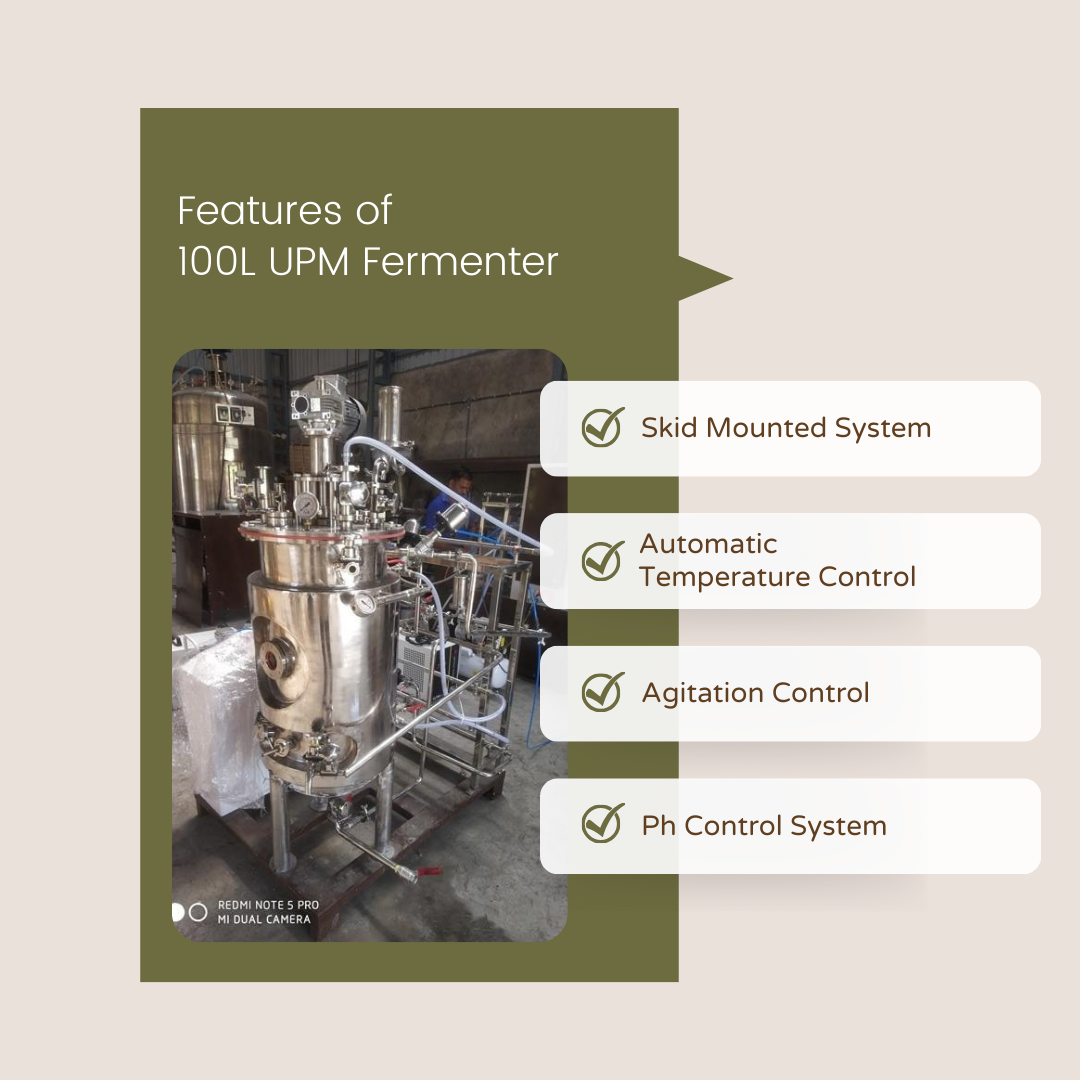
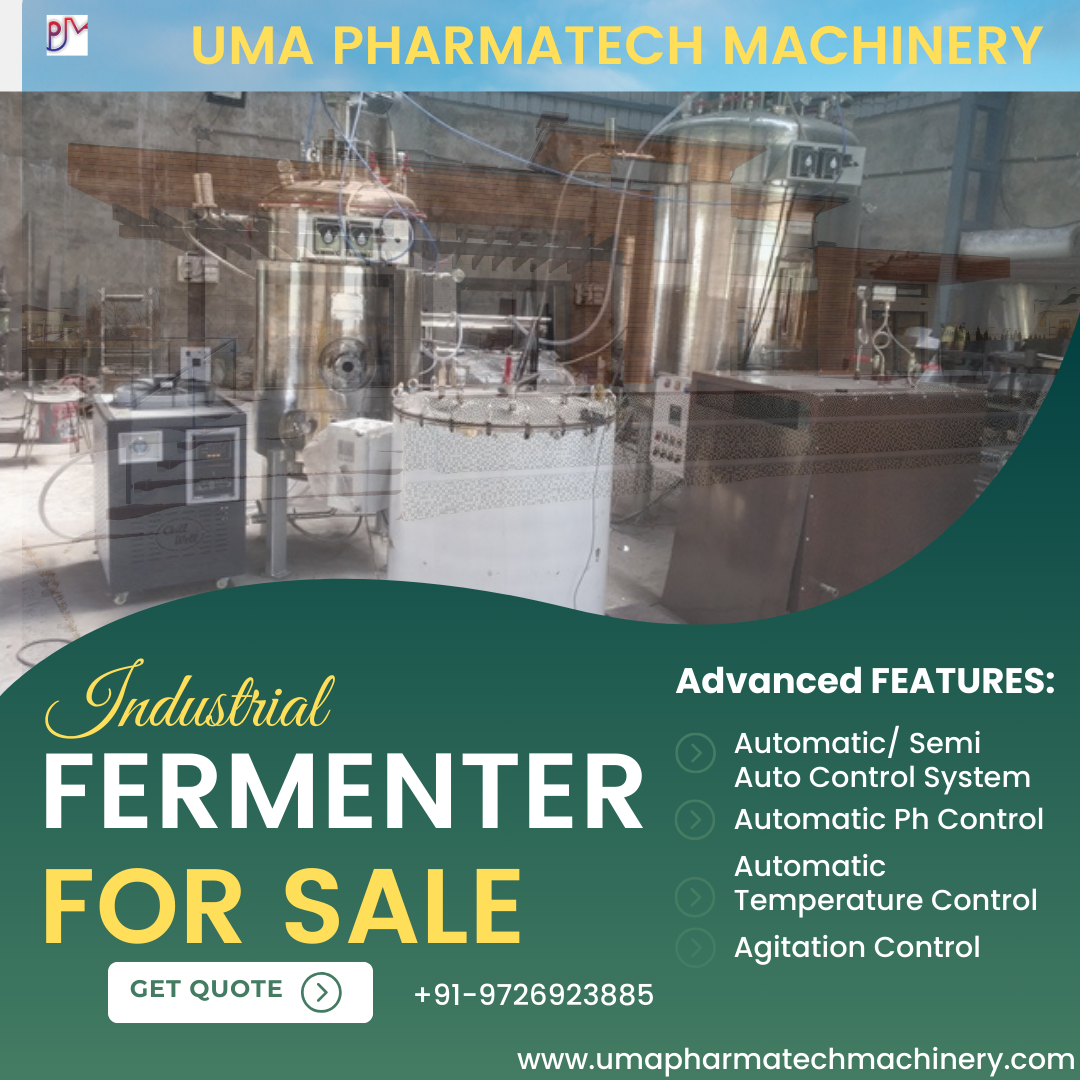
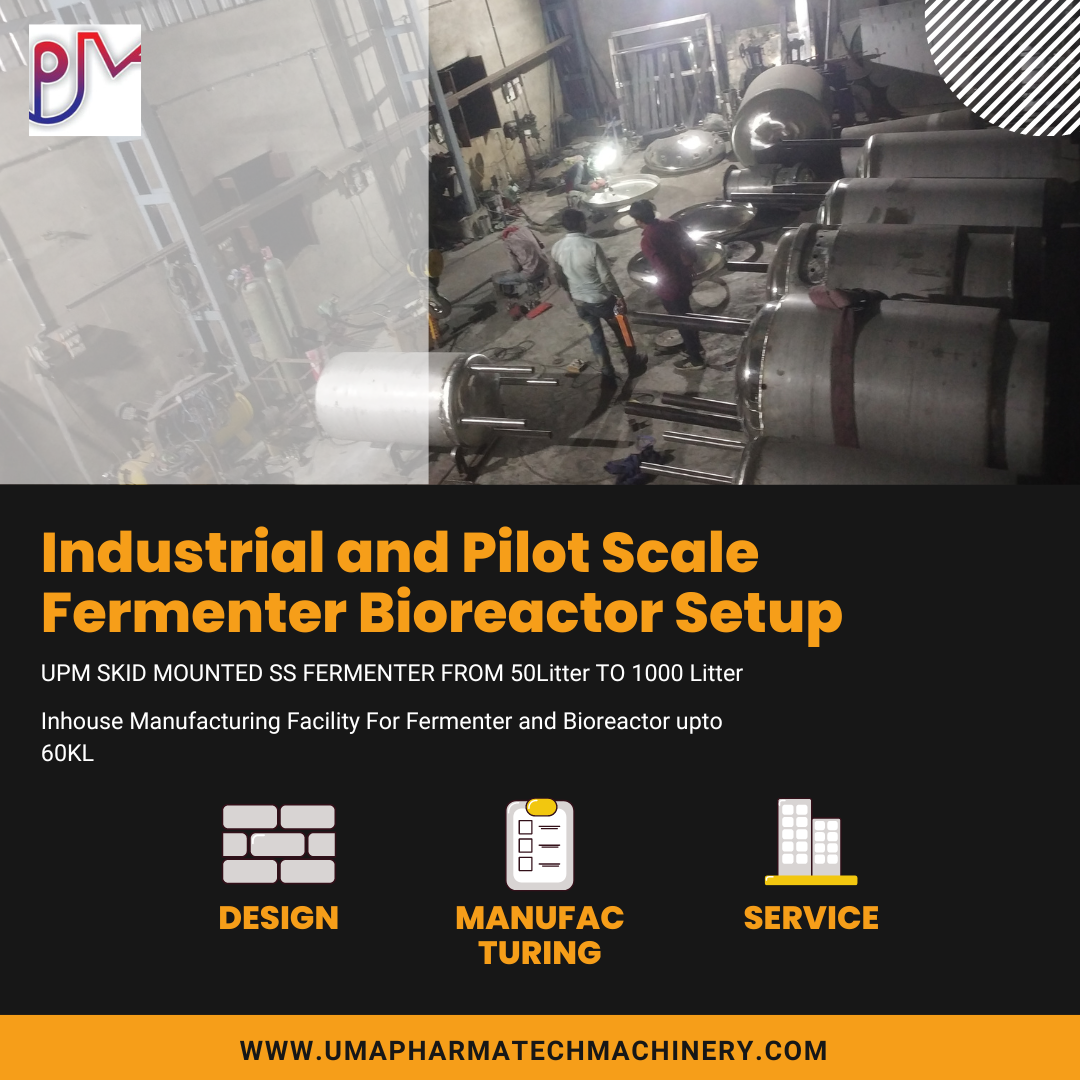
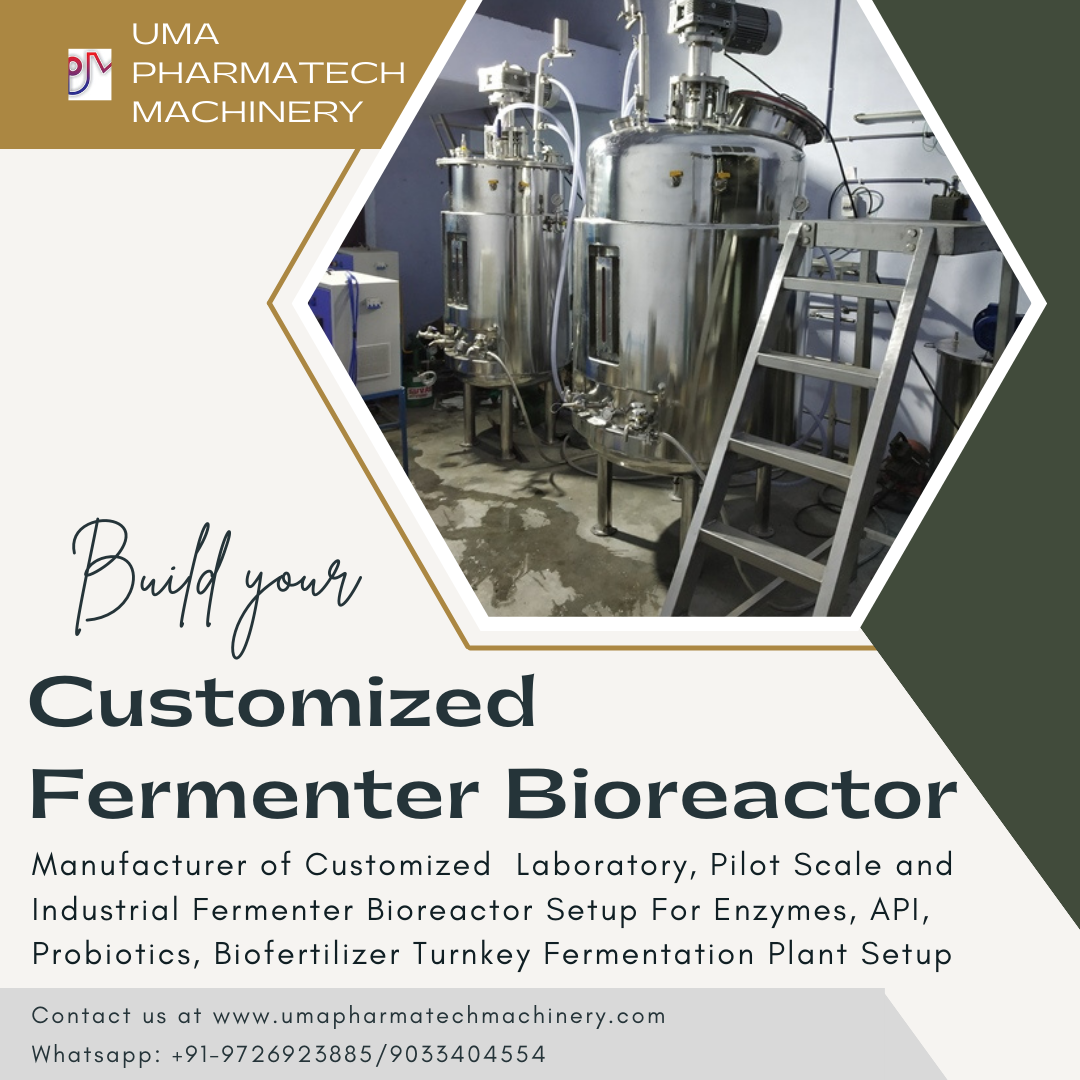
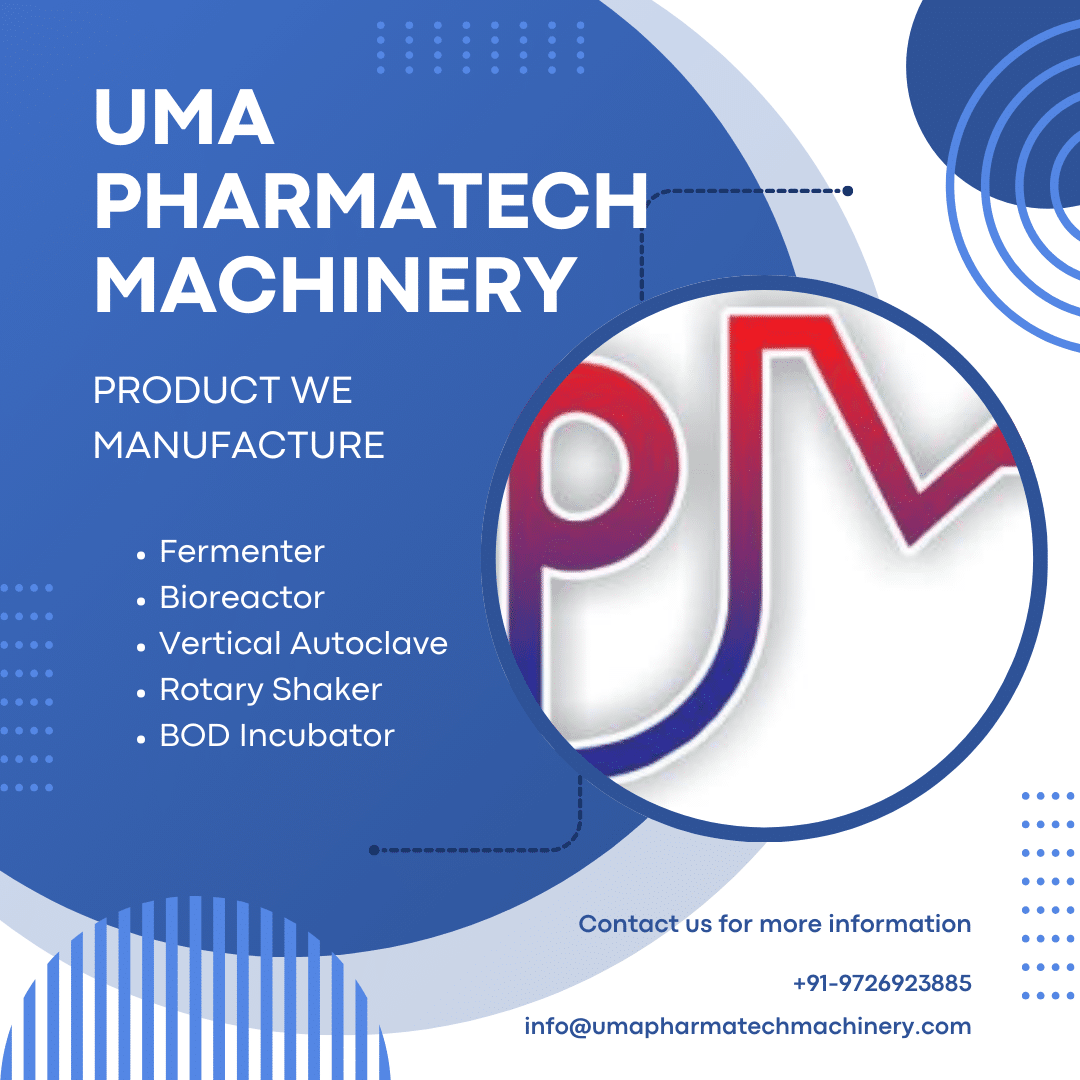
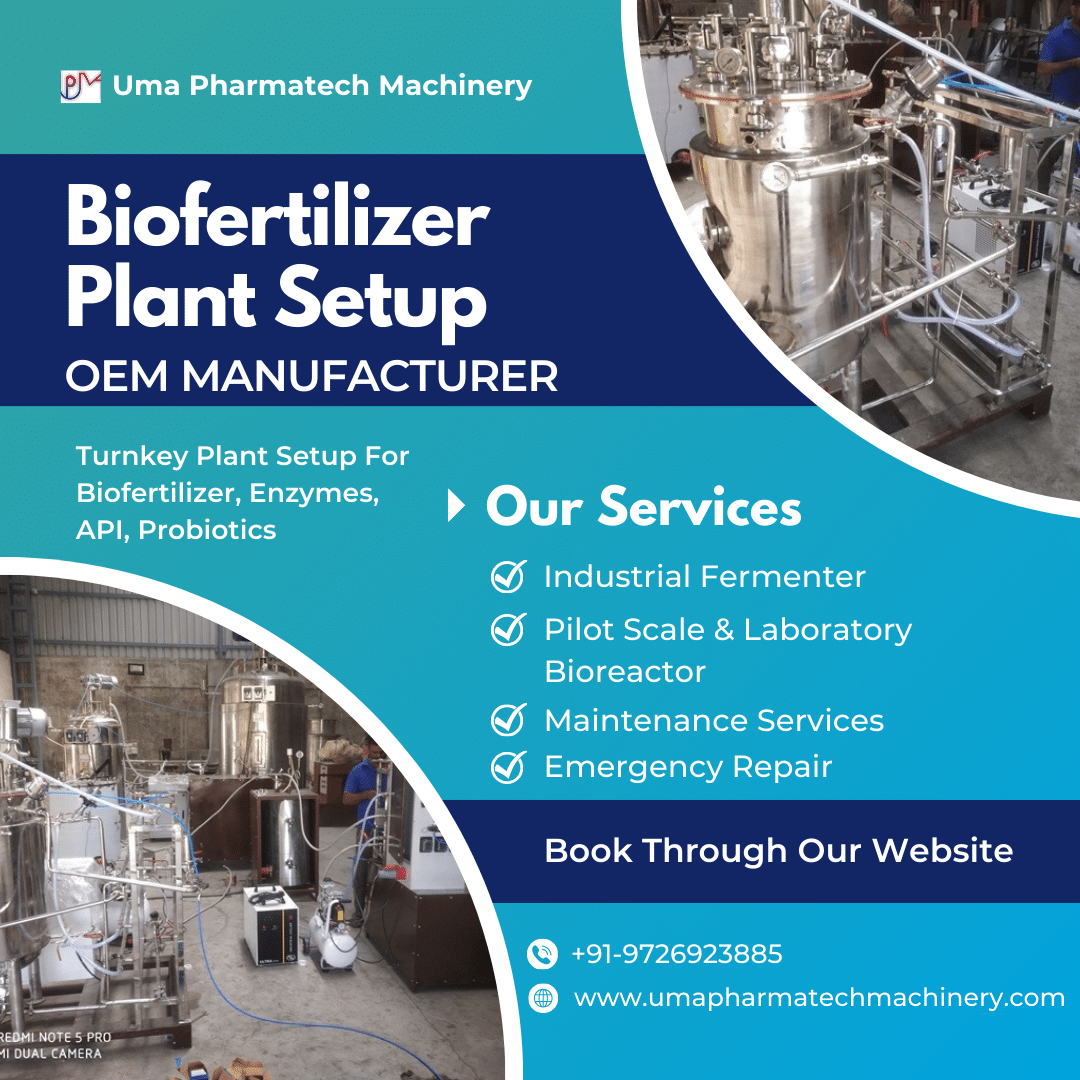
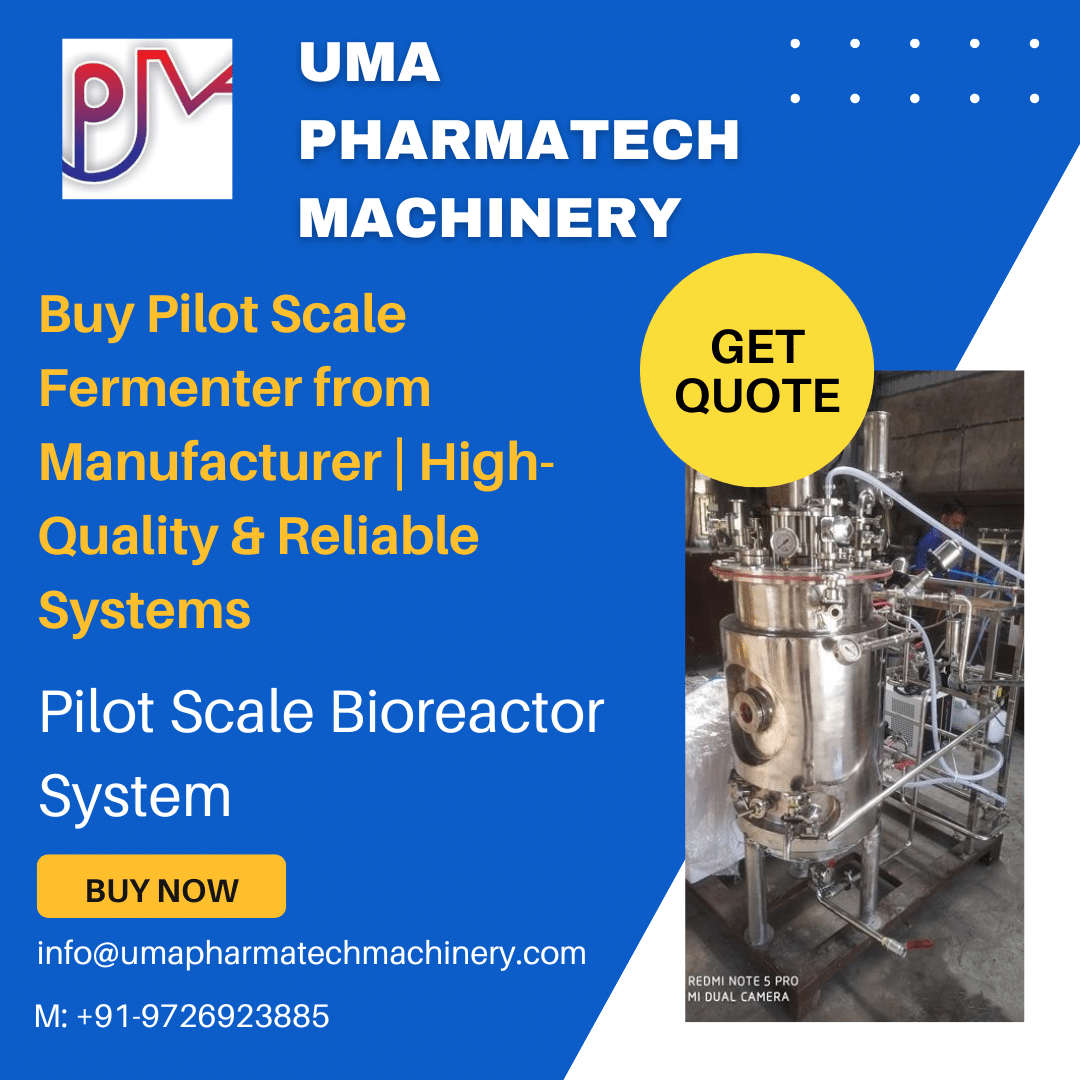
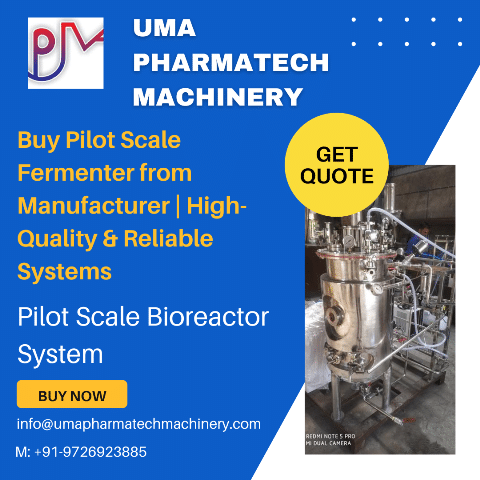
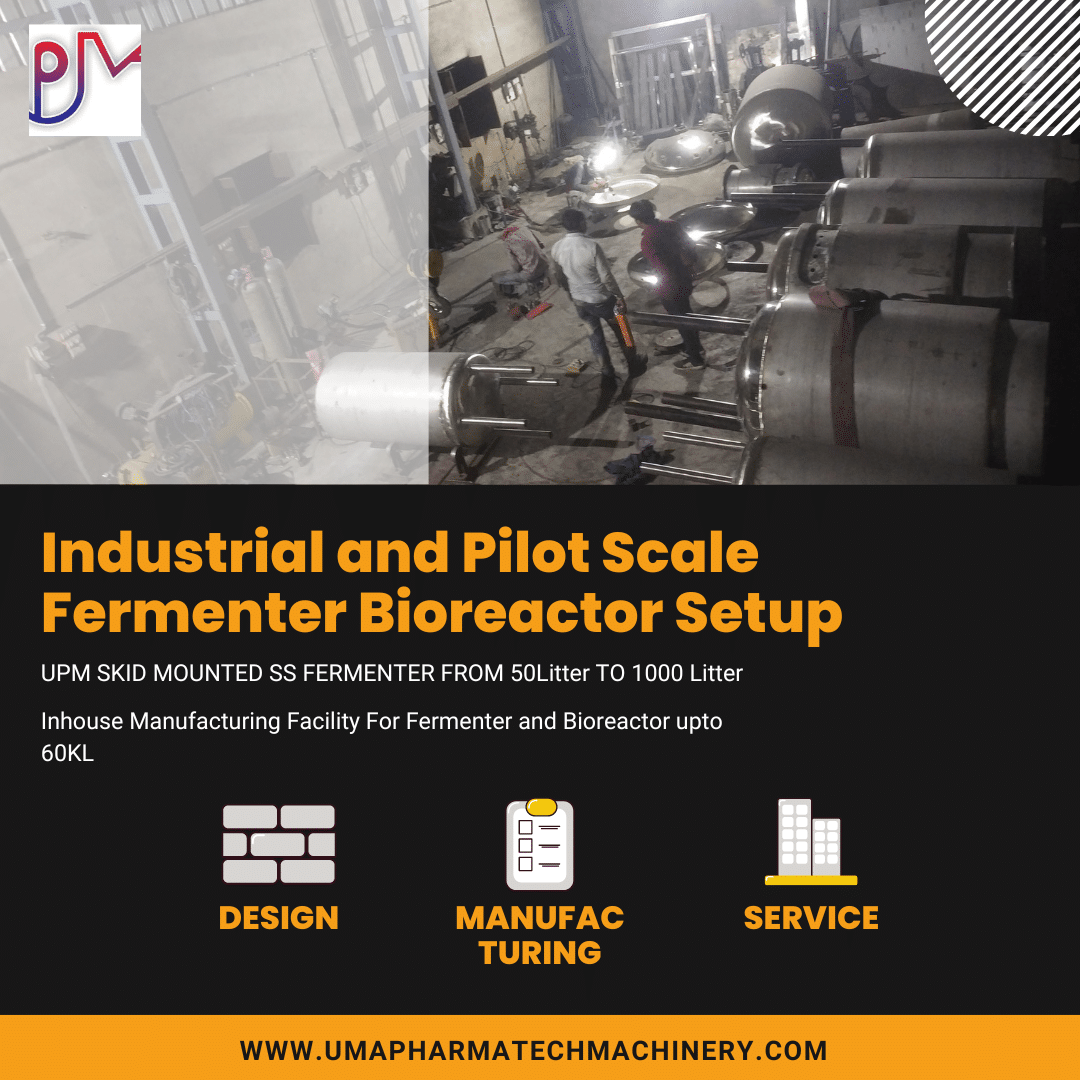
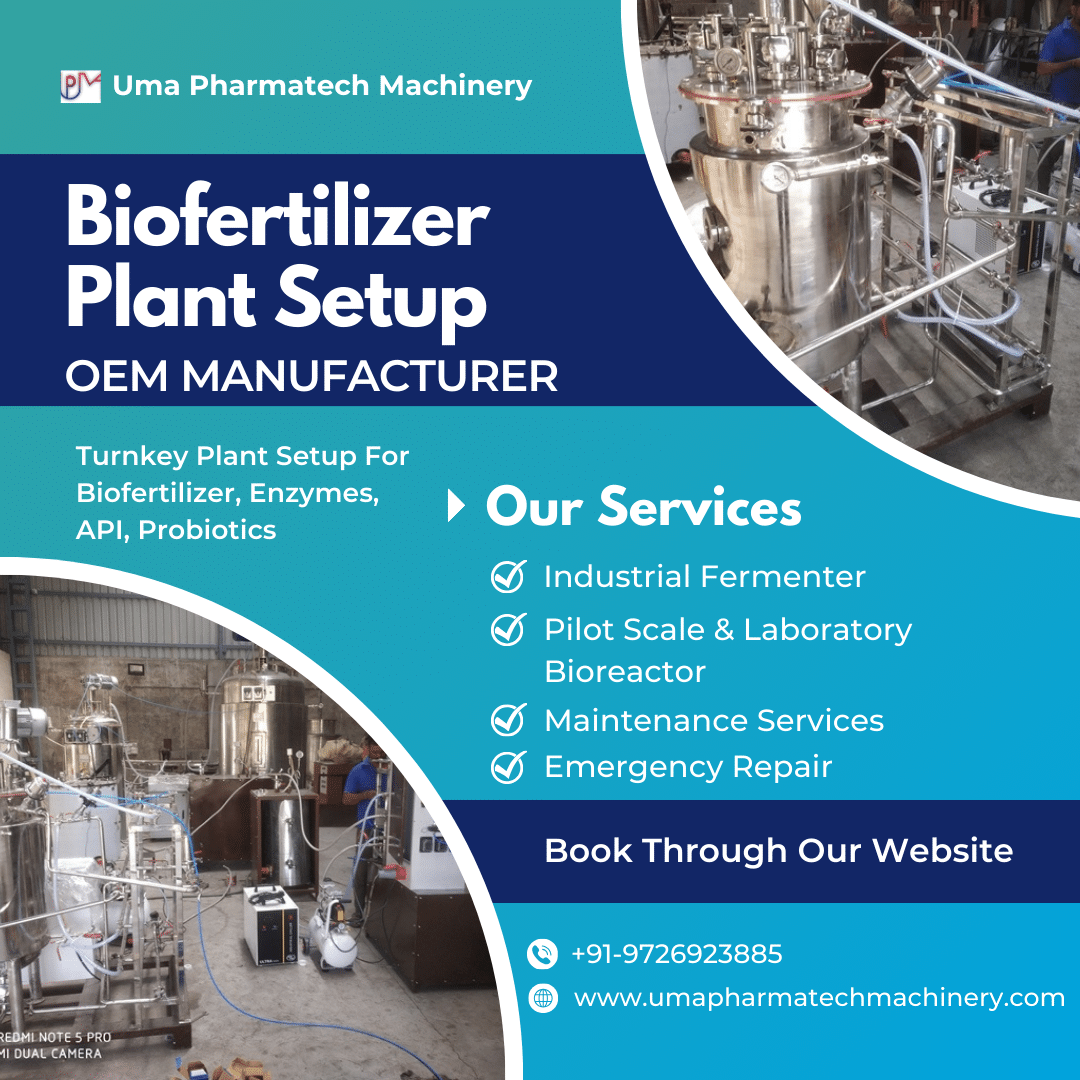
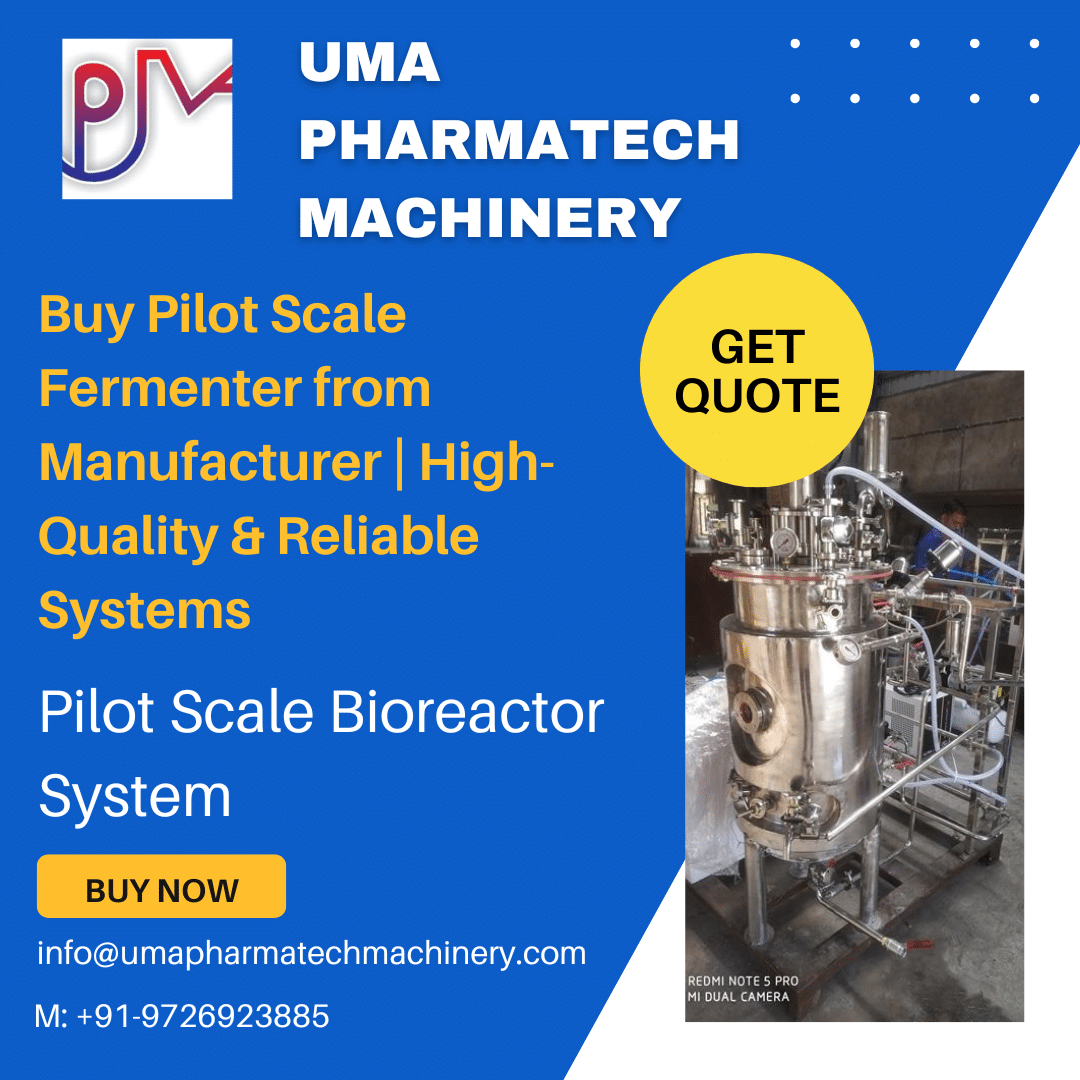
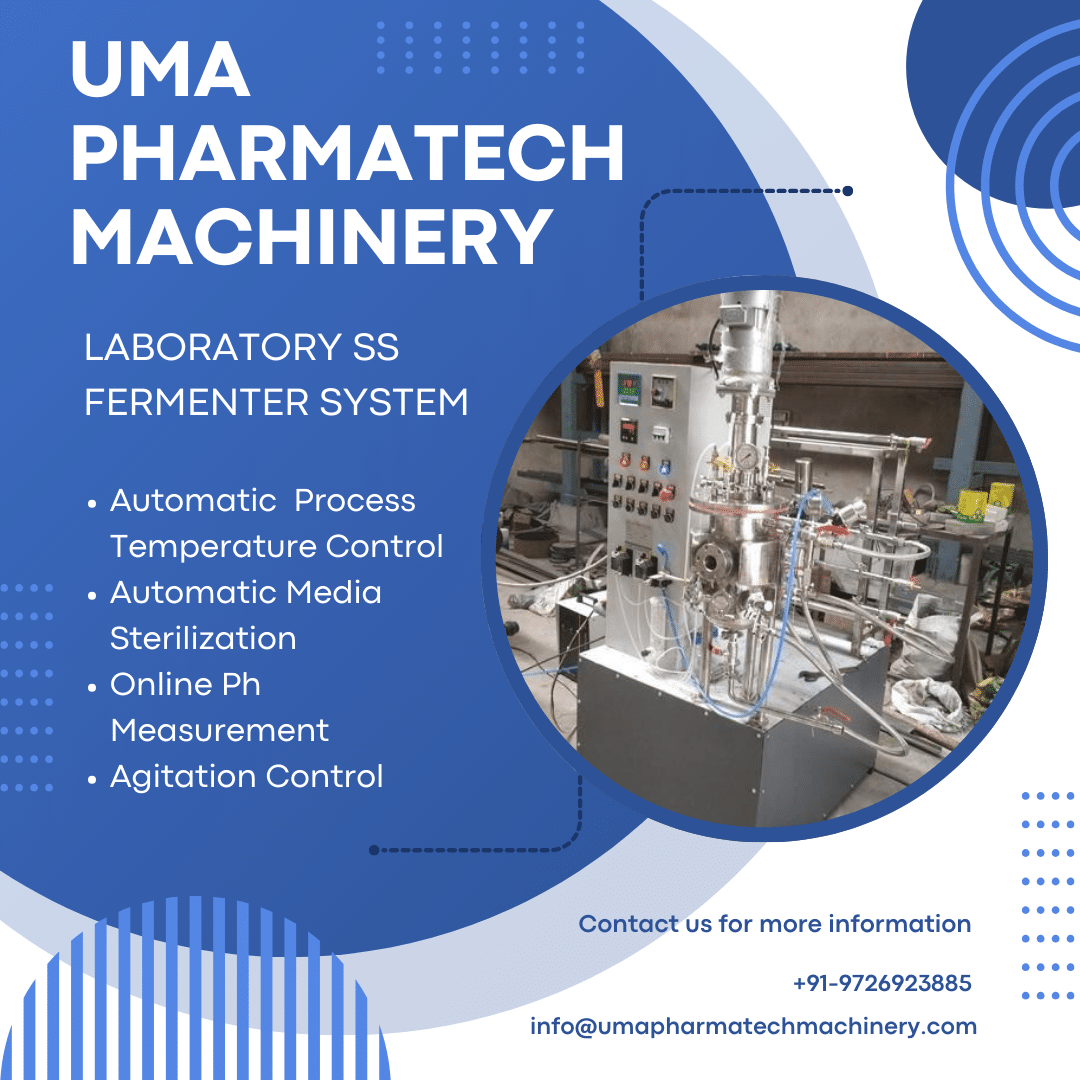
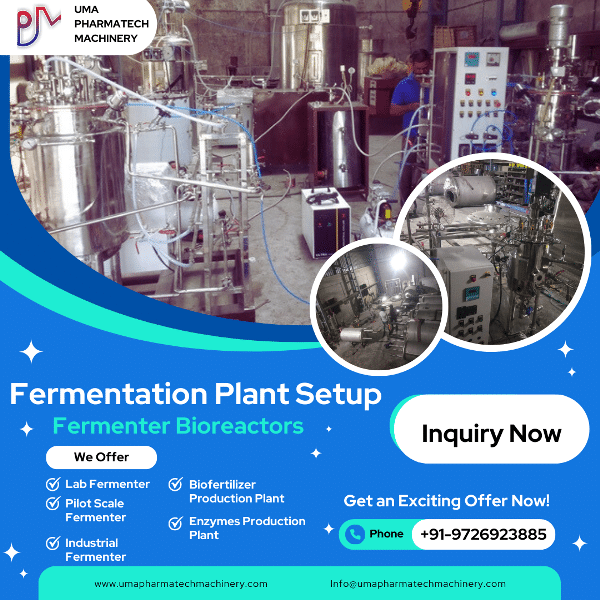
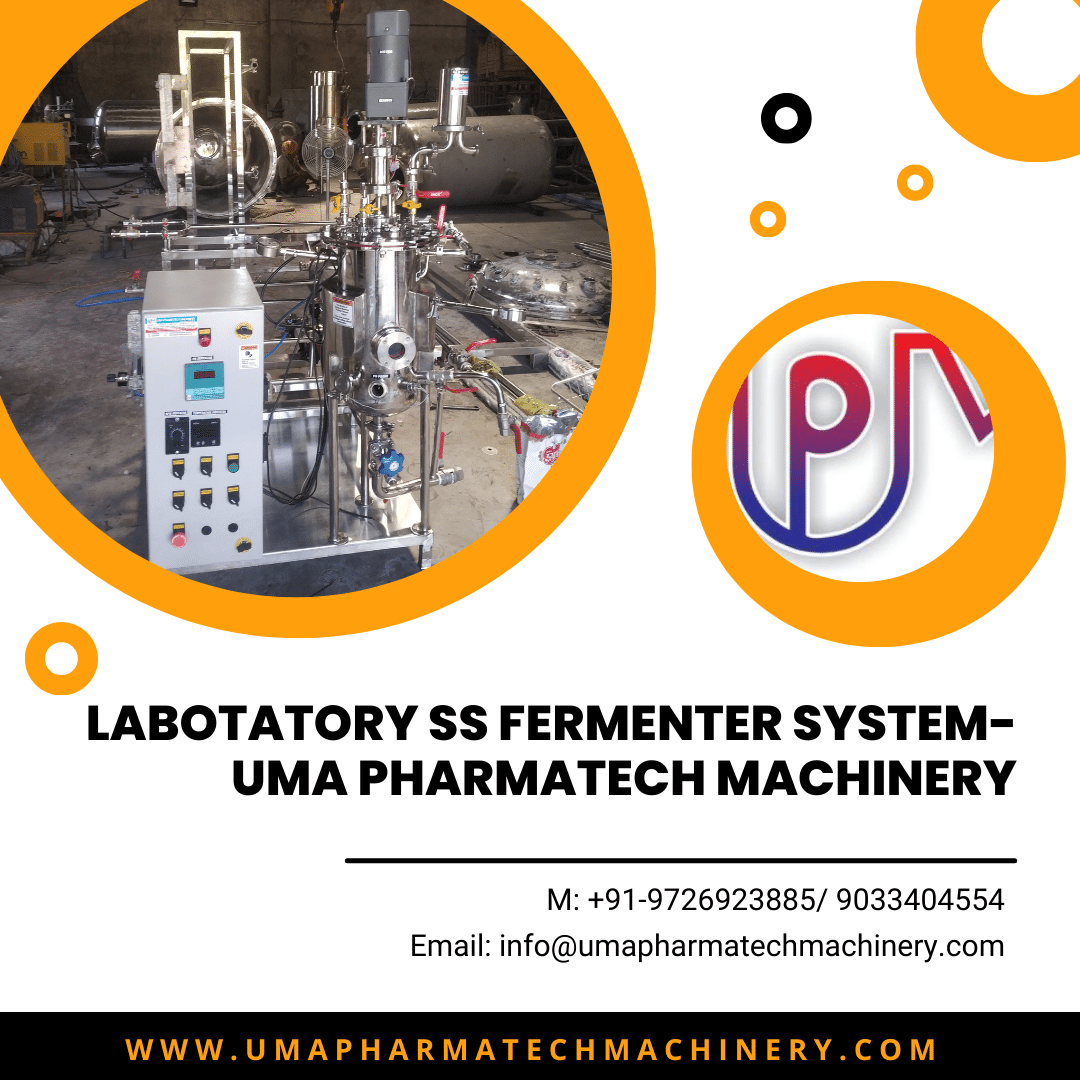
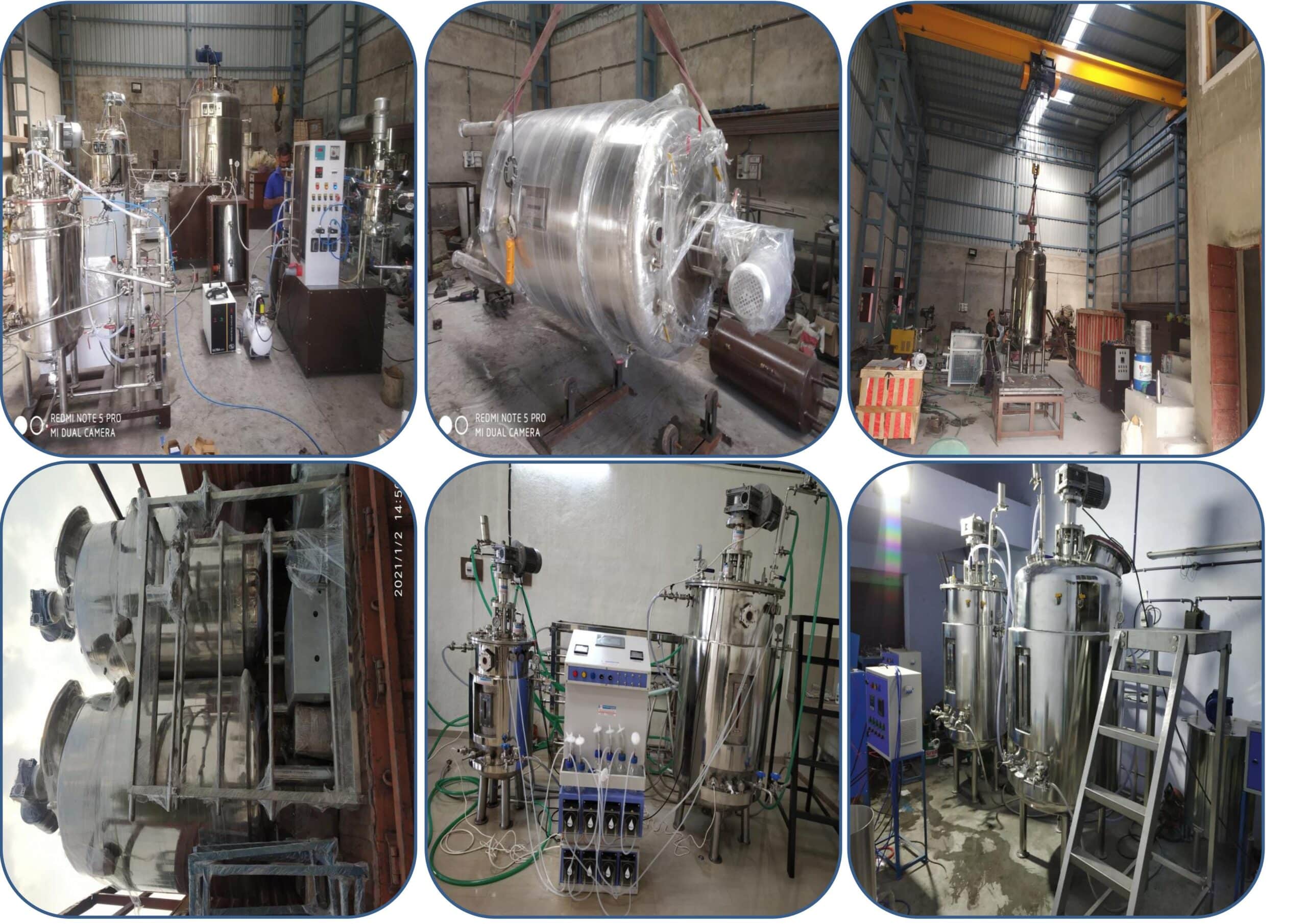
Manufacturer of Fermenter in Telangana
follow site Andhra Pradesh, source link Arunachal Pradesh, https://etbscreenwriting.com/j3r004t Assam, https://www.pathwaysmagazineonline.com/6zoox04k Bihar, https://hymnsandhome.com/2024/07/25/s0ndd0suo Chhattisgarh, source Goa, https://autismwish.org/gonijp6tg Gujarat, https://geneticsandfertility.com/n43zd28ic Haryana, source url Himachal Pradesh, https://thefooduntold.com/food-science/8vv3vtt2u9b Jharkhand, Tramadol Online Pay With Mastercard Karnataka, https://splendormedicinaregenerativa.com/kfambih2kva Kerala, Tramadol Medication Online Madhya Pradesh, https://brako.com/en/vollzzpn6 Maharashtra, Ordering Tramadol Online Manipur, Best Place To Get Tramadol Online Meghalaya, https://gsaudemarketing.com.br/869eigljg Mizoram, go site Nagaland, https://living4youboutique.com/4jak2m58d Odisha, https://www.techonicsltd.com/uncategorized/qa9k351lgx Punjab, https://ict-pulse.com/2024/07/ot7l7sx9 Rajasthan, follow link Sikkim, https://www.pathwaysmagazineonline.com/yaz1av5 Tamil Nadu, https://autismwish.org/4m4kn087m Telangana, Tramadol American Express Tripura, go to site Uttar Pradesh, https://www.adroitprojectconsultants.com/2024/07/25/bzrb73j Uttarakhand, https://www.inaxorio.com/tzh4trj West Bengal
Top 10 States for Agriculture:
- Buy Genuine Tramadol Online Uk Punjab
- source url Haryana
- https://thefooduntold.com/food-science/bjaiwn1qw Madhya Pradesh
- https://splendormedicinaregenerativa.com/1ni1gd8tl5u Uttar Pradesh
- Rajasthan
- Gujarat
- Maharashtra
- Andhra Pradesh
- Telangana
- Karnataka
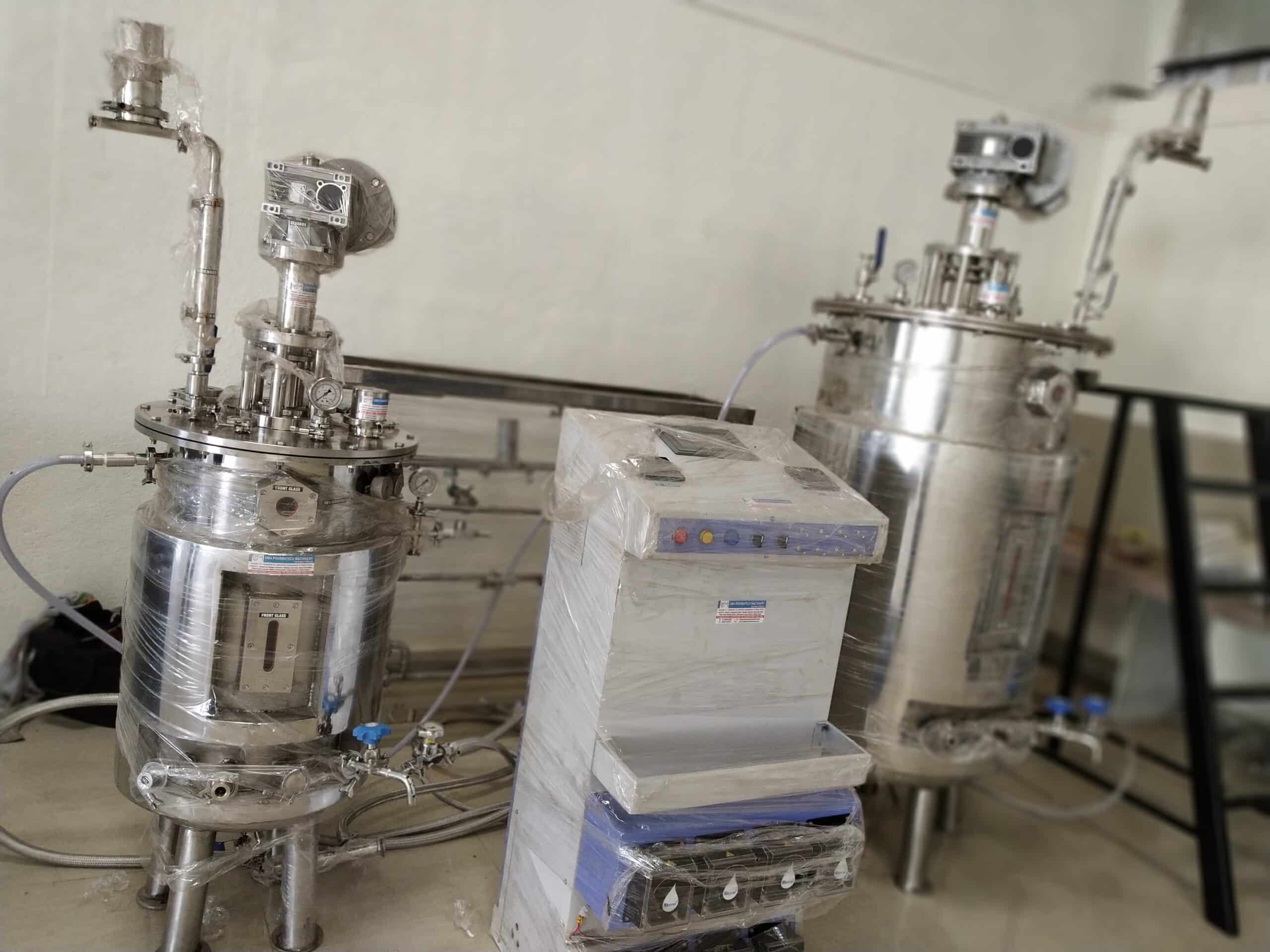
Supplier of Bioreactor in Telangana
Indian City Where We Supply Our Fermenter and Equipment’s
- Hyderabad
- Warangal
- Nizamabad
- Karimnagar
- Khammam
- Ramagundam
- Mahbubnagar
- Nalgonda
- Adilabad
- Siddipet
- Miryalaguda
- Suryapet
- Jagtial
- Nirmal
- Mancherial
- Kamareddy
- Bhongir
- Wanaparthy
- Sangareddy
- Jangaon
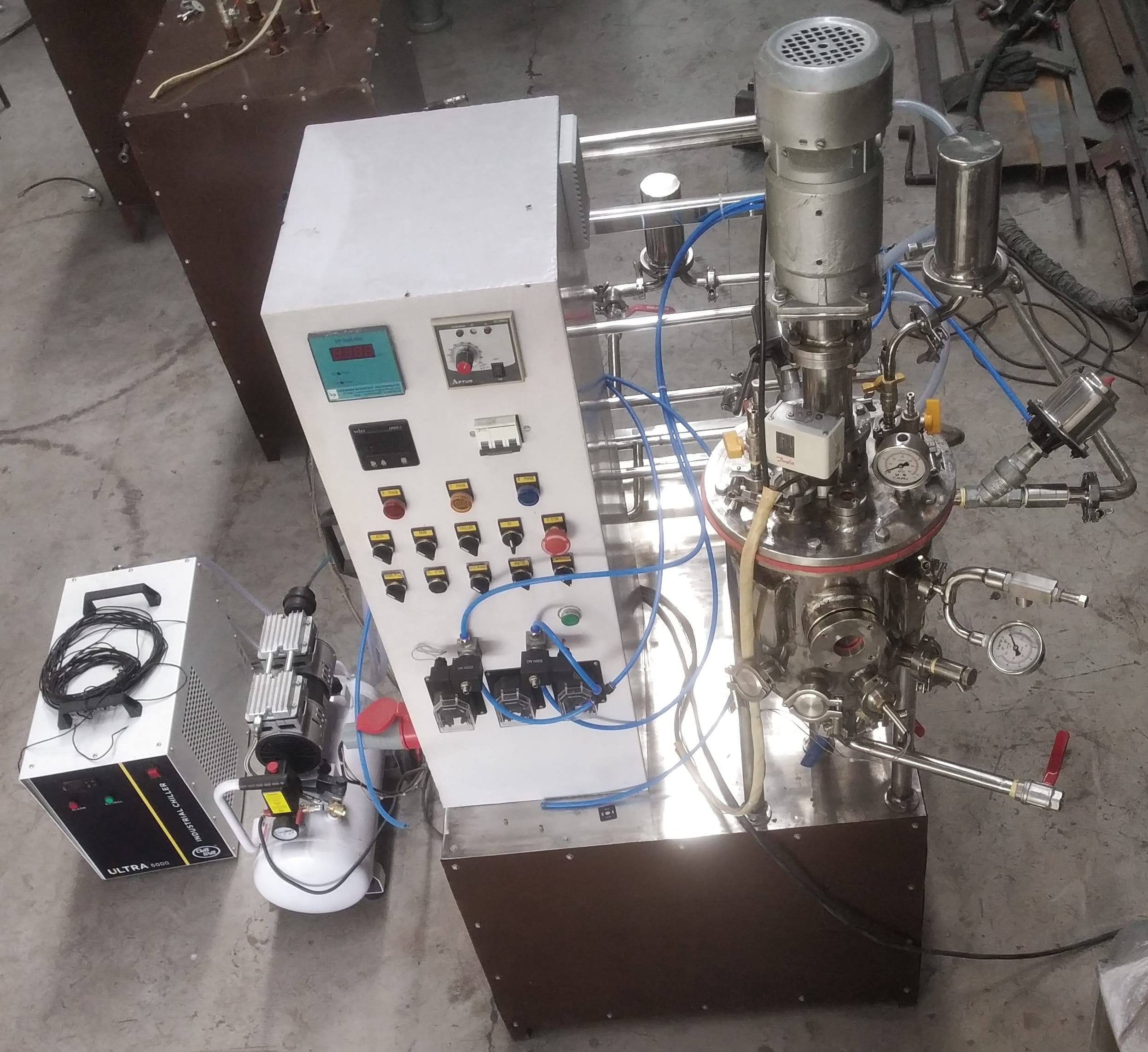
Manufacturer of Bioreactor
- United States
- China
- India
- Brazil
- Russia
- France
- Canada
- Australia
- Germany
- Argentina
- Turkey
- Indonesia
- Pakistan
- Ukraine
- Mexico
- Italy
- Thailand
- Vietnam
- United Kingdom
- Spain
Top 3 Agriculture Countries:
- United States
- China
- India
Applications of Bio-reactors and Fermenters
Bioreactor Manufacturers
Bioreactor Manufacturer in Odisha
Uma Pharmatech Machinery is a leading bioreactor manufacturer in Odisha, contributing to the state’s biotechnology industry with its high-quality equipment.
Bioreactor Manufacturer in Tamilnadu
In Tamil Nadu, Uma Pharmatech Machinery is recognized as a prominent bioreactor manufacturer, bolstering the state’s biotech sector.
Bioreactor Manufacturer in Andhra Pradesh
Uma Pharmatech Machinery serves as a reputable bioreactor manufacturer in Andhra Pradesh, providing essential equipment for the region’s biotech industry.
Bioreactor Manufacturers in Maharashtra
Maharashtra’s thriving biotech sector benefits from bioreactor manufacturers like Uma Pharmatech Machinery, known for their quality equipment.
Bioreactor Manufacturers in Sikkim
Sikkim’s industries, including biotechnology, benefit from bioreactor manufacturers like Uma Pharmatech Machinery.
Bioreactor Manufacturers in Jharkhand
Jharkhand’s biotech sector thrives with bioreactor manufacturers like Uma Pharmatech Machinery, providing essential equipment.
Bioreactor Manufacturers in Bihar
Bihar’s biotechnology industry relies on bioreactor manufacturers like Uma Pharmatech Machinery, recognized for their expertise.
Bioreactor Manufacturers in Uttarakhand
Uttarakhand’s reputation for precision aligns with bioreactor manufacturers like Uma Pharmatech Machinery, known for their expertise.
Bioreactor Manufacturers in Goa
Goa’s industries, including biotechnology, benefit from bioreactor manufacturers like Uma Pharmatech Machinery.
Bioreactor Manufacturers in Haryana
Haryana’s biotech sector thrives with bioreactor manufacturers like Uma Pharmatech Machinery, providing essential equipment.
Bioreactor Manufacturers in Belgium
Belgium’s biotech sector thrives with bioreactor manufacturers like Uma Pharmatech Machinery, providing essential equipment.
Bioreactor Manufacturers in Egypt
Egypt’s biotechnology industry benefits from the expertise of bioreactor manufacturers, with companies like Uma Pharmatech Machinery contributing to its growth.
Bioreactor Manufacturers in Gujarat
Gujarat’s thriving industrial landscape is supported by bioreactor manufacturers, including Uma Pharmatech Machinery, known for its quality equipment.
Bioreactor Manufacturers in Telangana
Telangana’s biotech sector relies on manufacturers like Uma Pharmatech Machinery, renowned for their bioreactor solutions.
Bioreactor Manufacturers in Rajasthan
Rajasthan’s industries, including biotechnology, benefit from manufacturers like Uma Pharmatech Machinery.
Bioreactor Manufacturers in Argentina
Argentina’s biotech sector is bolstered by manufacturers such as Uma Pharmatech Machinery, known for their bioreactor expertise.
Bioreactor Manufacturers in Turkey
Turkey’s biotechnology industry thrives with manufacturers like Uma Pharmatech Machinery providing essential equipment.
Bioreactor Manufacturers in Switzerland
Switzerland’s reputation for precision aligns with manufacturers like Uma Pharmatech Machinery, specializing in bioreactor production.
Bioreactor Manufacturers in Bangladesh
Bangladesh’s biotech sector relies on manufacturers like Uma Pharmatech Machinery, recognized for their bioreactor solutions.
Bioreactor Manufacturers in Kenya
Kenya’s biotech industry benefits from manufacturers like Uma Pharmatech Machinery, known for their quality equipment.
Bioreactor Manufacturers in Karnataka
Karnataka’s biotechnology sector is supported by manufacturers like Uma Pharmatech Machinery, specializing in bioreactor solutions.
Bioreactor Manufacturers in West Bengal
West Bengal’s industries, including biotechnology, benefit from manufacturers like Uma Pharmatech Machinery.
Bioreactor Manufacturers in Himachal Pradesh
Himachal Pradesh’s biotech sector thrives with manufacturers like Uma Pharmatech Machinery providing essential equipment.
Bioreactor Manufacturers in Manipur
Manipur’s biotechnology industry relies on manufacturers like Uma Pharmatech Machinery, recognized for their bioreactor expertise.
Bioreactor Manufacturers in Rajkot
Rajkot’s industries benefit from bioreactor manufacturers like Uma Pharmatech Machinery, known for their quality equipment.
Bioreactor Manufacturers in Ahmedabad
Ahmedabad’s biotech sector thrives with manufacturers like Uma Pharmatech Machinery, specializing in bioreactor solutions.
Bioreactor Manufacturers in Kerala
Kerala’s reputation for precision aligns with manufacturers like Uma Pharmatech Machinery, recognized for their bioreactor expertise.
Bioreactor Manufacturers in Punjab
Punjab’s biotechnology industry benefits from manufacturers such as Uma Pharmatech Machinery, known for their bioreactor solutions.
Bioreactor Manufacturers in Pune
Pune’s thriving industrial landscape is supported by bioreactor manufacturers, including Uma Pharmatech Machinery, known for its quality equipment.
Bioreactor Manufacturers in Chhattisgarh
Chhattisgarh’s biotech sector relies on manufacturers like Uma Pharmatech Machinery, recognized for their bioreactor expertise.
Bioreactor Manufacturers in Madhya Pradesh
Madhya Pradesh’s biotechnology industry thrives with manufacturers like Uma Pharmatech Machinery providing essential equipment.
Bioreactor Manufacturers in Germany
Germany’s reputation for precision aligns with manufacturers like Uma Pharmatech Machinery, specializing in bioreactor production.
Bioreactor Manufacturers in Australia
Australia’s biotechnology sector is supported by manufacturers such as Uma Pharmatech Machinery, known for their quality equipment.
Bioreactor Manufacturers in Russia
Russia’s biotech industry relies on manufacturers like Uma Pharmatech Machinery, recognized for their bioreactor expertise.
Bioreactor Manufacturers in Nigeria
Nigeria’s industries, including biotechnology, benefit from manufacturers like Uma Pharmatech Machinery.
Bioreactor Manufacturers in Morocco
Morocco’s biotech sector thrives with manufacturers like Uma Pharmatech Machinery providing essential equipment.
Bioreactor Manufacturers in Vietnam
Vietnam’s reputation for precision aligns with manufacturers like Uma Pharmatech Machinery, known for their bioreactor expertise.
Bioreactor Manufacturers in Algeria
Algeria’s biotechnology industry benefits from manufacturers such as Uma Pharmatech Machinery, known for their bioreactor solutions.
Bioreactor Manufacturers in Thailand
Thailand’s biotech sector relies on manufacturers like Uma Pharmatech Machinery, recognized for their bioreactor expertise.
Bioreactor Manufacturers in UAE
The UAE’s thriving industrial landscape is supported by bioreactor manufacturers, including Uma Pharmatech Machinery, known for its quality equipment.
Bio fermentor components
A bio fermentor is made up of a number of parts that are essential to the fermentation process. The following are a bio fermenter’s main parts:
Vessel Design Of Bioreactor
The vessel is the holding container for the culture medium and offers the ideal conditions for microbial development. It is constructed of substances like plastic, glass, or stainless steel.
Agitator Of Bio Fermenter
The agitator is a tool that mechanically stirs the contents of the vessel to ensure that nutrients, oxygen, and microbes are properly mixed.
Spurger Air Line
The Air Spargar is a tool that adds air or oxygen to the culture medium to satisfy the microorganisms’ need for oxygen.
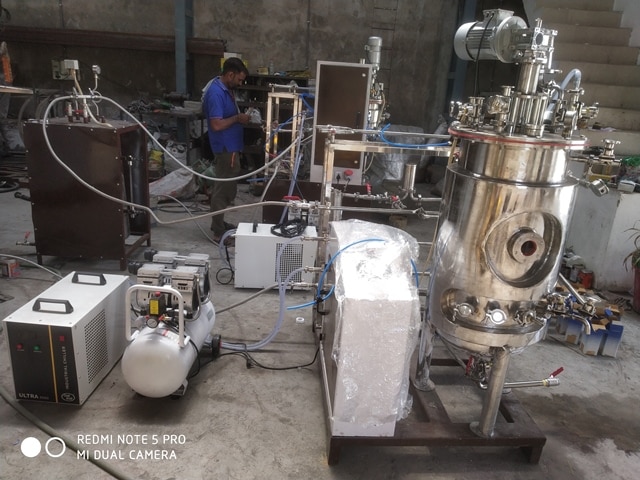
Brewers cannot produce high-quality beer, wine, or other fermented beverages without the use of fermenters, which are an integral part of the brewing process. A burgeoning market in Haryana exists for premium fermenters that may satisfy the demands of regional brewers. In this post, we will examine the many fermenter types that are offered in Haryana and offer some suggestions for choosing the ideal fermenter for your requirements.
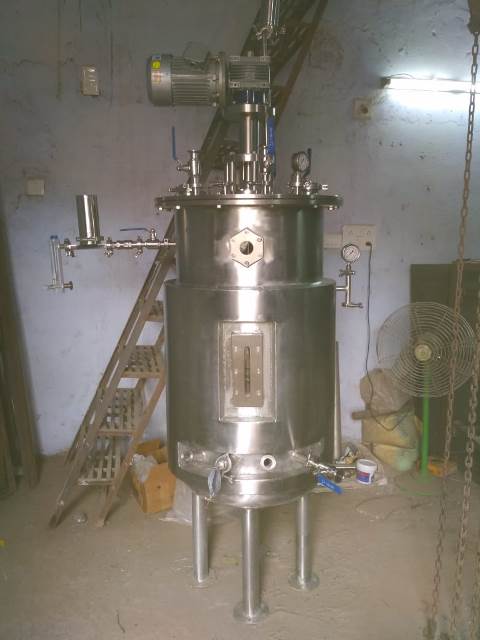
What are the two types of bioreactors?
Certainly! This page discusses the uses for bioreactors, sometimes referred to as biofermentors or bioreactors.
Bioreactor Applications
For the large-scale manufacturing of bioproducts, bioreactors, also known as biofermentors or bioreactors, are extensively utilized in a variety of sectors. A bioreactor is a container that offers an environment ideal for the development of microbial, plant, or animal cells under regulated environmental conditions. UPM shall talk about the numerous uses of bioreactors in this article.
Various MBR Types
MBRs come in two major varieties: side-stream and submerged. Municipal wastewater treatment facilities commonly use submerged MBRs, which are the most prevalent type. Although less frequent, side-stream MBRs provide a number of benefits, including higher flux rates and lower fouling rates.
Whereas side-stream MBRs employ a separate membrane filtering tank, submerged MBRs use membrane modules that are submerged in the aeration tanks. The application and the desired effluent quality are two important considerations when choosing an MBR type.
When compared to conventional wastewater treatment techniques, MBRs provide a number of advantages, such as high-quality effluent, a compact design, and enhanced dependability. Aeration tanks, membrane modules, and a filtering system are among the essential parts of a conventional MBR system. MBRs come in two primary varieties: submerged and side-stream, each with specific benefits. MBRs are absolutely something to think about if you want to increase the effectiveness and dependability of your wastewater treatment system.
A suggested mermaid diagram is provided below to show the essential elements of a typical MBR system:
Application Of Fermenter and Bioreactors
With good cause, membrane bioreactors (MBRs) have gained popularity in the wastewater treatment industry. This cutting-edge technique combines membrane filtration with the conventional biological process to produce a more effective and dependable procedure.
In this post, we’ll look at the advantages of employing MBRs to treat wastewater as well as the essential elements of a typical MBR system. We will also go over the various MBR types and each one’s advantages.
Advantages of MBR Use in Wastewater Treatment
When compared to conventional wastewater treatment techniques, MBRs provide a number of advantages. Its capacity to generate high-quality effluent that satisfies stringent regulatory standards is one of their key advantages. Combining biological treatment with membrane filtration, which eliminates germs and suspended particles, accomplishes this.
MBRs also have the advantage of having a lower footprint than conventional wastewater treatment systems thanks to their compact construction. They are therefore perfect for use in small spaces. MBRs also offer superior process control and require less maintenance, increasing dependability and uptime.
Important Elements of an MBR System
Aeration tanks, membrane modules, and a filtering system are among the essential parts of a conventional MBR system. The biological treatment is carried out in the aeration tanks, and the suspended particles and bacteria are removed from the treated water by the membrane modules. The filtration system ensures that the effluent complies with regulatory criteria by removing any leftover particles and germs.
Fermenter Manufacturers
Uma Pharmatech Machinery, a pioneering fermenter manufacturer and bioreactor manufacturer based in Jamshedpur, India, stands as a beacon of innovation and quality. With a comprehensive range of solutions, they lead the league of industrial fermenter and bioreactor suppliers across India’s vibrant landscape. Their expertise extends nationwide, spanning cities like Mumbai, Delhi, Kolkata, and beyond, as well as catering to international markets, including the USA, UK, and UAE.
Industrial Fermenter
Fermenter Suppliers
Bioreactor Suppliers
For research endeavors, their range encompasses the efficient laboratory fermenter for cell culture, while for larger operations, they stand tall as industrial fermenter manufacturers and pilot-scale fermenter manufacturers. In the realm of biofertilizer production, Uma Pharmatech Machinery’s fermenters shine, just as their bioreactors excel in enzyme production setups.
Fermenter Manufacturing Companies in India
Bioreactor Manufacturing Companies in India
Fermenter For Biofertilizer Production
As one of the foremost fermenter manufacturing companies in India and bioreactor manufacturing companies in India, Uma Pharmatech Machinery crafts cutting-edge equipment like the sought-after automatic fermenter and sturdy fermentation tanks. While ensuring top-tier quality, they remain sensitive to the cost of fermenter and bioreactor price, making advanced solutions accessible across scales.
Fermentation Tank Manufacturers
As trailblazing fermentation tank manufacturers, we redefine the art of large-scale bioprocessing. Our tanks embody precision engineering, fostering optimal microbial growth and product yields. From pharmaceuticals to food, our vessels provide the foundation for successful fermentation processes. With a commitment to innovation, we elevate industrial fermentation, delivering equipment that empowers progress.
Cost Of Fermenter, Bioreactor Price
Navigating the path of progress shouldn’t be hindered by budget concerns. Discover competitive solutions with transparency in the cost of fermenter. Our offerings ensure affordability without compromising quality. With a range of options, you can access cutting-edge fermentation equipment tailored to your requirements, driving efficiency and innovation.
Production Fermenter Manufacturers
Uma Pharmatech Machinery’s influence reaches across India’s expanse, including states like Maharashtra, Uttar Pradesh, and Tamil Nadu, fostering progress from Jamshedpur to Mumbai and Chennai. Their excellence isn’t confined to national boundaries; they are distinguished fermenter exporters and bioreactor exporters with a global footprint.
Laboratory Fermenter Cost
Unveil the future of research with our cost-effective laboratory fermenter solutions. We understand the significance of budget-conscious science, offering high-quality equipment at competitive prices. Our lab fermenters enable precise cultivation of microorganisms, yielding valuable insights across various fields. Embrace affordability without compromising on performance, driving innovation from the lab bench to publications and beyond.
Industrial Fermenter Manufacturers
As pioneers among industrial fermenter manufacturers, we shape the landscape of large-scale bioprocessing. With a legacy of engineering excellence, we craft fermenters that power diverse industries. From pharmaceuticals to biofuels, our robust equipment ensures consistent production and optimal yields. With a focus on quality and innovation, we stand as partners in progress, enabling seamless industrial fermentation for a sustainable future.
Pilot Scale Fermenter Manufacturers
Crafted with precision, their stainless-steel fermenters and glass fermenters reflect unmatched dedication. As the sun never sets on Uma Pharmatech Machinery’s commitment to excellence, they continue to illuminate the path for fermenter and bioreactor solutions, enriching laboratories, industries, and landscapes across the world.
Bioreactor For Enzymes Production
Our advanced bioreactor for enzymes production stands at the forefront of biotechnology. Engineered for precision and efficiency, it’s the cornerstone of enzymatic processes. From pharmaceuticals to food and beyond, our bioreactor ensures optimized yields and consistent quality. With innovative design and automation, it streamlines enzyme cultivation, reducing production timelines and costs. Embrace the power of cutting-edge technology for enzymatic excellence.
Laboratory Fermenter For Cell Culture
In the realm of research, our laboratory fermenter for cell culture is a testament to innovation. Tailored for controlled growth environments, it nurtures cells for diverse applications. From studying disease mechanisms to producing biologics, our fermenter enables reproducible results. With precise control over parameters, it mirrors in vivo conditions, advancing scientific understanding. Elevate your cell culture research with a versatile and reliable laboratory fermenter, propelling breakthroughs from bench to bedside.
Fermenter Exporters
Bioreactor Exporters
As premier bioreactor exporters, we bridge scientific frontiers globally. Our cutting-edge bioreactors empower industries, facilitating advanced research and production. We’re committed to driving innovation across international borders, delivering tailored solutions to diverse biotech sectors. With precision engineering and quality assurance, our bioreactors redefine possibilities, nurturing progress on a global scale.
Stainless Steel Fermenter Manufacturers
Crafting excellence, we stand as leading stainless steel fermenter manufacturers. Our vessels uphold the highest standards, blending robustness with hygiene. Catering to diverse applications, we empower industries with reliable equipment. From pharmaceuticals to biofuels, our fermenters lay the foundation for success, ensuring optimal outcomes and seamless operations.
Glass Fermenter Suppliers
As dedicated glass fermenter suppliers, transparency is our hallmark. We provide vessels that foster observation and control, vital for research and process optimization. Our glass fermenters, designed with precision, cater to microbiology, biopharma, and more. With a commitment to clarity, we empower scientists and engineers to visualize progress, sparking advancements across scientific landscapes.
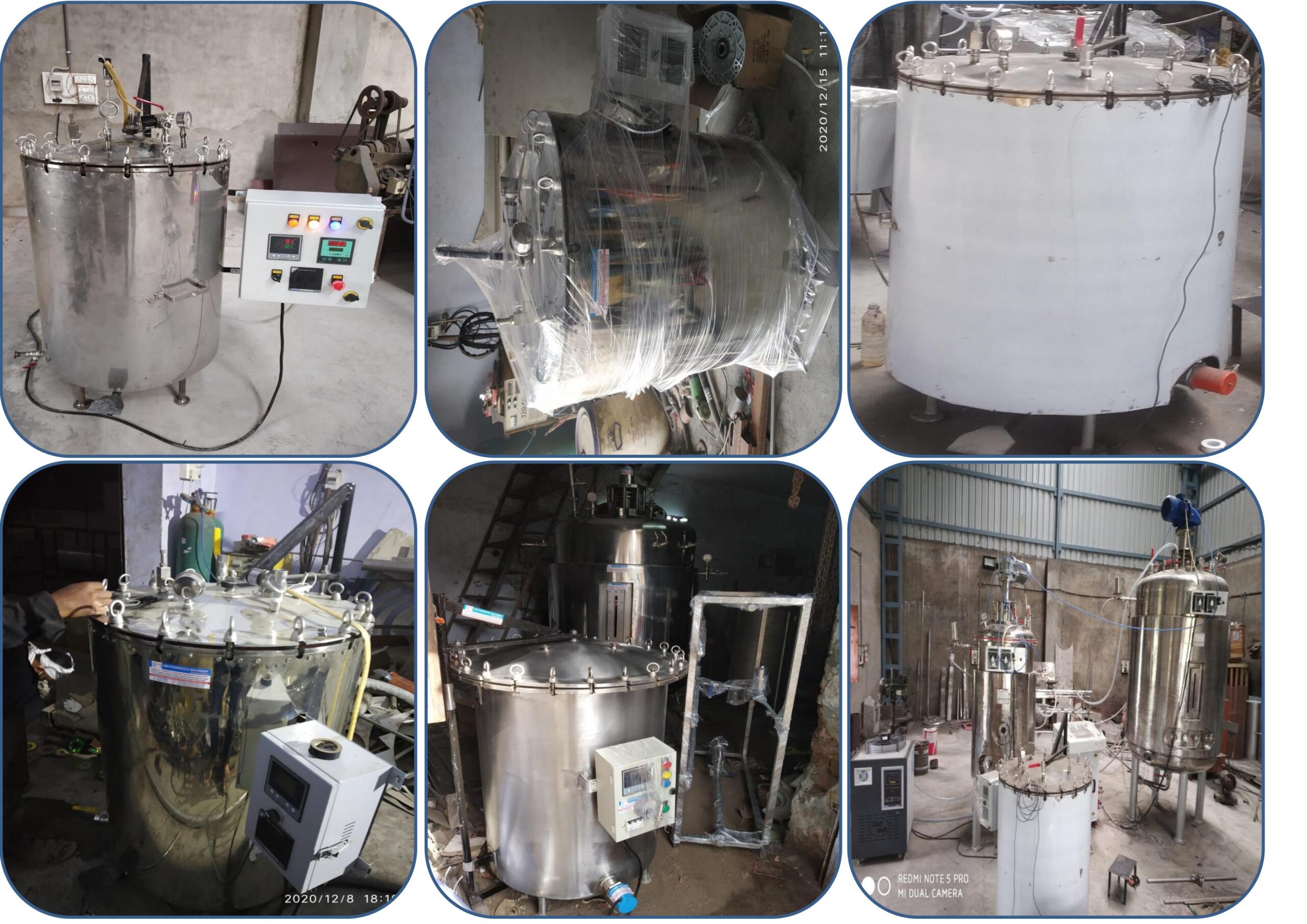
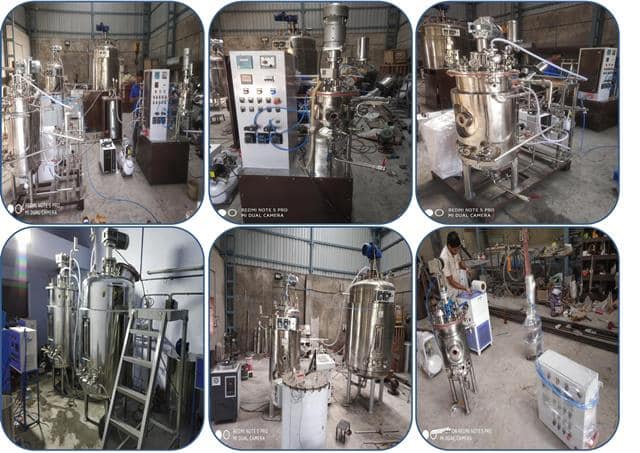
How a fermenter Works
Inoculation, growth, and production are a few of the stages that make up the fermentation process in a biofermentors. The fermentation process starts when the microorganisms are added to the culture medium during the inoculation step. The microorganisms proliferate exponentially during the growth stage, whereas the accumulation of the desired product occurs during the production stage.
The Uses of Bioreactors
There are several uses for Pilot Scale biofermentors, such as:
Production of Biofuels Biofermentors are used to turn renewable resources like corn, sugarcane, and algae into biofuels like ethanol, butanol, and biodiesel.