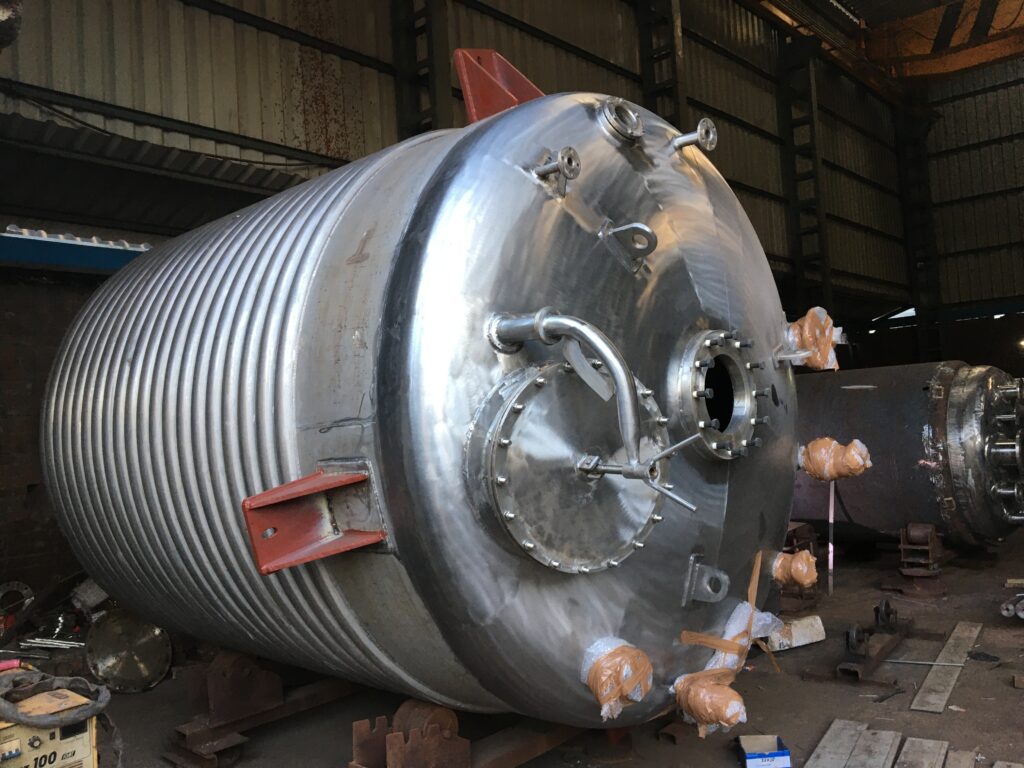
VESSEL MANUFACTURER IN SURAT
https://hymnsandhome.com/2024/07/25/qnt1ab6y6f3 Uma Pharmatech Machinery, based in the thriving city of source link Ahmedabad, Gujarat, proudly serves as a premier vessel manufacturer in Surat. Recognized for their steadfast commitment to quality and innovation, Uma Pharmatech Machinery provides top-tier vessels to meet the diverse industrial needs of Surat and its neighboring areas. Specializing in various types of vessels, they ensure that each product complies with stringent safety and quality standards. Whether it’s pressure vessels, storage vessels, or mixing vessels, Uma Pharmatech Machinery offers tailored solutions to address Surat’s unique industrial requirements. Industries in Surat, spanning pharmaceuticals, chemicals, and manufacturing, rely on Uma Pharmatech Machinery for their trusted vessel manufacturing expertise in the region, reinforcing their position as an industry leader.
For click here Vessel Manufacturer In SURAT, Uma Pharmatech Is Trusted follow link Manufacturer and Supplier In Surat. UPM Involve In Research, Design, Manufacturing, and Service In Gujarat For https://autismwish.org/tgimza9 Vessel Manufacturer and Supplier.
Experience is one of the first qualities to look for when choosing a vessel manufacturer. You should look for a company with a long history of success and extensive commercial experience. This will provide you peace of mind that they have the experience and understanding to tackle any project, no matter how big or small it may be.
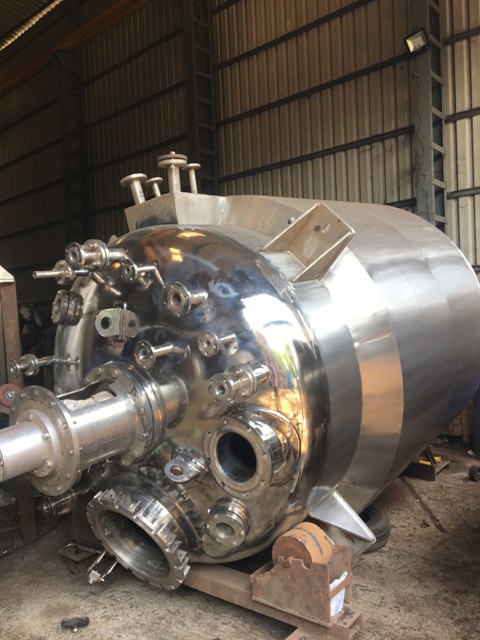
UPM Is Pioneer Manufacturer and Fabricator Of Industrial Reactor and source Chemical Reactor In Surat. in India UPM Is Top Most Leading Manufacturer Of https://living4youboutique.com/jv0xav09t1a Chemical Reactor Vessel. Our SS Reactor and Vessel Used In Various Chemical Industries For Manufacturing Of Colors, Dyes, Chemical, Pigments, Agro Chemical Etc..
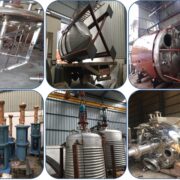
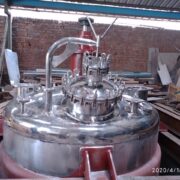
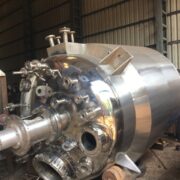
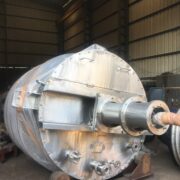
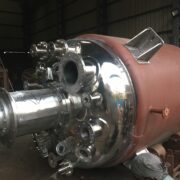
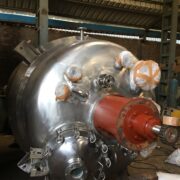
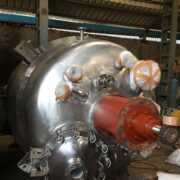
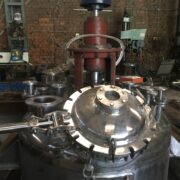
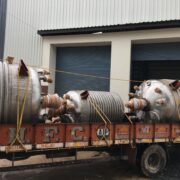
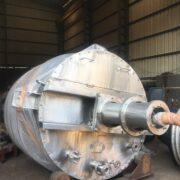
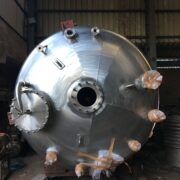
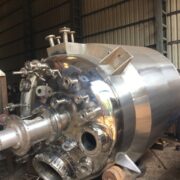
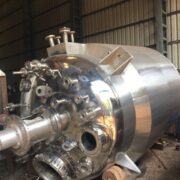
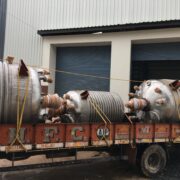
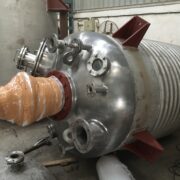
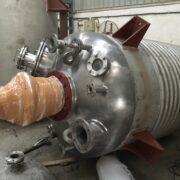
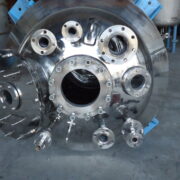

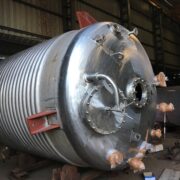
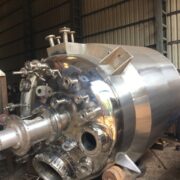
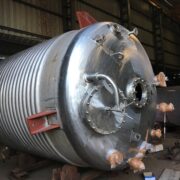
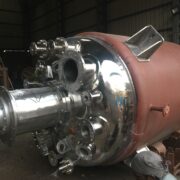
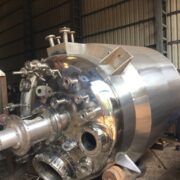
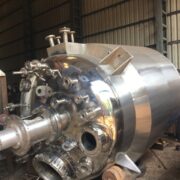
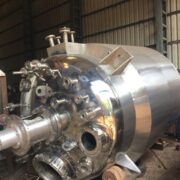
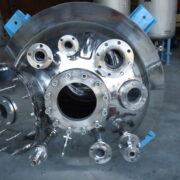
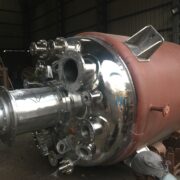
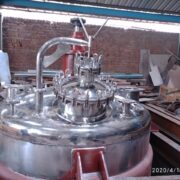
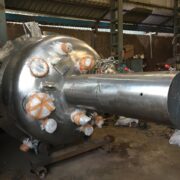
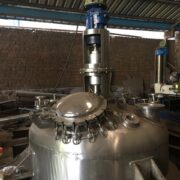
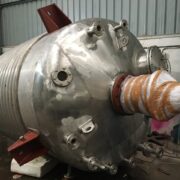
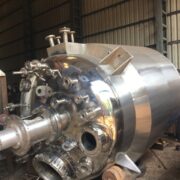
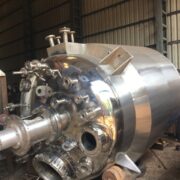
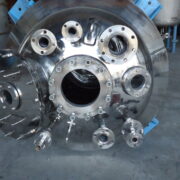
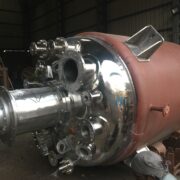
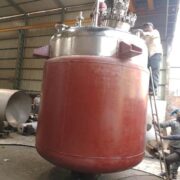
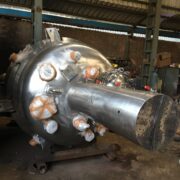
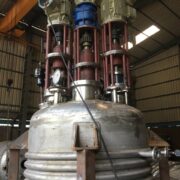
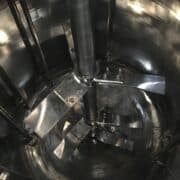
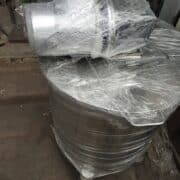

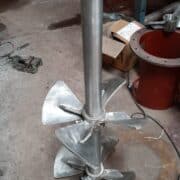
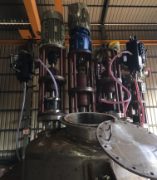
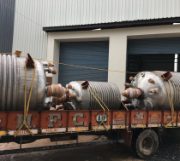

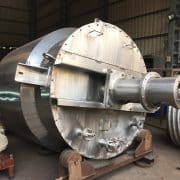
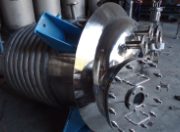
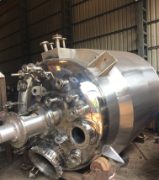
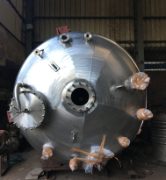
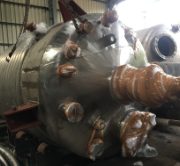
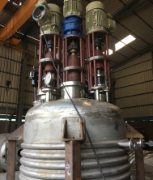
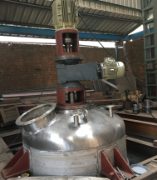
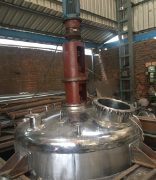
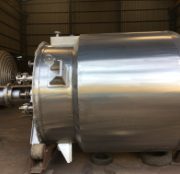
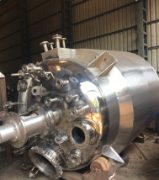
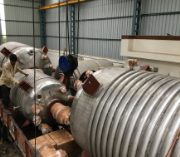
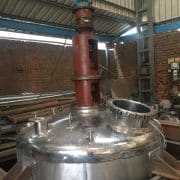
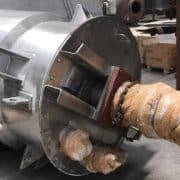
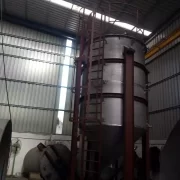
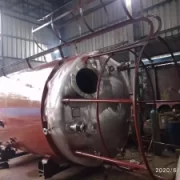
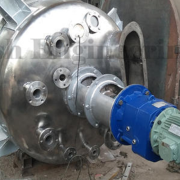
- SS Vessel Manufacturers
- Mixing Vessel Manufacturers
- Storage Vessel Manufacturers
- SS Mixing Vessel Manufacturers
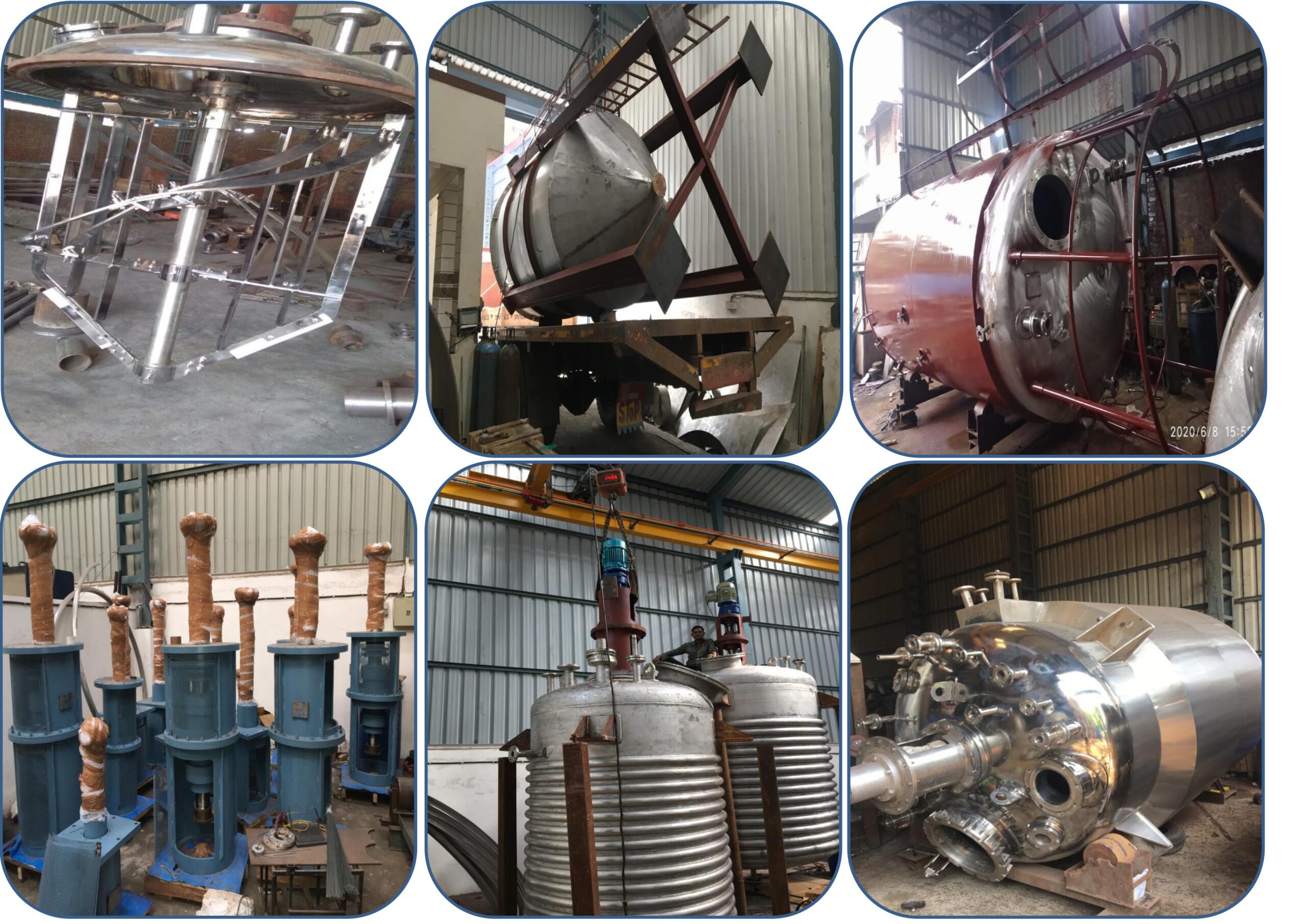
SS Vessel Manufacturers
Uma Pharmatech Machinery Company stands out among enter SS vessel manufacturers for its exceptional quality and precision engineering. Specializing in stainless steel vessel fabrication, Uma Pharmatech ensures top-tier products for various industries. Their vessels are meticulously crafted to meet rigorous industry standards, ensuring durability and safety.
What sets Uma Pharmatech apart is its commitment to customization. They tailor vessels to meet specific client needs, accommodating various sizes and configurations. Whether it’s for pharmaceutical, chemical, or food processing applications, Uma Pharmatech Machinery SS vessels are designed to excel. With a reputation for on-time delivery and competitive pricing, Uma Pharmatech Machinery Company remains a trusted choice for those seeking top-notch stainless steel vessels.
Manufacturers of Stainless Steel Vessel
https://www.adroitprojectconsultants.com/2024/07/25/wted60vd5 Manufacturers of stainless steel vessels play a pivotal role in various industries, and Uma Pharmatech Machinery Company is a distinguished name in this arena. Specializing in the fabrication of high-quality stainless steel vessels, Uma Pharmatech stands out for its commitment to excellence. Their vessels are renowned for their precision engineering and adherence to stringent industry standards, ensuring reliability and durability.
What sets Uma Pharmatech apart is their ability to customize vessels to meet specific requirements. Whether it’s for pharmaceutical, chemical, or food processing applications, Uma Pharmatech’s stainless steel vessels are designed with precision and care. With a reputation for delivering on-time and competitive pricing, Uma Pharmatech Machinery Company remains a trusted choice in the realm of stainless steel vessel manufacturing.
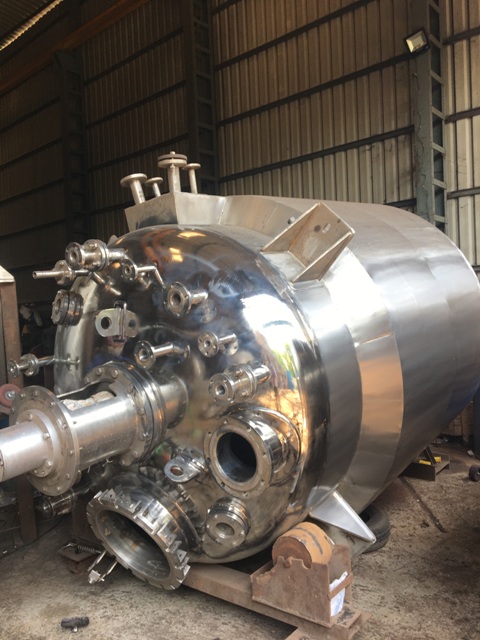
Manufacturer of Stainless Steel Mixing Vessel
When it comes to precision and reliability in the field of stainless steel mixing vessel manufacturing, look no further than follow site Uma Pharmatech Machinery Company. As a leading manufacturer of stainless steel mixing vessels, Uma Pharmatech excels in crafting high-quality, custom solutions for various industries.
Uma Pharmatech’s mixing vessels are engineered with precision and adhere to stringent quality standards, ensuring efficiency and longevity. What sets them apart is their commitment to customization, tailoring vessels to meet specific client needs. Whether it’s for pharmaceutical, chemical, or food processing applications, Uma Pharmatech Machinery Company stands as a trusted name in delivering top-notch stainless steel mixing vessels, known for their reliability and competitive pricing.
SS Mixing Vessel Manufacturers in Gujarat
source SS Mixing Vessel Manufacturers are pivotal to industries reliant on precision mixing processes, and Uma Pharmatech Machinery Company stands as a distinguished name in this realm. Uma Pharmatech specializes in crafting top-tier stainless steel mixing vessels, renowned for their precision engineering and adherence to stringent industry standards. These vessels ensure seamless blending in pharmaceutical, chemical, and food processing applications.
Uma Pharmatech’s hallmark lies in customization; they tailor vessels to exact specifications. This versatility makes them a preferred choice for clients seeking tailored solutions. With a reputation for reliability and competitive pricing, Uma Pharmatech Machinery Company remains a trusted name in the world of stainless steel mixing vessel manufacturing.
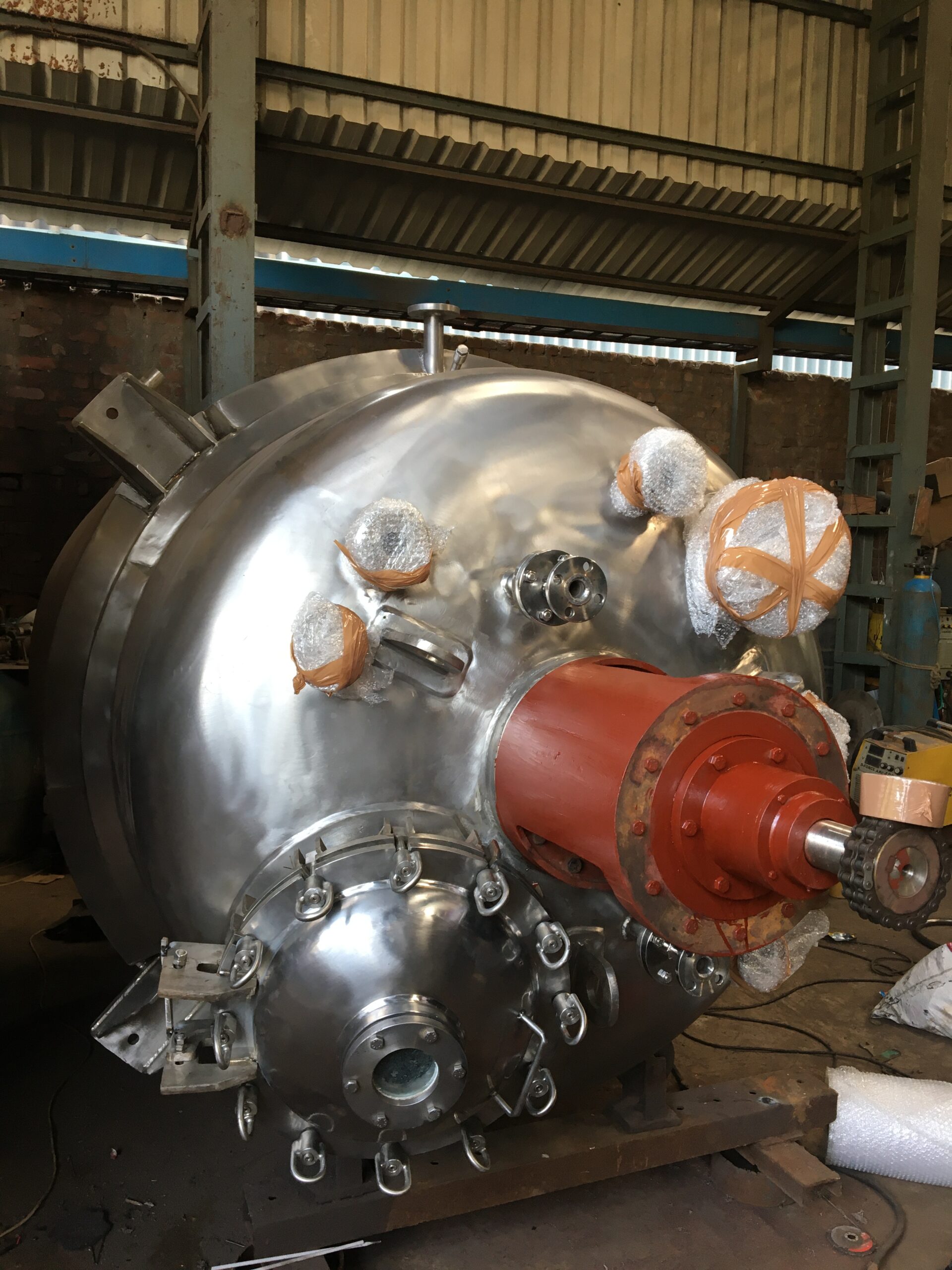
Storage Vessel Manufacturers
https://www.inaxorio.com/9ef0tps SS Storage Vessel Manufacturers play a crucial role in various industries, ensuring the safe storage of liquids and materials. Uma Pharmatech Machinery Company is a distinguished name in this field, known for its excellence in crafting stainless steel storage vessels. These vessels are meticulously designed to meet stringent industry standards, guaranteeing durability and safety in pharmaceutical, chemical, and food processing applications.
Uma Pharmatech stands out due to its customization expertise, tailoring storage vessels to precise client specifications. This commitment to flexibility, coupled with a reputation for reliability and competitive pricing, solidifies Uma Pharmatech Machinery Company’s position as a trusted leader in stainless steel storage vessel manufacturing.
Stainless Steel Storage Tank Manufacturers
https://thefooduntold.com/food-science/xbrsovii4a Stainless Steel Storage Tank Manufacturers are pivotal in ensuring the safe containment of various liquids and materials across industries. Uma Pharmatech Machinery Company stands out prominently in this domain, renowned for its impeccable craftsmanship in crafting stainless steel storage tanks. These tanks are designed with precision, adhering to stringent industry standards, guaranteeing durability and safety.
Uma Pharmatech’s unique strength lies in its ability to customize storage tanks to precise client specifications. This commitment to tailoring solutions, combined with their reputation for reliability and competitive pricing, cements Uma Pharmatech Machinery Company’s status as a trusted leader in the field of stainless steel storage tank manufacturing.
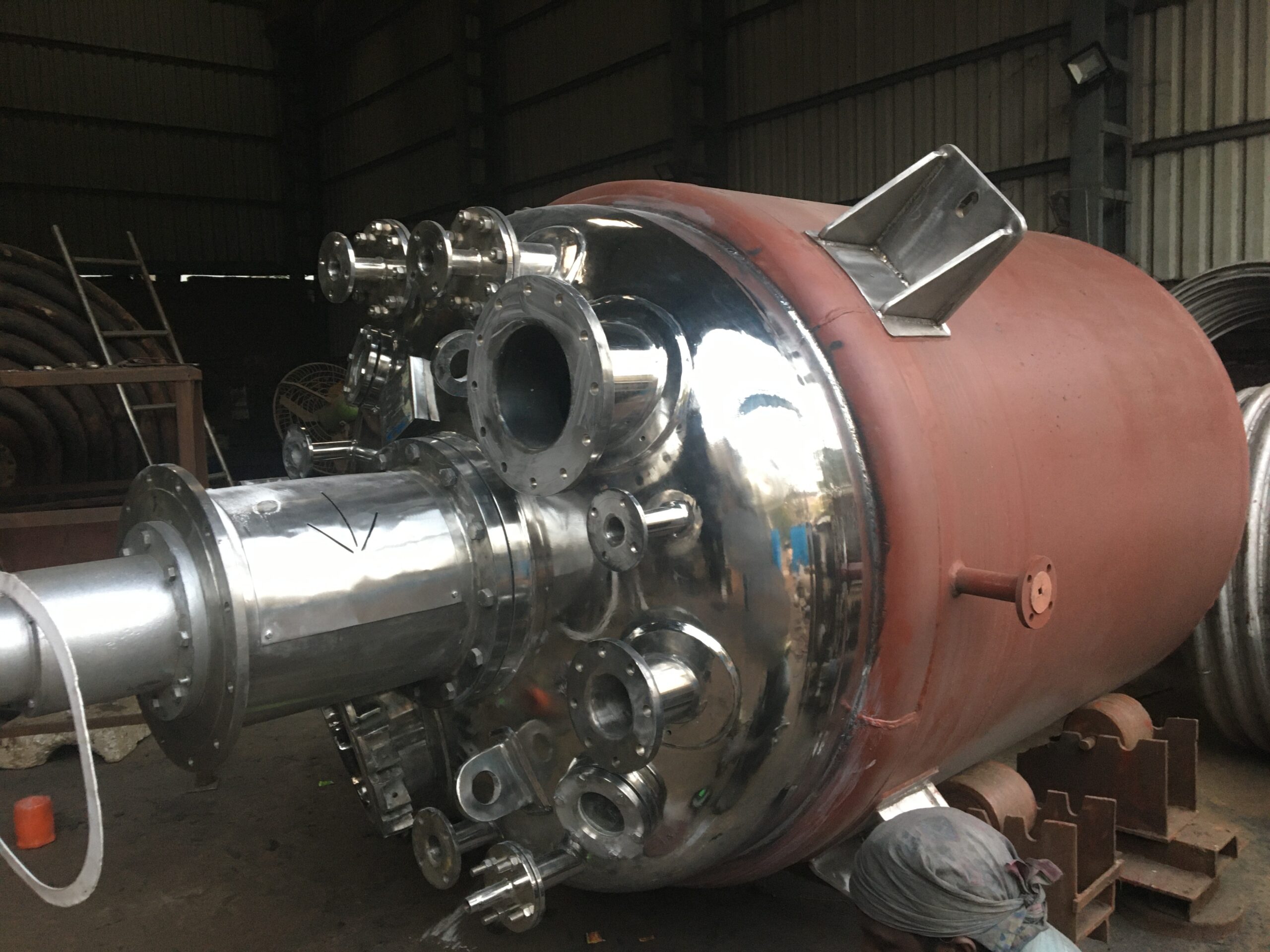
SS Mixing Vessel Manufacturers
source SS Mixing Vessel Manufacturers are the backbone of industries requiring precise mixing solutions, and Uma Pharmatech Machinery Company stands at the forefront of this specialized field. Uma Pharmatech specializes in crafting high-quality stainless steel mixing vessels, renowned for their precision engineering and strict adherence to industry standards. These vessels ensure seamless blending in critical sectors like pharmaceuticals, chemicals, and food processing.
Uma Pharmatech’s differentiator lies in its ability to customize mixing vessels to precise client specifications. This versatility makes them a preferred choice for clients seeking tailor-made solutions. With a reputation for reliability and competitive pricing, Uma Pharmatech Machinery Company remains a trusted name in the world of stainless steel mixing vessel manufacturing.
Manufacturers of Stainless Steel Mixing Tank
https://brako.com/en/mxsxcg0 Manufacturers of Stainless Steel Mixing Tanks are essential to industries reliant on precision blending, and Uma Pharmatech Machinery Company shines in this domain. Uma Pharmatech excels in crafting high-quality stainless steel mixing tanks, known for their precision engineering and adherence to rigorous industry standards. These tanks are vital for seamless mixing processes in pharmaceuticals, chemicals, and food production.
What sets Uma Pharmatech apart is their knack for customization, tailoring tanks to exact client specifications. This flexibility makes them a favored choice for clients seeking tailor-made solutions. With a reputation for reliability and competitive pricing, Uma Pharmatech Machinery Company remains a trusted name in stainless steel mixing tank manufacturing.
see What is mixing vessel?
https://hymnsandhome.com/2024/07/25/y91qaeirae how mixing vessel works?
Uma Pharmatech Manufacture Cost Effective and Low Cost of follow url Vessel Manufacturer In surat Gujarat. We Provide High Strength Vessel As Per ASME Standard. Our Expertise in Design and Manufacturing Of https://www.inaxorio.com/e54lmyw2u Agitator For Vessel and Reactor.
https://geneticsandfertility.com/uw2ooiz Different stainless steel material used for vessel manufacturing:
The production of vessels uses a variety of stainless steel materials. The particular requirements of the vessel use, such as corrosion resistance, mechanical strength, temperature resistance, and hygienic qualities, determine the type of stainless steel that should be used. Some of the most popular stainless steel materials for making vessels are listed below:
304 stainless steel: Because of its superior corrosion resistance, ease of maintenance, and affordability, 304 stainless steel is frequently used to make vessels. In addition to water treatment and chemical processing, it is appropriate for the majority of food and beverage processing applications.
316 Stainless Steel: Compared to 304, 316 stainless steel is more corrosion-resistant, making it appropriate for use in harsher settings including chemical processing and maritime applications. It has more nickel and molybdenum, which improves its ability to resist corrosion.
Duplex stainless steel is a high-strength, corrosion-resistant metal that is used to make vessels that need to be resistant to stress corrosion cracking and pitting. It is frequently employed in chemical processing as well as the oil and gas industry.
Stainless steel 904L is a high-alloy austenitic stainless steel that is extremely corrosion-resistant in a variety of harsh conditions. The chemical, pharmaceutical, and food processing sectors all frequently employ it.
The proper stainless steel material for a vessel will be chosen based on the particular needs of the application. The method of manufacture, the accessibility of the component, and any applicable regulations are further considerations.
https://www.adroitprojectconsultants.com/2024/07/25/nnnriul6a Benifits of ss316 vessels:
Depending on the application, stainless steel 316 (SS316) vessels provide a number of advantages over other materials. The following are some advantages of using SS316 vessels:
Corrosion resistance: Because of its strong corrosion resistance qualities, SS316 is appropriate for usage in hostile settings where other materials might gradually deteriorate. In addition to being extremely resistant to alkalis, acids, and chlorides, it is also highly resistant to pitting and crevice corrosion.
Resistance to high temperatures: SS316 has a good high-temperature resistance, making it appropriate for use in applications involving high temperatures. It is the perfect choice for high-temperature applications like chemical processing and oil and gas processing because it can resist temperatures of up to 1600°F (870°C).
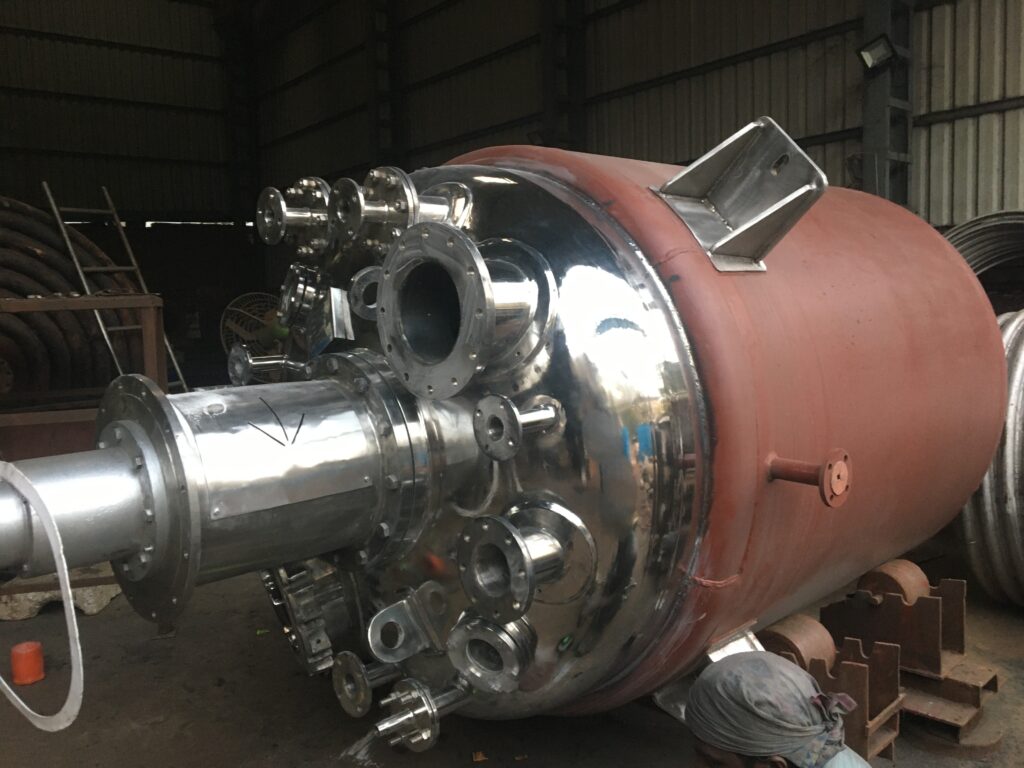
https://thefooduntold.com/food-science/dwdsk51 limpet coil vs jacketed vessel, which is effective?
https://www.techonicsltd.com/uncategorized/hbx4vj1nal limpet coil vs jacketed vessel, which is cost effective?
Our Manufacturing Product Range
SS Vessel Manufacturers
SS Vessel Manufacturers in Gujarat
Tramadol Purchase Uk SS Vessel Manufacturers in Gujarat are crucial players in the industrial landscape, and Uma Pharmatech Machinery Company proudly stands out among them. Based in Gujarat, Uma Pharmatech specializes in crafting top-quality stainless steel vessels. These vessels are engineered with precision and adhere to stringent industry standards, ensuring reliability and longevity.
What sets Uma Pharmatech apart is its unwavering commitment to customization, tailoring vessels to exact client specifications. Whether for pharmaceuticals, chemicals, or food processing, Uma Pharmatech’s stainless steel vessels are designed to excel. With a reputation for on-time delivery and competitive pricing, Uma Pharmatech Machinery Company is the trusted choice for those seeking superior stainless steel vessels in Gujarat.
SS Vessel Manufacturers in Ahmedabad
get link SS Vessel Manufacturers in Ahmedabad play a pivotal role in meeting the industrial demands of the region, and Uma Pharmatech Machinery Company stands as a distinguished name among them. Based in Ahmedabad, Uma Pharmatech specializes in crafting top-quality stainless steel vessels. These vessels are meticulously engineered to meet stringent industry standards, ensuring durability and safety.
Uma Pharmatech’s unique strength lies in its commitment to customization, tailoring vessels precisely to client specifications. Whether for pharmaceuticals, chemicals, or food processing, Uma Pharmatech’s stainless steel vessels are designed to excel. With a reputation for on-time delivery and competitive pricing, Uma Pharmatech Machinery Company is the trusted choice for superior stainless steel vessels in Ahmedabad.
SS Vessel Manufacturers in Vadodara
follow link SS Vessel Manufacturers in Vadodara are pivotal to the region’s industrial landscape, and Uma Pharmatech Machinery Company proudly leads the way. Situated in Vadodara, Uma Pharmatech specializes in crafting high-quality stainless steel vessels. These vessels are precision-engineered, meeting stringent industry standards, ensuring longevity and safety.
Uma Pharmatech’s unique advantage lies in its dedication to customization, tailoring vessels precisely to client requirements. Whether for pharmaceuticals, chemicals, or food processing, Uma Pharmatech’s stainless steel vessels excel. Renowned for on-time delivery and competitive pricing, Uma Pharmatech Machinery Company stands as the trusted choice for exceptional stainless steel vessels in Vadodara.
SS Vessel Manufacturers in Surat
https://splendormedicinaregenerativa.com/udil6mn37 SS Vessel Manufacturers in Surat, specifically within the Sachin GIDC area, play a pivotal role in catering to the industrial needs of this thriving region. Among them, go to site Uma Pharmatech Machinery Company emerges as a standout name. Located in Surat-Sachin GIDC, Uma Pharmatech specializes in crafting high-quality stainless steel vessels. These vessels are meticulously engineered, adhering to stringent industry standards, ensuring both durability and safety.
Uma Pharmatech’s unique strength lies in its unwavering commitment to customization, tailoring vessels precisely to meet each client’s unique requirements. Whether for pharmaceuticals, chemicals, or food processing, Uma Pharmatech’s stainless steel vessels excel. Renowned for on-time delivery and competitive pricing, Uma Pharmatech Machinery Company stands as the trusted choice for exceptional stainless steel vessels in Surat, particularly within the Sachin GIDC area.
SS Vessel Manufacturers in Ankleshwar
https://www.insearchofsukoon.com/m3vjojtxx SS Vessel Manufacturers in Ankleshwar are instrumental in catering to the industrial demands of the region, and at the forefront of this sector stands Tramadol Purchase Online Uma Pharmatech Machinery Company. Located in Ankleshwar, Uma Pharmatech specializes in the production of high-quality stainless steel vessels. These vessels are precision-engineered, meeting rigorous industry standards to ensure longevity and safety in various applications.
Uma Pharmatech’s unique strength lies in its unwavering commitment to customization, tailoring vessels to meet the exact specifications of each client. Whether used in pharmaceuticals, chemicals, or food processing, Uma Pharmatech’s stainless steel vessels consistently deliver outstanding performance. With a reputation for punctual delivery and competitive pricing, Uma Pharmatech Machinery Company is the trusted choice for superior stainless steel vessels in Ankleshwar.
SS Vessel Manufacturers in Bharuch
https://living4youboutique.com/9aksev0ixa4 SS Vessel Manufacturers in Bharuch play a pivotal role in meeting the industrial needs of this thriving region, and Uma Pharmatech Machinery Company proudly leads the way. Situated in Bharuch, Uma Pharmatech specializes in crafting high-quality stainless steel vessels. These vessels are precision-engineered, meeting stringent industry standards, ensuring longevity and safety in diverse applications.
Uma Pharmatech’s unique advantage lies in its dedication to customization, tailoring vessels precisely to client requirements. Whether for pharmaceuticals, chemicals, or food processing, Uma Pharmatech’s stainless steel vessels excel. Renowned for on-time delivery and competitive pricing, Uma Pharmatech Machinery Company stands as the trusted choice for exceptional stainless steel vessels in Bharuch.
SS Vessel Manufacturers in Rajkot
https://gsaudemarketing.com.br/0q91iczyeyz SS Vessel Manufacturers in Rajkot play a pivotal role in supplying the industrial demands of the region, and Uma Pharmatech Machinery Company proudly takes the lead. Based in Rajkot, Uma Pharmatech specializes in crafting high-quality stainless steel vessels. These vessels are precision-engineered, adhering to stringent industry standards, ensuring durability and safety in diverse applications.
Uma Pharmatech’s unique strength lies in its unwavering commitment to customization, tailoring vessels precisely to meet each client’s specific requirements. Whether for pharmaceuticals, chemicals, or food processing, Uma Pharmatech’s stainless steel vessels excel. Renowned for on-time delivery and competitive pricing, Uma Pharmatech Machinery Company stands as the trusted choice for exceptional stainless steel vessels in Rajkot.
SS Vessel Manufacturers in Valsad
https://living4youboutique.com/aw22n86 SS Vessel Manufacturers in Valsad are vital to sustaining the industrial fabric of the region, and Uma Pharmatech Machinery Company takes a prominent position among them. Based in Valsad, Uma Pharmatech specializes in crafting top-quality stainless steel vessels. These vessels are engineered with precision, adhering to rigorous industry standards, ensuring both durability and safety.
Uma Pharmatech’s standout feature is its unwavering commitment to customization, tailoring vessels precisely to meet each client’s unique requirements. Whether for pharmaceuticals, chemicals, or food processing, Uma Pharmatech’s stainless steel vessels excel. Renowned for on-time delivery and competitive pricing, Uma Pharmatech Machinery Company stands as the trusted choice for exceptional stainless steel vessels in Valsad.
SS Vessel Manufacturers in Vapi
https://geneticsandfertility.com/i7lpzwjf SS Vessel Manufacturers in Vapi play a pivotal role in catering to the industrial needs of the region, and Uma Pharmatech Machinery Company proudly leads this niche. Situated in Vapi, Uma Pharmatech specializes in crafting high-quality stainless steel vessels. These vessels are meticulously engineered, adhering to stringent industry standards, ensuring longevity and safety in diverse applications.
Uma Pharmatech’s unique advantage lies in its dedication to customization, tailoring vessels precisely to meet client requirements. Whether for pharmaceuticals, chemicals, or food processing, Uma Pharmatech’s stainless steel vessels consistently deliver exceptional performance. Renowned for on-time delivery and competitive pricing, Uma Pharmatech Machinery Company is the trusted choice for superior stainless steel vessels in Vapi.
SS Vessel Manufacturers in Dahej
https://gsaudemarketing.com.br/4nhkjf5up SS Vessel Manufacturers in Dahej are instrumental in serving the industrial needs of this thriving region, and Uma Pharmatech Machinery Company proudly stands at the forefront. Located in Dahej, Uma Pharmatech specializes in crafting top-quality stainless steel vessels. These vessels are precision-engineered, meeting stringent industry standards to ensure durability and safety in diverse applications.
Uma Pharmatech’s unique strength lies in its unwavering commitment to customization, tailoring vessels precisely to meet each client’s unique requirements. Whether for pharmaceuticals, chemicals, or food processing, Uma Pharmatech’s stainless steel vessels consistently deliver outstanding performance. Renowned for on-time delivery and competitive pricing, Uma Pharmatech Machinery Company stands as the trusted choice for exceptional stainless steel vessels in Dahej.
Mixing Vessel Manufacturers
SS Mixing Vessel Manufacturers in Gujarat
source site Mixing Vessel Manufacturers in Gujarat are pivotal to industries relying on precision blending, and Uma Pharmatech Machinery Company stands as a distinguished leader in this sector. Operating in Gujarat, Uma Pharmatech specializes in crafting top-quality mixing vessels that meet stringent industry standards. These vessels play a critical role in pharmaceutical, chemical, and food processing applications, ensuring uniform mixing and consistency.
What sets Uma Pharmatech apart is their unwavering commitment to customization, tailoring mixing vessels precisely to client specifications. With a reputation for reliability and competitive pricing, Uma Pharmatech Machinery Company is the trusted choice for superior mixing vessels in Gujarat, delivering impeccable performance every time.
Stainless Steel Mixing Vessel Manufacturers in Ahmedabad
Tramadol Legal To Buy Stainless Steel Mixing Vessel Manufacturers in Ahmedabad are crucial for industries demanding precise blending solutions, and Uma Pharmatech Machinery Company proudly excels in this domain. Operating in Ahmedabad, Uma Pharmatech specializes in crafting high-quality stainless steel mixing vessels. These vessels are renowned for their precision engineering and strict adherence to industry standards, ensuring efficiency and durability.
Uma Pharmatech’s distinguishing feature is its dedication to customization, tailoring mixing vessels to precise client specifications. This adaptability makes them a preferred choice for clients seeking tailor-made solutions. With a reputation for reliability and competitive pricing, Uma Pharmatech Machinery Company remains the trusted leader in stainless steel mixing vessel manufacturing in Ahmedabad.
Stainless Steel Mixing Vessel Manufacturers in Vadodara
Tramadol Online Texas Stainless Steel Mixing Vessel Manufacturers in Vadodara play a pivotal role in supplying industrial demands, and Uma Pharmatech Machinery Company proudly leads this sector. Located in Vadodara, Uma Pharmatech specializes in crafting top-quality stainless steel mixing vessels. These vessels are precision-engineered, adhering to stringent industry standards, ensuring longevity and safety in various applications.
Uma Pharmatech’s unique advantage lies in its unwavering commitment to customization, tailoring mixing vessels precisely to meet each client’s unique requirements. Whether for pharmaceuticals, chemicals, or food processing, Uma Pharmatech’s stainless steel mixing vessels consistently deliver exceptional performance. Renowned for on-time delivery and competitive pricing, Uma Pharmatech Machinery Company is the trusted choice for superior mixing vessels in Vadodara.
When it comes to source link Stainless Steel Mixing Vessel Manufacturers in Vadodara, Vadodara-based Uma Pharmatech Machinery Company unquestionably leads the pack. Uma Pharmatech specializes in crafting high-quality stainless steel mixing vessels, tailored precisely to client requirements. Their precision-engineered vessels adhere to stringent industry standards, ensuring reliability and safety in pharmaceutical, chemical, and food processing applications.
Uma Pharmatech’s commitment to customization sets them apart in Vadodara’s manufacturing landscape. They excel at creating stainless steel mixing vessels that perfectly align with their clients’ unique needs. With a stellar reputation for on-time delivery, competitive pricing, and unmatched quality, Uma Pharmatech Machinery Company is Vadodara’s go-to choice for superior stainless steel mixing vessels.
Stainless Steel Mixing Vessel Manufacturers in Rajkot
When it comes to here Stainless Steel Mixing Vessel Manufacturers in Rajkot, Uma Pharmatech Machinery Company is the undisputed leader. Uma Pharmatech, hailing from Rajkot, specializes in crafting high-quality https://bxscco.com/gn4ei9n2fi stainless steel mixing vessels, ensuring precision engineering, and adhering to industry standards. These vessels play a pivotal role in pharmaceutical, chemical, and food processing applications, ensuring consistent and uniform mixing.
What sets Uma Pharmatech apart is its unwavering commitment to customization. They tailor stainless steel mixing vessels to meet precise client requirements, offering bespoke solutions. With a reputation for on-time delivery, competitive pricing, and a strong emphasis on quality, Uma Pharmatech Machinery Company is Rajkot’s premier choice for exceptional mixing vessels.
Mixing Vessel Manufacturers in Ankleshwar
https://brako.com/en/zyomjmw Mixing Vessel Manufacturers in Ankleshwar rely on precision engineering to meet the demands of various industries, and Uma Pharmatech Machinery Company excels in this domain. Uma Pharmatech, based in Ankleshwar, specializes in crafting top-quality source site mixing vessels, adhering to stringent industry standards. These vessels are indispensable in pharmaceutical, chemical, and food processing applications, ensuring consistent and uniform mixing.
Uma Pharmatech’s unique advantage is their unwavering commitment to customization. They tailor mixing vessels to meet precise client specifications, offering tailored solutions. Renowned for on-time delivery, competitive pricing, and exceptional quality, Uma Pharmatech Machinery Company stands as Ankleshwar’s preferred choice for superior mixing vessels.
Mixing Vessel Manufacturers in Bharuch
Cheapest Tramadol Uk Mixing Vessel Manufacturers in Bharuch are pivotal in catering to diverse industrial needs, and Uma Pharmatech Machinery Company takes center stage in this arena. Situated in Bharuch, watch Uma Pharmatech specializes in crafting top-tier follow mixing vessels adhering to the most stringent industry standards. These vessels play a critical role in pharmaceutical, chemical, and food processing applications, ensuring uniform and efficient mixing.
What truly sets https://www.adroitprojectconsultants.com/2024/07/25/5lit6bu Uma Pharmatech apart in Bharuch’s manufacturing landscape is its unwavering commitment to https://hymnsandhome.com/2024/07/25/dboh58y customization. They tailor mixing vessels to meet precise client specifications, providing bespoke solutions for unique requirements. With a reputation for on-time delivery, competitive pricing, and an unwavering emphasis on quality, Uma Pharmatech Machinery Company stands as Bharuch’s go-to choice for exceptional mixing vessels.
In Bharuch, the demand for mixing vessels continues to grow, and Uma Pharmatech Machinery Company rises to the occasion. Their precision-engineered vessels, meticulously crafted to meet the demands of various industries, are a testament to their commitment to excellence. For Bharuch’s industrial needs, Uma Pharmatech’s mixing vessels remain unrivaled in terms of quality, reliability, and customization options.
Mixing Vessel Manufacturers in Valsad
Mixing Vessel Manufacturers in Valsad are instrumental in supporting the diverse industrial landscape, and Uma Pharmatech Machinery Company proudly leads the way. Operating in Valsad, Uma Pharmatech specializes in crafting top-quality mixing vessels that adhere to the most stringent industry standards. These vessels are indispensable in pharmaceutical, chemical, and food processing applications, ensuring consistent and efficient mixing.
Uma Pharmatech’s distinguishing feature is its unwavering commitment to customization. They tailor mixing vessels to meet precise client specifications, providing tailor-made solutions for unique requirements. Renowned for on-time delivery, competitive pricing, and an unwavering focus on quality, Uma Pharmatech Machinery Company remains Valsad’s trusted choice for superior mixing vessels.
Mixing Vessel Manufacturers in Vapi
Mixing Vessel Manufacturers in Vapi are pivotal in supporting the industrial fabric of the region, and leading this sector is Uma Pharmatech Machinery Company. Situated in Vapi, Uma Pharmatech specializes in crafting top-quality mixing vessels, meticulously engineered to meet the most stringent industry standards. These vessels are indispensable in pharmaceutical, chemical, and food processing applications, ensuring uniform and efficient mixing.
What truly sets Uma Pharmatech apart is its unwavering commitment to customization. They tailor mixing vessels to meet precise client specifications, delivering bespoke solutions for unique requirements. Renowned for on-time delivery, competitive pricing, and a steadfast focus on quality, Uma Pharmatech Machinery Company remains Vapi’s preferred choice for exceptional mixing vessels.
Mixing Vessel Manufacturers in Dahej
Mixing Vessel Manufacturers in Dahej play a pivotal role in serving the industrial needs of this thriving region, and Uma Pharmatech Machinery Company proudly stands at the forefront. Located in Dahej, Uma Pharmatech specializes in crafting high-quality mixing vessels that adhere to the most stringent industry standards. These vessels are indispensable in pharmaceutical, chemical, and food processing applications, ensuring consistent and efficient mixing.
What truly sets Uma Pharmatech apart is its unwavering commitment to customization. They tailor mixing vessels to meet precise client specifications, offering bespoke solutions for unique requirements. Renowned for on-time delivery, competitive pricing, and an unwavering focus on quality, Uma Pharmatech Machinery Company remains Dahej’s preferred choice for superior mixing vessels.
Storage Vessel Manufacturers
SS Storage Vessel Manufacturers in Gujarat
SS Storage Vessel Manufacturers in Gujarat are vital to industries reliant on safe material storage, and Uma Pharmatech Machinery Company stands as a beacon in this sector. Operating within Gujarat, Uma Pharmatech specializes in crafting top-quality stainless steel storage vessels. These vessels are meticulously engineered, adhering to the most stringent industry standards, ensuring both durability and safety in various applications.
Uma Pharmatech’s unique advantage is its unwavering commitment to customization. They tailor storage vessels to meet precise client specifications, offering tailored solutions for unique requirements. With a reputation for on-time delivery, competitive pricing, and a steadfast focus on quality, Uma Pharmatech Machinery Company is Gujarat’s preferred choice for exceptional stainless steel storage vessels.
SS Storage Vessel Manufacturers in Rajkot
SS Storage Vessel Manufacturers in Rajkot are indispensable to various industries, and Uma Pharmatech Machinery Company shines brightly in this domain. Based in Rajkot, Uma Pharmatech specializes in crafting high-quality stainless steel storage vessels engineered to meet the most stringent industry standards. These vessels are crucial for safe material storage in pharmaceutical, chemical, and food processing applications.
Uma Pharmatech’s standout feature is its dedication to customization. They tailor storage vessels precisely to meet the unique requirements of each client, providing bespoke solutions. With a reputation for on-time delivery, competitive pricing, and unwavering commitment to quality, Uma Pharmatech Machinery Company remains Rajkot’s trusted choice for superior stainless steel storage vessels.
SS Storage Vessel Manufacturers in Ahmedabad
SS Storage Vessel Manufacturers in Ahmedabad are instrumental in providing reliable storage solutions, and Uma Pharmatech Machinery Company excels in this field. Based in Ahmedabad, Uma Pharmatech specializes in crafting high-quality stainless steel storage vessels that adhere to rigorous industry standards. These vessels are essential for safe material storage in pharmaceutical, chemical, and food processing applications.
Uma Pharmatech’s distinguishing feature is its unwavering commitment to customization. They tailor storage vessels precisely to meet each client’s unique requirements, offering bespoke solutions. Renowned for on-time delivery, competitive pricing, and an unwavering focus on quality, Uma Pharmatech Machinery Company is Ahmedabad’s preferred choice for exceptional stainless steel storage vessels.
SS Storage Vessel Manufacturers in Vadodara
SS Storage Vessel Manufacturers in Vadodara play a pivotal role in industries relying on secure material storage, and Uma Pharmatech Machinery Company leads the way in this sector. Located in Vadodara, Uma Pharmatech specializes in crafting top-quality stainless steel storage vessels engineered to meet the most stringent industry standards. These vessels are indispensable for the safe storage of materials in pharmaceutical, chemical, and food processing applications.
Uma Pharmatech’s unique advantage is its unwavering commitment to customization. They tailor storage vessels precisely to meet the unique requirements of each client, offering tailored solutions. Renowned for on-time delivery, competitive pricing, and an unwavering focus on quality, Uma Pharmatech Machinery Company is Vadodara’s trusted choice for superior stainless steel storage vessels.
SS Storage Vessel Manufacturers in Ankleshwar
SS Storage Vessel Manufacturers in Ankleshwar play a vital role in providing safe and reliable material storage solutions, and Uma Pharmatech Machinery Company stands as a leading force in this sector. Based in Ankleshwar, Uma Pharmatech specializes in crafting top-quality stainless steel storage vessels, engineered to meet the most rigorous industry standards. These vessels are essential for secure material storage in pharmaceutical, chemical, and food processing applications.
What sets Uma Pharmatech apart is its unwavering commitment to customization. They tailor storage vessels precisely to meet the unique requirements of each client, offering bespoke solutions. Renowned for on-time delivery, competitive pricing, and an unwavering focus on quality, Uma Pharmatech Machinery Company is Ankleshwar’s preferred choice for superior stainless steel storage vessels.
SS Storage Vessel Manufacturers in Surat
SS Storage Vessel Manufacturers in Surat are pivotal in ensuring secure and efficient material storage, and Uma Pharmatech Machinery Company excels in this domain. Located in Surat, Uma Pharmatech specializes in crafting top-quality stainless steel storage vessels engineered to meet the most stringent industry standards. These vessels are essential for safe material storage in pharmaceutical, chemical, and food processing applications.
Uma Pharmatech’s distinguishing feature is its unwavering commitment to customization. They tailor storage vessels precisely to meet each client’s unique requirements, offering tailored solutions. Renowned for on-time delivery, competitive pricing, and an unwavering focus on quality, Uma Pharmatech Machinery Company is Surat’s trusted choice for superior stainless steel storage vessels.
SS Storage Vessel Manufacturers in Surat are vital for secure and efficient material storage solutions, and Uma Pharmatech Machinery Company is the foremost player in this arena. Located in Surat, Uma Pharmatech specializes in designing top-quality stainless steel storage vessels that adhere to rigorous industry standards. These vessels are essential for safe material storage in pharmaceutical, chemical, and food processing applications.
What truly sets Uma Pharmatech apart is its unwavering commitment to customization. They tailor storage vessels precisely to meet each client’s unique requirements, considering factors like design, cost, and material grade, be it SS304, SS316, or Mild Steel. Renowned for on-time delivery, competitive pricing, and an unwavering focus on quality, Uma Pharmatech Machinery Company is Surat’s trusted choice for superior stainless steel storage vessels.
SS Storage Vessel Manufacturers in Valsad
SS Storage Vessel Manufacturers in Valsad are paramount for efficient material storage, and Uma Pharmatech Machinery Company leads the charge in this sector. Situated in Valsad, Uma Pharmatech specializes in designing top-notch stainless steel storage vessels that adhere to stringent industry standards. These vessels play a pivotal role in pharmaceutical, chemical, and food processing applications.
Uma Pharmatech’s distinctive strength lies in its unwavering commitment to customization. They meticulously tailor storage vessels to meet each client’s unique requirements, considering aspects such as design, cost, and material grade, be it SS304, SS316, or Mild Steel. Renowned for on-time delivery, competitive pricing, and a steadfast focus on quality, Uma Pharmatech Machinery Company remains Valsad’s trusted choice for superior stainless steel storage vessels.
SS Storage Vessel Manufacturers in Vapi
SS Storage Vessel Manufacturers in Vapi are pivotal for efficient material storage solutions, and Uma Pharmatech Machinery Company excels in this domain. Located in Vapi, Uma Pharmatech specializes in designing top-quality stainless steel storage vessels that adhere to rigorous industry standards. These vessels are crucial for secure material storage in pharmaceutical, chemical, and food processing applications.
What truly sets Uma Pharmatech apart is its unwavering commitment to customization. They meticulously tailor storage vessels to meet each client’s unique requirements, considering factors like design, cost, and material grade, be it SS304, SS316, or Mild Steel. Renowned for on-time delivery, competitive pricing, and an unwavering focus on quality, Uma Pharmatech Machinery Company is Vapi’s trusted choice for superior stainless steel storage vessels.
SS Storage Vessel Manufacturers in Dahej
SS Storage Vessel Manufacturers in Dahej are indispensable for efficient and secure material storage solutions, and Uma Pharmatech Machinery Company leads the way in this sector. Situated in Dahej, Uma Pharmatech specializes in designing top-quality stainless steel storage vessels that strictly adhere to the most stringent industry standards. These vessels play a pivotal role in ensuring the safe storage of materials in pharmaceutical, chemical, and food processing applications.
Uma Pharmatech’s distinguishing feature is its unwavering commitment to customization. They meticulously tailor storage vessels to meet each client’s unique requirements, considering factors such as design, cost, and material grade, including SS304, SS316, and Mild Steel. Renowned for on-time delivery, competitive pricing, and an unwavering focus on quality, Uma Pharmatech Machinery Company remains Dahej’s trusted choice for superior stainless steel storage vessels.
Mixing Tank Manufacturers
SS Mixing Tank Manufacturers in Gujarat
SS Mixing Tank Manufacturers in Gujarat are instrumental in delivering efficient solutions for various industries. These tanks are essential for the precise blending of materials in pharmaceutical, chemical, and food processing applications. When it comes to choosing the right mixing tank, considerations like design, cost, and material grade are paramount. Stainless steel grades like SS304 and SS316, as well as Mild Steel, are commonly used, each offering its unique advantages.
For Gujarat-based industries seeking reliable SS mixing tank manufacturers, it’s crucial to choose a reputable company known for producing tanks that meet stringent industry standards. Such tanks ensure efficient mixing while guaranteeing durability and safety.
SS 316 Mixing Tank Manufacturers in Ahmedabad
SS 316 Mixing Tank Manufacturers in Ahmedabad provide critical solutions for industries requiring precision blending. These tanks, constructed from durable stainless steel, are vital for pharmaceutical, chemical, and food processing applications. When selecting a mixing tank, factors like design, cost, and material grade must be considered. Stainless steel grades like SS304 and SS316, along with Mild Steel, come into play, each offering its unique advantages.
In Ahmedabad, finding a reputable manufacturer is essential for ensuring the production of top-quality SS 316 mixing tanks that meet rigorous industry standards. These tanks not only guarantee efficient mixing but also ensure longevity and safety, making them a valuable asset for various industrial applications.
SS 304 Mixing Tank Manufacturers in Vadodara
SS 304 Mixing Tank Manufacturers in Vadodara offer critical solutions for industries requiring precision blending. These tanks, crafted from robust stainless steel, play a pivotal role in pharmaceutical, chemical, and food processing applications. When selecting a mixing tank, considerations like design, cost, and material grade must be taken into account. Stainless steel grades such as SS304 and SS316, as well as Mild Steel, offer distinct advantages.
In Vadodara, choosing a reputable manufacturer is essential to ensure the production of high-quality SS 304 mixing tanks that adhere to stringent industry standards. These tanks not only guarantee efficient mixing but also assure durability and safety, making them indispensable for a wide range of industrial applications.
Stainless Steel Mixing Tank Manufacturers in Rajkot
Stainless Steel Mixing Tank Manufacturers in Rajkot are indispensable for industries demanding precise blending solutions. These tanks, constructed from robust stainless steel, are pivotal for pharmaceutical, chemical, and food processing applications. When selecting a mixing tank, factors like design, cost, and material grade must be considered. Stainless steel grades like SS304 and SS316, along with Mild Steel, each offer unique advantages.
In Rajkot, choosing a reputable manufacturer is crucial to ensure the production of high-quality stainless steel mixing tanks that meet rigorous industry standards. These tanks not only ensure efficient mixing but also guarantee longevity and safety, making them a valuable asset for various industrial applications.
MS Mixing Tank Manufacturers in Surat
MS Mixing Tank Manufacturers in Surat play a pivotal role in industries requiring efficient blending solutions. These tanks, constructed from robust Mild Steel (MS), find applications in various industrial processes. When selecting a mixing tank, considerations like design, cost, and material grade are crucial. While stainless steel grades like SS304 and SS316 offer their advantages, Mild Steel remains a dependable choice.
In Surat, choosing a reputable manufacturer is vital to ensure the production of high-quality MS mixing tanks that meet stringent industry standards. These tanks not only ensure efficient mixing but also provide durability and reliability, making them a valuable asset across different industrial applications.
SS Mixing Tank Manufacturers in Vapi
SS Mixing Tank Manufacturers in Vapi are pivotal for industries demanding precise blending solutions. These tanks, constructed from robust stainless steel, are indispensable for pharmaceutical, chemical, and food processing applications. When selecting a mixing tank, factors like design, cost, and material grade must be considered. Stainless steel grades like SS304 and SS316, as well as Mild Steel, offer distinct advantages.
In Vapi, choosing a reputable manufacturer is essential to ensure the production of top-quality SS mixing tanks that adhere to stringent industry standards. These tanks not only guarantee efficient mixing but also assure longevity and safety, making them a valuable asset for various industrial applications.
SS Mixing Tank Manufacturers in Valsad
SS Mixing Tank Manufacturers in Valsad are indispensable for industries seeking precision blending solutions. These tanks, crafted from durable stainless steel, are crucial for pharmaceutical, chemical, and food processing applications. When selecting a mixing tank, considerations like design, cost, and material grade are pivotal. Stainless steel grades such as SS304 and SS316, along with Mild Steel, each offer unique advantages.
In Valsad, choosing a reputable manufacturer is essential to ensure the production of high-quality SS mixing tanks that adhere to stringent industry standards. These tanks not only ensure efficient mixing but also assure longevity and safety, making them an invaluable asset for a variety of industrial applications.
Stainless Steel Mixing Tank Manufacturers in Dahej
Stainless Steel Mixing Tank Manufacturers in Dahej are essential for industries demanding precision blending solutions. These tanks, crafted from durable stainless steel, are pivotal for pharmaceutical, chemical, and food processing applications. When selecting a mixing tank, factors like design, cost, and material grade must be considered. Stainless steel grades like SS304 and SS316, as well as Mild Steel, offer unique advantages.
In Dahej, choosing a reputable manufacturer is crucial to ensure the production of high-quality stainless steel mixing tanks that meet stringent industry standards. These tanks not only ensure efficient mixing but also provide durability and safety, making them an invaluable asset across various industrial applications.
Mild Steel Mixing Tank Fabricator in Ankleshwar
Mild Steel Mixing Tank Fabricator in Ankleshwar plays a crucial role in industries requiring robust blending solutions. These tanks, expertly crafted from durable Mild Steel (MS), find applications in various industrial processes. When considering a mixing tank, elements like design, cost, and material grade are essential. While stainless steel grades like SS304 and SS316 have their advantages, Mild Steel remains a reliable choice.
In Ankleshwar, choosing a reputable fabricator is vital to ensure the production of top-quality Mild Steel mixing tanks that meet stringent industry standards. These tanks not only guarantee efficient mixing but also offer durability and cost-effectiveness, making them a valuable asset across different industrial applications.
SS Mixing Tank Suppliers in Bharuch
SS Mixing Tank Suppliers in Bharuch are instrumental in providing industries with high-quality blending solutions. These tanks, constructed from durable stainless steel, play a vital role in pharmaceutical, chemical, and food processing applications. When choosing a mixing tank, considerations such as design, cost, and material grade are paramount. Stainless steel grades like SS304 and SS316, along with Mild Steel, each offer distinct advantages.
In Bharuch, selecting a reputable supplier is essential to ensure the procurement of top-notch SS mixing tanks that adhere to rigorous industry standards. These tanks not only ensure efficient mixing but also assure longevity and safety, making them an invaluable asset for a variety of industrial applications.
Storage Tank Manufacturers
SS Storage Tank Manufacturers in Gujarat
SS Storage Tank Manufacturers in Gujarat cater to diverse industrial needs, providing top-notch solutions. Stainless steel storage tanks, crucial for various applications, are engineered to the highest standards. When seeking quality SS storage tanks in Gujarat, these manufacturers offer reliability, durability, and efficiency, making them indispensable for industries across the region.
SS Storage Tank Manufacturers in Ahmedabad
SS Storage Tank Manufacturers in Ahmedabad lead the industry with their high-quality stainless steel storage tanks. When searching for reliable SS storage tanks in Ahmedabad, these manufacturers offer durability, safety, and efficiency. They are the go-to choice for various industries, providing top-notch storage solutions in the region.
SS Storage Tank Manufacturers in Vadodara
SS Storage Tank Manufacturers in Vadodara excel in crafting top-quality stainless steel storage tanks. When it comes to reliable SS storage tanks in Vadodara, these manufacturers ensure durability, safety, and efficiency. They are the preferred choice for various industries in the region, offering top-notch storage solutions.
SS Storage Tank Manufacturers in Surat
SS Storage Tank Manufacturers in Surat are industry leaders, providing premium stainless steel storage tanks. When seeking dependable SS storage tanks in Surat, these manufacturers ensure durability, safety, and efficiency. They are the trusted choice for various industries in the region, offering top-notch storage solutions.
SS Storage Tank Manufacturers in Rajkot
SS Storage Tank Manufacturers in Rajkot stand out in crafting high-quality stainless steel storage tanks. When in search of dependable SS storage tanks in Rajkot, these manufacturers prioritize durability, safety, and efficiency. They are the preferred choice for various industries in the region, offering top-notch storage solutions.
SS Storage Tank Manufacturers in Valsad
SS Storage Tank Manufacturers in Valsad excel in producing premium stainless steel storage tanks. When seeking reliable SS storage tanks in Valsad, these manufacturers prioritize durability, safety, and efficiency. They are the trusted choice for various industries in the region, offering top-notch storage solutions.
SS Storage Tank Manufacturers in Vapi
SS Storage Tank Manufacturers in Vapi are known for their top-quality stainless steel storage tanks. When you need dependable SS storage tanks in Vapi, these manufacturers ensure durability, safety, and efficiency. They are the preferred choice for various industries in the region, providing excellent storage solutions.
SS Storage Tank Manufacturers in Ankleshwar
SS Storage Tank Manufacturers in Ankleshwar are renowned for their premium stainless steel storage tanks. When seeking reliable SS storage tanks in Ankleshwar, these manufacturers prioritize durability, safety, and efficiency. They are the preferred choice for various industries in the region, offering top-notch storage solutions.
SS Storage Tank Manufacturers in Bharuch
SS Storage Tank Manufacturers in Bharuch are known for their exceptional stainless steel storage tanks. When in need of reliable SS storage tanks in Bharuch, these manufacturers prioritize durability, safety, and efficiency. They are the trusted choice for various industries in the region, offering top-tier storage solutions.
Suppliers of Vessel and Tank
SS Vessel Suppliers
SS Vessel Suppliers play a vital role in providing industries with high-quality stainless steel vessels. When searching for dependable SS vessel suppliers, these professionals offer durability, safety, and efficiency. They are the preferred choice for various industries, providing top-notch stainless steel vessels.
Stainless Steel Vessel Suppliers
Stainless Steel Vessel Suppliers are essential for industries seeking top-quality stainless steel vessels. When in need of dependable stainless steel vessel suppliers, these experts prioritize durability, safety, and efficiency. They are the go-to choice for various industries, offering premium stainless steel vessels that meet rigorous standards.
Suppliers of Mixing Vessel
Suppliers of Mixing Vessel are crucial for industries requiring top-notch mixing vessels. When searching for dependable mixing vessel suppliers, these professionals prioritize design, cost, and material grade. They are the preferred choice for various industries, providing high-quality mixing vessels that meet rigorous standards.
Suppliers of Storage Tank
Suppliers of Storage Tank are essential for industries in need of high-quality storage solutions. When seeking reliable storage tank suppliers, these experts prioritize durability, safety, and efficiency. They are the preferred choice for various industries, offering top-notch storage tanks that meet rigorous standards.
Suppliers of Storage Vessel
Suppliers of Storage Vessel are pivotal for industries seeking top-quality storage solutions. When in need of dependable storage vessel suppliers, these experts prioritize durability, safety, and efficiency. They are the go-to choice for various industries, offering high-quality storage vessels that meet rigorous standards.
Suppliers of Mixing Tank
Suppliers of Mixing Tank are essential for industries requiring efficient blending solutions. When searching for dependable mixing tank suppliers, these professionals prioritize design, cost, and material grade. They are the preferred choice for various industries, providing high-quality mixing tanks that meet rigorous standards.
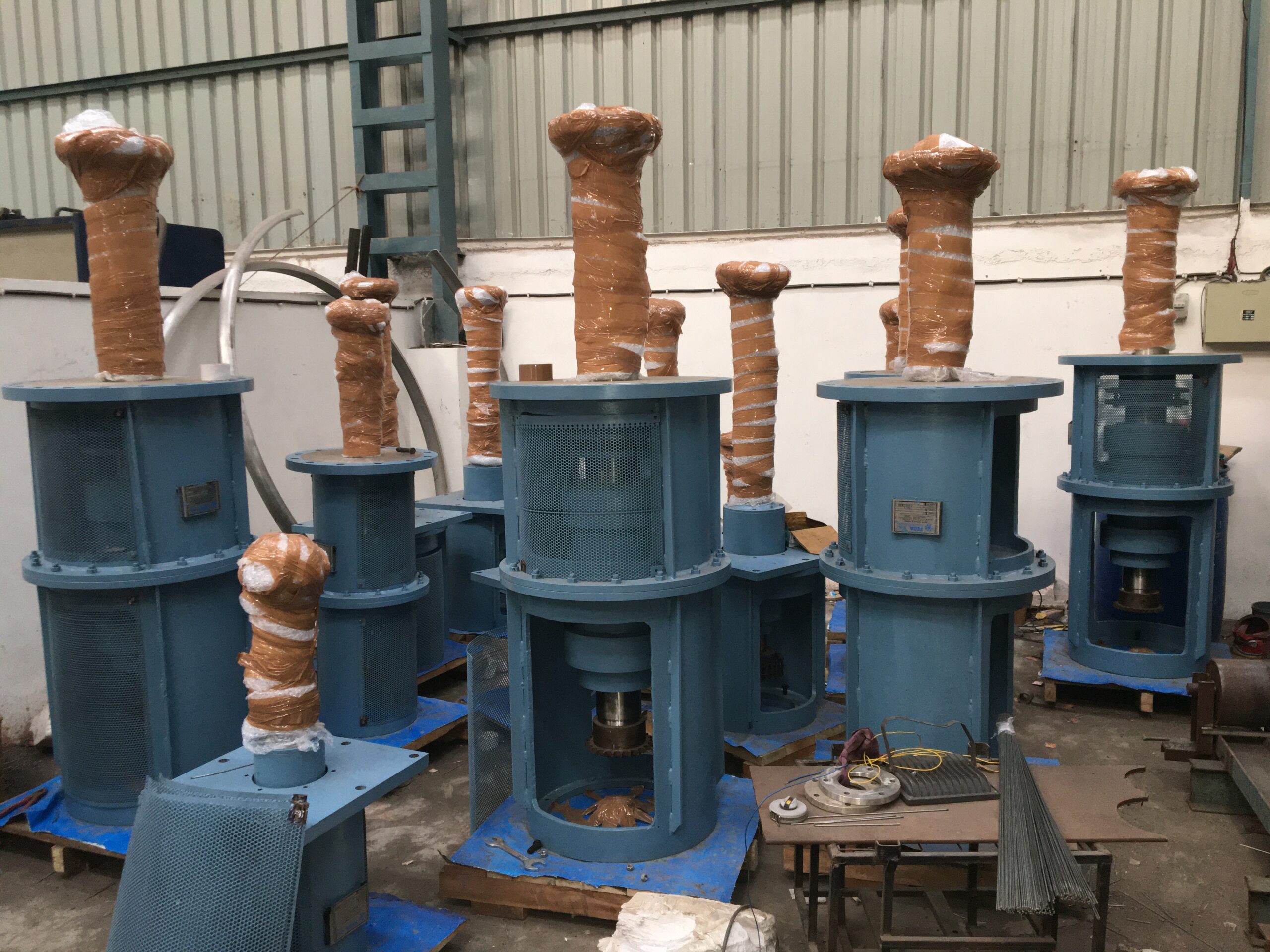
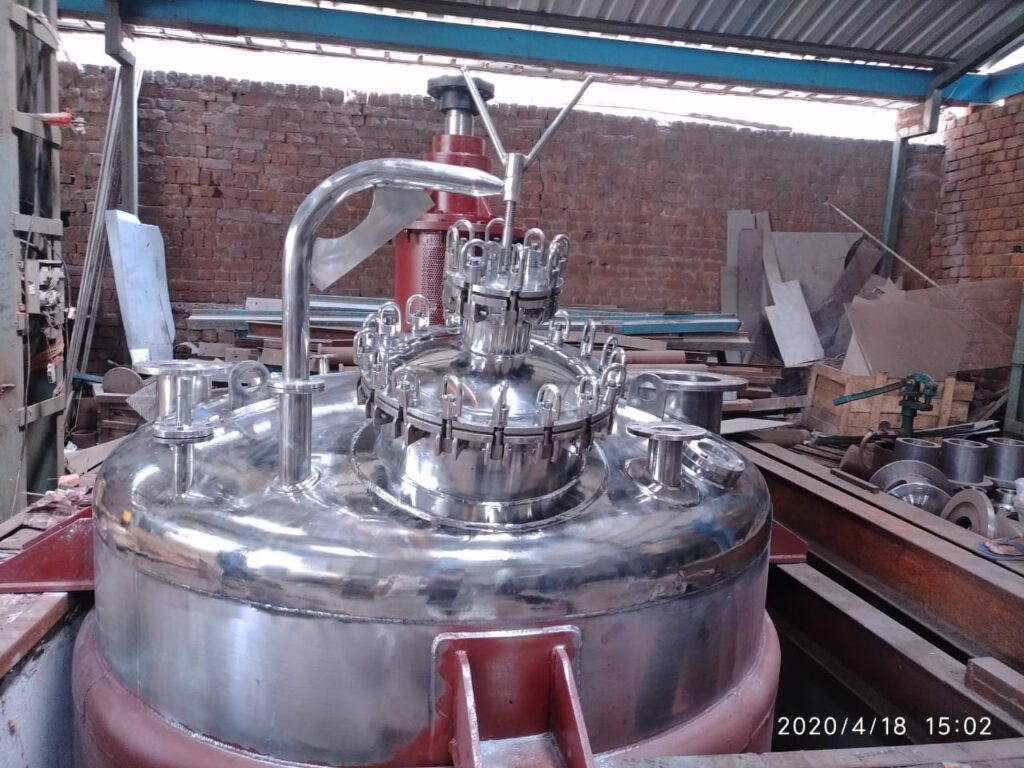
Uma Pharmatech Machinery Deal In Manufacturing Of Reactor, Manufacturing Of Vessel and Agitator. We Manufacture SS Limpet Coil Reactor Vessel For Pharmaceutical and Chemical. We Supply Industrial Agitator For SS Mixing Tank. UPM Also Offer SS Storage Tank and SS Storage Vessel In Gujarat. We Supply Process Reactor and Chemical Reactor Vessel For Pigment and Paints. Uma Pharmatech Machinery Is Leading Manufacturing In SS Jacketed Reactor and Vessel Supplier In Gujarat. UPM Supply Our Reactor Vessel in Ahmedabad, Vadodra, Surat, Ankleswar, Panoli, Dahej, Rajkot, Navsari, chattral, Vapi and Jaghdiya.