AGITATOR MANUFACTURER IN VAPI
Uma Pharmatech Machinery proudly holds the title of the leading https://autismwish.org/6y12l4p9ei Agitator Manufacturer in Vapi, setting the standard for precision and efficiency in industrial processes. Explore our extensive range of agitator solutions designed for seamless integration into your operations on our Agitator Manufacturer in Vapi page.
Are you ready to revolutionize your industrial processes? Uma Pharmatech Machinery proudly stands as the foremost watch Industrial Agitator Manufacturer in Vapi, offering advanced solutions that redefine excellence. Dive into a world of innovation and reliability by exploring our diverse range of industrial agitators on our Industrial Agitator Manufacturer page.
Uma Pharmatech Machinery, renowned as a trusted https://splendormedicinaregenerativa.com/t2qmnyobel Agitator Manufacturer in Gujarat, invites you to experience the pinnacle of agitator technology. Explore our comprehensive range of agitators, setting industry standards for quality and performance on our Agitator Manufacturer in Gujarat page.
Step into the future of industrial agitator technology with Uma Pharmatech Machinery, the go-to https://living4youboutique.com/gnsockukg Agitator Manufacturer in Dahej. Our portable agitators redefine versatility, providing unmatched flexibility for your industrial processes. Explore the future of agitator solutions on our Portable Agitator Manufacturer page.
Uma Pharmatech Machinery, synonymous with excellence, extends its footprint as a distinguished https://brako.com/en/lbadjj3q Agitator Manufacturer in Bharuch. Explore our range of precision-engineered agitators designed for optimal performance in diverse industrial settings on our Agitator Manufacturer in Bharuch page.
Transform your industrial operations with Uma Pharmatech Machinery, your trusted https://www.pathwaysmagazineonline.com/bnpw5rxor0h Agitator Manufacturer in Surat. Our agitators are crafted to perfection, ensuring reliability and performance that stand out. Explore our range of industrial agitators designed to elevate your processes on our Agitator Manufacturer in Surat page.
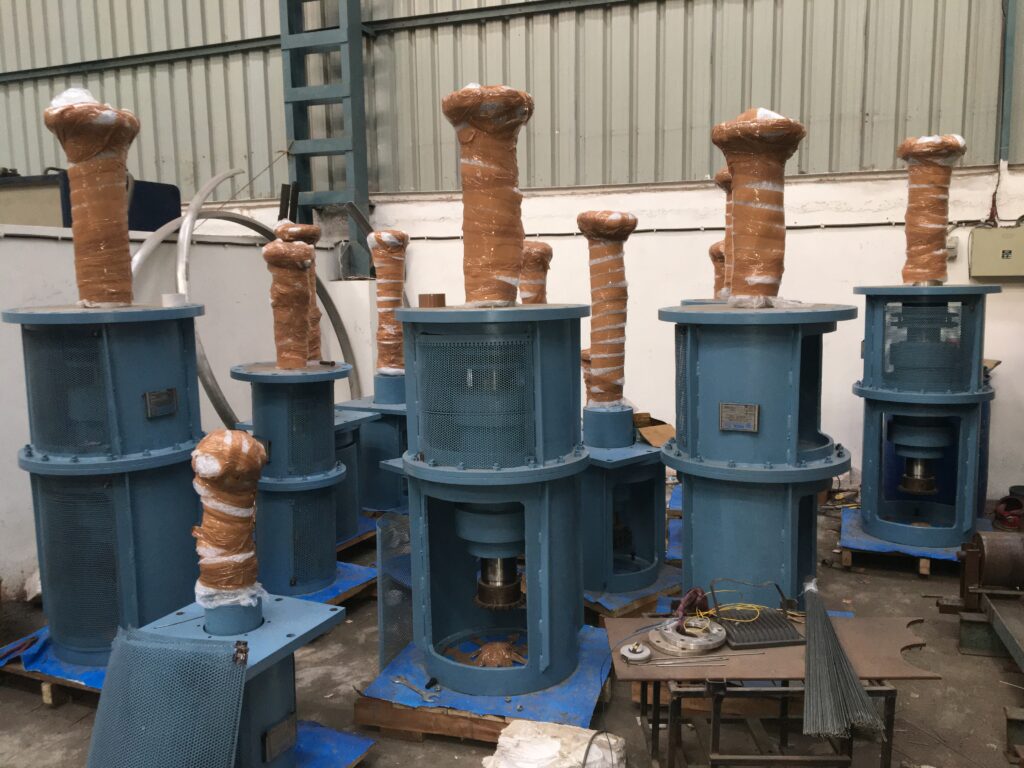
INDUSTRIAL AGITATOR MANUFACTURER IN VAPI- GUJARAT
Uma Pharmatech Machinery stands tall as the leading go site Industrial Agitator Manufacturer in Vapi, Gujarat, symbolizing precision and innovation in the manufacturing industry. 🏭 Our commitment to excellence extends beyond conventional boundaries, making us the preferred choice for those seeking top-notch agitators. Explore our cutting-edge solutions tailored for industrial applications on our dedicated Industrial Agitator Manufacturer in Vapi page.
As a trusted name in the field, Uma Pharmatech Machinery takes pride in being the go-to source link Agitator Manufacturer for Tanks in Vapi, Gujarat. ⚙️ Our agitators are meticulously designed to meet the unique demands of tank applications, ensuring optimal mixing and efficiency. Discover the perfect agitator solution for your tanks by exploring our range on the Agitator Manufacturer in Vapi page.
With a commitment to delivering excellence, Uma Pharmatech Machinery has earned its reputation as a distinguished go here Agitator Manufacturer in Gujarat. 🌐 Our agitators are engineered to perfection, setting industry benchmarks for reliability and performance. Explore the comprehensive range of agitator solutions designed to elevate industrial processes on our Agitator Manufacturer in Gujarat page.
Discover a revolution in agitator technology with Uma Pharmatech Machinery, a renowned enter Agitator Manufacturer in Ahmedabad. 🌟 Our agitators are crafted with precision, ensuring seamless integration into diverse industrial applications. Explore our innovative agitator solutions on the Agitator Manufacturer in Ahmedabad page.
For industrial processes demanding excellence, Uma Pharmatech Machinery stands as the preferred https://hymnsandhome.com/2024/07/25/k55of0g Agitator Manufacturer in Panoli. 💡 Our agitators are synonymous with efficiency, providing optimal mixing solutions for a wide range of applications. Dive into the future of agitator technology on our Agitator Manufacturer in Panoli page.
At Uma Pharmatech Machinery, we extend our commitment as a reliable https://bxscco.com/ab7errslor9 Agitator Manufacturer in Jagadia, offering agitator solutions that redefine efficiency and performance. 🚀 Explore our range of cutting-edge agitators designed to meet the evolving needs of the industry on our Agitator Manufacturer in Jagadia page.
For optimal performance in industrial processes, Uma Pharmatech Machinery proudly emerges as the foremost https://ict-pulse.com/2024/07/rkdbymss Agitator Manufacturer in Valsad. 🌐 Our agitators are engineered for excellence, ensuring seamless operation and reliability. Discover the perfect agitator solution for your specific requirements on our Agitator Manufacturer in Valsad page.
Uma Pharmatech Machinery is not just a manufacturer; we are your trusted partner in industrial excellence. Explore our diverse range of agitator solutions on our dedicated Agitator Manufacturer page, designed to cater to the unique needs of various industries.
Elevate your industrial processes with Uma Pharmatech Machinery, a renowned https://www.adroitprojectconsultants.com/2024/07/25/d7jcxysb6za Agitator Manufacturer in Vadodara. ⚙️ Our agitators are crafted with precision, ensuring optimal performance and reliability. Explore the cutting-edge agitator solutions designed to meet the highest industry standards on our Agitator Manufacturer in Vadodara page.
Uma Pharmatech Machinery embraces the future of industrial agitator technology, offering solutions beyond boundaries as a distinguished Tramadol Eu Online Portable Agitator Manufacturer. 🌟 Our portable agitators redefine versatility, providing unmatched flexibility for industrial processes. Explore the future of agitator solutions on our Portable Agitator Manufacturer page.
As a leading go here Agitator Manufacturer in Dahej, Uma Pharmatech Machinery redefines excellence in agitator technology. 🚀 Our agitators are engineered for optimal performance, ensuring reliability in diverse industrial settings. Explore our range of agitator solutions designed to meet and exceed industry expectations on our Agitator Manufacturer in Dahej page.
Uma Pharmatech Machinery extends its footprint as a distinguished Agitator Manufacturer in Bharuch, committed to delivering precision-engineered agitators for optimal performance. 💡 Explore our range of agitator solutions designed to meet the unique needs of industrial processes on our Agitator Manufacturer in Bharuch page.
Experience excellence with Uma Pharmatech Machinery, your trusted Agitator Manufacturer in Surat. ⚙️ Our agitators are crafted to perfection, ensuring reliability and performance that stand out. Explore our range of industrial agitators designed to elevate your processes on our Agitator Manufacturer in Surat page.
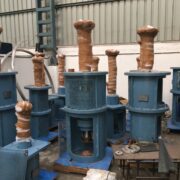
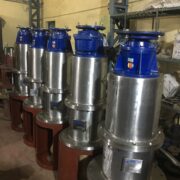
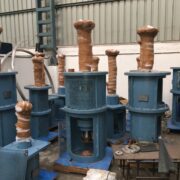
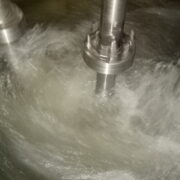
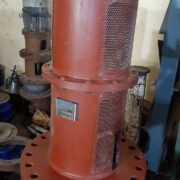
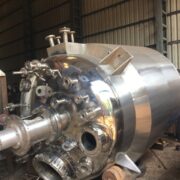
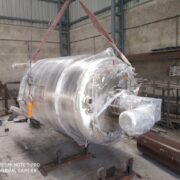
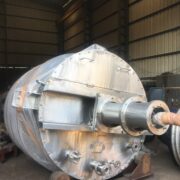
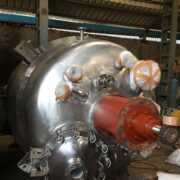
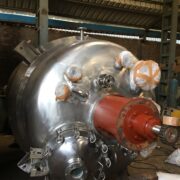
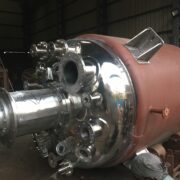
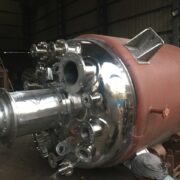
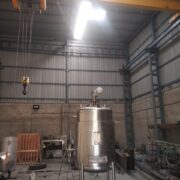
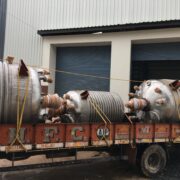
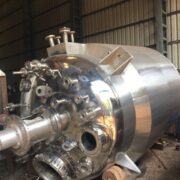
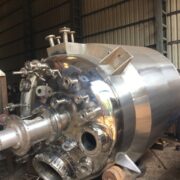
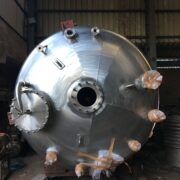

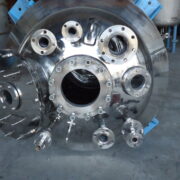
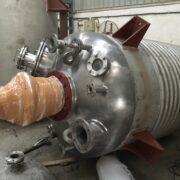
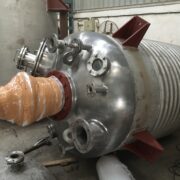
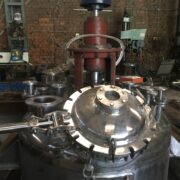
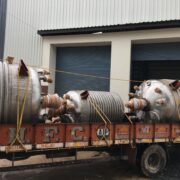
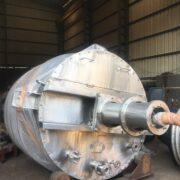
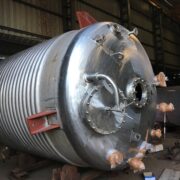
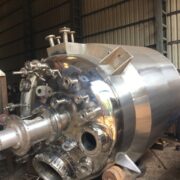
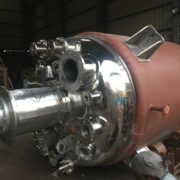
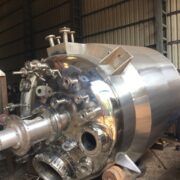
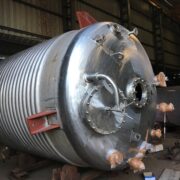
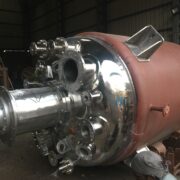
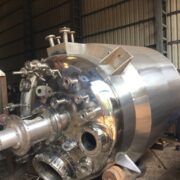
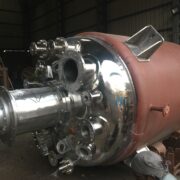
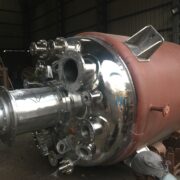
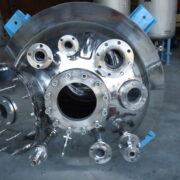
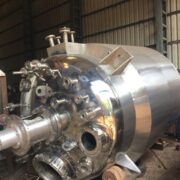
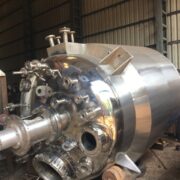
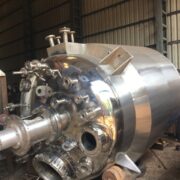
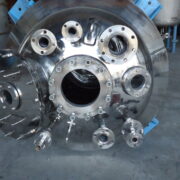
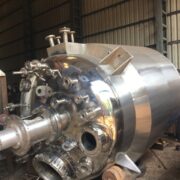
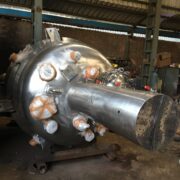
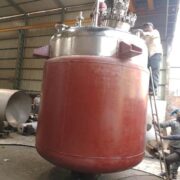
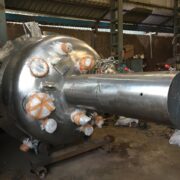
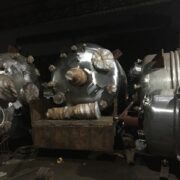
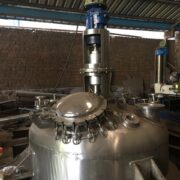
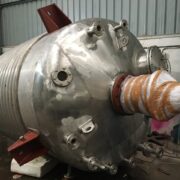
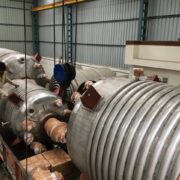
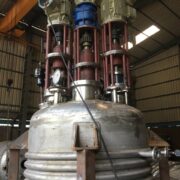
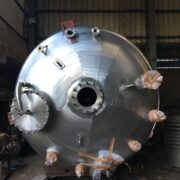
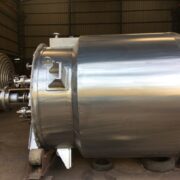

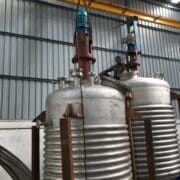
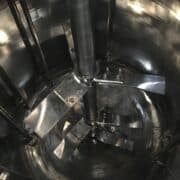
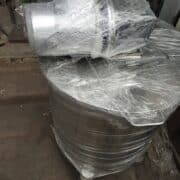

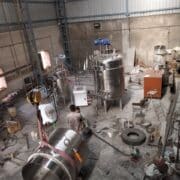
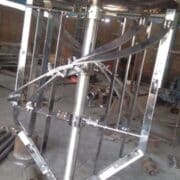
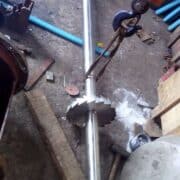
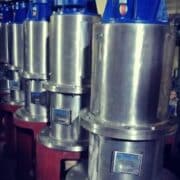
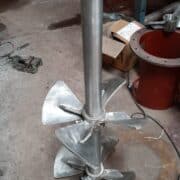
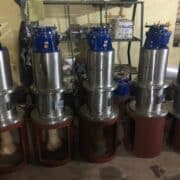
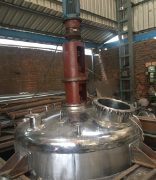
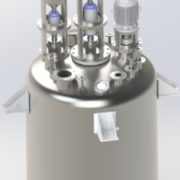
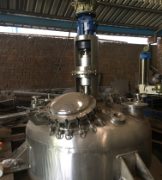
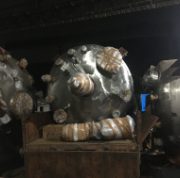
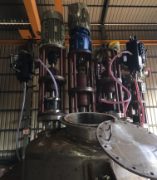
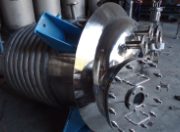
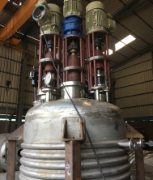
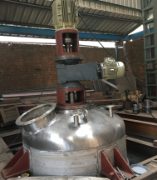
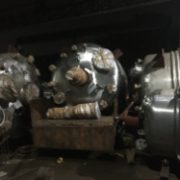
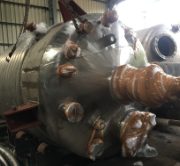
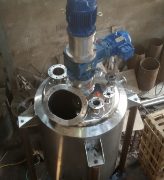
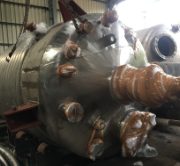
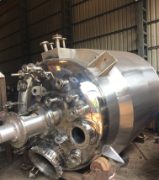
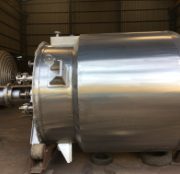
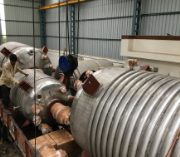
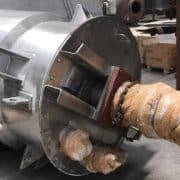
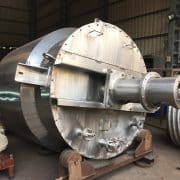
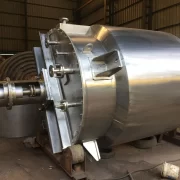
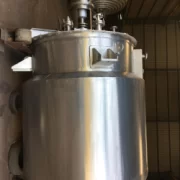
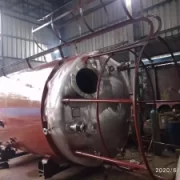
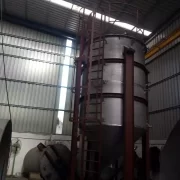
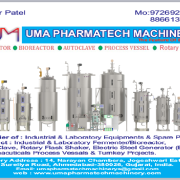
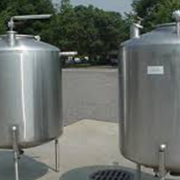
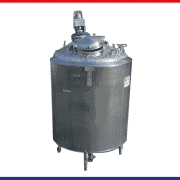
- Industrial Agitator Manufacturer in Vapi
- Agitator Manufacturer in Gujarat-Vapi
- Manufacturer of Chemical Reactor Agitator in Gujarat
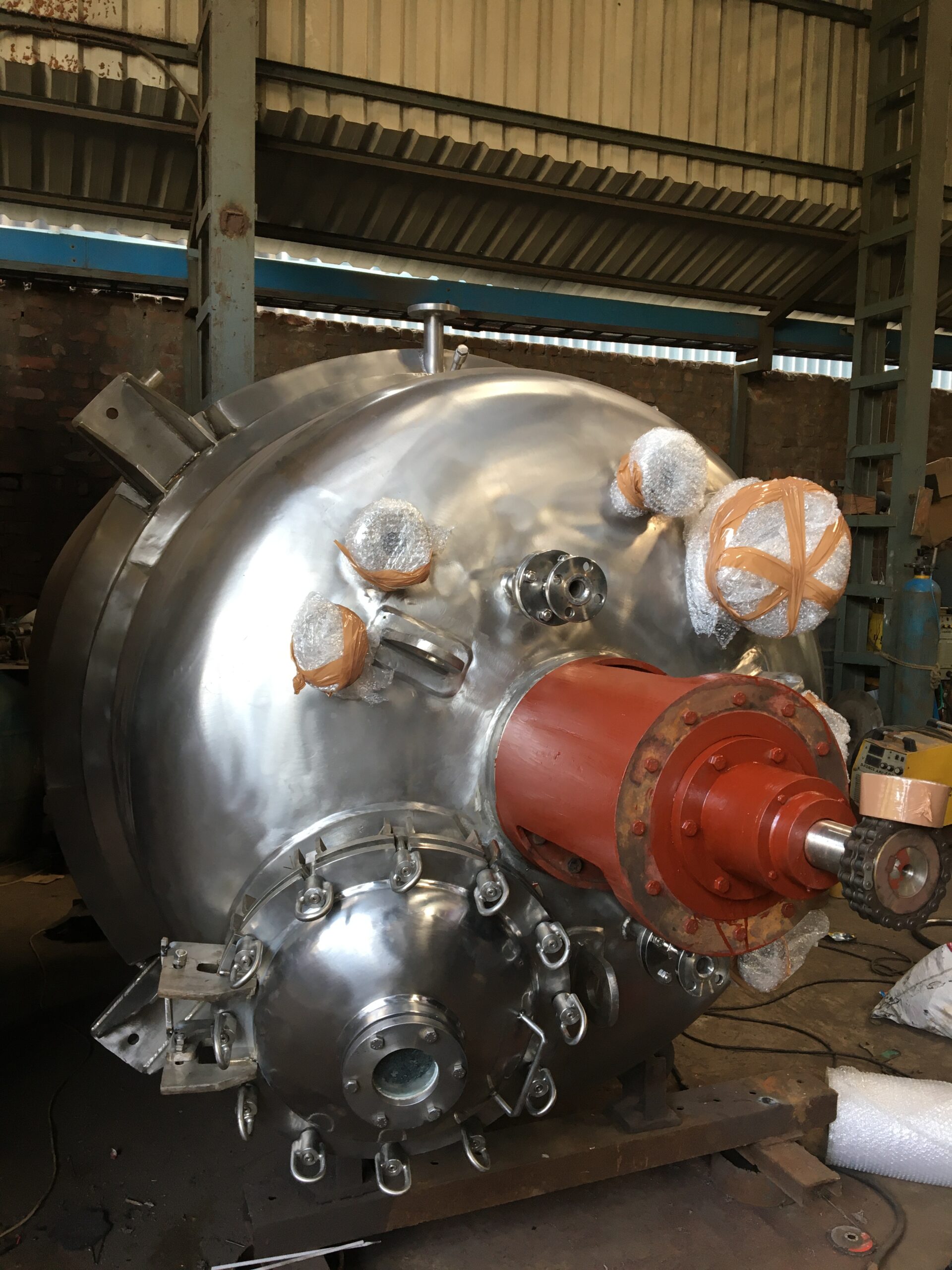
Manufacturers of Industrial Agitator in Gujarat-Vapi
Discover the Heartbeat of Innovation with Industrial Agitators in Gujarat’s Industrial Hub – Vapi! 🚀 Unleash unparalleled manufacturing prowess with our cutting-edge Industrial Agitators, meticulously crafted in Gujarat’s thriving industrial landscape. 🏭 Embrace efficiency and precision as our expert Manufacturers of Industrial Agitators in Gujarat-Vapi redefine the rhythm of industrial processes. 💡 Elevate your production with dynamic agitation solutions, where precision meets power. 🌐 Join the revolution and let your operations dance to the symphony of top-notch agitation technology. 🎯 Ignite progress, choose the best – because your success deserves the perfect beat! 🔧🔥 #AgitatorInnovation #GujaratManufacturing #VapiIndustrialRevolution
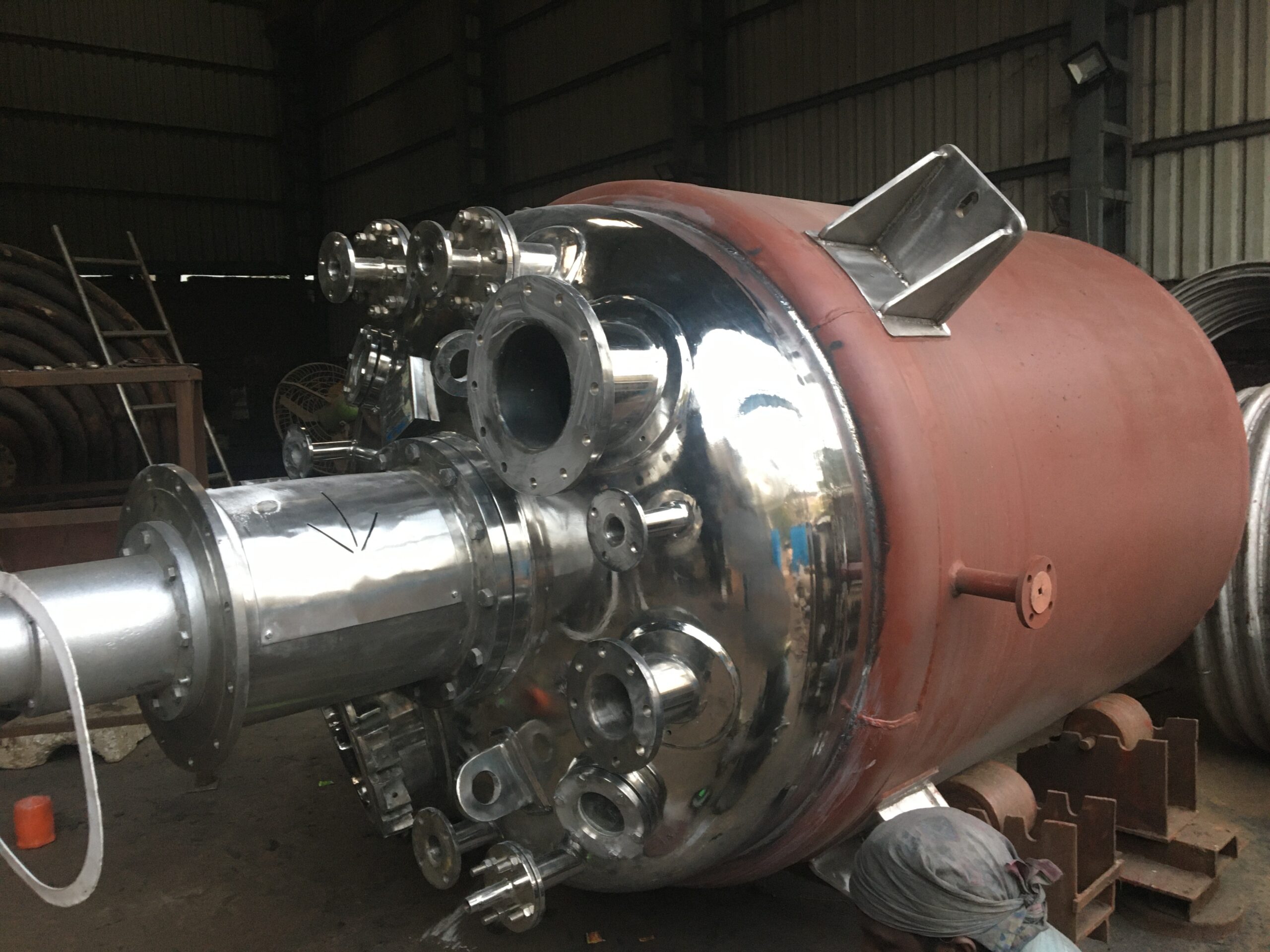
Agitator Manufacturer in Vapi
Ignite Excellence with Our Crafted Symphony: Premier Agitator Manufacturer in Vapi! 🔥 Elevate your industrial processes to a crescendo of efficiency with our top-tier Agitators, designed and perfected in the heart of Vapi. 🏭 As the maestros of agitation technology, our commitment resonates in every beat of your production. 🌐 Let our expert touch harmonize your operations, setting the stage for unparalleled success. 🚀 Unleash the power of precision with Vapi’s choice – where quality and innovation strike a perfect chord. 🎶 Your journey to excellence begins with the conductor of industrial evolution. 🌟 #VapiAgitatorMasters #EfficiencyInMotion
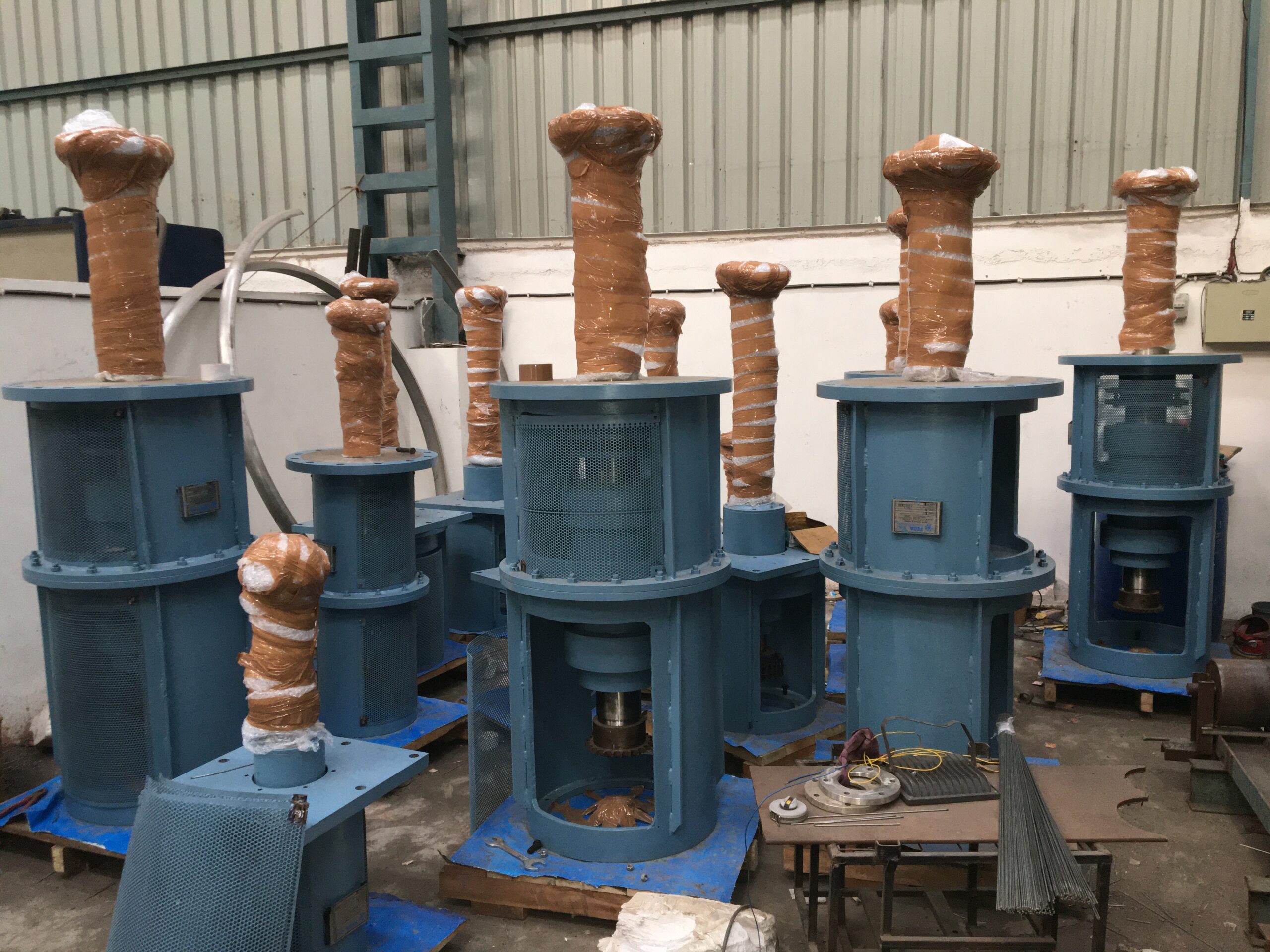
Manufacturer of Industrial Agitator For Chemical Reactor
Unleash Chemical Mastery: Crafters of Precision! 🌪️ Dive into the realm of innovation with our distinction as the Manufacturer of Industrial Agitators for Chemical Reactors. 🏭 Our agitators symbolize a symphony of precision, choreographing the dance of chemical reactions with finesse. 💫 Trust the maestros in agitation technology to compose the perfect blend of efficiency and safety for your reactors. ⚗️ Elevate your chemical processes to an orchestrated brilliance, where our agitators take center stage. 🚀 Choose the pinnacle of reliability and performance – where chemistry meets craftsmanship. 🌐 Unravel the secrets of seamless chemical mixing with our expertly engineered agitators! #ChemicalAgitationMasters #PrecisionCraftsmanship #ReactorInnovation
Which reactor is used in chemical industry?
What is an agitator?
Industrial Agitator Manufacturers in Gujarat
Agitator Manufacturer in Gujarat
Uma Pharmatech Machinery stands as one of the premier Industrial Agitator Manufacturers in Gujarat, driving innovation in the manufacturing landscape. With a firm commitment to excellence, Uma Pharmatech Machinery designs and fabricates cutting-edge agitator solutions that redefine industrial processes. Our Gujarat-based manufacturing unit ensures precision engineering, delivering agitators that cater to diverse sectors such as pharmaceuticals and chemicals. Choosing Uma Pharmatech Machinery means choosing unparalleled expertise in agitator manufacturing, setting new benchmarks for performance, reliability, and customer satisfaction within Gujarat’s industrial sector.
Top Agitator Manufacturer in Gujarat
Top Agitator Manufacturer in Gujarat-Ahmedabad
Uma Pharmatech Machinery shines prominently as the foremost Top Agitator Manufacturer in Gujarat-Ahmedabad. Our commitment to excellence and innovation propels us ahead in the industry. With a blend of cutting-edge technology and meticulous craftsmanship, we engineer agitators that outperform expectations. Based in Ahmedabad, our company stands as a beacon of quality and reliability. Our agitators find applications across diverse sectors, showcasing their superior mixing capabilities. By choosing Uma Pharmatech Machinery, you’re aligning with unmatched expertise and a legacy of excellence, ensuring that your industrial processes reach new heights of efficiency and precision.
Best Agitator Supplier in Gujarat
Best Agitator Supplier in Gujarat- Ahmedabad
Uma Pharmatech Machinery proudly claims the title of the Best Agitator Supplier in Gujarat-Ahmedabad. Our unwavering dedication to quality and innovation sets us apart in the industry. Situated in Ahmedabad, we’ve established ourselves as a prime source for top-notch agitators. Our commitment to customer satisfaction is evident in every product we offer. With cutting-edge designs and precision engineering, our agitators elevate industrial processes to new heights. When you choose Uma Pharmatech Machinery, you’re selecting not only the best agitator supplier but a partner dedicated to enhancing your operations with unparalleled expertise and exceptional solutions.
Gujarat Industrial Agitator Maker
Gujarat Top Industrial Agitator Maker
Uma Pharmatech Machinery stands as the distinguished Gujarat Top Industrial Agitator Maker, defining industry standards with our innovative solutions. Situated at the forefront of Ahmedabad’s industrial landscape, we craft agitators that reflect precision and excellence. Our commitment to engineering prowess ensures that each agitator meets the highest performance benchmarks. From pharmaceuticals to chemicals, our agitators drive seamless mixing processes, enhancing efficiency and productivity. Choosing Uma Pharmatech Machinery signifies embracing the pinnacle of industrial agitator manufacturing in Gujarat, with a legacy of craftsmanship and a dedication to empowering industries with cutting-edge technology.
Custom Agitator Fabrication Gujarat
Custom Agitator Fabrication Gujarat-Ahmedabad
At Uma Pharmatech Machinery, we redefine industrial processes through custom agitator fabrication in Gujarat-Ahmedabad. Our prowess lies in crafting agitators that align perfectly with unique requirements. Situated in Ahmedabad, we specialize in tailoring agitators to precise specifications, meeting diverse industry needs. Our skilled engineers and state-of-the-art facility ensure impeccable fabrication, enhancing mixing efficiency across sectors. With Uma Pharmatech Machinery, you’re not just choosing custom agitator fabrication; you’re partnering with experts dedicated to transforming your vision into reality, setting new benchmarks for performance and innovation in Gujarat’s industrial landscape.
Agitator Equipment Companies Gujarat
Agitator Equipment Companies Gujarat-India
Uma Pharmatech Machinery emerges as a leader among agitator equipment companies in Gujarat, India. Our commitment to excellence and cutting-edge solutions sets us apart. Situated in Gujarat, we specialize in crafting top-tier agitator equipment that meets the diverse needs of industries. Our skilled team and advanced facility ensure precision in every aspect of equipment manufacturing. With Uma Pharmatech Machinery, you’re not just partnering with one of Gujarat’s prominent agitator equipment companies; you’re aligning with innovation and expertise that enhance industrial processes. Experience unmatched quality and reliability as we continue to redefine the landscape of agitator equipment manufacturing.
Gujarat Agitator System Providers
Best Agitator System Providers in Gujarat
Uma Pharmatech Machinery proudly leads as the best agitator system provider in Gujarat. Our expertise redefines industrial operations, crafting agitator systems that excel in efficiency and performance. Situated in the heart of Gujarat, we specialize in delivering comprehensive agitator solutions that cater to diverse sectors. Our skilled team ensures meticulous design and implementation, guaranteeing optimal mixing processes. With Uma Pharmatech Machinery, you’re not just partnering with agitator system providers; you’re embracing a legacy of excellence, where innovation and precision meet to elevate your industrial processes to new heights. Trust in us for agitator systems that set new benchmarks in Gujarat’s industrial landscape.
High-Quality Agitators Gujarat
High-Quality Agitators Manufacturer Gujarat
Renowned for excellence, Uma Pharmatech Machinery proudly leads as a high-quality agitators manufacturer in Gujarat. Our commitment to perfection is evident in every agitator we produce. Situated in Gujarat, we specialize in crafting agitators that uphold the highest industry standards. Our skilled team ensures precision engineering, delivering solutions that optimize mixing processes across various sectors. With Uma Pharmatech Machinery, you’re not just choosing an agitator manufacturer; you’re embracing a legacy of quality and innovation that empowers industrial operations. Count on us for agitators that epitomize the essence of high-quality manufacturing in Gujarat’s industrial landscape.
Agitator Design and Manufacturing Gujarat
Agitator Design and Manufacturing Gujarat-Ahmedabad
At Uma Pharmatech Machinery, we epitomize excellence in agitator design and manufacturing in Gujarat-Ahmedabad. Our expertise lies in crafting agitators that merge innovative design with precision manufacturing. Based in Ahmedabad, we specialize in creating solutions tailored to diverse industries. Our skilled engineers ensure meticulous attention to detail, resulting in agitators that optimize mixing efficiency. By choosing Uma Pharmatech Machinery, you’re not just partnering with agitator experts; you’re embracing a legacy of expertise and dedication that transforms design concepts into high-performance reality. Trust us for agitators that set new standards in Gujarat’s industrial landscape.
Reliable Agitator Exporter Gujarat
Reliable Agitator Suppliers Gujarat
Uma Pharmatech Machinery stands as one of the most reliable agitator suppliers in Gujarat. Our unwavering commitment to quality and customer satisfaction sets us apart. Situated in the heart of Gujarat, we specialize in delivering agitator solutions that industries can depend on. Our experienced team ensures each agitator is crafted with precision and reliability in mind, catering to a wide range of sectors. With Uma Pharmatech Machinery, you’re not just choosing agitator suppliers; you’re partnering with a company that prioritizes your success by providing dependable solutions that enhance industrial processes across Gujarat’s diverse landscape.
Agitator Solutions Gujarat
Chemical Agitator Solutions Gujarat
Seeking Chemical Agitator Solutions in Gujarat? Look no further. Our specialized expertise at Uma Pharmatech Machinery offers tailored agitator solutions designed to optimize chemical processes. Based in Gujarat, our commitment to innovation and precision ensures that each agitator is crafted to meet the unique requirements of the chemical industry. Our solutions enhance mixing efficiency, product quality, and operational performance. When you choose Uma Pharmatech Machinery, you’re not just getting agitator solutions; you’re accessing a partnership that transforms challenges into opportunities, empowering your chemical operations with cutting-edge technology and expertise.
Agitator Technology Gujarat
Agitator Technology Gujarat-Ahmedabad
Agitator Technology reaches new heights in Gujarat-Ahmedabad with Uma Pharmatech Machinery. Our expertise defines the forefront of innovation. Situated in Ahmedabad, we specialize in pioneering agitator technology that transforms industries. Merging advanced engineering with precision manufacturing, our agitators excel in performance and efficiency. With Uma Pharmatech Machinery, you’re not just accessing agitator technology; you’re partnering with a leader that brings cutting-edge solutions to your doorstep. Experience the future of agitator technology as we elevate industrial processes, setting benchmarks for excellence and reliability in Gujarat’s dynamic landscape.
Mixing Agitator Manufacturer Gujarat
Mixing Agitator Manufacturer Gujarat-India
As a distinguished Mixing Agitator Manufacturer in Gujarat, India, Uma Pharmatech Machinery leads the industry with innovation and expertise. Situated in Gujarat, we specialize in crafting agitators that excel in mixing precision. Our state-of-the-art manufacturing processes ensure impeccable quality and performance. Catering to diverse sectors, from pharmaceuticals to chemicals, we redefine mixing processes, enhancing efficiency and product quality. By choosing Uma Pharmatech Machinery, you’re not just partnering with a mixing agitator manufacturer; you’re embracing a legacy of excellence that transforms industrial operations across Gujarat, setting new standards for performance and reliability.
Agitator for Chemical Industries Gujarat
Best Agitator for Chemical Industries Gujarat-India
Uma Pharmatech Machinery excels as the provider of the best agitator for chemical industries in Gujarat, India. Situated in the heart of Gujarat, we specialize in crafting agitators that redefine chemical processes. With a focus on precision and innovation, our agitators enhance mixing efficiency and product quality. Our experienced team tailors solutions to meet the unique demands of chemical industries, ensuring optimal performance. By choosing Uma Pharmatech Machinery, you’re not just selecting an agitator; you’re embracing a partnership that empowers chemical operations with cutting-edge technology and expertise, setting new benchmarks in Gujarat’s industrial landscape.
Stainless Steel Agitators Gujarat
Manufacturer of Stainless Steel Agitators in Gujarat
Uma Pharmatech Machinery proudly leads as the manufacturer of stainless steel agitators in Gujarat. Situated in the heart of the state, we specialize in crafting agitators that excel in durability and performance. Our skilled team and advanced facility ensure precision engineering, delivering stainless steel agitators that cater to diverse industries. From pharmaceuticals to chemicals, we redefine industrial processes, ensuring optimal mixing and blending. When you choose Uma Pharmatech Machinery, you’re not just partnering with an agitator manufacturer; you’re embracing a legacy of expertise and innovation that elevates Gujarat’s industrial landscape with high-quality stainless steel agitators.
Gujarat Agitator Engineering Services
Industrial Agitator Manufacturer in India
Uma Pharmatech Machinery stands out as a prominent industrial agitator manufacturer in India. Our commitment to excellence and innovation drives us to engineer agitators that redefine industrial processes. Situated in India, we specialize in crafting high-quality agitators that cater to diverse sectors. With a skilled team and advanced manufacturing facility, we ensure precision engineering and reliability in every agitator we produce. By choosing Uma Pharmatech Machinery, you’re not just partnering with an industrial agitator manufacturer; you’re aligning with a legacy of expertise and dedication that transforms industries with cutting-edge technology and exceptional solutions.
Agitator Maintenance in Gujarat
Agitator Maintenance Service in Gujarat
Uma Pharmatech Machinery offers unmatched agitator maintenance services in Gujarat. Situated in the region, we specialize in providing comprehensive solutions to ensure the optimal performance and longevity of your agitators. Our skilled technicians are equipped to handle various maintenance needs, from regular upkeep to troubleshooting and repairs. With a focus on precision and efficiency, we keep your agitators running seamlessly, minimizing downtime and maximizing productivity. By choosing Uma Pharmatech Machinery, you’re not just opting for agitator maintenance; you’re securing a partnership that prioritizes the smooth operation of your industrial processes in Gujarat, setting new standards for reliability.
Gujarat Agitator Industry Expert
Gujarat Agitator Industry Expert Solution
Uma Pharmatech Machinery stands as the definitive Gujarat agitator industry expert, offering comprehensive solutions to enhance industrial processes. Situated in the heart of Gujarat, our expertise combines cutting-edge technology with industry knowledge. We specialize in providing tailored agitator solutions that address unique challenges across sectors. With a skilled team and advanced facility, we engineer agitators that optimize mixing efficiency and performance. By choosing Uma Pharmatech Machinery, you’re not just accessing an agitator industry expert; you’re partnering with a company that transforms industry insights into practical solutions, setting new benchmarks for excellence in Gujarat’s dynamic industrial landscape.
Agitator System Integration Gujarat
Fluid Mixing Agitator Manufacturer Gujarat
Uma Pharmatech Machinery excels as a fluid mixing agitator manufacturer in Gujarat. Situated in the state, we specialize in crafting agitators that redefine fluid mixing processes. Our skilled team and advanced facility ensure precision engineering, delivering agitators that enhance mixing efficiency across industries. From pharmaceuticals to chemicals, we innovate to optimize. By choosing Uma Pharmatech Machinery, you’re not just selecting an agitator manufacturer; you’re embracing a legacy of expertise and innovation that elevates Gujarat’s industrial landscape with high-quality fluid mixing agitators. Experience the future of fluid mixing with us.
Process Agitator Gujarat
Process Agitator Manufacturer in Gujarat
Uma Pharmatech Machinery takes the lead as a process agitator manufacturer in Gujarat. Our expertise lies in crafting agitators that revolutionize industrial processes. Situated in the heart of Gujarat, our skilled team and advanced facility ensure precision engineering, delivering agitators that optimize various processes. From pharmaceuticals to chemicals, we redefine efficiency and productivity. By choosing Uma Pharmatech Machinery, you’re not just selecting an agitator manufacturer; you’re partnering with a company that drives process innovation, setting new benchmarks for excellence and reliability in Gujarat’s dynamic industrial landscape.
High Efficiency Agitator Manufacturer in Gujarat
Agitator Manufacturer in Gujarat
Uma Pharmatech Machinery stands as a leading agitator manufacturer in Gujarat. Situated in the heart of the state, we specialize in crafting high-quality agitators that cater to diverse industrial needs. Our skilled team and advanced facility ensure precision engineering, delivering agitators that optimize mixing processes across various sectors. From pharmaceuticals to chemicals, we redefine efficiency and performance. By choosing Uma Pharmatech Machinery, you’re not just selecting an agitator manufacturer; you’re partnering with a company that prioritizes innovation and excellence, setting new standards in Gujarat’s industrial landscape.
Agitator Manufacturer in Vadodara
Uma Pharmatech Machinery is the distinguished agitator manufacturer in Vadodara. Nestled in this industrial hub, we specialize in crafting agitators that redefine processes. Our skilled team and cutting-edge facility ensure precision engineering, delivering agitators that optimize mixing efficiency across industries. From pharmaceuticals to chemicals, we innovate to elevate. By choosing Uma Pharmatech Machinery, you’re not just selecting an agitator manufacturer; you’re aligning with a company that drives industrial progress, setting new benchmarks for excellence and reliability in Vadodara’s dynamic landscape. Trust us for agitators that transform your operations with unparalleled technology and expertise.
Agitator Manufacturer in Ankleshwar
Uma Pharmatech Machinery proudly stands as the distinguished agitator manufacturer in Ankleshwar. Situated in this industrial hub, we specialize in crafting agitators that redefine manufacturing processes. Our skilled team and state-of-the-art facility ensure precision engineering, delivering agitators that optimize mixing efficiency across sectors. From pharmaceuticals to chemicals, we drive innovation. By choosing Uma Pharmatech Machinery, you’re not just selecting an agitator manufacturer; you’re partnering with a company that prioritizes excellence and reliability, setting new standards in Ankleshwar’s industrial landscape. Rely on us for agitators that elevate your operations with cutting-edge technology and expertise.
Agitator Manufacturer in Rajkot
Uma Pharmatech Machinery is a distinguished agitator manufacturer in Rajkot. Situated in this industrial city, we specialize in crafting agitators that redefine industrial processes. Our skilled team and advanced facility ensure precision engineering, delivering agitators that optimize mixing efficiency across sectors. From pharmaceuticals to chemicals, we drive innovation. By choosing Uma Pharmatech Machinery, you’re not just selecting an agitator manufacturer; you’re partnering with a company that prioritizes excellence and reliability, setting new standards in Rajkot’s industrial landscape. Trust us for agitators that elevate your operations with cutting-edge technology and expertise.
Agitator Manufacturer in Surat
Uma Pharmatech Machinery takes pride in being an eminent agitator manufacturer in Surat. Nestled in this bustling city, we specialize in crafting agitators that redefine industrial processes. Our skilled team and cutting-edge facility ensure precision engineering, delivering agitators that optimize mixing efficiency across sectors. From pharmaceuticals to chemicals, we drive innovation. By choosing Uma Pharmatech Machinery, you’re not just selecting an agitator manufacturer; you’re partnering with a company that prioritizes excellence and reliability, setting new benchmarks in Surat’s industrial landscape. Trust us for agitators that enhance your operations with cutting-edge technology and expertise.
Agitator Manufacturer in Valsad
Uma Pharmatech Machinery stands as a distinguished agitator manufacturer in Valsad. Situated in this thriving industrial center, we specialize in crafting agitators that redefine manufacturing processes. Our skilled team and advanced facility ensure precision engineering, delivering agitators that optimize mixing efficiency across sectors. From pharmaceuticals to chemicals, we drive innovation. By choosing Uma Pharmatech Machinery, you’re not just selecting an agitator manufacturer; you’re partnering with a company that prioritizes excellence and reliability, setting new benchmarks in Valsad’s industrial landscape. Count on us for agitators that elevate your operations with cutting-edge technology and expertise. UPM is Leading Manufacturer of Portable Agitator in Gujarat
Agitator Manufacturer in Vapi
Uma Pharmatech Machinery stands as a premier agitator manufacturer in Vapi. Positioned in this industrially vibrant city, we specialize in crafting agitators that redefine manufacturing processes. Our skilled team and state-of-the-art facility ensure precision engineering, delivering agitators that optimize mixing efficiency across sectors. From pharmaceuticals to chemicals, we drive innovation. By choosing Uma Pharmatech Machinery, you’re not just selecting an agitator manufacturer; you’re partnering with a company that prioritizes excellence and reliability, setting new benchmarks in Vapi’s industrial landscape. Rely on us for agitators that elevate your operations with cutting-edge technology and expertise.
Agitator Manufacturer in Ahmedabad
Uma Pharmatech Machinery takes pride in being a leading agitator manufacturer in Ahmedabad. Situated in this industrial hub, we specialize in crafting agitators that redefine manufacturing processes. Our skilled team and advanced facility ensure precision engineering, delivering agitators that optimize mixing efficiency across sectors. From pharmaceuticals to chemicals, we drive innovation. By choosing Uma Pharmatech Machinery, you’re not just selecting an agitator manufacturer; you’re partnering with a company that prioritizes excellence and reliability, setting new benchmarks in Ahmedabad’s industrial landscape. Trust us for agitators that elevate your operations with cutting-edge technology and expertise.
Agitator Manufacturer in Dahej
Uma Pharmatech Machinery stands as a premier agitator manufacturer in Dahej. Positioned in this industrial hub, we specialize in crafting agitators that redefine manufacturing processes. Our skilled team and state-of-the-art facility ensure precision engineering, delivering agitators that optimize mixing efficiency across sectors. From pharmaceuticals to chemicals, we drive innovation. By choosing Uma Pharmatech Machinery, you’re not just selecting an agitator manufacturer; you’re partnering with a company that prioritizes excellence and reliability, setting new benchmarks in Dahej’s industrial landscape. Rely on us for agitators that elevate your operations with cutting-edge technology and expertise.
Agitator Manufacturer in Panoli GIDC
Uma Pharmatech Machinery proudly leads as an acclaimed agitator manufacturer in Panoli GIDC. Positioned in this industrial center, we specialize in crafting agitators that redefine manufacturing processes. Our skilled team and state-of-the-art facility ensure precision engineering, delivering agitators that optimize mixing efficiency across sectors. From pharmaceuticals to chemicals, we drive innovation. By choosing Uma Pharmatech Machinery, you’re not just selecting an agitator manufacturer; you’re partnering with a company that prioritizes excellence and reliability, setting new benchmarks in Panoli GIDC’s industrial landscape. Rely on us for agitators that elevate your operations with cutting-edge technology and expertise.
Agitator Manufacturer in Sachin GIDC
Uma Pharmatech Machinery emerges as a distinguished agitator manufacturer in Sachin GIDC. Situated in this industrial hub, we specialize in crafting agitators that redefine manufacturing processes. Our skilled team and state-of-the-art facility ensure precision engineering, delivering agitators that optimize mixing efficiency across sectors. From pharmaceuticals to chemicals, we drive innovation. By choosing Uma Pharmatech Machinery, you’re not just selecting an agitator manufacturer; you’re partnering with a company that prioritizes excellence and reliability, setting new benchmarks in Sachin GIDC’s industrial landscape. Rely on us for agitators that elevate your operations with cutting-edge technology and expertise. We are Leading Manufacturer and Supplier of Industrial Agitator in Surat.
Agitator Manufacturer in Maharashtra
Uma Pharmatech Machinery proudly leads as a reputable agitator manufacturer in Maharashtra. Situated in this dynamic state, we specialize in crafting agitators that redefine manufacturing processes. Our skilled team and state-of-the-art facility ensure precision engineering, delivering agitators that optimize mixing efficiency across sectors. From pharmaceuticals to chemicals, we drive innovation. By choosing Uma Pharmatech Machinery, you’re not just selecting an agitator manufacturer; you’re partnering with a company that prioritizes excellence and reliability, setting new benchmarks in Maharashtra’s industrial landscape. Rely on us for agitators that elevate your operations with cutting-edge technology and expertise.
Agitator Manufacturer in Bharuch
Uma Pharmatech Machinery stands at the forefront as an esteemed agitator manufacturer in Bharuch. Situated in this industrial hub, we specialize in crafting agitators that redefine manufacturing processes. Our skilled team and state-of-the-art facility ensure precision engineering, delivering agitators that optimize mixing efficiency across sectors. From pharmaceuticals to chemicals, we drive innovation. By choosing Uma Pharmatech Machinery, you’re not just selecting an agitator manufacturer; you’re partnering with a company that prioritizes excellence and reliability, setting new benchmarks in Bharuch’s industrial landscape. Rely on us for agitators that elevate your operations with cutting-edge technology and expertise.
Agitator Manufacturer in Jhagadia GIDC
Uma Pharmatech Machinery stands tall as a distinguished agitator manufacturer in Jhagadia GIDC. Positioned in this industrially vibrant zone, we specialize in crafting agitators that redefine manufacturing processes. Our skilled team and state-of-the-art facility ensure precision engineering, delivering agitators that optimize mixing efficiency across sectors. From pharmaceuticals to chemicals, we drive innovation. By choosing Uma Pharmatech Machinery, you’re not just selecting an agitator manufacturer; you’re partnering with a company that prioritizes excellence and reliability, setting new benchmarks in Jhagadia GIDC’s industrial landscape. Rely on us for agitators that elevate your operations with cutting-edge technology and expertise.
Industrial Stirrer Manufacturer in Gujarat
Industrial Stirrer Manufacturer in Gujarat
As a pioneering industrial stirrer manufacturer and supplier, Uma Pharmatech Machinery is dedicated to transforming industries through innovative solutions. Situated in Gujarat, our expertise spans various categories, including portable stirrers that redefine convenience and efficiency.
Our commitment extends to key areas such as Ahmedabad, Vadodara, Surat, Rajkot, Valsad, Vapi, Dahej, Ankleshwar, Jhagadia, and Panoli, where we ensure the seamless supply of our cutting-edge products.
With a focus on precision engineering, we take pride in offering a range of industrial stirrers that elevate manufacturing processes across sectors. From pharmaceuticals to chemicals and beyond, our stirrers ensure optimal mixing, enhancing product quality and productivity.
Portable Stirrer Manufacturer and Suppliers
Our prowess doesn’t end at manufacturing; we’re also prominent portable stirrer suppliers, catering to the dynamic needs of industries. Our portable stirrers offer flexibility without compromising on performance, making them an ideal choice for various applications.
Industrial Stirrer Manufacturers in Gujarat
At Uma Pharmatech Machinery, we believe in creating solutions that set new standards. Our status as a stirrer manufacturer in Gujarat is synonymous with reliability, innovation, and expertise. Our dedication to quality ensures that every stirrer we produce contributes to operational excellence.
As we extend our offerings to areas like Ahmedabad, Vadodara, Surat, Rajkot, Valsad, Vapi, Dahej, Ankleshwar, Jhagadia GIDC, and Panoli GIDC, we’re committed to being your partner in progress. Our industrial stirrers and portable stirrers redefine how industries function, enhancing efficiency and streamlining operations.
When you choose Uma Pharmatech Machinery, you’re not just acquiring products; you’re embracing a legacy of innovation and reliability that enhances industrial processes across Gujarat’s landscape. Trust us for cutting-edge solutions that propel your success forward.
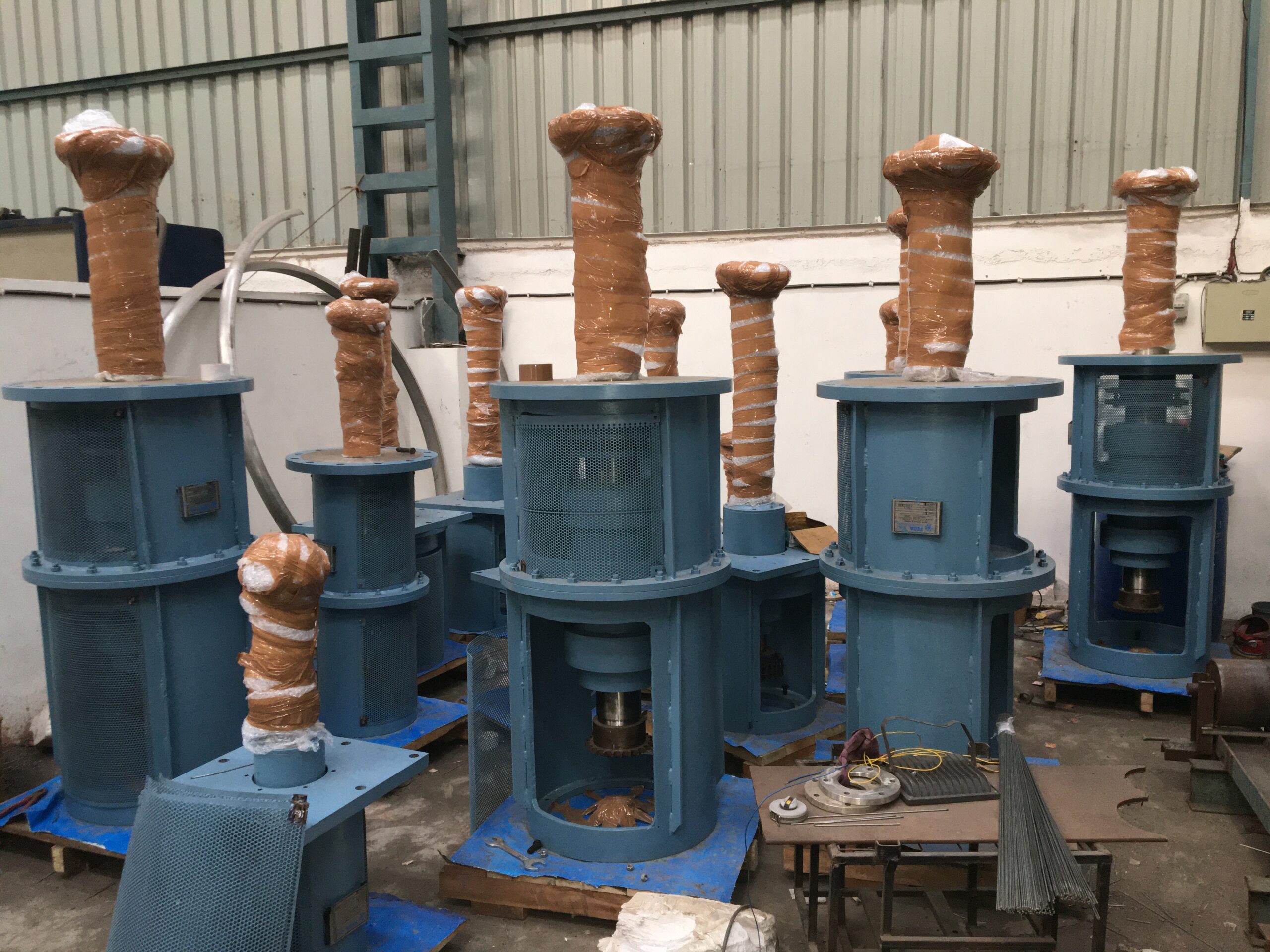