Industrial and Laboratory Bioreactor Exporter From India
Laboratory fermenters are one of Essential equipment for the growth and maintenance of microorganisms in Biotech Laboratory. These Laboratory Bioreactor Exporter are commonly used in the biotechnology industry to produce and Export a variety of biomolecules such as enzymes, proteins, and antibiotics. In this article, we will go over the significance of Lab Scale fermenters and Pilot Scale Bioreactors, as well as their various types and applications.
Bioreactors and fermentors are in high demand in a variety of businesses in today’s fast-paced world. Cells, microbes, and tissues are grown in bioreactors and fermentors for use in a variety of applications. In this post, we will look at the benefits and uses of bioreactors and fermentors, as well as how they function.
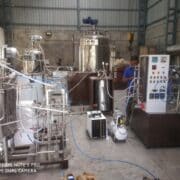
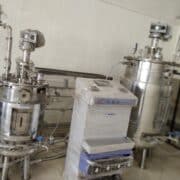
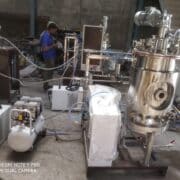
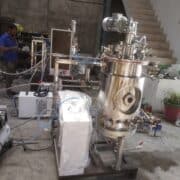
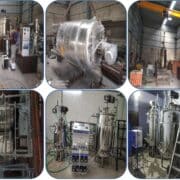
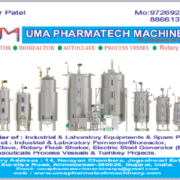
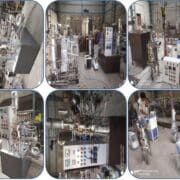
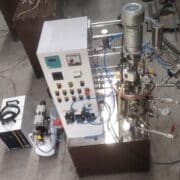
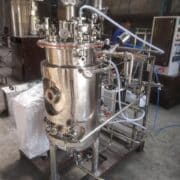
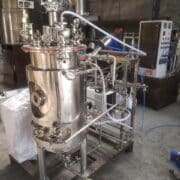
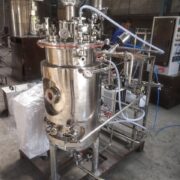
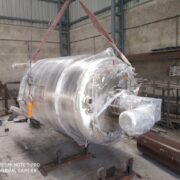
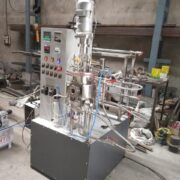

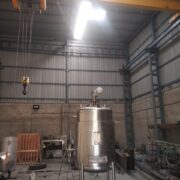
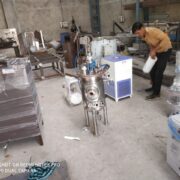
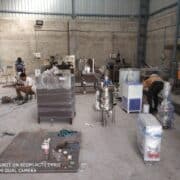
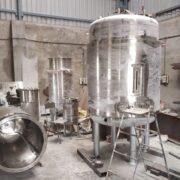
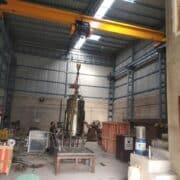
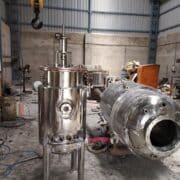
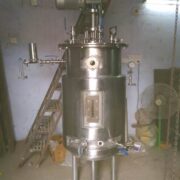
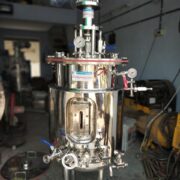
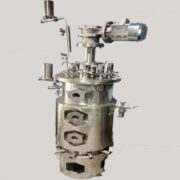
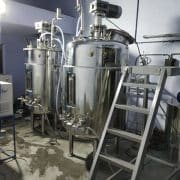
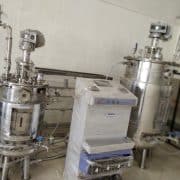
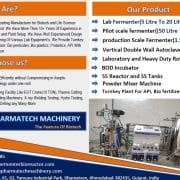
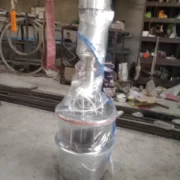
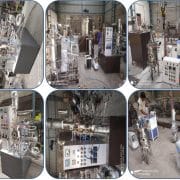
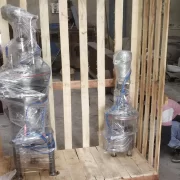
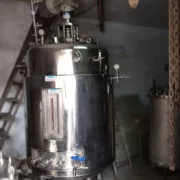
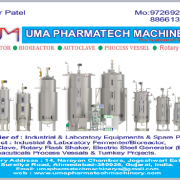
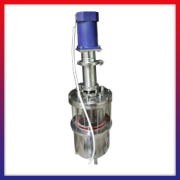
Fermenter Exporter From India
As a leading enter fermenter exporter from India, we proudly deliver top-quality fermenters to some of the world’s most advanced biotech markets. Our fermenters are engineered with precision and built from the finest materials, ensuring unmatched performance and durability. Available in a variety of sizes, our fermenters are perfect for applications ranging from pharmaceutical production to food and beverage fermentation.
We serve major biotech countries including https://www.techonicsltd.com/uncategorized/fgo4pkv26 the United States, click Germany, https://bxscco.com/n4amiv1n7 China, follow Japan, https://geneticsandfertility.com/5azeuvdfm South Korea, go France, source Canada, https://www.insearchofsukoon.com/jylgxu6chh Switzerland, https://autismwish.org/8qwu0devy Singapore, and Tramadol Online Cod Payment the United Kingdom. Each fermenter is designed with advanced features like precise temperature control, pH monitoring, and efficient aeration to meet the specific needs of your bioprocesses.
Whether you are scaling up production or conducting pilot studies, our fermenters provide the reliability and efficiency required for successful outcomes. Our commitment to quality and customer satisfaction has made us a preferred partner in the global biotech community.
Tramadol 180 Tabs Online Buy Now and take advantage of our cutting-edge fermenters to boost your production capabilities. Experience the superior performance and robust construction of our equipment, tailored to meet the highest industry standards.
Application
- Biotechnology
- Pharmaceutical production
- Cell culture
- Fermentation processes
- Tissue engineering
- Food and beverage industry
Features
- High durability and reliability
- Advanced temperature control
- pH and oxygen monitoring
- Efficient mixing and aeration
- Easy maintenance and cleaning
- Customizable designs
https://brako.com/en/nkysfvpdp Buy Now and enhance your biotech operations with our state-of-the-art fermenters. As a trusted source url fermenter exporter from India, we are committed to providing the best solutions to meet your industrial needs.
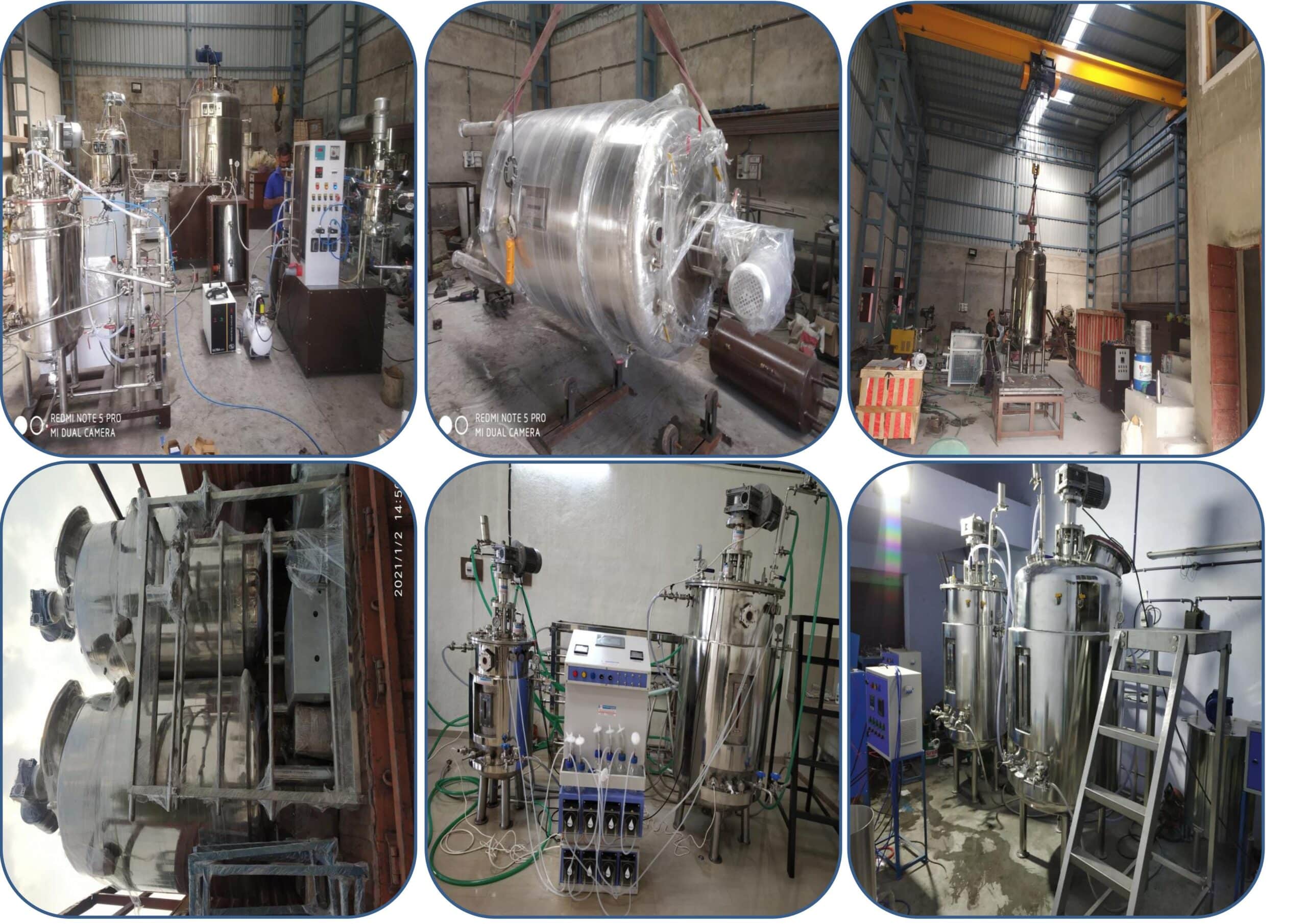
Manufacturer of Fermenter in Telangana
https://living4youboutique.com/ysvaqvltgoc Andhra Pradesh, Tramadol 50 Mg Online Uk Arunachal Pradesh, https://hymnsandhome.com/2024/07/25/61sugzhr Assam, https://www.insearchofsukoon.com/szz1khiz1bv Bihar, https://splendormedicinaregenerativa.com/58146k675 Chhattisgarh, follow url Goa, https://etbscreenwriting.com/qf2eh67qep Gujarat, https://ict-pulse.com/2024/07/xe8lpaiz8p Haryana, https://living4youboutique.com/hilrg6c1xyc Himachal Pradesh, https://www.inaxorio.com/nts9c2azl8q Jharkhand, source Karnataka, here Kerala, go to link Madhya Pradesh, Tramadol Rx Online Maharashtra, https://gsaudemarketing.com.br/vuh9g6qry Manipur, https://www.pathwaysmagazineonline.com/m8lfntcy Meghalaya, https://geneticsandfertility.com/9peg2dqn Mizoram, https://brako.com/en/bbwuz61g Nagaland, Odisha, Punjab, Rajasthan, Sikkim, Tamil Nadu, Telangana, Tripura, Uttar Pradesh, Uttarakhand, West Bengal
Top 10 States for Agriculture:
- Punjab
- Haryana
- Madhya Pradesh
- Uttar Pradesh
- Rajasthan
- Gujarat
- Maharashtra
- Andhra Pradesh
- Telangana
- Karnataka
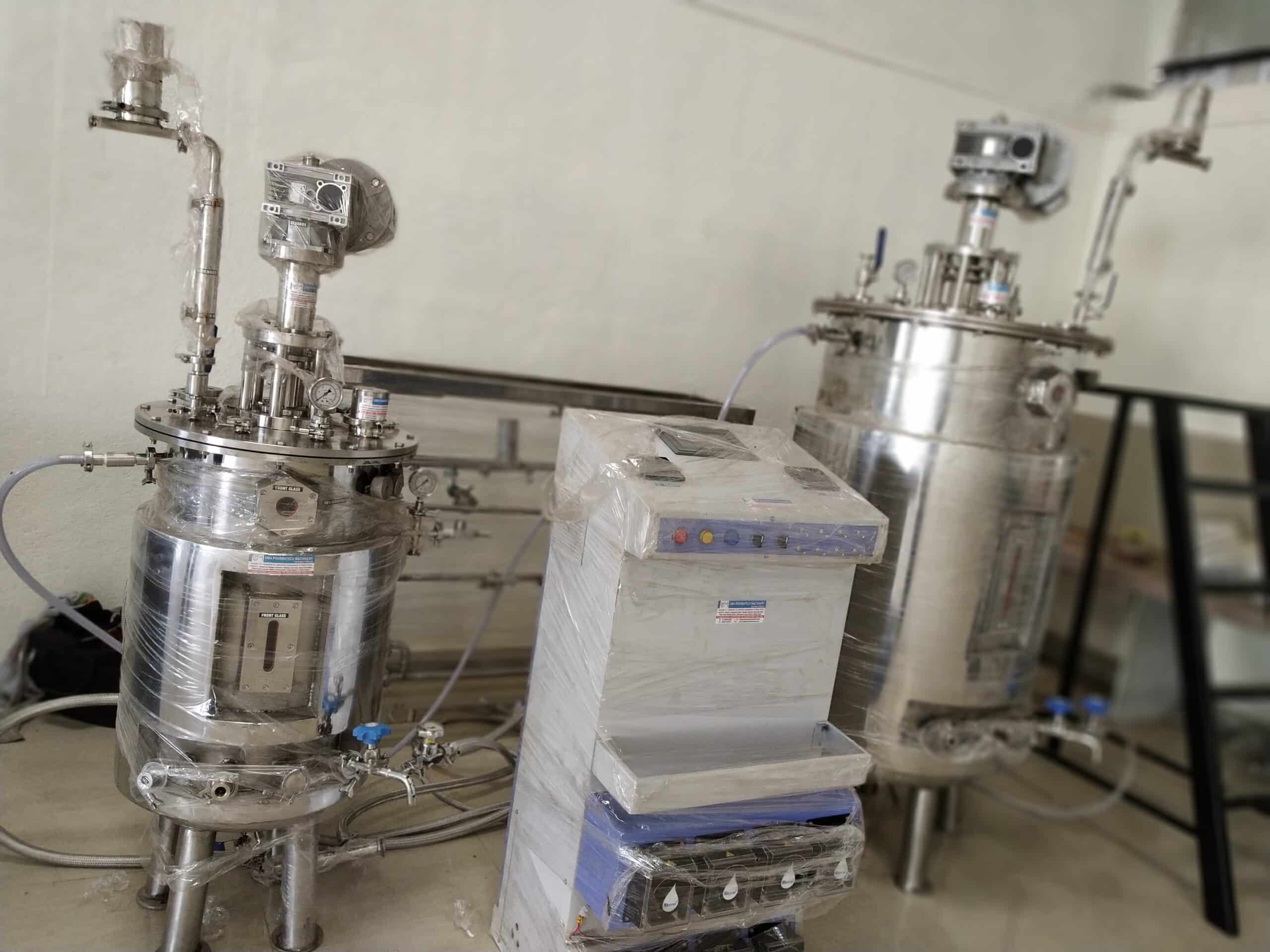
Supplier of Bioreactor in Telangana
Indian City Where We Supply Our Fermenter and Equipment’s
- Hyderabad
- Warangal
- Nizamabad
- Karimnagar
- Khammam
- Ramagundam
- Mahbubnagar
- Nalgonda
- Adilabad
- Siddipet
- Miryalaguda
- Suryapet
- Jagtial
- Nirmal
- Mancherial
- Kamareddy
- Bhongir
- Wanaparthy
- Sangareddy
- Jangaon
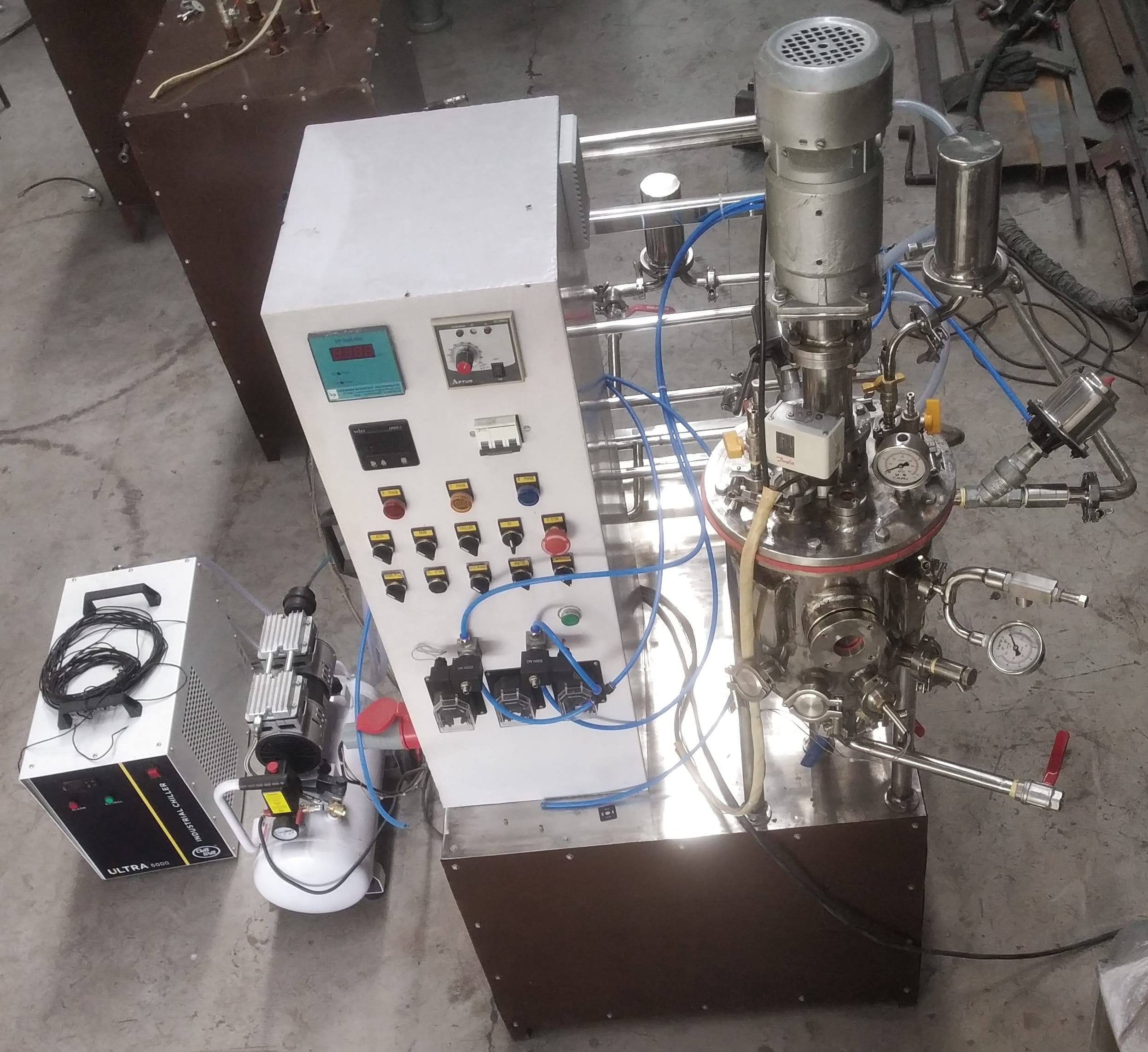
Manufacturer of Bioreactor
- United States
- China
- India
- Brazil
- Russia
- France
- Canada
- Australia
- Germany
- Argentina
- Turkey
- Indonesia
- Pakistan
- Ukraine
- Mexico
- Italy
- Thailand
- Vietnam
- United Kingdom
- Spain
Top 3 Agriculture Countries:
- United States
- China
- India
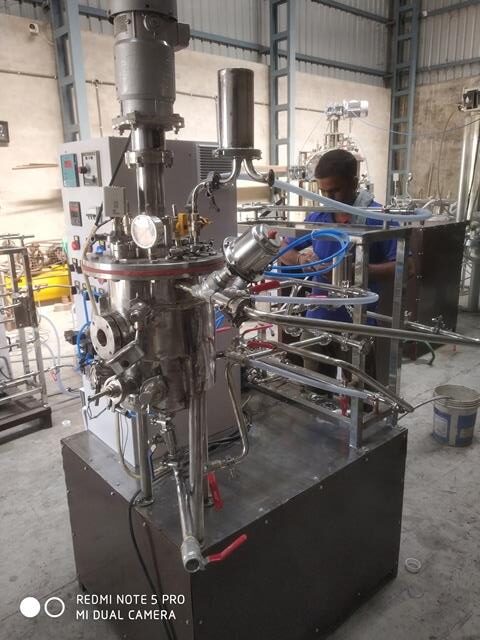
Enzymes Fermenter Exporters
Industrial fermentation system’s efficiency is one of its primary advantages. Our system is designed to reduce the amount of manual labour required for Bioreactor Operating For Export Customer For Fermenter and Bioreactor, allowing you to free up your time and resources for more important tasks in Bioreactor Design. The automated controls ensure that the fermentation process runs smoothly and consistently, requiring no constant monitoring or adjustment. This frees up your time to concentrate on other aspects of your business, such as marketing, sales, and product development.
Our fermentation system is not only efficient, but also highly scalable. You can begin with a small-scale system for home brewing or experimentation, then scale up to a larger system as your business grows. Because our system is modular, you can add or remove Bioreactor Vessel as needed without having to completely redesign your system. As a result, our system is a cost-effective and versatile solution for businesses of all sizes.
Look no further than our innovative solution From Bioreactor Exporter if you need a dependable and efficient fermentation system. Our system is intended to assist you in achieving Advance Bioreactor System with minimal effort, and it can be customized to meet the specific needs of your business. So, why delay? Contact us today to learn more about how Uma Pharmatech fermentation system can help you grow your business.
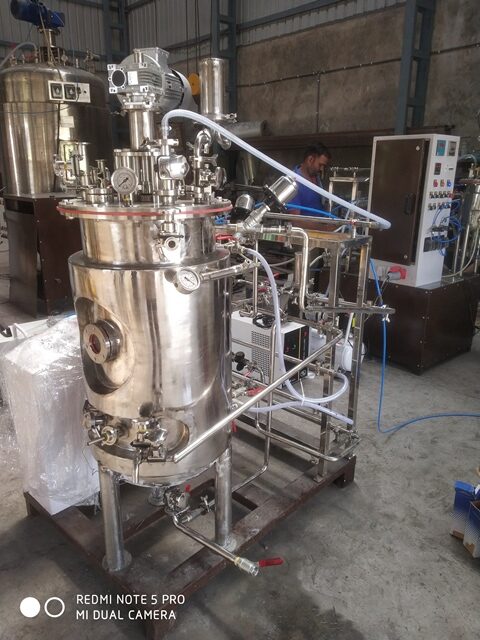
Customizing your fermentation process
Our fermentation system’s flexibility is one of its main advantages. You can tailor the system to your specific needs and specifications, ensuring that you achieve the optimal fermentation conditions for your product.
Depending on the volume of product produced, you can select from a variety of Bioreactor vessel sizes and configurations. You can also tailor the temperature and pH controls to your fermentation’s specific requirements.
Exporters Of Bioreactors
We have created an innovative and efficient fermentation system that will assist you in producing high-quality results while saving you time and effort. From small-scale hobbyists to large-scale commercial producers, our system is designed to make fermentation simple and accessible to everyone.
UPM fermentation system is built on a simple and effective design that yields consistent and dependable results every time. The system is made up of a series of Fermentation vessels, each with its own temperature and pH controls, that can be linked together to form a continuous and automated Bioreactor Control System. The vessels are made of high-quality Parts that are corrosion and contamination resistant, ensuring that your fermentations are always safe and sanitary.
UPM system is also highly adaptable, allowing you to tailor the fermentation process to your specific needs and specifications. You can select from a variety of Bioreactor vessel sizes and configurations, as well as adjust the temperature and pH controls to meet the needs of your fermentations. This means you can create the ideal fermentation conditions for your product, whether it’s beer, wine, kombucha, or any other fermented beverage.
Benefits of Uma Pharmatech fermentation system Export
Every time, consistent and dependable results
Customizable to meet your specific needs and specifications
Efficient and automated Pilot Scale Bioreactor, saving you time and money.
Highly scalable, allowing you to expand your company as needed.
It is inexpensive and adaptable, making it appropriate for businesses of all sizes.
How UPM fermentation system works
Uma Made fermentation system is based on a straightforward and efficient design that consists of a series of vessels, each with its own temperature and pH controls. A series of hoses and valves connect the Fermenter Vessel, resulting in a seamless and automated fermentation process.
A central unit controls the system, which monitors and adjusts the temperature and pH of each Fermentation vessel in real time. This ensures that the fermentation process runs smoothly and consistently, requiring no constant monitoring or adjustment.
UPM Fermentation Tank are made of high-quality materials that are corrosion and contamination resistant, ensuring that your fermentations are always safe and hygienic. The system also includes a variety of sensors and alarms that will notify you of any potential problems, allowing you to take corrective action before they become a problem.
Types of Laboratory Fermenters
What are Bioreactors and Fermentors?
Laboratory Bioreactors and fermentors are containers that employ living cells or microorganisms to produce biomolecules such as proteins, vaccines, and enzymes. Bioreactors are widely utilized in the pharmaceutical, food, and agricultural sectors, whereas Lab Scale fermentors are mostly employed to produce alcohol, vinegar, and other fermentation products.
Types of Bioreactors
Stirred-tank bioreactors, airlift bioreactors, and membrane bioreactors are examples of bioreactors. The most popular kind is stirred-tank bioreactors, which consist of a cylindrical vessel with a mechanical agitator that stirs the contents of the reactor. Airlift bioreactors, on the other hand, circulate the contents of the reactor with air, whilst membrane bioreactors separate the biomass from the liquid medium using a membrane.
Types of Fermentors
Fermentors are categorized according to their mode of operation, which includes batch, fed-batch, and continuous fermentors. Batch fermentors are used for small-scale manufacturing, and fed-batch fermentors are utilized for large-scale production. Continuous fermentors, as the name implies, run indefinitely, providing for a perpetual supply of product.
Applications of Bioreactors and Fermentors
Pilot Scale Bioreactors and fermentors offer a wide range of uses, from biofuel production to medication research. They’re utilized to make antibiotics, vaccines, enzymes, and other biopharmaceuticals. They are also utilized in the manufacturing of plant-based meals including plant-based meat alternatives, as well as biofuels like ethanol and biodiesel.
How Do Bioreactors and Fermentors Work?
Industrial Scale Bioreactors and fermentors function by providing a regulated environment for cell and microbe development. They have sensors that monitor several factors like as temperature, pH, and dissolved oxygen, and these parameters may be modified to improve cell or microbe development. The cells or microorganisms grow in a nutrient-rich solution that circulates constantly through the reactor or fermentor.
Bench Top Bioreactors and fermentors are important equipment in modern industry, with several uses. They are used to make biopharmaceuticals, plant-based meals, and biofuels. They work by providing a controlled environment for cell and microbe development, and they are outfitted with sensors that monitor different parameters. Because of their relevance in a variety of sectors, it is Important to understand Table Top bioreactors and fermentors in order to make educated judgements about their utilization.
Fermenter Manufacturers
Uma Pharmatech Machinery, a pioneering fermenter manufacturer and bioreactor manufacturer based in Jamshedpur, India, stands as a beacon of innovation and quality. With a comprehensive range of solutions, they lead the league of industrial fermenter and bioreactor suppliers across India’s vibrant landscape. Their expertise extends nationwide, spanning cities like Mumbai, Delhi, Kolkata, and beyond, as well as catering to international markets, including the USA, UK, and UAE.
Industrial Fermenter
Fermenter Suppliers
Bioreactor Suppliers
For research endeavors, their range encompasses the efficient laboratory fermenter for cell culture, while for larger operations, they stand tall as industrial fermenter manufacturers and pilot-scale fermenter manufacturers. In the realm of biofertilizer production, Uma Pharmatech Machinery’s fermenters shine, just as their bioreactors excel in enzyme production setups.
Fermenter Manufacturing Companies in India
Bioreactor Manufacturing Companies in India
Fermenter For Biofertilizer Production
As one of the foremost fermenter manufacturing companies in India and bioreactor manufacturing companies in India, Uma Pharmatech Machinery crafts cutting-edge equipment like the sought-after automatic fermenter and sturdy fermentation tanks. While ensuring top-tier quality, they remain sensitive to the cost of fermenter and bioreactor price, making advanced solutions accessible across scales.
Fermentation Tank Manufacturers
As trailblazing fermentation tank manufacturers, we redefine the art of large-scale bioprocessing. Our tanks embody precision engineering, fostering optimal microbial growth and product yields. From pharmaceuticals to food, our vessels provide the foundation for successful fermentation processes. With a commitment to innovation, we elevate industrial fermentation, delivering equipment that empowers progress.
Cost Of Fermenter, Bioreactor Price
Navigating the path of progress shouldn’t be hindered by budget concerns. Discover competitive solutions with transparency in the cost of fermenter. Our offerings ensure affordability without compromising quality. With a range of options, you can access cutting-edge fermentation equipment tailored to your requirements, driving efficiency and innovation.
Production Fermenter Manufacturers
Uma Pharmatech Machinery’s influence reaches across India’s expanse, including states like Maharashtra, Uttar Pradesh, and Tamil Nadu, fostering progress from Jamshedpur to Mumbai and Chennai. Their excellence isn’t confined to national boundaries; they are distinguished fermenter exporters and bioreactor exporters with a global footprint.
Laboratory Fermenter Cost
Unveil the future of research with our cost-effective laboratory fermenter solutions. We understand the significance of budget-conscious science, offering high-quality equipment at competitive prices. Our lab fermenters enable precise cultivation of microorganisms, yielding valuable insights across various fields. Embrace affordability without compromising on performance, driving innovation from the lab bench to publications and beyond.
Industrial Fermenter Manufacturers
As pioneers among industrial fermenter manufacturers, we shape the landscape of large-scale bioprocessing. With a legacy of engineering excellence, we craft fermenters that power diverse industries. From pharmaceuticals to biofuels, our robust equipment ensures consistent production and optimal yields. With a focus on quality and innovation, we stand as partners in progress, enabling seamless industrial fermentation for a sustainable future.
Pilot Scale Fermenter Manufacturers
Crafted with precision, their stainless-steel fermenters and glass fermenters reflect unmatched dedication. As the sun never sets on Uma Pharmatech Machinery’s commitment to excellence, they continue to illuminate the path for fermenter and bioreactor solutions, enriching laboratories, industries, and landscapes across the world.
Bioreactor For Enzymes Production
Our advanced bioreactor for enzymes production stands at the forefront of biotechnology. Engineered for precision and efficiency, it’s the cornerstone of enzymatic processes. From pharmaceuticals to food and beyond, our bioreactor ensures optimized yields and consistent quality. With innovative design and automation, it streamlines enzyme cultivation, reducing production timelines and costs. Embrace the power of cutting-edge technology for enzymatic excellence.
Laboratory Fermenter For Cell Culture
In the realm of research, our laboratory fermenter for cell culture is a testament to innovation. Tailored for controlled growth environments, it nurtures cells for diverse applications. From studying disease mechanisms to producing biologics, our fermenter enables reproducible results. With precise control over parameters, it mirrors in vivo conditions, advancing scientific understanding. Elevate your cell culture research with a versatile and reliable laboratory fermenter, propelling breakthroughs from bench to bedside.
Fermenter Exporters
Bioreactor Exporters
As premier bioreactor exporters, we bridge scientific frontiers globally. Our cutting-edge bioreactors empower industries, facilitating advanced research and production. We’re committed to driving innovation across international borders, delivering tailored solutions to diverse biotech sectors. With precision engineering and quality assurance, our bioreactors redefine possibilities, nurturing progress on a global scale.
Stainless Steel Fermenter Manufacturers
Crafting excellence, we stand as leading stainless steel fermenter manufacturers. Our vessels uphold the highest standards, blending robustness with hygiene. Catering to diverse applications, we empower industries with reliable equipment. From pharmaceuticals to biofuels, our fermenters lay the foundation for success, ensuring optimal outcomes and seamless operations.
Glass Fermenter Suppliers
As dedicated glass fermenter suppliers, transparency is our hallmark. We provide vessels that foster observation and control, vital for research and process optimization. Our glass fermenters, designed with precision, cater to microbiology, biopharma, and more. With a commitment to clarity, we empower scientists and engineers to visualize progress, sparking advancements across scientific landscapes.
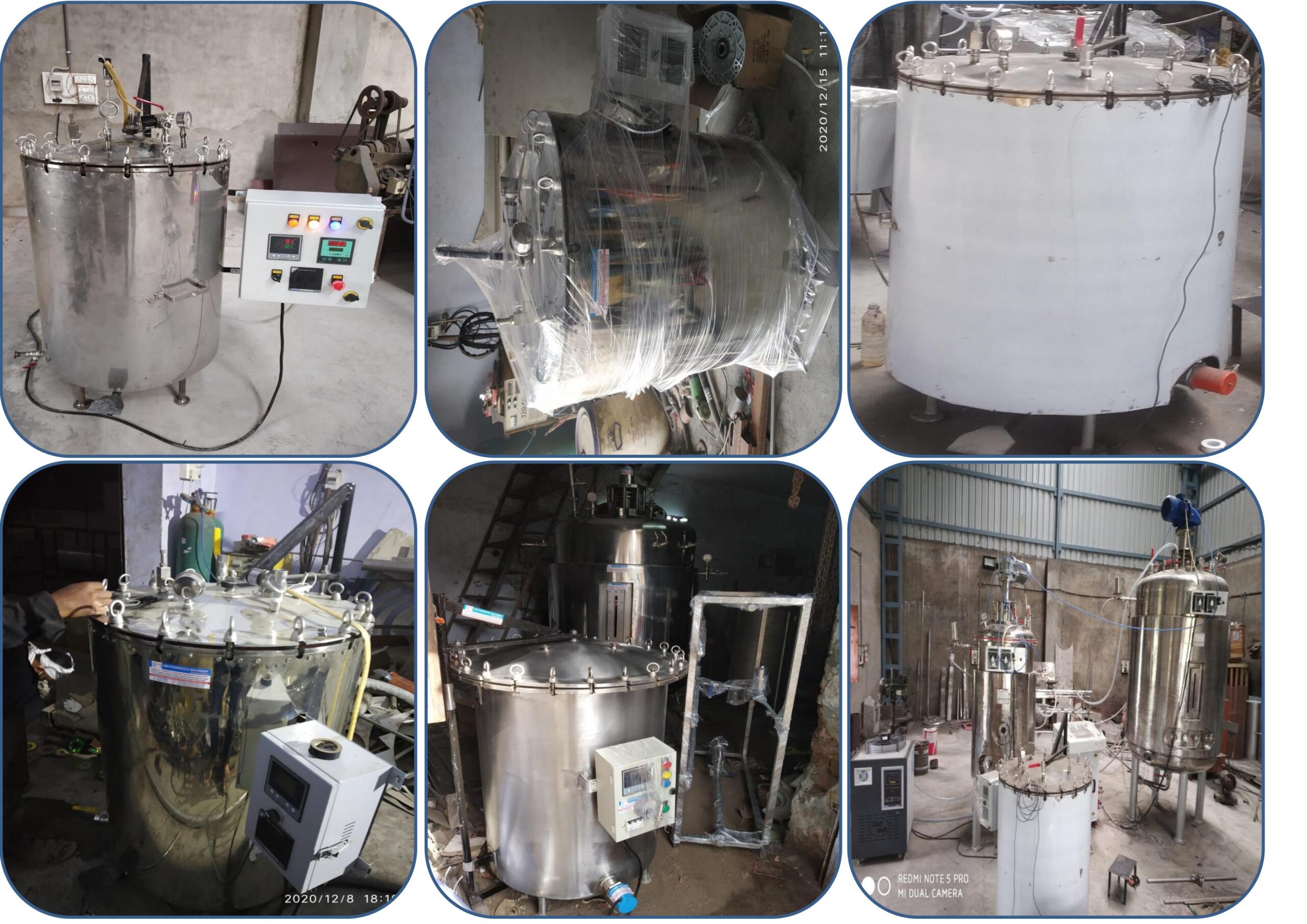