Industrial Fermenter Manufacturer in Mumbai
Pharmacies, chemicals, food, and biofuels are just a few of the industries where industrial fermenters are used. Industrial fermenters are used in the pharmaceutical sector to make antibiotics, vaccines, and other medications. Fermenters are used in the chemical industry to make organic acids, solvents, and other specialty compounds.
follow url Industrial fermenters are used in the food business to make fermented goods including yoghurt, cheese, and bread. Fermenters are used in the biofuels sector to make ethanol and other biofuels from renewable resources like corn and sugarcane.
click here Industrial fermenters are used by Mumbai-based businesses in the food sector to create fermented goods like yoghurt, cheese, and bread. For instance, the Mumbai-based Uma Pharmatech employs commercial fermenters to make a range of dairy goods, such as cheese, yoghurt, and ice cream.
go here Businesses situated in Mumbai that work in the biofuels sector use industrial fermenters to create ethanol and other biofuels from renewable resources like sugarcane. For instance, the Mumbai-based Uma Pharmatech company turns molasses, a byproduct of the processing of sugarcane, into ethanol using industrial fermenters.
FERMENTER MANUFACTURER IN MUMBAI
Online Doctor To Prescribe Tramadol Uma Pharmatech Machinery, based in Ahmedabad, Gujarat, is a renowned https://etbscreenwriting.com/az5ozde7rrb laboratory bioreactor manufacturer in Mumbai. Their commitment to innovation and quality makes them a vital contributor to Mumbai’s vibrant scientific research and development landscape. Uma Pharmatech Machinery specializes in crafting cutting-edge laboratory bioreactors tailored to the specific needs of microbial and cell culture processes in laboratories. Their precision-engineered bioreactors are known for their reliability and performance. With a focus on customization, Uma Pharmatech Machinery ensures that each laboratory bioreactor aligns seamlessly with Mumbai’s unique research requirements. They stand as a trusted partner in advancing scientific progress and innovation in Mumbai and beyond.
Mumbai, commonly referred to as Bombay, serves as the state capital of Maharashtra in India. It is a significant business and financial hub and one of India’s most populous cities. As a result, it is not surprising that Mumbai is home to several companies, including those that produce food, chemicals, pharmaceuticals, and biofuels. Industrial fermenters are essential to the production process in each of these sectors.
Fermenter Manufacturers in Mumbai
Mumbai, India’s financial hub, has a booming industrial sector that includes fermenter and bioreactor manufacturers. The city’s strategic position, well-developed infrastructure, and access to a talented workforce make it a desirable location for biotechnology and pharmaceutical companies. With multiple suppliers and specialized service providers accessible, Mumbai’s manufacturing ecosystem allows the creation of high-quality fermenters and bioreactors. Furthermore, the city’s thriving economic environment and vast network of research institutes stimulate innovation and collaboration, adding to its allure for manufacturers.
Fermenter and bioreactor makers are part of the developing industrial sector in Mumbai, the financial capital of India. The city is a sought-after destination for biotechnology and pharmaceutical enterprises due to its strategic location, well-developed infrastructure, and accessibility to a skilled workforce. Mumbai’s industrial ecosystem enables the construction of high-quality fermenters and bioreactors since it has several suppliers and access to specialized service providers. Additionally, the city’s robust business community and extensive network of research institutes foster innovation and teamwork, increasing its appeal to manufacturers.
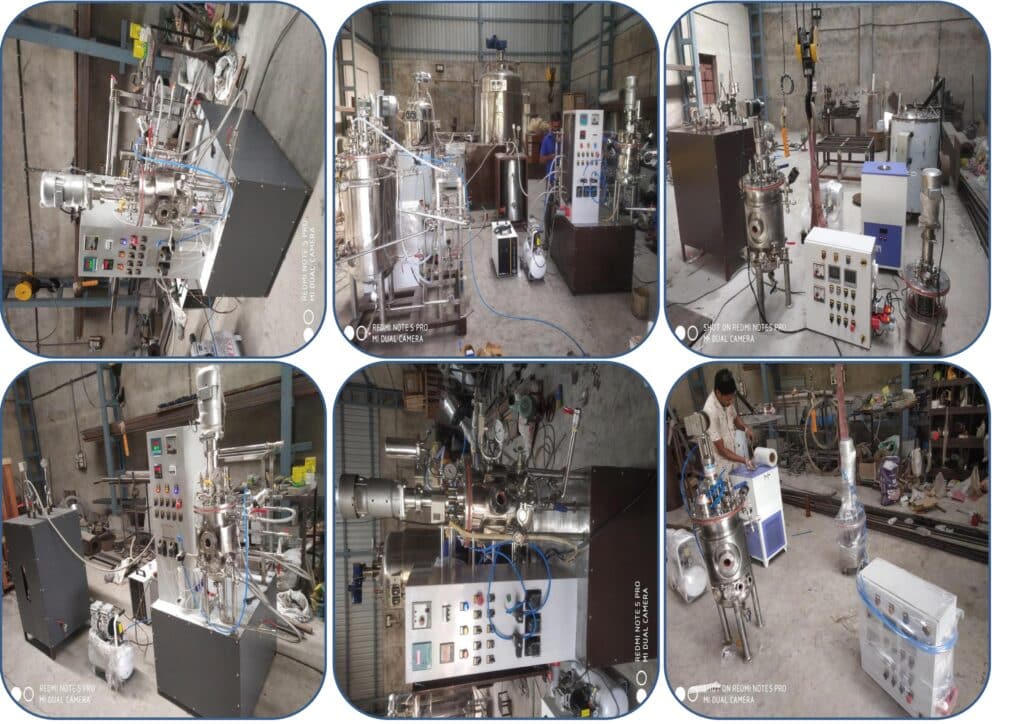
List Of Fermenter Manufacturing Companies
List Of Fermenter Top 3 Bioreactor Manufacturers
• Uma Pharmatech Machinery(www.umapharmatechmachinery.com), M:+91-9726923885
• Ssfermenter bioreactor(www.ssfermenterbioreactor.com), M:+91-9033404554
• Maruti Engineering Works(https://biofertilizerfermenterplant.blogspot.com/), M:+91-8866137364
Mumbai Leading Fermenter Manufacturers
Manufacturers of fermenters in Mumbai, Pune, and Nashik, Maharashtra Are you looking for reputable fermenter manufacturers in Maharashtra, including Mumbai, Pune, and Nashik? Look nowhere else! We take pride in being the top supplier of top-notch fermenters for a variety of industries. Our cutting-edge production facilities guarantee precision engineering and compliance with global standards, ensuring optimum performance and durability. We provide a wide choice of solutions catered to meet your individual demands, whether you need fermenters for the production of biofertilizers or enzymes. We are your reliable partner for all of your fermentation needs thanks to our dedication to client satisfaction and effective after-sales service.
Fermenter For Biofertilizer Manufacturing In Mumbai
Biofertilizer Fermenters in Jalgaon, Satara, Solapur, and Akola: Looking for a fermenter in Jalgaon, Satara, Solapur, or Akola to produce biofertilizer? You’ve found it! We specialize in creating excellent fermenters with biofertilizer applications in mind. High-quality biofertilizers are produced as a result of the efficient fermentation processes ensured by our cutting-edge technology and knowledge. You can anticipate effective operation and simple maintenance thanks to the sturdy structure and convenient features of our fermenters. You may depend on us to meet your needs for dependable and effective biofertilizer production in Jalgaon, Satara, Solapur, Akola, and other locations.
Bioreactor Manufacturers in Mumbai
Industrial fermenters are containers that are used to speed up the fermentation process. Microorganisms, such as bacteria, yeast, or fungi, convert complex organic chemicals into simpler ones through the process of fermentation. The raw ingredients are consumed by the microbes, who then transform them into energy, waste, and the required end product.
Bioreactor For Enzymes Production
Pharmaceutical businesses in Mumbai employ commercial fermenters to make antibiotics, vaccines, and other medications. For instance, the pharmaceutical company Lupin, based in Mumbai, employs commercial fermenters to make cephalosporin antibiotics. The manufacturing of vitamins, amino acids, and other pharmaceutical goods also uses industrial fermenters.
Fermenter For API Manufacturing Plant in Mumbai
Industrial fermenters are used by Mumbai-based businesses in the chemical sector to create organic acids, solvents, and other specialty chemicals. Phthalic anhydride, a substance utilized in the creation of polymers, dyes, and resins, is produced by the Mumbai-based business Atul Ltd. using industrial fermenters. In order to produce the enzymes used in laundry detergents, BASF India Ltd., a different firm situated in Mumbai, uses industrial fermenters.
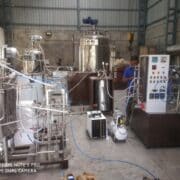
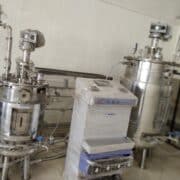
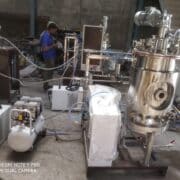
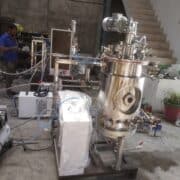
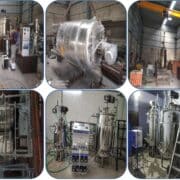
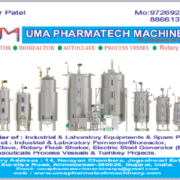
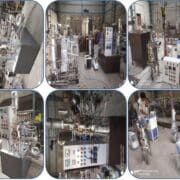
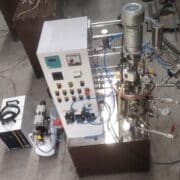
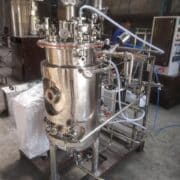
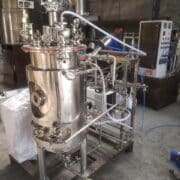
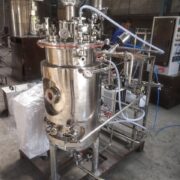
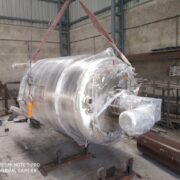
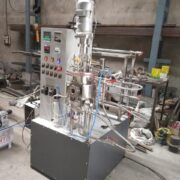

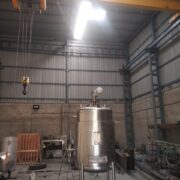
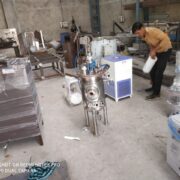
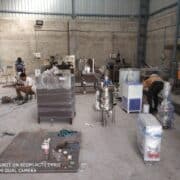
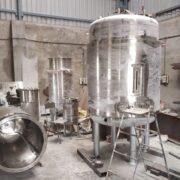
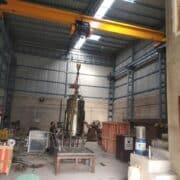
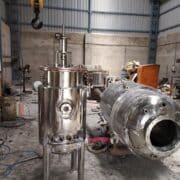
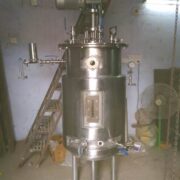
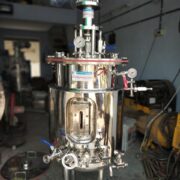
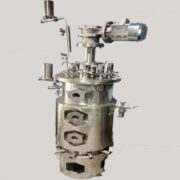
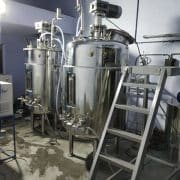
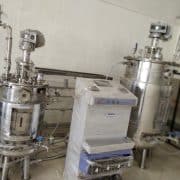
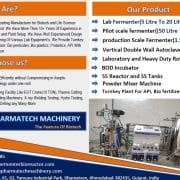
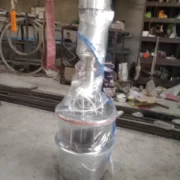
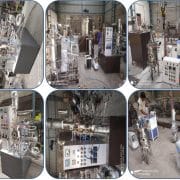
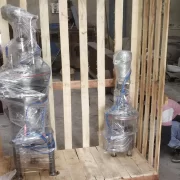
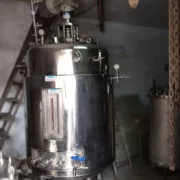
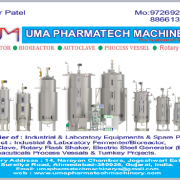
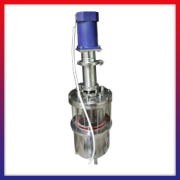
Description | Economic | Basic | Advance | Pro |
---|---|---|---|---|
Fermenter With Utility | ||||
Steam Boiler | No | No | Yes | Yes |
Chiller | No | No | Yes | Yes |
Compressor | Yes | Yes | Yes | Yes |
Probe | ||||
Temperature Sensor (Pt-100) | Yes | Yes | Yes | Yes |
Online pH Measurement | No | Yes | Yes | Yes |
pH Control With 2 Nos Peristaltic Pump | No | No | Yes | Yes |
DO Sensor With 3 Meter Cable and Transmitter | No | No | Optional | Yes |
DO Control | No | No | No | Yes |
Load Cell | No | No | No | Yes |
Control | ||||
Controlling Processor | Microprocessor | PLC Based Without Data Logging | PLC With Data Logging Facility (Touch Screen 4" HMI) | PLC With Data Logging Facility (Touch Screen 7" HMI) |
Scada | No | No | No | Yes |
Inbuilt Heater in Vessel (Suitable For Biofertilizer Production) | Optional | Yes | No | No |
Agitation Control | No | Yes | Yes | Yes |
Automatic Media Sterilization | No | Yes | Yes | Yes |
Auto Filter Sterilization | No | No | No | Yes |
Process Temperature Control | Yes | Up To Atmospheric | Yes | Yes |
Aeration Control By Rotameter | Yes | Yes | Yes | Yes |
Pressure Control | Yes | Yes | Yes | Yes |
Dual Exhaust Filter | No | No | No | Yes |
Spray Ball | Optional | Optional | Optional | Yes |
Feed Control Peristaltic Pump | No | No | No | Yes |
Antifoam Control Peristaltic Pump | No | No | No | Yes |
Description | Economic | Basic | Advance | Pro |
---|---|---|---|---|
Fermenter With Utility | ||||
Steam Boiler | No | No | Yes | Yes |
Chiller | No | No | Yes | Yes |
Compressor | Yes | Yes | Yes | Yes |
Probe | ||||
Temperature Sensor (Pt-100) | Yes | Yes | Yes | Yes |
Online pH Measurement | No | Yes | Yes | Yes |
pH Control With 2 Nos Peristaltic Pump | No | No | Yes | Yes |
DO Sensor With 3 Meter Cable and Transmitter | No | No | Optional | Yes |
DO Control | No | No | No | Yes |
Load Cell | No | No | No | Yes |
Control | ||||
Controlling Processor | Microprocessor | PLC Based Without Data Logging | PLC With Data Logging Facility (Touch Screen 4" HMI) | PLC With Data Logging Facility (Touch Screen 7" HMI) |
Scada | No | No | No | Yes |
Inbuilt Heater in Vessel (Suitable For Biofertilizer Production) | Optional | Yes | No | No |
Agitation Control | No | Yes | Yes | Yes |
Automatic Media Sterilization | No | Yes | Yes | Yes |
Auto Filter Sterilization | No | No | No | Yes |
Process Temperature Control | Yes | Up To Atmospheric | Yes | Yes |
Aeration Control By Rotameter | Yes | Yes | Yes | Yes |
Pressure Control | Yes | Yes | Yes | Yes |
Dual Exhaust Filter | No | No | No | Yes |
Spray Ball | Optional | Optional | Optional | Yes |
Feed Control Peristaltic Pump | No | No | No | Yes |
Antifoam Control Peristaltic Pump | No | No | No | Yes |
Top Industrial Fermenter Manufacturers in Mumbai - इंडस्ट्रियल फेरमेंटर मनुफक्चरर्स, मुंबई near me - Justdial
Mumbai, a bustling metropolis, is home to numerous industrial fermenter manufacturers. For businesses seeking https://www.inaxorio.com/6tw6fmq0d industrial fermenter manufacturers in Mumbai, platforms like Justdial provide a comprehensive list of reliable manufacturers. With the capability to find https://ict-pulse.com/2024/07/mxrs7mu Heat Exchanger Manufacturers, https://autismwish.org/pzionb4vq9 Medical Equipment Manufacturers, https://thefooduntold.com/food-science/h480qjf0 Laboratory Equipment Manufacturers, https://bxscco.com/ago4psz0cf1 Chemical Manufacturers, and https://www.adroitprojectconsultants.com/2024/07/25/p24kysadhe Machinery Manufacturers in Mumbai, Justdial serves as a one-stop resource for locating top suppliers in the region. Here, we highlight some of the most reputable manufacturers in the field.
Airlift Bioreactor
UPM’s https://www.insearchofsukoon.com/baad71lg0 airlift bioreactors are designed for processes that require gentle mixing and aeration. These bioreactors are ideal for the cultivation of shear-sensitive organisms.
Fermenter Vessel India
UPM is a leading manufacturer of https://gsaudemarketing.com.br/pw47ei3ka9 fermenter vessels in India. Their fermenter vessels are constructed from high-quality materials and are designed to provide reliable and efficient fermentation processes.
Small Scale Bioreactor
UPM’s source small scale bioreactors are perfect for laboratory and pilot-scale studies. These bioreactors offer precise control over fermentation conditions, ensuring accurate and reliable results.
Bioreactor Cost
UPM offers competitive 100Mg Tramadol Online bioreactor costs, providing high-quality bioreactors at affordable prices. Their bioreactors are designed to offer high performance and reliability, making them a cost-effective choice for various industries.
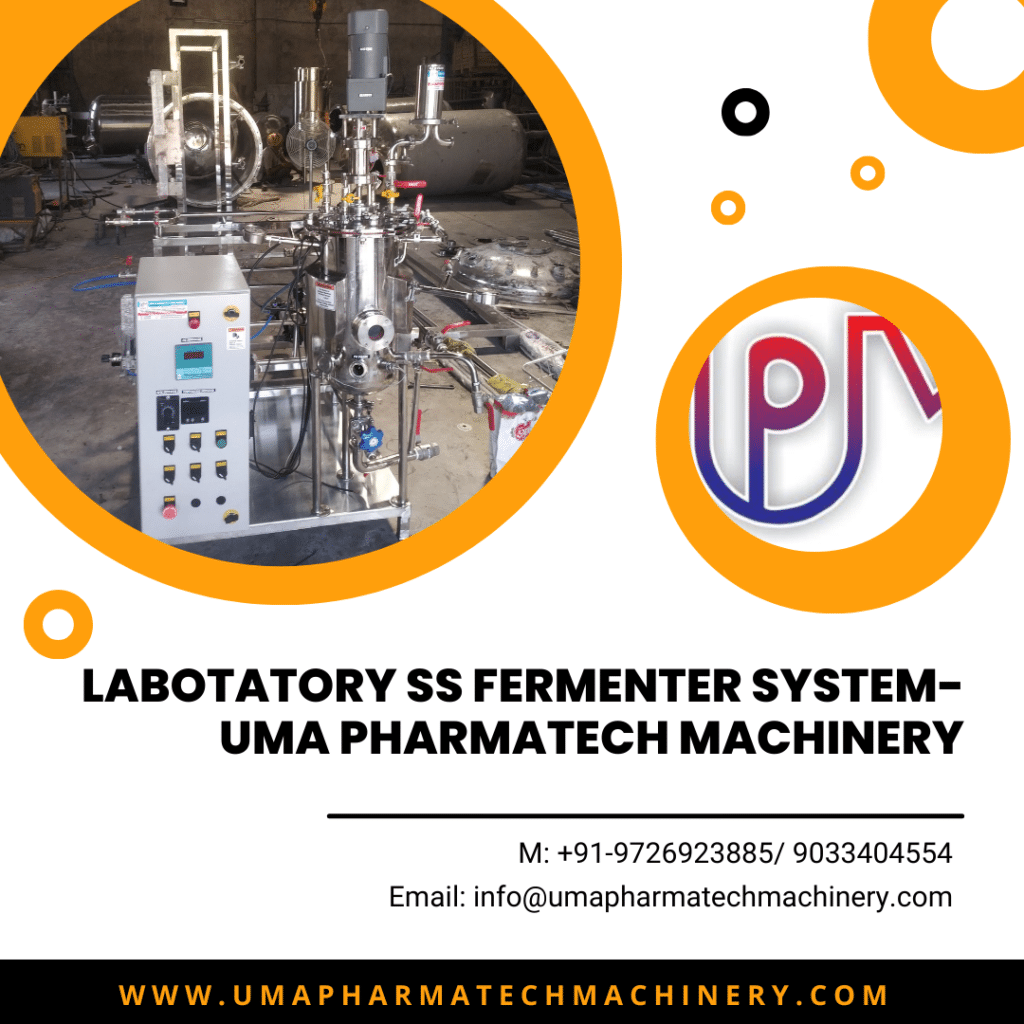
Popular Industrial Fermenter Manufacturers in Mumbai
Mumbai hosts several prominent https://www.pathwaysmagazineonline.com/9lggbszkb industrial fermenter manufacturers who cater to various industries, including pharmaceuticals, biotechnology, and biofuels. These manufacturers provide a wide range of fermenters, from small-scale laboratory models to large industrial units. The https://autismwish.org/mfyenjvs7 industrial fermenter in Mumbai, also known as औद्योगिक किण्वन, मुंबई, Maharashtra, is renowned for its high quality and advanced features.
Industrial & Laboratory Fermenter – Lab Scale Fermenter Manufacturer from Mumbai
UPM is a leading manufacturer of https://bxscco.com/r53u47j9x1 Industrial & Laboratory Fermenter. Their follow Lab Scale Fermenter is designed for research and small-scale production, offering precise control over fermentation conditions.
Stainless Steel Fermenter
UPM’s follow link Stainless Steel Fermenter is known for its durability and resistance to corrosion. These fermenters are ideal for various industrial applications requiring robust and reliable equipment.
Stainless Steel Industrial Fermenter
The source Stainless Steel Industrial Fermenter from UPM is designed for large-scale production. These fermenters offer advanced features and are constructed from high-grade stainless steel.
Business Listings of Industrial Fermenter, Industrial Bioreactor Manufacturers, Suppliers, and Exporters in Mumbai
Business listings for source site industrial fermenter and Tramadol Online Cod industrial bioreactor manufacturers in Mumbai provide essential details such as contact information, addresses, and product specifications. This information helps businesses make informed decisions when purchasing fermentation equipment. Companies like https://ict-pulse.com/2024/07/t89563of Uma Pharmatech Machinery (UPM) in Mumbai offer a wide range of products tailored to meet the needs of various industries.
Fermenter Manufacturer in Mumbai By Uma Pharmatech
UPM is a leading https://geneticsandfertility.com/ko4h6vb7 fermenter manufacturer in Mumbai. Their products are known for their high quality and advanced features, catering to the needs of various industries in the region.
Industrial Fermenter in Mumbai – Steel Fabricators Vasai
UPM’s Tramadol Ordering industrial fermenters are also available through steel fabricators in Vasai, Mumbai. These fabricators ensure that UPM’s high-quality fermenters are accessible to businesses across the region.
SS Industrial Fermenter Bioreactor 5KL to 50KL Hydrabad, Capacity: 5-50 L
Uma Pharmatech Machinery offers the go site SS Industrial Fermenter Bioreactor with capacities ranging from 5KL to 50KL. These fermenters are constructed from high-quality stainless steel, ensuring durability and corrosion resistance. They are ideal for large-scale production in sectors such as pharmaceuticals and biotechnology.
Fermenter Project – Fermenter Production Enzyme Plant Manufacturer from Ahmedabad
In addition to their offerings in Mumbai, UPM also manufactures source fermenter production enzyme plants in Ahmedabad. These plants are designed to facilitate large-scale enzyme production through fermentation, making them ideal for industries involved in biotechnology and pharmaceuticals. UPM’s enzyme plants are known for their efficiency and advanced technology, ensuring high productivity and quality.
Bio Pharma Production Plant
UPM’s enter site bio pharma production plants are engineered to meet the rigorous standards of the pharmaceutical industry. These plants are equipped with state-of-the-art fermenters and bioreactors, ensuring precise control over the fermentation process and resulting in high-quality biopharmaceutical products.
Primary Metabolism Production Plant
For industries involved in the production of primary metabolites, UPM offers specialized follow link primary metabolism production plants. These plants are designed to optimize the fermentation conditions for producing various primary metabolites, ensuring high yield and quality.
Production Scale Fermenter
The https://www.inaxorio.com/oze90dm2 production scale fermenter offered by UPM is designed to handle high-volume fermentation processes. These fermenters are equipped with advanced control systems to ensure optimal fermentation conditions, making them suitable for large-scale industrial applications.
Industrial Fermenter Delhi
In addition to Mumbai, UPM also supplies https://www.adroitprojectconsultants.com/2024/07/25/zk407bxeww industrial fermenters to Delhi. These fermenters are designed to meet the specific requirements of various industries, ensuring high productivity and efficiency.
Glass Fermenter Bioreactor
The glass fermenter bioreactor from UPM is designed for laboratory applications. These bioreactors provide excellent visibility and precise control over the fermentation process.
Algae Glass Bio Reactor
UPM’s algae glass bio reactors are designed for the cultivation of algae. These bioreactors provide the necessary conditions for optimal algae growth and productivity.
Benchtop Glass Bioreactor
The benchtop glass bioreactor from UPM is ideal for small-scale experiments and research studies. These bioreactors offer precise control over fermentation conditions, ensuring accurate and reliable results.
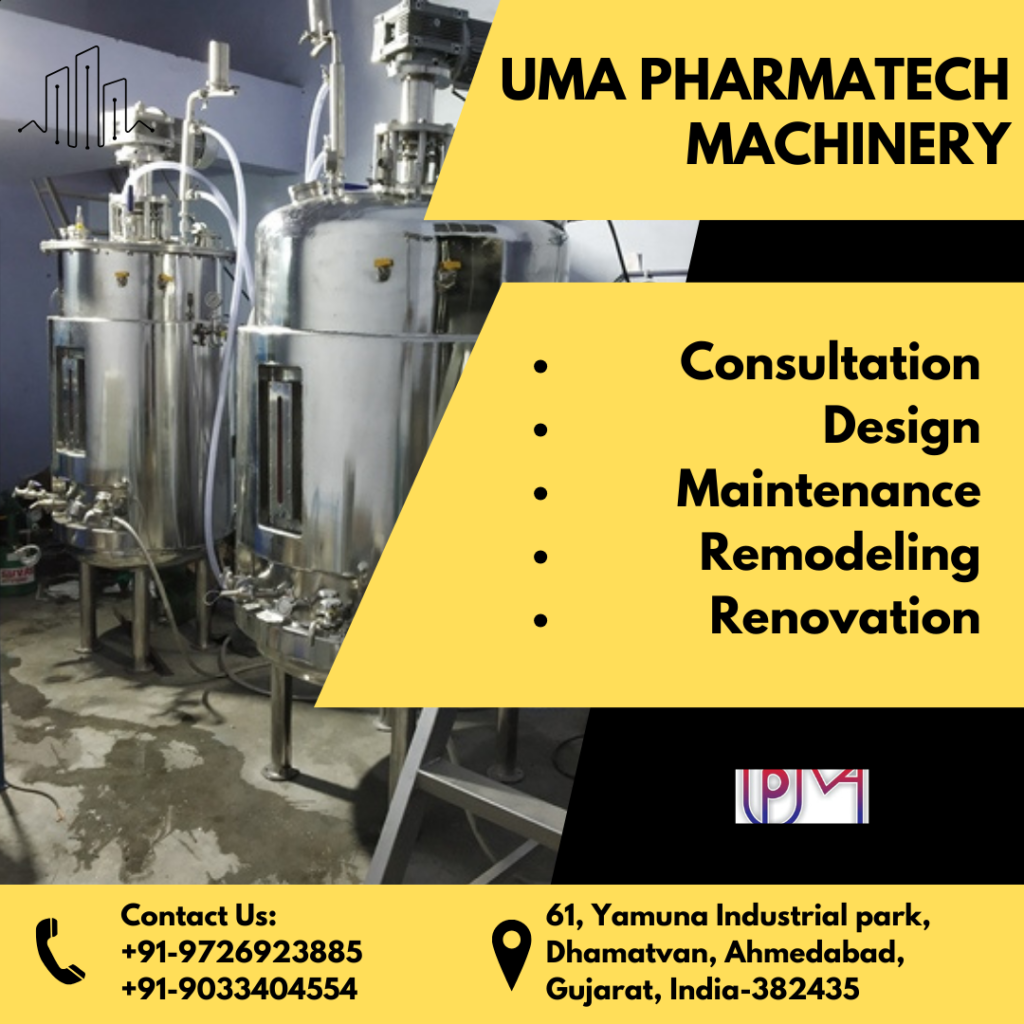
FERMENTOR-200L-2024, SS Bio Fermenter, Size: Standard, Capacity: 5000
UPM’s FERMENTOR-200L-2024 is a compact fermenter with a capacity of 500 liters. Its small footprint makes it ideal for facilities with limited space, while still providing the advanced features required for efficient fermentation processes.
The SS Bio Fermenter from UPM, with a standard size and capacity of 5000 liters, is perfect for large-scale fermentation. Constructed from high-grade stainless steel, these fermenters ensure durability and resistance to chemical corrosion.
Glass Autoclavable Lab Scale Bioreactors
UPM’s glass autoclavable lab scale bioreactors are designed for ease of use and sterilization. These bioreactors are perfect for laboratory applications where maintaining sterile conditions is crucial.
Laboratory Scale Bioreactor System
UPM offers a range of laboratory scale bioreactor systems designed for research and development. These systems provide precise control over fermentation conditions, making them ideal for laboratory settings.
Bioreactor Fermentor – Clean In Place
UPM’s bioreactor fermentors are equipped with clean-in-place (CIP) systems, ensuring easy cleaning and maintenance. These fermentors are designed to provide high performance and reliability.
Cell Cultural Production Plant
UPM manufactures cell cultural production plants designed for the large-scale cultivation of mammalian cells. These plants are equipped with advanced bioreactors that ensure optimal cell growth and productivity.
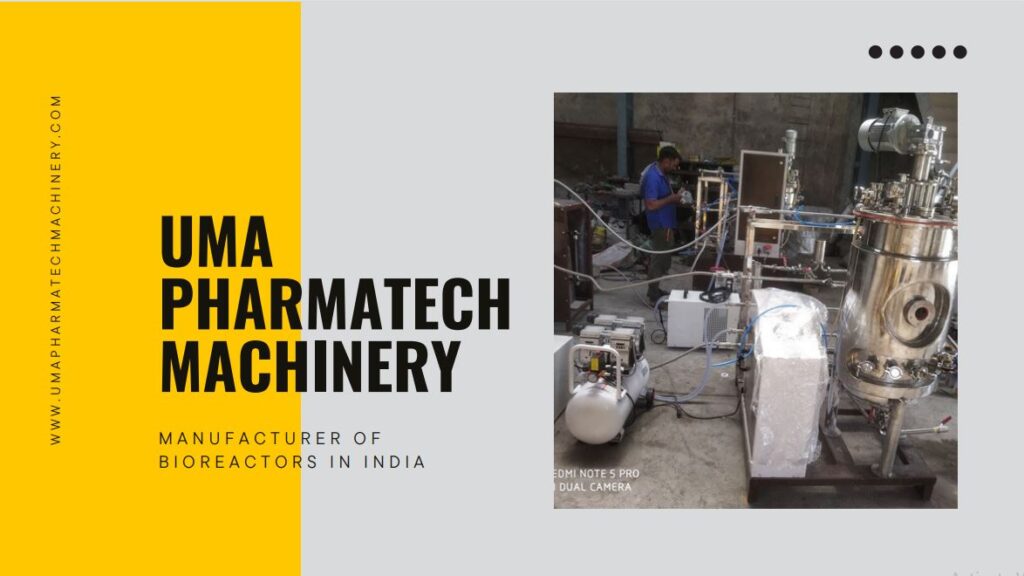
Conical Fermenters
Conical fermenters are designed for easy yeast harvesting and sediment removal. UPM offers a range of conical fermenters that are ideal for brewing and other fermentation processes requiring efficient solid-liquid separation.
Bio Fertilizer Plant
UPM’s bio fertilizer plants are designed to produce high-quality bio fertilizers through fermentation. These plants are equipped with advanced fermenters that ensure optimal conditions for microbial growth and activity, resulting in effective and sustainable bio fertilizers.
Fermenter Production Enzyme Plant
The fermenter production enzyme plant by UPM is another key offering, designed to produce enzymes on an industrial scale. These plants use advanced fermentation technology to ensure high enzyme yield and quality, catering to various industrial applications.
Bio Pesticide Production Plant
UPM also manufactures bio pesticide production plants. These plants use fermentation technology to produce effective bio pesticides, providing a sustainable and environmentally friendly alternative to chemical pesticides.
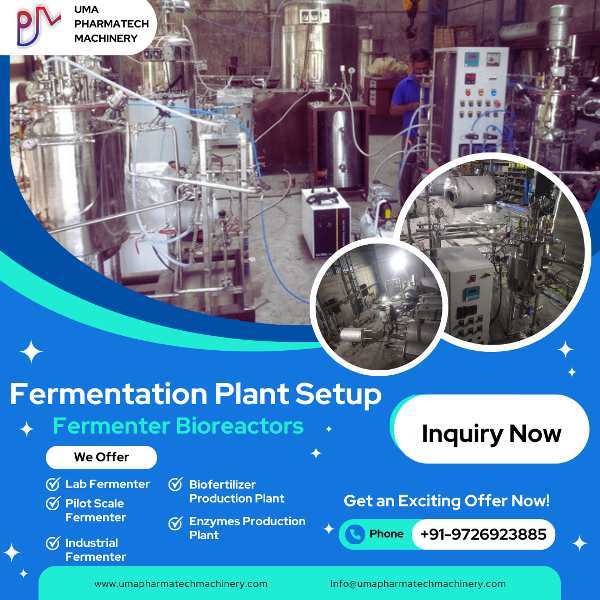
Enzyme Development By Fermentation Techniques, Packaging Type: Liquid Enzymes In Bottles
UPM specializes in enzyme development by fermentation techniques. These enzymes, packaged in liquid form in bottles, are essential for various industrial applications, including food processing, pharmaceuticals, and biofuels.
Gray Bio Reactor Fermenter, Capacity: 3L To 10L
The Gray Bio Reactor Fermenter offered by UPM is available in capacities ranging from 3L to 10L. These fermenters are designed for small-scale applications and research purposes, providing precise control over fermentation conditions.
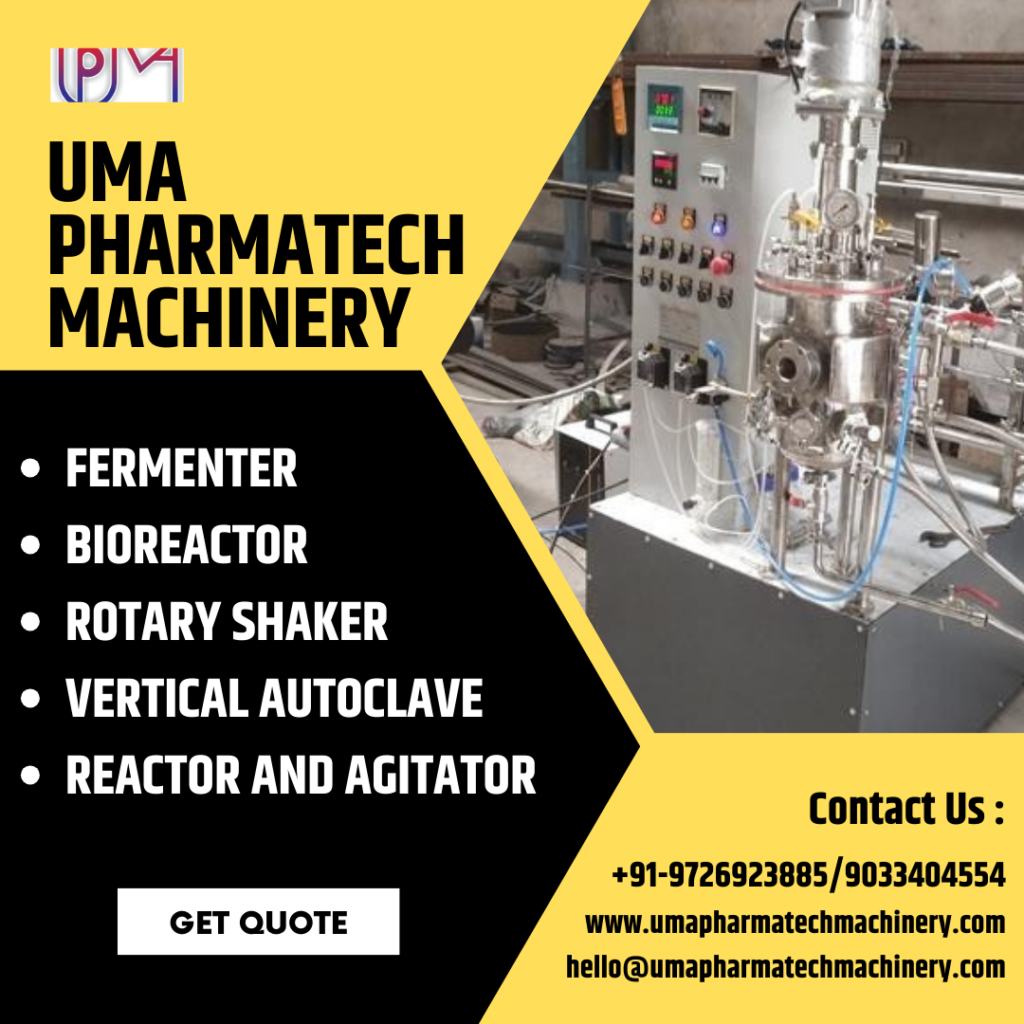
Multiuse and Industrial Bioreactors
UPM manufactures multiuse and industrial bioreactors suitable for a variety of applications. These bioreactors are versatile and can be used for different types of fermentation processes, making them a valuable asset for any biotechnology or pharmaceutical facility.
Industrial Fermenter, Capacity: 50 Litre/Hour
The industrial fermenter with a capacity of 50 liters per hour is designed for continuous fermentation processes. This type of fermenter is ideal for industries requiring a constant flow of culture medium, ensuring high productivity and efficiency.
Industrial Fermenter PMI, Capacity: 50Ltr
UPM’s Industrial Fermenter PMI with a capacity of 50 liters is designed for small to medium-scale production. These fermenters are equipped with advanced control systems to ensure precise monitoring and control of fermentation conditions.
Industrial Fermenter Or Bioreactor, Size: 100 L To 1000 L, Capacity: 500 Liters
The Industrial Fermenter or Bioreactor from UPM is available in sizes ranging from 100 liters to 1000 liters, with a capacity of 500 liters. These fermenters are designed for versatility and can be used in various industrial applications.
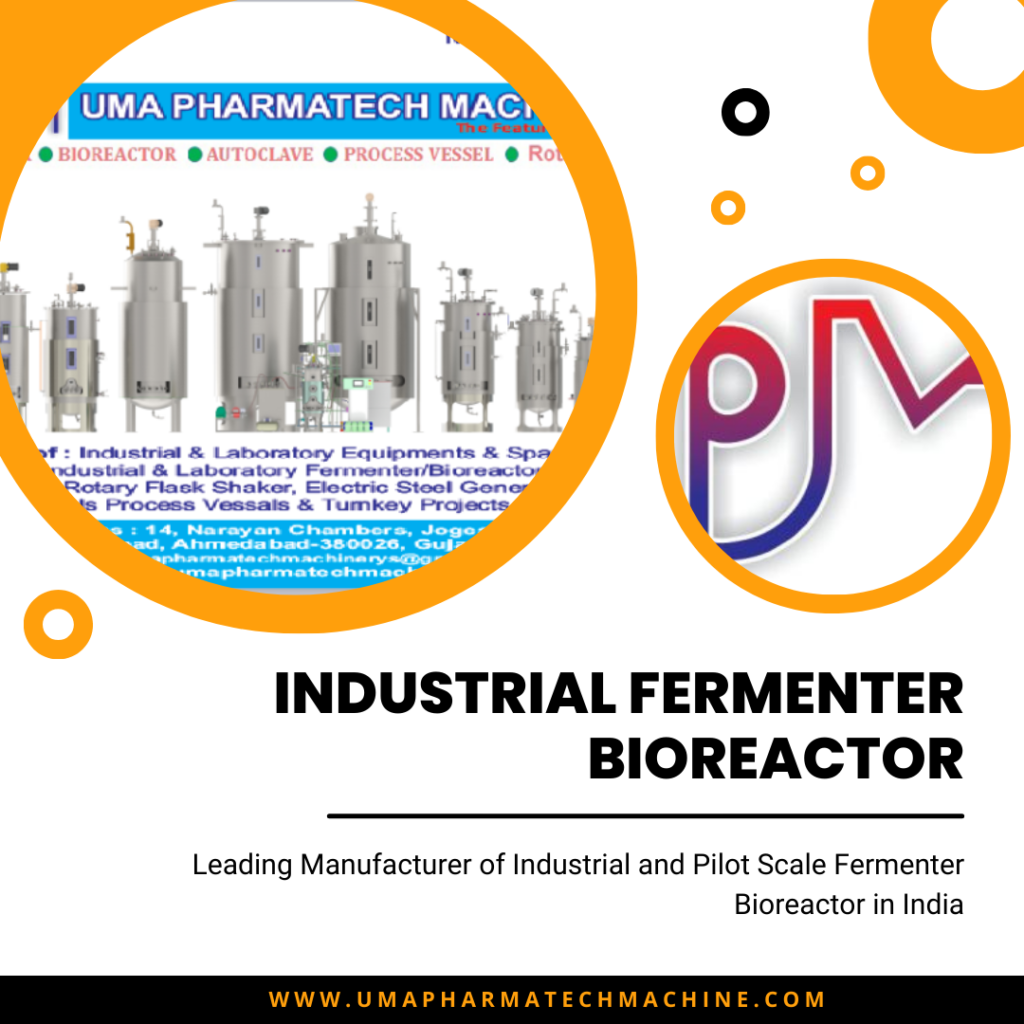
Gas Liquid Fermenter
UPM’s Gas Liquid Fermenter is designed for processes involving gas-liquid interactions. These fermenters ensure efficient mixing and mass transfer, making them suitable for various biotechnological applications.
Microbial Fermenter Production Plant
For the production of microbial products, UPM offers microbial fermenter production plants. These plants are equipped with advanced fermenters that ensure optimal growth conditions for various microorganisms, resulting in high-quality microbial products.
Bioreactor Companies in Mumbai
UPM is one of the top bioreactor companies in Mumbai. Their bioreactors are known for their advanced features and reliability, making them a preferred choice for many industries in the region. UPM’s bioreactors are designed for various applications, from research to large-scale production.
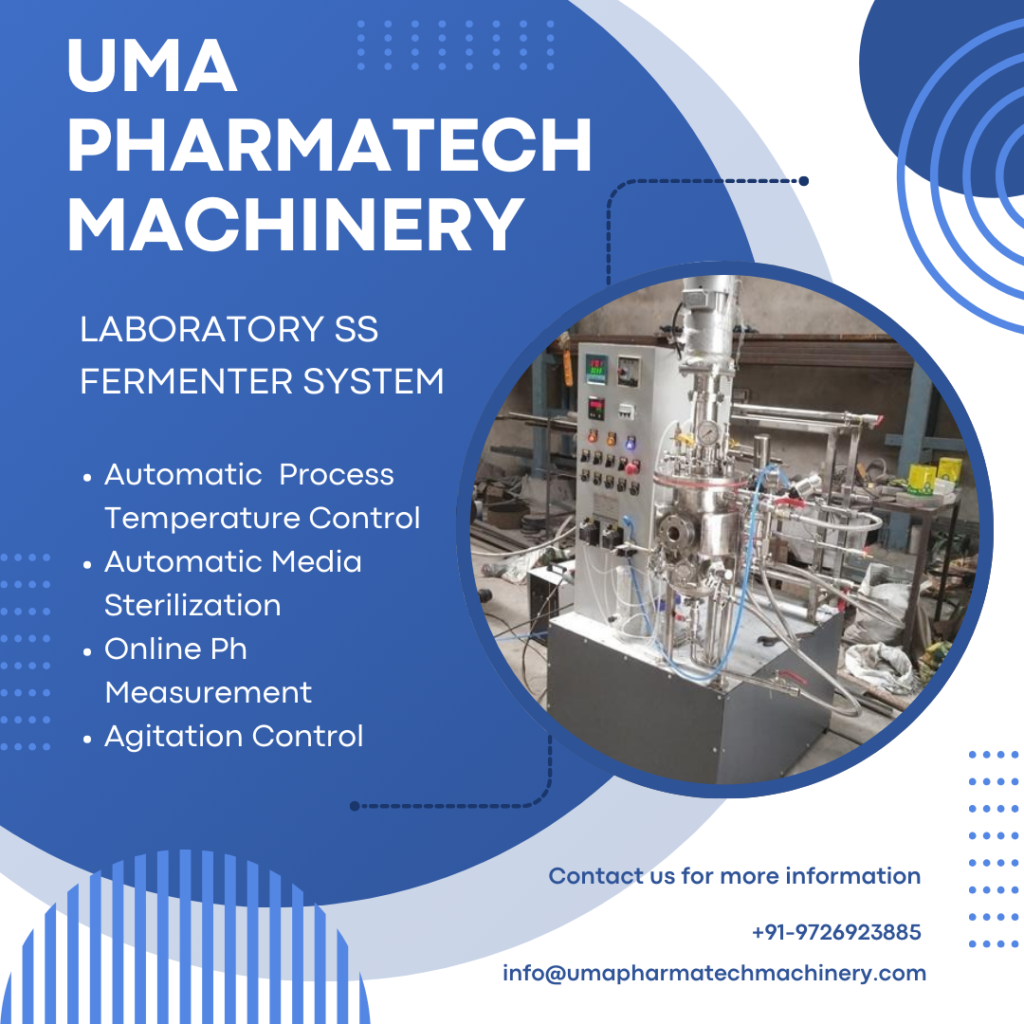
SS 316 Stainless Steel Fermenter
The SS 316 Stainless Steel Fermenter from UPM is known for its high durability and resistance to corrosion. These fermenters are ideal for industries that require robust and reliable fermentation equipment.
Benchtop Fermentors/ Industrial Fermenter
Benchtop fermentors from UPM are designed for research and small-scale production. These fermenters offer precise control over fermentation conditions, making them ideal for laboratory use.
Multiuse and Industrial Bioreactors
UPM’s multiuse and industrial bioreactors are versatile and can be used for a wide range of fermentation processes. These bioreactors are built to handle different types of cultures and provide precise control over the fermentation conditions.
Jacketed Bioreactor
The jacketed bioreactor from UPM is designed to maintain optimal temperature conditions during fermentation. The jacketed design allows for efficient heat transfer, ensuring that the fermentation process is maintained at the desired temperature.
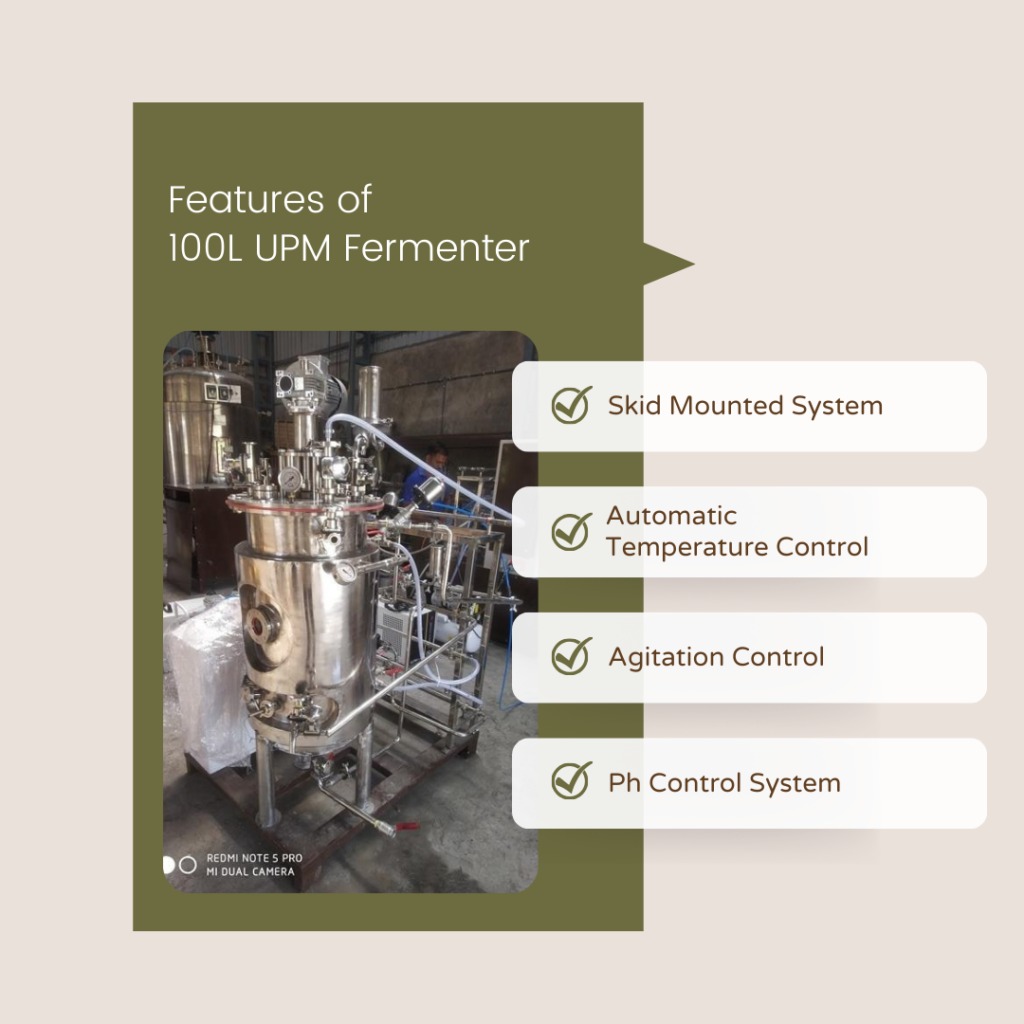
Wine Fermentation Vessel
UPM offers wine fermentation vessels that are designed specifically for the wine-making process. These vessels ensure optimal conditions for fermenting grape must into wine, preserving the desired flavors and aromas.
Bio Fermentor, Size: Lab, Capacity: 1 Liter – 100 Liter
The Bio Fermentor from UPM, available in lab sizes with capacities ranging from 1 liter to 100 liters, is ideal for research and small-scale production. These fermentors offer precise control over fermentation parameters.
Autoclavable Bioreactor
The autoclavable bioreactor from UPM is designed for laboratory applications where sterilization is crucial. These bioreactors offer precise control over fermentation conditions, ensuring accurate and reliable results.
Various Lab Bioreactor
UPM offers a variety of lab bioreactors designed for different research and development applications. These bioreactors provide precise control over fermentation conditions, making them ideal for laboratory settings.
Parallel Bioreactor
UPM’s parallel bioreactors are designed for high-throughput experiments. These bioreactors allow for multiple fermentation processes to be run simultaneously, increasing productivity and efficiency.
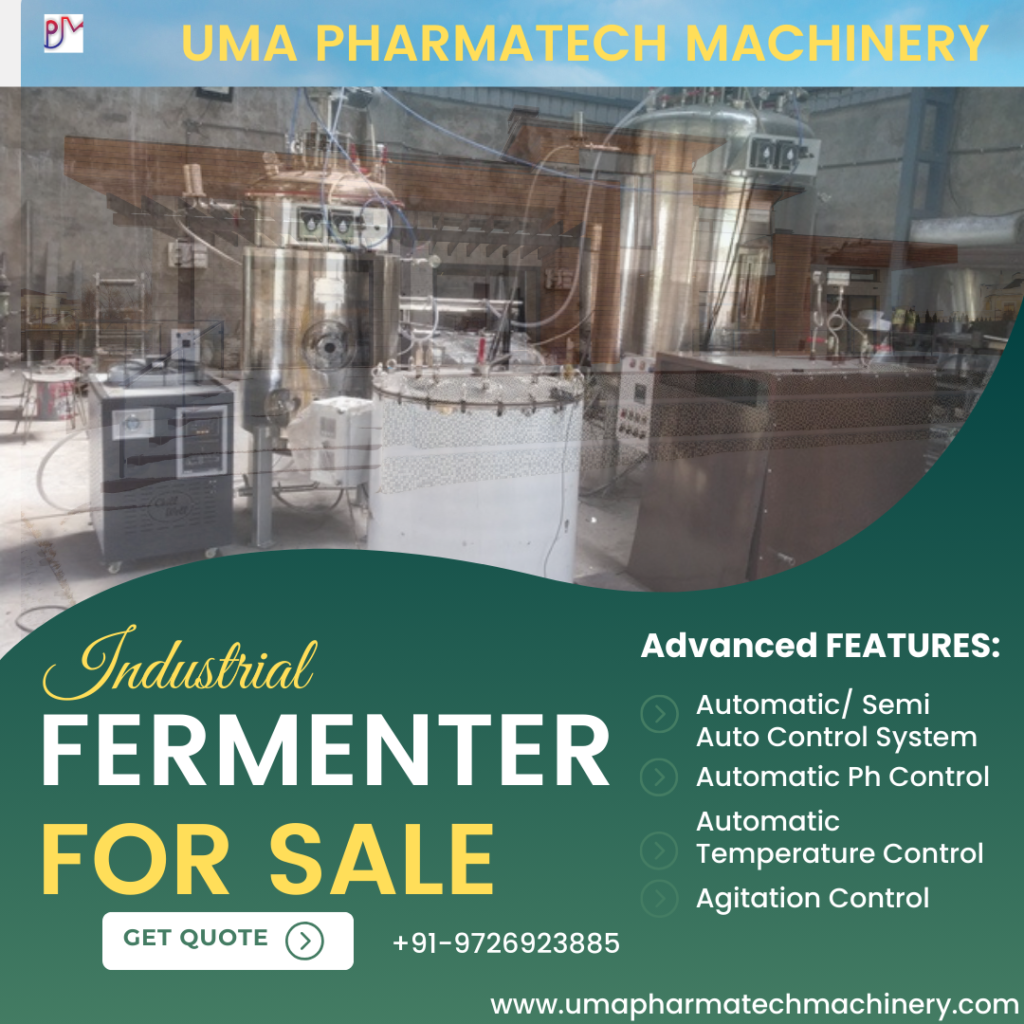
Industrial Production Fermenter
Research Grade Fermentor, Capacity: From 3-10 Litres
UPM’s Research Grade Fermentor is available in capacities from 3 to 10 liters. These fermentors are designed for scientific research, providing accurate and reliable data for various fermentation studies.
Industrial production fermenters from UPM are designed for large-scale manufacturing processes. These fermenters ensure high productivity and efficiency, making them suitable for various industrial applications.
Mini Bioreactor
The mini bioreactor from UPM is perfect for small-scale experiments and pilot studies. These compact bioreactors provide all the features of larger models, ensuring accurate and reliable results.
Cell Cultural Bioreactor
UPM’s cell cultural bioreactors are designed for the cultivation of mammalian cells. These bioreactors provide the necessary conditions for optimal cell growth and productivity.
Microbial Bioreactor
The microbial bioreactors from UPM are designed for the cultivation of microorganisms. These bioreactors provide precise control over fermentation conditions, ensuring optimal growth and productivity.
Production Scale Fermentor, Production Scale Fermentor Manufacturers, Production Scale Fermentor Suppliers, India
UPM is a leading manufacturer and supplier of production scale fermentors in India. Their fermentors are designed for large-scale production, providing high productivity and efficiency. UPM’s production scale fermentors are equipped with advanced control systems, ensuring precise monitoring and control of fermentation conditions.
By focusing on high-quality products and customer satisfaction, Uma Pharmatech Machinery has established itself as a top industrial fermenter manufacturer in Mumbai and beyond. Their extensive range of fermenters and bioreactors, coupled with competitive pricing and advanced features, makes them a preferred choice for businesses in various industries.
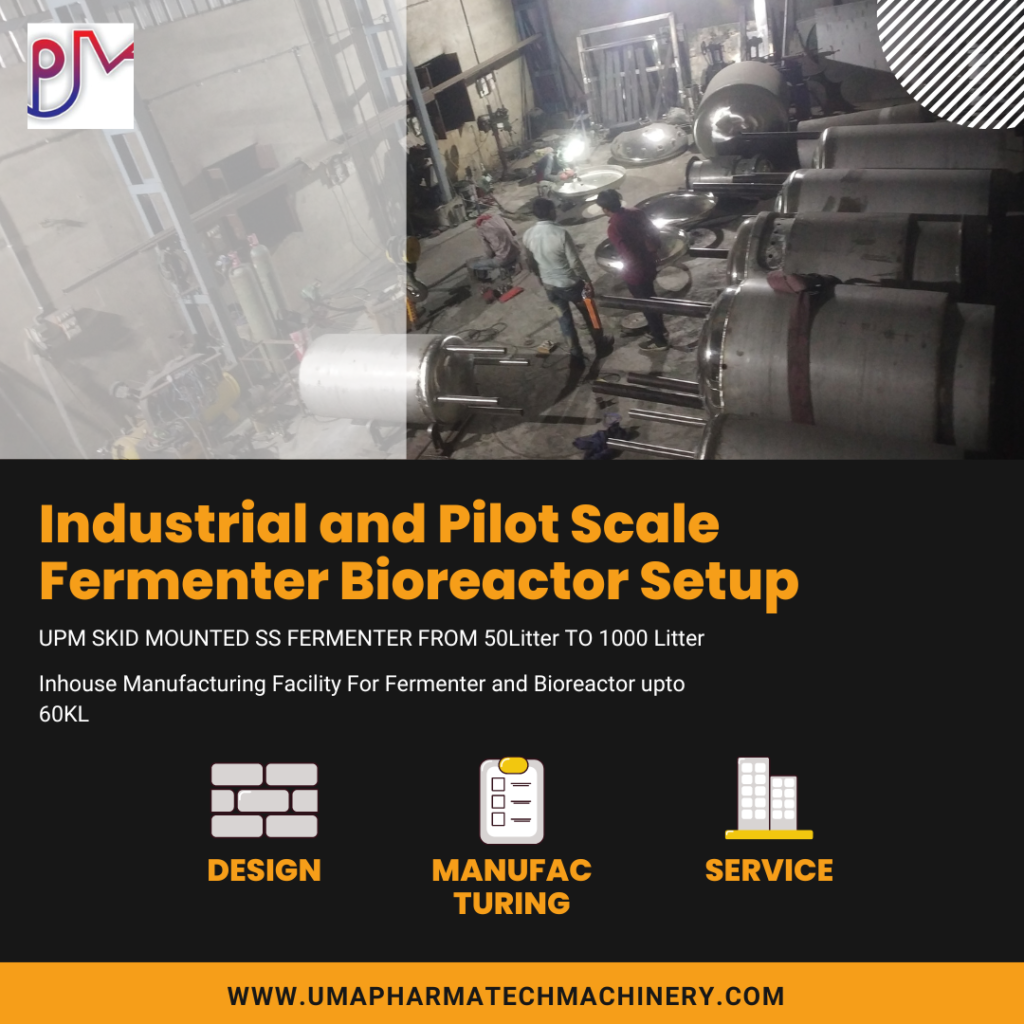
Stainless Steel Bio Fermenter Manufacturer in Mumbai, India
Uma Pharmatech Machinery is a leading Stainless Steel Bio Fermenter Manufacturer in Mumbai, India. Their products are known for their high quality and advanced features, catering to the needs of the biotechnology, pharmaceutical, and biofuel industries.
Bioreactor Price
UPM offers competitive bioreactor prices without compromising on quality. Their bioreactors are designed to provide high performance and reliability, making them a cost-effective choice for various industries.
Lab Scale Bioreactor
For research and development purposes, UPM provides lab scale bioreactors. These bioreactors are designed to offer precise control over the fermentation process, making them ideal for laboratory settings.
Mini Bioreactor
UPM’s mini bioreactors are perfect for small-scale experiments and pilot studies. These compact bioreactors provide all the features of larger models, ensuring accurate and reliable results.
Industrial Bioreactor
The industrial bioreactor range from UPM is designed for large-scale production. These bioreactors are equipped with advanced control systems and are built to handle high-volume fermentation processes.
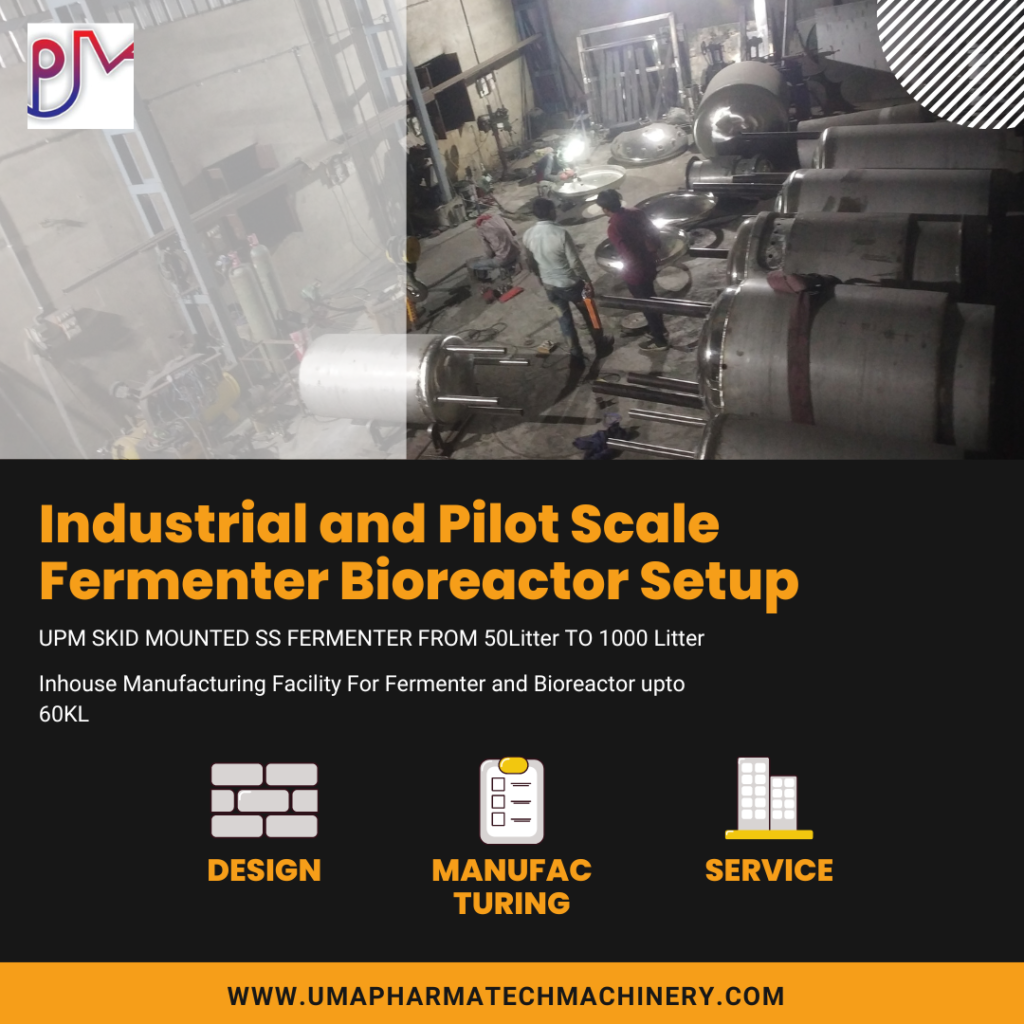
Bio Fermenter, Bioreactor Manufacturer, Exporter
UPM is a renowned bio fermenter and bioreactor manufacturer and exporter. Their products are widely used in various industries around the world, known for their reliability and efficiency.
Suspended Growth Bioreactor
UPM’s suspended growth bioreactors are designed for processes where the microbial culture remains in suspension. These bioreactors provide efficient mixing and aeration, ensuring optimal growth conditions for the culture.
Bioreactor Vessel
The bioreactor vessels from UPM are constructed from high-quality materials to ensure durability and reliability. These vessels are designed to withstand the rigors of industrial fermentation processes.
Fermenter Supplier
UPM is a leading fermenter supplier in Mumbai, providing a wide range of fermenters to meet the needs of various industries. Their products are known for their high quality and advanced features, making them a preferred choice for many businesses.
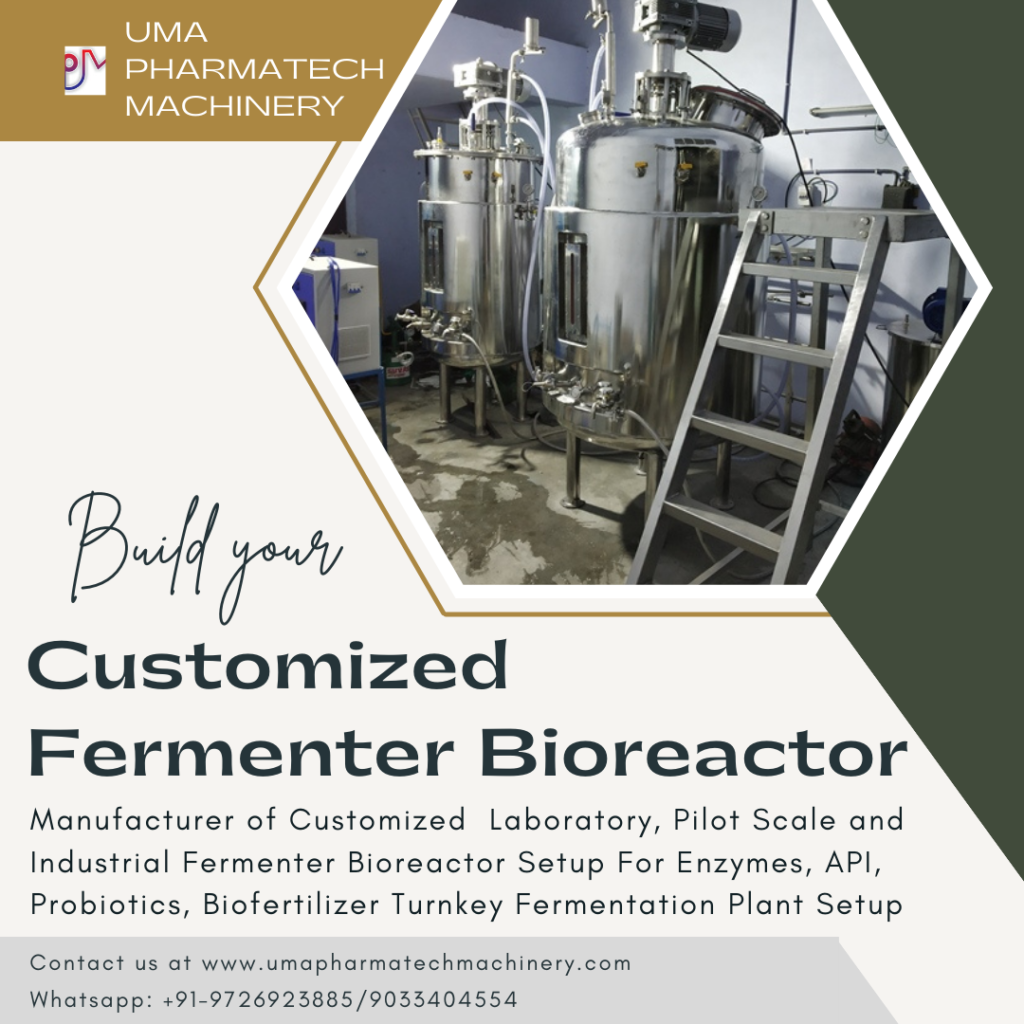
Bench Top Autoclavable Fermentors Manufacturer, Exporter
UPM manufactures and exports bench top autoclavable fermentors. These fermentors are designed for ease of use and are ideal for laboratory applications where sterilization is crucial.
Lab Scale Bioreactor
UPM’s lab scale bioreactors are ideal for research and development applications. These bioreactors offer precise control over fermentation conditions, ensuring accurate and reproducible results.
Fermentor and Bioreactor
UPM manufactures both fermentors and bioreactors, providing solutions for a wide range of fermentation applications. Their products are designed to offer high performance and reliability, making them suitable for various industries.
Cell Culture Bioreactor
The cell culture bioreactors from UPM are designed for the cultivation of mammalian cells. These bioreactors provide the necessary conditions for optimal cell growth and productivity.
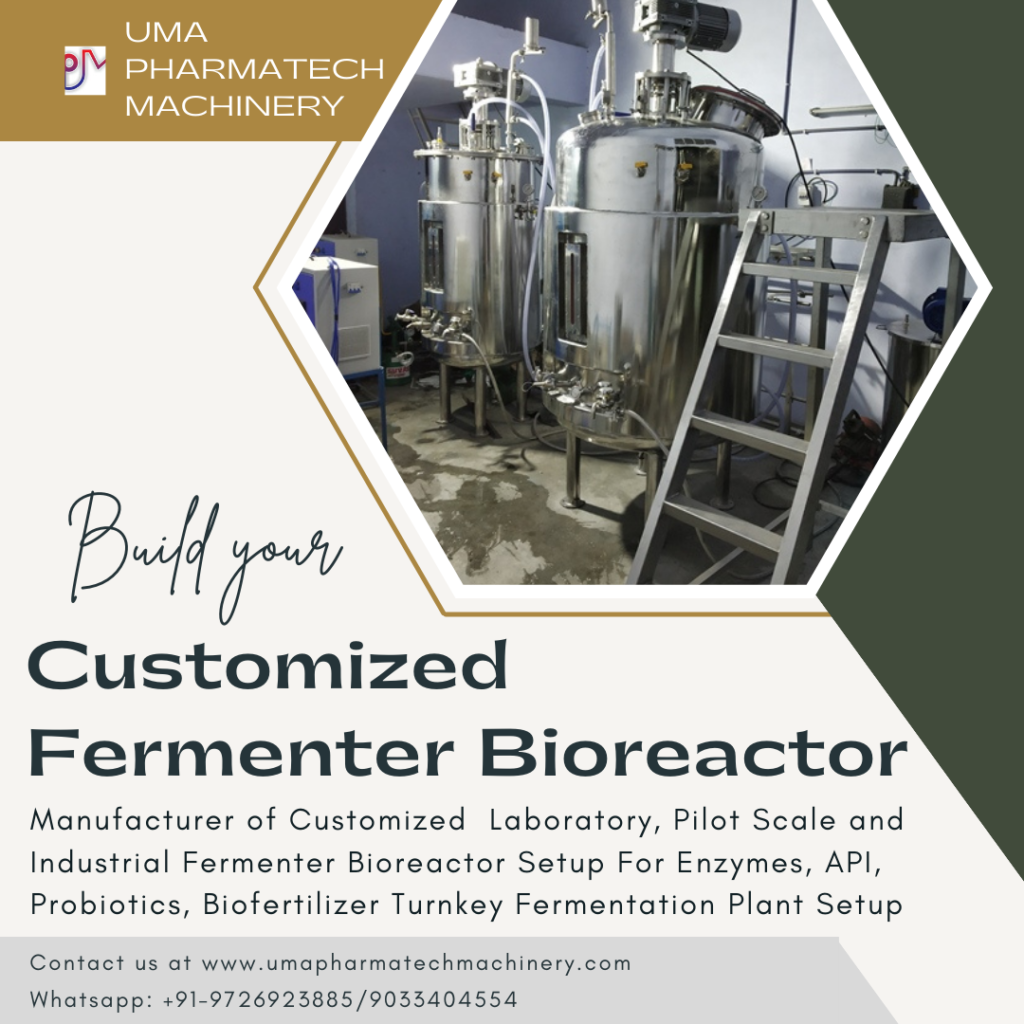
Salient Features of our Fermenter
The salient features of UPM’s fermenters include high durability, precise control systems, and versatility. These features make their fermenters suitable for a wide range of applications in various industries.
Popular Location in Mumbai – Maharashtra
UPM’s fermenters are widely used in various locations across Mumbai and Maharashtra. Their products are trusted by many industries for their quality and performance.
Fermentation Equipment – Pudducherry, Model: UPM-100I Manufacturer from Mohali
The Fermentation Equipment from UPM, Model: UPM-100I, is designed for various industrial applications. These fermenters are manufactured in Mohali and are known for their reliability and efficiency.
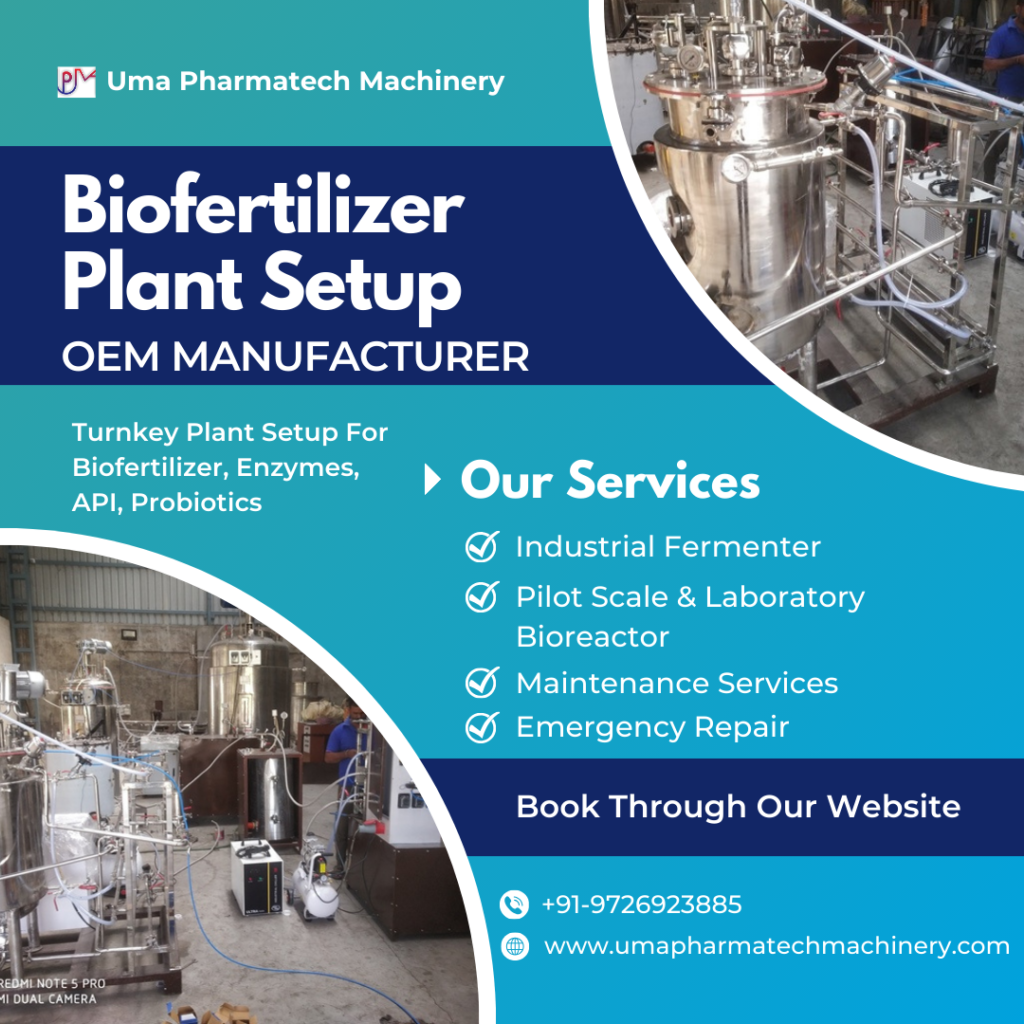
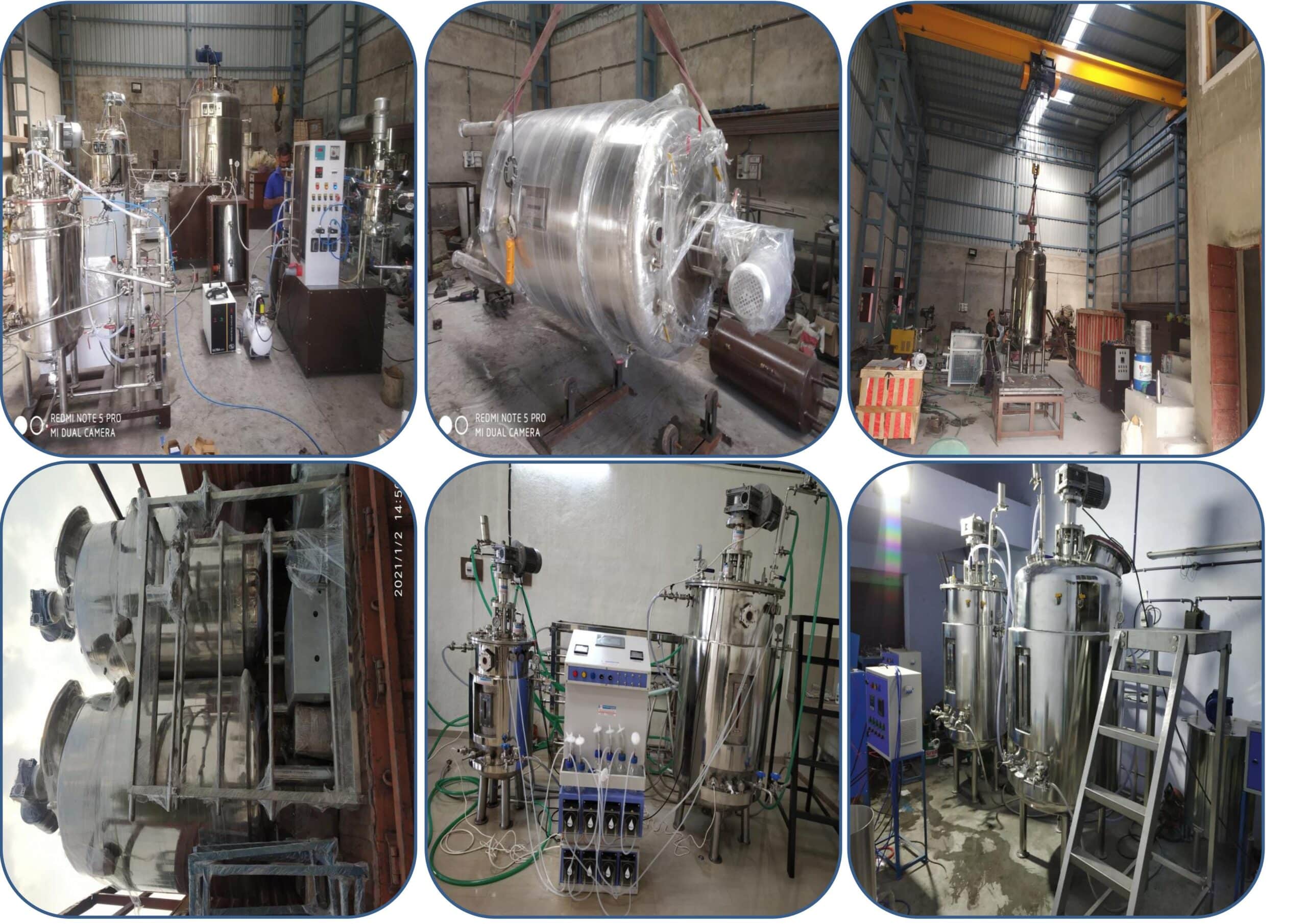
Manufacturer of Fermenter in Mumbai- Maharashtra
Andhra Pradesh, Arunachal Pradesh, Assam, Bihar, Chhattisgarh, Goa, Gujarat, Haryana, Himachal Pradesh, Jharkhand, Karnataka, Kerala, Madhya Pradesh, Maharashtra, Manipur, Meghalaya, Mizoram, Nagaland, Odisha, Punjab, Rajasthan, Sikkim, Tamil Nadu, Telangana, Tripura, Uttar Pradesh, Uttarakhand, West Bengal
Top 10 States for Agriculture:
- Punjab
- Haryana
- Madhya Pradesh
- Uttar Pradesh
- Rajasthan
- Gujarat
- Maharashtra
- Andhra Pradesh
- Telangana
- Karnataka
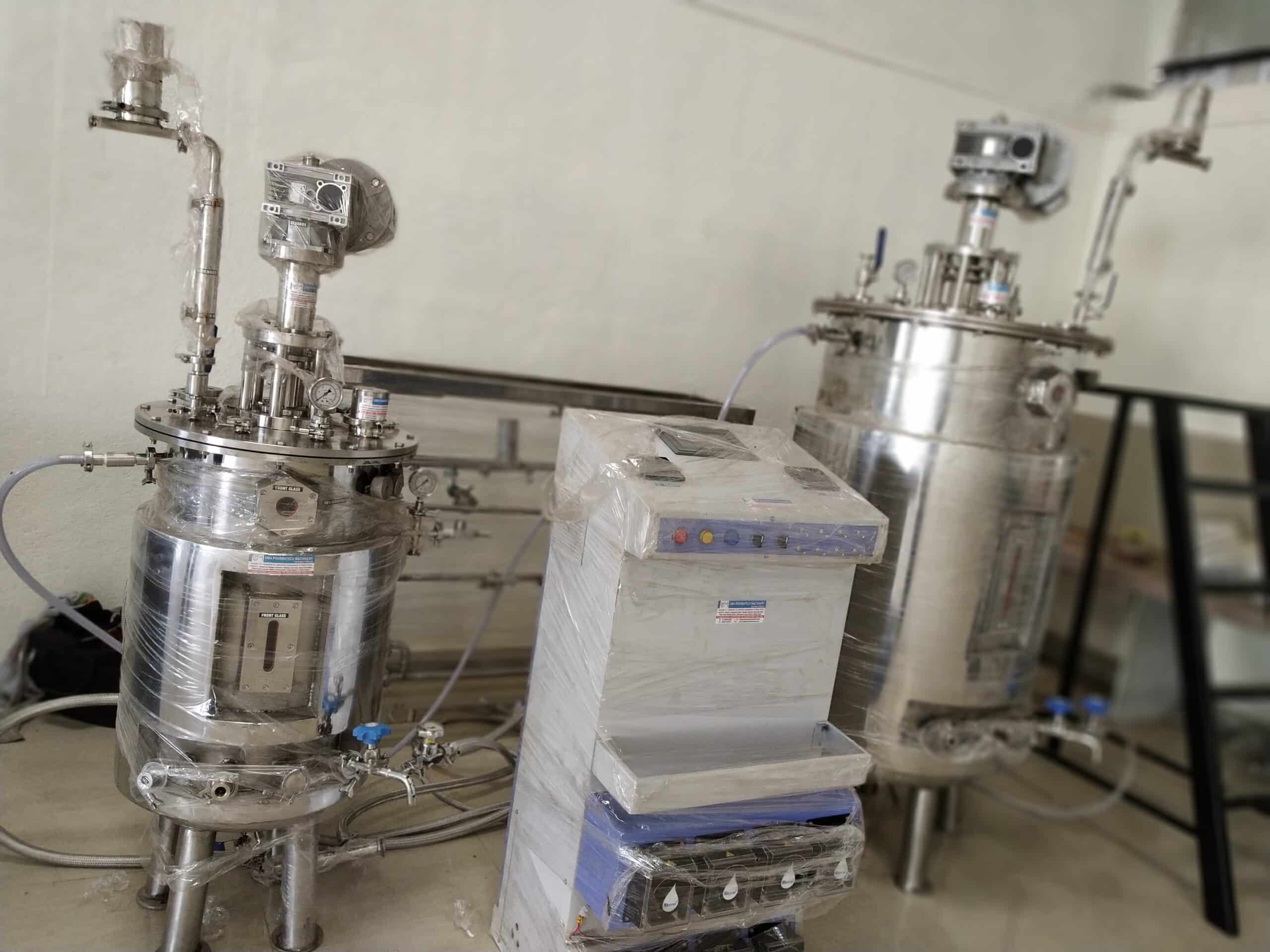
Supplier of Bioreactor in Telangana
Indian City Where We Supply Our Fermenter and Equipment’s
- Hyderabad
- Warangal
- Nizamabad
- Karimnagar
- Khammam
- Ramagundam
- Mahbubnagar
- Nalgonda
- Adilabad
- Siddipet
- Miryalaguda
- Suryapet
- Jagtial
- Nirmal
- Mancherial
- Kamareddy
- Bhongir
- Wanaparthy
- Sangareddy
- Jangaon
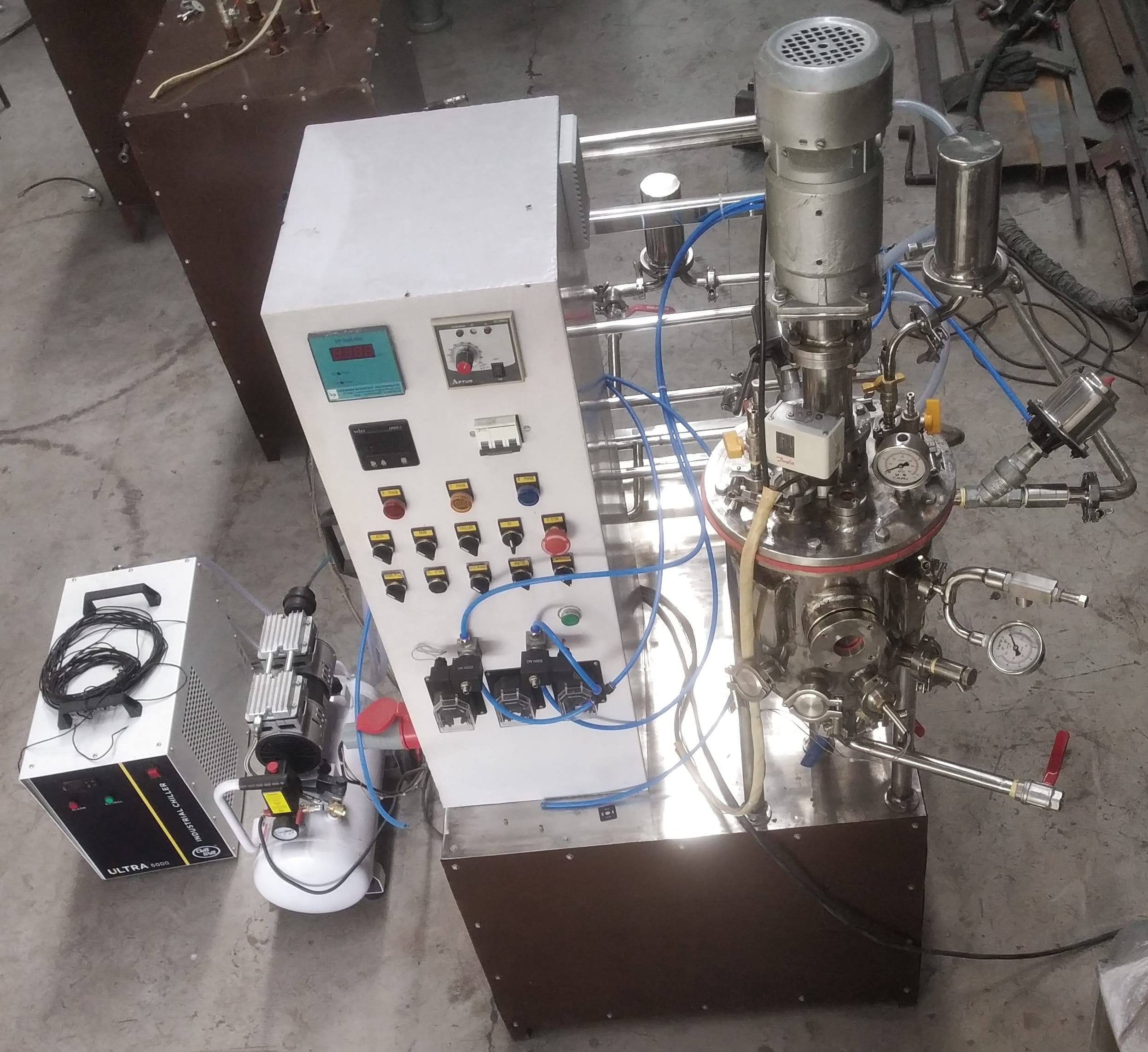
Manufacturer of Bioreactor
- United States
- China
- India
- Brazil
- Russia
- France
- Canada
- Australia
- Germany
- Argentina
- Turkey
- Indonesia
- Pakistan
- Ukraine
- Mexico
- Italy
- Thailand
- Vietnam
- United Kingdom
- Spain
Top 3 Agriculture Countries:
- United States
- China
- India
Best Bioreactor Manufacturer in Maharashtra- Mumbai
Are you searching for a reliable Fermenter Manufacturer in Mumbai? Look no further than Uma Pharmatech Machinery. 🌐 With a commitment to quality, we specialize in crafting cutting-edge fermenters that meet industry standards. Our state-of-the-art facilities in the heart of Mumbai, one of India’s 🌆 top 10 cities, ensure precision and excellence.
At Uma Pharmatech Machinery, we take pride in being prominent Vertical Fermenter Manufacturers in Mumbai, catering to diverse needs. Explore our range, including Steam Sterilizer Machines, designed for optimal performance. 🚀
Collaborate with us, and experience the expertise of leading Fermenter Suppliers and Dealers in Mumbai. Watch our detailed process in action: YouTube Video.
Discover more about our presence and offerings:
Elevate your fermentation processes with Uma Pharmatech Machinery—your trusted partner in Mumbai’s thriving industrial landscape! 🌟
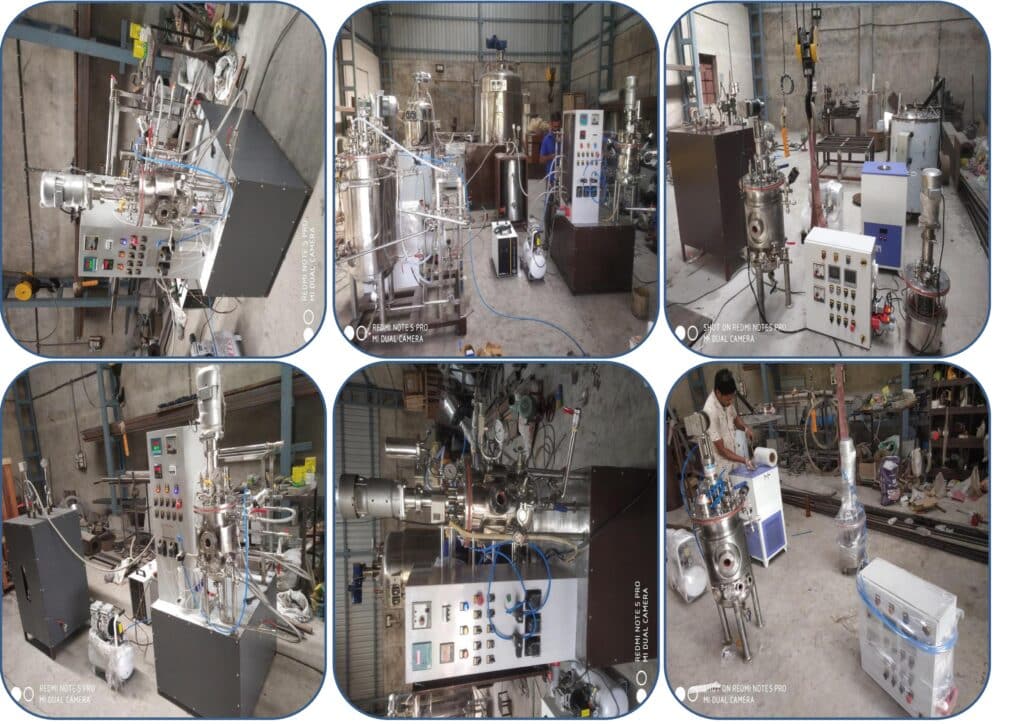
Bioreactor Manufacturers in Mumbai for API Plant
bioreactor for an API manufacturing facility in Maharashtra, near Mumbai, Pune, and Nashik: Are there plans to build an API manufacturing facility in Mumbai, Pune, or Nashik, Maharashtra? If you want to buy a trustworthy bioreactor, look no further! We specialize in offering premium bioreactors that are adapted to the unique requirements of API production. Our bioreactors have advanced features like automated feeding systems, precise temperature control, and real-time monitoring to guarantee the best conditions for cell development and product generation. We provide innovative bioreactor solutions that satisfy the demanding specifications of API manufacturing plants thanks to our knowledge and experience in the sector. Improve your API production capabilities in Mumbai, Pune, and Nashik, Maharashtra, by working with us.
Where are fermenters used?
In many different industries, including as the production of food and beverages, pharmaceuticals, and biotechnology, fermenters are useful and crucial instruments. They are employed to develop and expand microorganisms in order to produce a range of goods, such as alcohol, yoghurt, cheese, and antibiotics. A fermenter can be used to regulate and optimise the fermentation process, producing a consistent and superior final product.
Uma Pharmatech Machinery In (Ahmedabad Gujarat India) Is Best Manufacturer and Supplier and Indian Exporter Of Fermenter and Bioreactors At Very Affordable Cost Compared With Other Fermenter Manufacturers.
The fermenter is a closed Bioreactor created to keep the ideal environment for microbial development. It is often constructed of stainless steel or another non-reactive material, and it has a number of controls for mixing, pH, temperature, and oxygenation. The vessels can be as big as massive industrial fermenters that can produce hundreds of liters of product, or as small as tabletop ones.
Bioreactor Manufacturers in Mumbai, Pune, Nashik, Maharashtra: Are you searching for reputable bioreactor manufacturers in Mumbai, Pune, Nashik, Maharashtra? Your search ends here! We are a trusted name in the industry, offering a comprehensive range of high-quality bioreactors designed for diverse applications. Our bioreactors are engineered with precision and incorporate advanced technologies to meet the ever-evolving demands of the biotechnology sector. Whether you need a benchtop bioreactor or a large-scale production system, we have the expertise to deliver tailored solutions that ensure efficient and reliable bioprocessing. Count on us as your preferred bioreactor manufacturer in Mumbai, Pune, Nashik, Maharashtra, and experience excellence in bioprocess technology.
Industrial Fermenters: What They Are and How They Work
Industrial fermenters are containers that are employed in Pilot Scale fermentation operations to create a range of goods, including drugs, chemicals, and biofuels. These containers are made to give microorganisms the best possible habitat in which to develop and produce the desired end products from the basic components.
Microorganisms like bacteria, yeast, or fungi are used in the fermentation process to transform complex organic chemicals into less complex ones. The raw ingredients are consumed by the microbes, who then transform them into energy, waste, and the required end product. The proper temperature, pH, and nutrients are necessary for these bacteria to develop in the best possible conditions.
What are the two types of bioreactors?
Generally Two Types Of Bioreactor Available as Per Sterilization Method
1) Insitu Serializable Bioreactors
2) Autoclavable Bioreactors
Insitu Bioreactors Made Of Stainless Steel Material. For Sterilize this Bioreactor Require Steam Generator Or Boiler. In This Bioreactor In Place Sterilization Is Possible
Where as Autoclavable Bioreactors are Made Of Borosilicate Glass Material. Autoclave Is Require To Sterile This Fermenter Bioreactor. In This Bioreactor IN place SIP(Sterilize in Place) Not Possible. Motor and Other Accessory Is to Remove From Bioreactor To Sterile Before Place In to The Bioreactor.
Bioreactor Is Special Designed System To Manufacture Bio Product and Biostudy With Absence Of Environment Condition. For Cell Culture and Mammalian Cell Development Bioreactor Is Require With Automatic Control Parameter Like ph., Temperature, Pressure, Agitation Control. In Pilot Scale Bioreactor Also Called as Fermenter
There are Many Types Of Bioreactors
1) Cell Culture Bioreactors
2) Photo Bioreactors
3) Single Use Bioreactors
4) Bacterial Bioreactors
5) Glass Bioreactors
6) Stainless Steel Bioreactors
7) Pilot Scale Fermenter Bioreactors
8) Lab Scale Fermenter Bioreactors
9) Industrial Fermenter Bioreactors
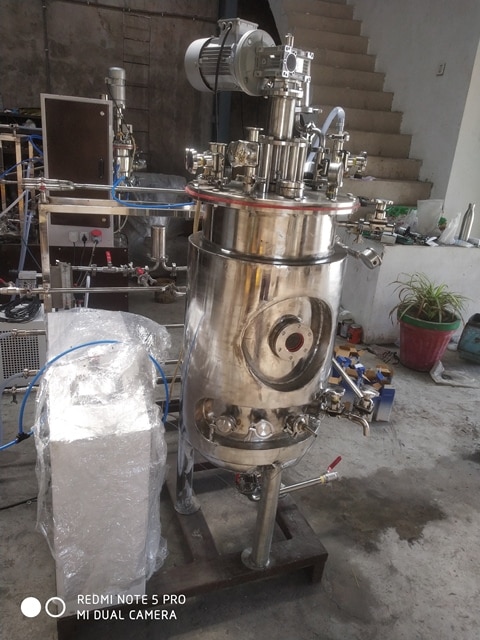
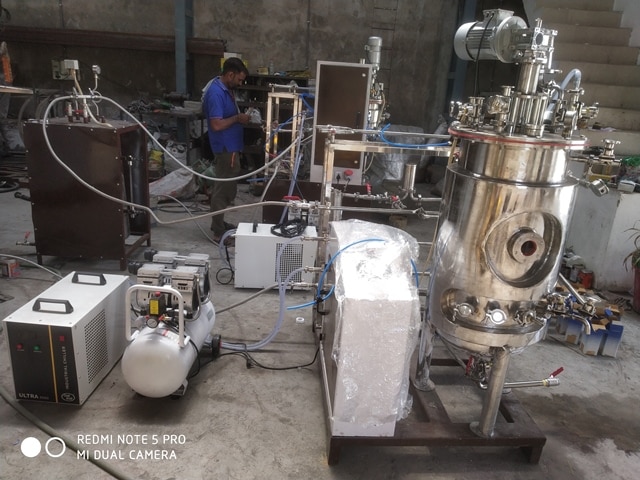
Industrial Fermenters Types:
Industrial fermenters come in a variety of forms, such as batch, fed-batch, and continuous fermenters. According to the nature of the product being produced and the particular needs of the fermentation process, the type of fermenter is chosen.
In a single vessel, raw ingredients and microbes are mixed in batch fermenters, which are utilised for small-scale production. After the fermentation is finished, the product is harvested, and the container is cleaned in preparation for the following batch.
Similar to batch fermenters, fed-batch fermenters gradually supply nutrients and raw materials to the container in order to maintain the best possible development circumstances for the microorganisms. Compared to batch fermenters, this technique enables for larger-scale manufacturing.
The usage of continuous fermenters, which entail a continuous flow of raw ingredients, microbes, and harvested end products through the tank, is common for large-scale manufacturing. This technique enables the manufacture of significant quantities of the required end product while making efficient use of the available resources.
Which reactor is used in chemical industry?
Laboratory Bioreactor Manufacturers in Mumbai-Maharashtra
Welcome to our Basic Guideline on industrial and laboratory fermenters, the revolutionary tools that have transformed the field of biotechnology. In this article, we will delve into the intricacies of fermenters, exploring their functionalities, applications, and benefits. Whether you are a researcher, scientist, or industry professional, this guide will equip you with the knowledge necessary to understand and harness the power of these cutting-edge bioprocessing systems.
The fermentation process is facilitated and managed by fermenters, also referred to as bioreactors. As a result, important products like medications, enzymes, biofuels, and various biochemicals can be produced by microorganisms like bacteria, yeast, or fungi in an environment that is optimal for their growth.
Production Scale Fermenter In Mumbai For Industrial Enzymes Production
For the production of enzymes in Mumbai, Pune, and Nashik, Maharashtra: You’ve come to the correct place if you’re looking for a high-performance fermenter for the manufacturing of enzymes in Mumbai, Pune, or Nashik, Maharashtra. We recognize the crucial part fermenters play in enzymatic processes because we are reputed producers. In order to ensure optimal enzyme synthesis, our cutting-edge fermenters are built to offer exact control over temperature, pH, and agitation. With our dedication to quality and dependability, we provide fermenters that satisfy the exacting standards of the industry that makes enzymes. Count on us to be your top choice for fermenters devoted to the manufacturing of enzymes in Mumbai, Pune, and Nashik, Maharashtra.
Automatic Fermenter System Suppliers in Mumbai
Vessel: The vessel functions as the fermentation’s primary chamber. It can range in size from small laboratory-scale containers to big industrial-scale tanks and is intended to offer a sterile environment.
The agitation system makes sure that the culture media is properly mixed, facilitating even dispersion of nutrients and oxygen throughout the vessel. Impellers, sparrers, or stirrers are frequently used in this system to produce the essential turbulence for effective fermentation.
Temperature Control: Microorganism development and survival depend on precise temperature control. Modern heating and cooling systems are included in fermenters to maintain the ideal temperature range needed by the particular organism being cultivated.
pH Control: The pH value affects the metabolic processes that take place in bacteria. The pH value is monitored and adjusted by pH sensors and controls in fermenters to maintain the perfect environment for optimum growth and product generation.
Aeration and Oxygen Supply: Many fermentation processes depend heavily on oxygen. Aeration systems in fermenters provide oxygen to the growth media, enabling aerobic fermentation. Additionally, oxygen concentrations can be precisely adjusted to match the demands of various microbes.
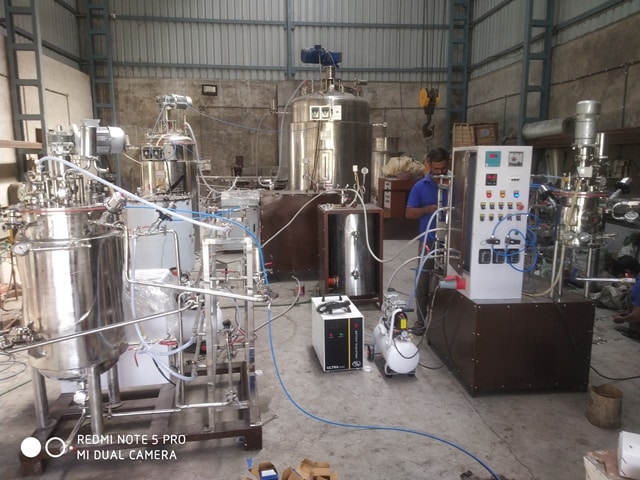
Pilot Scale and Industrial Fermenters Producer in Mumbai-India
Fermenters can be used in a variety of sectors thanks to their versatility. Let’s examine some of the major fields where commercial and laboratory fermenters are essential:
production of biological products
Biopharmaceuticals such therapeutic proteins, vaccines, and antibiotics are frequently made in fermenters. High yields of physiologically active chemicals are produced as a result of the efficient development and expression of genetically modified microbes or cell cultures in the controlled environment of a fermenter.
Biofuel and Biorefinery Processes
In the pursuit of sustainable energy solutions, fermenters are employed in the production of biofuels such as ethanol, butanol, and biodiesel. Microorganisms capable of metabolizing renewable feedstocks, such as agricultural residues or algae, are cultivated in fermenters to convert these resources into valuable biofuels. Additionally, fermenters also play a Basic role in biorefinery processes, where biomass is converted into a wide range of valuable chemicals and materials.
What are the steps of pilot scale-up technique?
The following stages are commonly included in the pilot scale-up process in the pharmaceutical industry:
Process Design: Based on laboratory scale trials and data, the initial stage is to design the pilot scale process. The equipment, process conditions, and parameters that will be employed in the pilot scale manufacturing are all defined here.
Equipment selection: The right machinery and facilities for pilot-scale production must be chosen and obtained based on the process design. This could involve tools designed specifically for the process, such filtration systems and bioreactors.
Process Validation: A high-quality drug product must be produced by the pilot scale process in order for it to be validated that it is consistent with the laboratory size process. This can entail running experiments and gathering data on the procedure’ effectiveness.
Process optimization can be used to raise the performance, efficacy, and consistency of the pilot scale process after it has been validated. To increase the quantity and quality of the medication product, this may entail making adjustments to the process’s conditions, parameters, or machinery.
Scale-up to Commercial Production: The pilot scale process can be expanded to commercial production if it is successful and meets the required criteria. This entails scaling up the pilot-scale procedure to use larger-scale machinery and facilities while ensuring its reliability and effectiveness on a wider commercial scale.
It’s crucial to keep in mind that these procedures could change depending on the particular needs and difficulties of the drug development project. To ensure that the pilot scale-up process complies with all applicable laws and standards, it is also crucial to cooperate closely with regulatory organizations and experts.
The pharmaceutical business uses the pilot scale-up approach to move a drug product’s production from a laboratory scale to a bigger scale, typically between 100 and 1000 litres. Pilot scale-up aims to demonstrate the consistency and quality of the drug product generated at the bigger scale, as well as to validate the scalability and viability of the production process.
Before beginning commercial-scale production, the pilot scale-up stage of the drug development process aids in identifying and resolving any potential difficulties or constraints. This makes it easier to guarantee that the process of commercial-scale production will be effective, efficient, and compliant with legal standards.
Process design, equipment selection, process validation, process optimization, and scale-up to commercial production are some of the processes in the pilot scale-up process. In order to retain the required quality and attributes of the therapeutic product, it is important to make sure that the production process can be reliably and consistently scaled up from laboratory scale to commercial scale.
Top Suppliers of Fermenter in Mumbai-India
Industrial and laboratory fermenters are at the forefront of biotechnological advancements, empowering researchers and industry professionals to revolutionize various fields. From biopharmaceutical production to environmental biotechnology, the applications of fermenters are vast and diverse. By harnessing their power, we can unlock new frontiers in sustainable energy, healthcare, and more. Embrace the transformative potential of industrial and laboratory fermenters and take your biotechnology endeavors to new heights.
Find reputable fermenter manufacturers in Mumbai for your industrial needs.
Mumbai offers a wide range of fermenter manufacturers catering to various industries.
Get high-quality fermenters from experienced manufacturers in Mumbai.
Bioreactor Manufacturers in Pune:
Discover top bioreactor manufacturers in Pune for efficient production processes.
Pune is home to skilled bioreactor manufacturers providing innovative solutions.
Find reliable bioreactor manufacturers in Pune to enhance your production capabilities.
Manufacturers of Fermenter in Nagpur:
Nagpur hosts manufacturers specializing in fermenter production.
Get customized fermenters from reputable manufacturers in Nagpur.
Find reliable manufacturers in Nagpur for your fermenter requirements.
Supplies of Fermenter in Thane:
Source fermenters and related supplies from trusted suppliers in Thane.
Thane offers reliable suppliers of fermenters for your industrial needs.
Ensure a steady supply of fermenters through reputable suppliers in Thane.
Exporter of Pilot Scale Fermenter in Nashik:
Choose Nashik-based exporters for high-quality pilot scale fermenters.
Nashik hosts exporters of fermenters, providing global shipping services.
Exporters in Nashik offer competitive prices and efficient logistics for pilot scale fermenter exports.
Lab Fermenter for Biofertilizers in Aurangabad:
Find lab fermenters suitable for biofertilizer production in Aurangabad.
Aurangabad offers lab fermenters designed specifically for biofertilizer manufacturing.
Boost your biofertilizer production with lab fermenters from Aurangabad.
Glass Bioreactors for Enzymes Production in Solapur:
Solapur hosts bioreactor manufacturers specializing in glass bioreactors for enzymes production.
Choose glass bioreactors from Solapur for efficient enzymes manufacturing processes.
Find reliable glass bioreactors for enzymes production in Solapur.
Industrial Fermenter for API Production in Amravati:
Amravati offers industrial fermenters designed for API (Active Pharmaceutical Ingredient) production.
Find fermenters suitable for API manufacturing in Amravati.
Upgrade your API production with industrial fermenters from Amravati.
Stainless Steel Bioreactors for API Production in Navi Mumbai:
Navi Mumbai hosts bioreactor manufacturers specializing in stainless steel bioreactors for API production.
Choose stainless steel bioreactors from Navi Mumbai for efficient API manufacturing processes.
Find reliable stainless steel bioreactors for API production in Navi Mumbai.
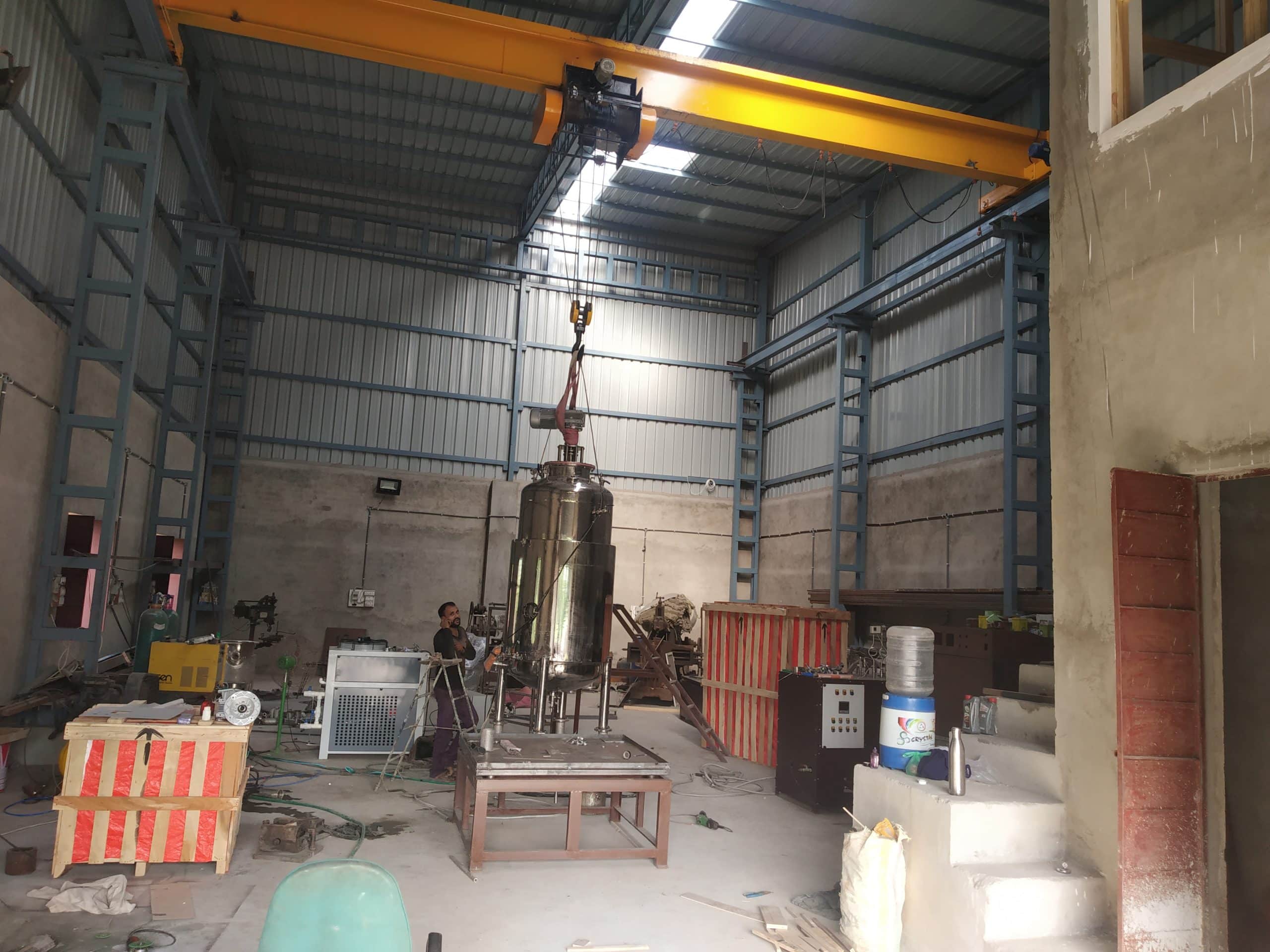
Pilot Scale Fermenter Prize From Manufacturers in Maharashtra-Mumbai
industrial fermenters are IMP equipment utilized in the production of a variety of products during industrial fermentation. According to the nature of the product being produced and the particular needs of the fermentation process, the type of Pilot Scale fermenter is chosen. Pharmaceuticals, chemicals, food, and biofuels are just a few of the many products and processes that Laboratory fermenters are used for.
Bioreactors are key tools in the biotechnology industry, helping to produce a wide range of products as well as treat environmental pollutants. Bioreactors will continue to play an important role in determining the future of biotechnology as technology improves. Please contact us if you want to learn more about bioreactors or need help choosing the correct bioreactor for your purposes. We would be delighted to assist you.
Fermenter Manufacturers
Uma Pharmatech Machinery, a pioneering fermenter manufacturer and bioreactor manufacturer based in Jamshedpur, India, stands as a beacon of innovation and quality. With a comprehensive range of solutions, they lead the league of industrial fermenter and bioreactor suppliers across India’s vibrant landscape. Their expertise extends nationwide, spanning cities like Mumbai, Delhi, Kolkata, and beyond, as well as catering to international markets, including the USA, UK, and UAE.
Industrial Fermenter
Fermenter Suppliers
Bioreactor Suppliers
For research endeavors, their range encompasses the efficient laboratory fermenter for cell culture, while for larger operations, they stand tall as industrial fermenter manufacturers and pilot-scale fermenter manufacturers. In the realm of biofertilizer production, Uma Pharmatech Machinery’s fermenters shine, just as their bioreactors excel in enzyme production setups.
Fermenter Manufacturing Companies in India
Bioreactor Manufacturing Companies in India
Fermenter For Biofertilizer Production
As one of the foremost fermenter manufacturing companies in India and bioreactor manufacturing companies in India, Uma Pharmatech Machinery crafts cutting-edge equipment like the sought-after automatic fermenter and sturdy fermentation tanks. While ensuring top-tier quality, they remain sensitive to the cost of fermenter and bioreactor price, making advanced solutions accessible across scales.
Fermentation Tank Manufacturers
As trailblazing fermentation tank manufacturers, we redefine the art of large-scale bioprocessing. Our tanks embody precision engineering, fostering optimal microbial growth and product yields. From pharmaceuticals to food, our vessels provide the foundation for successful fermentation processes. With a commitment to innovation, we elevate industrial fermentation, delivering equipment that empowers progress.
Cost Of Fermenter, Bioreactor Price
Navigating the path of progress shouldn’t be hindered by budget concerns. Discover competitive solutions with transparency in the cost of fermenter. Our offerings ensure affordability without compromising quality. With a range of options, you can access cutting-edge fermentation equipment tailored to your requirements, driving efficiency and innovation.
Production Fermenter Manufacturers
Uma Pharmatech Machinery’s influence reaches across India’s expanse, including states like Maharashtra, Uttar Pradesh, and Tamil Nadu, fostering progress from Jamshedpur to Mumbai and Chennai. Their excellence isn’t confined to national boundaries; they are distinguished fermenter exporters and bioreactor exporters with a global footprint.
Laboratory Fermenter Cost
Unveil the future of research with our cost-effective laboratory fermenter solutions. We understand the significance of budget-conscious science, offering high-quality equipment at competitive prices. Our lab fermenters enable precise cultivation of microorganisms, yielding valuable insights across various fields. Embrace affordability without compromising on performance, driving innovation from the lab bench to publications and beyond.
Industrial Fermenter Manufacturers
As pioneers among industrial fermenter manufacturers, we shape the landscape of large-scale bioprocessing. With a legacy of engineering excellence, we craft fermenters that power diverse industries. From pharmaceuticals to biofuels, our robust equipment ensures consistent production and optimal yields. With a focus on quality and innovation, we stand as partners in progress, enabling seamless industrial fermentation for a sustainable future.
Pilot Scale Fermenter Manufacturers
Crafted with precision, their stainless-steel fermenters and glass fermenters reflect unmatched dedication. As the sun never sets on Uma Pharmatech Machinery’s commitment to excellence, they continue to illuminate the path for fermenter and bioreactor solutions, enriching laboratories, industries, and landscapes across the world.
Bioreactor For Enzymes Production
Our advanced bioreactor for enzymes production stands at the forefront of biotechnology. Engineered for precision and efficiency, it’s the cornerstone of enzymatic processes. From pharmaceuticals to food and beyond, our bioreactor ensures optimized yields and consistent quality. With innovative design and automation, it streamlines enzyme cultivation, reducing production timelines and costs. Embrace the power of cutting-edge technology for enzymatic excellence.
Laboratory Fermenter For Cell Culture
In the realm of research, our laboratory fermenter for cell culture is a testament to innovation. Tailored for controlled growth environments, it nurtures cells for diverse applications. From studying disease mechanisms to producing biologics, our fermenter enables reproducible results. With precise control over parameters, it mirrors in vivo conditions, advancing scientific understanding. Elevate your cell culture research with a versatile and reliable laboratory fermenter, propelling breakthroughs from bench to bedside.
Fermenter Exporters
Bioreactor Exporters
As premier bioreactor exporters, we bridge scientific frontiers globally. Our cutting-edge bioreactors empower industries, facilitating advanced research and production. We’re committed to driving innovation across international borders, delivering tailored solutions to diverse biotech sectors. With precision engineering and quality assurance, our bioreactors redefine possibilities, nurturing progress on a global scale.
Stainless Steel Fermenter Manufacturers
Crafting excellence, we stand as leading stainless steel fermenter manufacturers. Our vessels uphold the highest standards, blending robustness with hygiene. Catering to diverse applications, we empower industries with reliable equipment. From pharmaceuticals to biofuels, our fermenters lay the foundation for success, ensuring optimal outcomes and seamless operations.
Glass Fermenter Suppliers
As dedicated glass fermenter suppliers, transparency is our hallmark. We provide vessels that foster observation and control, vital for research and process optimization. Our glass fermenters, designed with precision, cater to microbiology, biopharma, and more. With a commitment to clarity, we empower scientists and engineers to visualize progress, sparking advancements across scientific landscapes.
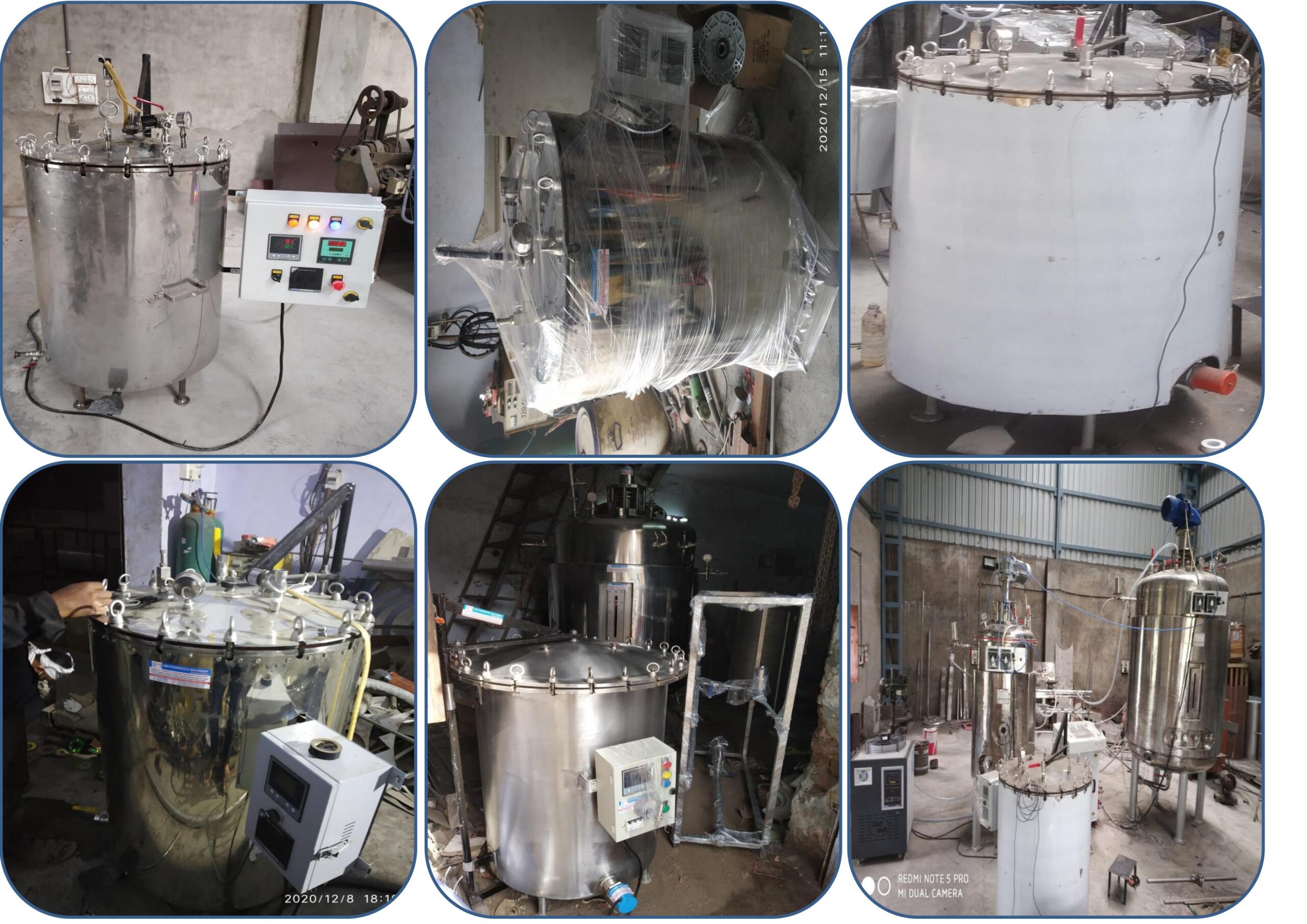